Способ производства древесного активированного угля. Технология производства угля активированного
Производство активированного угля
Активированный уголь известен всем. Большинство знают о нем как о небольших черных таблетках, употребляемых при пищевых отравлениях – по принципу «дешево и сердито». Однако задумывался ли кто-нибудь, из чего делают активированный уголь, и как это происходит? Ведь этот процесс куда более сложный, чем может показаться на первый взгляд.
Что являет собой активированный уголь
Грубо говоря, активированный уголь – это углерод практически без примесей, имеющий вид очень легкого и очень пористого вещества. На самом деле, очень пористого – поверхность 1 грамма готового вещества в зависимости от способа изготовления может иметь поверхность от 500 до 1800 м² - только представьте, таблетка, которую вы принимаете, отравившись, имеет поверхность площадью более километра квадратного!
Изготовляют уголь из множества различных видов сырья, как минеральных, так и органических. Для разных марок и назначений это может быть древесный уголь, каменный уголь, нефтяной кокс, торф, скорлупа грецких и кокосовых орехов, плодовые косточки и многое другое. Медицинский активированный уголь производят именно из кокосового угля.
Сферы применения активированного угля в современной жизни
Сфера применения активированного угля весьма широка. О его свойствах знали еще в древности – на Руси его изготовляли в домашних условиях, чаще всего – из березовых поленьев; для этого даже не нужно было ничего делать – просто угли, оставшиеся после растопки бани, вносили в парилку для активации. По качествам этот прообраз не шел ни в какое сравнение с современными марками угля, однако уже тогда его использовали для лечения желудочных расстройств как у людей, так и у домашнего скота, фильтровали с его помощью воду и домашние алкогольные напитки, и многое другое.
В промышленных масштабах его впервые начали использовать военные. Активированный уголь стал ключевым элементом противогаза, разработанного Н.Д. Зелинским в годы Первой мировой войны – когда немецкие войска начали выпускать на поле боя хлор. Уголь в те годы благодаря своим абсорбирующим свойствам спас множество жизней.
В современном мире его применяют во множестве сфер:
- В пищевой промышленности (например, для очистки сахара)
- В химической промышленности в качестве катализатора реакций
- В медицине
- В фармацевтике
- В очистительных сооружениях для очистки воздуха и воды от промышленных отходов
- В бытовых фильтрах для питьевой воды
а также в многих других сферах.
Все дело в его свойствах – активированный уголь прекрасный абсорбент, очень легкий, очень эффективный, и главное – очень дешевый. Изготовлять его можно практически везде, технология производства хоть и непростая, но не требует длительного времени и чересчур сложных процессов – со всем справляются всего два аппарата. Сайт elgreloo.com предлагает вам ознакомиться с технологией изготовления активированного угля.
Промышленная технология производства активированного угля
Весь процесс производства активированного угля состоит из двух этапов:
- Пиролиз (карбонизация)
- Активация
Производство начинается с того, что сырье, будь то каменный уголь, торф или скорлупки, измельчают до частиц размером всего в несколько сантиметров. После этого его загружают в специальные печи для карбонизации. Существует несколько конструкций печей, применяемых для этой цели. Самые распространенные из них:
- Шахтные
- Вертикальные роторные
- Горизонтальные роторные
- Многополочные
Не смотря на различия конструкции, принцип действия у них один – сырье подвергается термической обработке без доступа кислорода. Температуры в печах предельно высокие – от 600 до 950 градусов по цельсию. В итоге углеродосодержащие сырье превращается в угольки наподобие тех, что остаются от дров после потухшего костра – они обладают первичной прочностью угля, однако у них очень небольшие поры, и абсорбируют вещества они достаточно плохо.
Для того, чтобы активированный уголь стал таковым, карбонизированное сырье проходит через еще один этап производства – непосредственно активацию. В итоге оно получает специфичную внутреннюю структуру, которая и отвечает за прекрасные адсорбционные свойства готового продукта.
Существует два способа активации. В первом варианте карбонизат пропитывают хлоридом цинка или карбонатом калия, а после нагревают до температуры около 600 градусов по Цельсию – опять же таки, без доступа кислорода. Активированный уголь вообще очень не любит открытый воздух – он стремительно окисляется и впитывает в себя сторонние вещества из воздуха, теряя свои свойства.
Второй, самый распространенный способ – наследие древнерусского способа активации, о котором упоминалось ранее. Карбонизированное сырье обрабатывают без доступа воздуха перегретым паром или же его смесью с углекислым газом. Для такой обработки нужна температура до 900 градусов по Цельсию, которой добиться уже сложнее – а потому был создан аппарат, использующий свойства самого угля для его активации. В аппаратах этой конструкции в зону активации пропускается строго дозированное количество воздуха, благодаря чему часть угля самовозгорается – и создает необходимую для активации температуру. Этот способ, впрочем, применяется нечасто, так как существенно снижает выход готового продукта.
Далее все достаточно просто – готовый активированный уголь охлаждают, сортируют, при необходимости подвергают дополнительной обработке, измельчают и упаковывают в том виде, в котором мы его знаем.
Рекомендуем почитать другие полезные статьи по теме
elgreloo.com
Сырье для производства активированного угля
Сырье для производства активированного угля
Активированные угли могут быть получены из разнообразного углеродсодержащего сырья: древесины, каменного и бурого угля, торфа и т. п.
В промышленном производстве активированных углей в качестве сырья чаще всего используются каменный уголь, скорлупа кокосовых орехов и древесина.
Сначала углеродсодержащее сырье подвергают карбонизации – обжигу при высокой температуре в инертной атмосфере без доступа воздуха. Однако полученный карбонизат обладает плохими адсорбционными свойствами, поскольку размеры его пор невелики и внутренняя площадь поверхности мала. Поэтому карбонизат подвергают активации для получения специфической структуры пор и улучшения адсорбционных свойств. Сущность процесса активации состоит во вскрытии пор, находящихся в углеродном материале в закрытом состоянии.
Активация углей может осуществляться посредством обработки водяным паром или специальными химическими реагентами. Активация водяным паром проводится при температуре 800–1000 °C в строго контролируемых условиях. При этом на поверхности пор происходит химическая реакция между водяным паром и углем, в результате чего образуется развитая структура пор и увеличивается внутренняя поверхность угля. С помощью такого процесса можно получать угли, обладающие различными адсорбционными свойствами.
Активация водяным паром позволяет получать угли с внутренней площадью поверхности до 1 500 м2 на грамм угля. Благодаря этой огромной площади контакта активированные угли являются прекрасными адсорбентами. Тем не менее не вся эта площадь может быть доступна для адсорбции, поскольку крупные молекулы адсорбируемых веществ не могут проникать в поры малого размера.
Древесный уголь получают при сжигании растительного материала, в большинстве своем – дерева. Производится он достаточно широко в развивающихся странах, где до сих пор древесина используется в качестве топлива для приготовления пищи и обогрева. Древесный уголь образуется путем нагревания древесины при определенной температуре в отсутствие кислорода. Все, что остается после этого процесса, является черным углеродным материалом – углем.
Так как эффективность процесса адсорбции напрямую зависит от площади поверхности соприкосновения угля и среды, врачи рекомендуют в медицинских целях при отравлениях принимать активированный уголь в виде взвеси порошка в воде.
Некоторые фанатики «натурального происхождения продуктов» предпочитают готовить самостоятельно активированный уголь, который потом может приниматься внутрь, использоваться в водных фильтрах или для очистки продуктов перегонки.
Чтобы изготовить активированный уголь самому, рекомендуется использовать кору таких деревьев, как:
? береза,
? дуб,
? ель,
? ольха,
? осина,
? сосна,
? тополь.
Возраст этих деревьев не должен превышать пятидесяти лет. Кору деревьев необходимо очистить от древесины, сердцевины, сучков. Очищенная кора сжигается на костре до исчезновения огня. Угли, которые появляются в результате сгорания, нужно собрать, выбирая самые большие из них.
Стряхнув золу и пыль, следует поместить угли в посуду, закрыть плотно крышкой и дать им остыть. Как только угольки охладятся, нужно снова очистить их от пыли. В очищенном виде истолочь их в ступе до мелких (не очень) гранул и обязательно просеять. Активированный уголь домашнего производства готов!
Следующая глава >
med.wikireading.ru
Станки для производства активированного угля из каменного и бурого производительностью 1200 тонн в год
На данной линии возможно производство, как активированного угля высокого качества, так и топливных гранул, без дальнейшей обработки.
- Угольная пыль, мелкие, крупные куски бурого угля, (возможно использование каменного угля, торфа) машинами подачи сырья из буртов хранения подаются на транспортёры.
- По транспортёру сырье подается в дробилку, где всё сырьё разбивается до однородного состояния
- По транспортёру сырьевая масса передаётся в двухвалковую смесительную машину, где сырьевая масса становится однородной и пластичной.
-По транспортёру сырьевая масса поступает на вибросито, где отделяются не кондиционные по размерам фрагменты
-Не кондиционные фрагменты по возвратному транспортёру возвращаются на повторное измельчение.
-По транспортёру однородная сырьевая масса поступает на магнитный сепаратор, где удаляются металлические стружки, образовавшиеся при добыче сырья и его измельчении.
-По транспортёру сырьевая масса поступает в сушильную машину сырья. Если состояние сырья этого требует. Проходя по машине на протяжении 16 метровв режиме вращения, влажная сырьевая масса обрабатывается сухим паром. Пар подаётся с бойлера по трубам. Влажность снижается с 40% до 4-5%.
-Сухое сырьё по транспортёру подаётся в брикетирующую машину.
-В брикетирующей машине из сырьевой массы, формируются гранулы, путём давления в форме овальных таблеток.
-Из брикетирующей машины готовые гранулы по транспортёру поступают в зону загрузки печей карбонизации.
-Гранулы раскладываются на специальных противнях, слоем определенной технологией толщиной, и с помощью погрузчика, загружаются в печи карбонизации. В печи карбонизации проходит первичное выжигание органики и карбонизация гранул.
-Через установленный технологией промежуток времени протвени с карбонизированным сырьём достают из печи подъёмником.
-Из дробилки по транспортёру гранула подаётся на вибросито тонкой очистки.
-В зависимости от требований к качестве продукта полученные гранулы, по транспортёру могут быть отправлены в ванну азотирования. Для углей высшего качества, применяемых в пищевой и фармакологической промышленности, азотирование рекомендуется.
-Гранулу транспортёром подают к печам активации.
-У печей активации гранула размещается на специальных поддонах и с помощью подъёмника, грузится в печь активации.
- В печи гранула угля активируется паром. Пар поступает из бойлера по трудам.
- По истечении заданного технологией периода времени, подъёмник достаёт поддон с активированным углем.
-При необходимости если, была нарушена технология производства, и произошло спекание активированного угля, спекшийся уголь по транспортёру подается на измельчитель.
-Уголь остывает и по транспортёру подаётся в участок упаковки.
-Вупаковочной уголь фасуется в бумажные зашиваемые мешки с навеской 0,5-10 кг.
-Погрузчиком, активированный уголь, отвозят на склад готовой продукции.
Угольная пыль, мелкие, крупные куски бурого угля, (возможно использование каменный уголь, торф) машинами подачи сырья из буртов хранения подаются на транспортёры.
- По транспортёру сырье подаются в дробилку, где всё сырьё разбивается до однородного состояния
- По транспортёрусырьевая масса передаётся в двухвалковую смесительную машину, где сырьевая масса становится однородной и пластичной. При необходимости на этом этапе в сырьевую смесь прибавляютвяжущие элементы, они необходимы, когда уголь рыхлый и гранула не держит форму.
-По транспортёру сырьевая масса поступает на вибросито, где отделяются не кондиционныепо размерамфрагменты.
-Не кондиционные фрагментыпо возвратному транспортёру возвращаются на повторное измельчение.
-По транспортёру однородная сырьевая масса поступает на магнитный сепаратор, где удаляются металлические стружки, образовавшиеся при добыче сырья и его измельчении.
-По транспортёру сырьевая масса поступает в сушильную машину сырья. Если состояние сырья этого требует. Проходя по машине на протяжении 16 метровв режиме вращения, влажная сырьевая масса обрабатывается сухим паром. Пар подаётся с бойлера по трубам. Влажность снижается с 40% до 4-5%.
-Сухое сырьё по транспортёру подаётся в брикетирующую машину.
-В брикетирующей машине из сырьевой массы, формируются гранулы, путём давления в форме овальных таблеток.
-Из брикетирующей машины готовые гранулы поступаютна упаковочную машину, где упаковываются в мешки по 25 кг., или Биг-Бэги по 1000 кг.
- Погрузчикупакованные в мешки гранулы отвозит на склад.
*Примечание № 1 топливо для тепловых узлов.
Потребителей тепла и дополнительного топливав комплексе 7 машин. Это сушильная машина 500 кг пара час, две печи активации 5,5 тонн пара в час, запуск печей карбонизации, 4 штуки, запуск и работадвух печей активации. Экономически и технологически самым удобным топливом является газ. Находясь на угольном месторождении, оптимальным источником газа является газификация углей. Для этого в комплектацию включен газогенератор.
*Примечание № 2 рабочие циклы
Цикл работы: печь карбонизации 30 мин, производительность печи 24 часа 10-12 тонн.
Активационная печь: цикл активации 4 часа
Разгрузка печи 30 минут
Загрузка печи 20 минут до 1 часа.
За 24 часа 4—2.5 тонны готового сырья
*Примечание №3
В зависимости от требований к качеству конечного продукта. Для медицинских целей одни, для очистки воды или очистки воздуха другие. Разработаны разные технологии производства активированного угля. Технология изготовления различается по температурным и временным режимам активации, а также закладываемым в смеситель добавочным сырьем.
www.v-hold.ru
Оборудование по производству активированного угля. Оборудование из Китая
Оборудование по производству активированного угля
Сначала углеродсодержащее сырье подвергают карбонизации - обжигу при высокой температуре в инертной атмосфере без доступа воздуха. Однако полученный карбонизат обладает плохими адсорбционными свойствами, поскольку размеры его пор невелики и внутренняя площадь поверхности мала. Поэтому карбонизат подвергают активации для получения специфической структуры пор и улучшения адсорбционных свойств.
Активация
Активация углей может осуществляться посредством обработки водяным паром или специальными химическими реагентами. Активация водяным паром проводится при температуре 800 - 1000 °C в строго контролируемых условиях. При этом на поверхности пор происходит химическая реакция между водяным паром и углем, в результате чего образуется развитая структура пор и увеличивается внутренняя поверхность угля. С помощью такого процесса можно получать угли, обладающие различными адсорбционными свойствами.
Активация водяным паром позволяет получать угли с внутренней площадью поверхности до 1500 м2 на грамм угля. Благодаря этой огромной площади поверхности активированные угли являются прекрасными адсорбентами. Тем не менее, не вся эта площадь может быть доступна для адсорбции, поскольку крупные молекулы адсорбируемых веществ не могут проникать в поры малого размера
Связанных с проведением избирательной сорбции и очисткой растворов, газов, паров от примесей органических и других веществ. Применение активированных углей имеет глобальное значение для решения экологических проблем охраны окружающей среды.
Активные угли – пористые углеродные тела, создающие при контакте с газообразной или жидкой средой значительную площадь поверхности для протекания сорбционного процесса.
Базовая комплектация LU-AZ 1200-1 Ежегодная производительность 1200 тонн активированного угля (расчет из 345 дней в году, ежедневно 24 часа в 3 смены) Оборудование производится по лицензии США при использовании их технологии Мини-завод состоит из 3-х участков: Состав оборудования Участок подготовки продукции №1. Цех подготовки сырья: 1.Конверторная печь Φ1.5×20 м (1 штука)
2.Котел паровой 0,5 куб.м (по емкости и емкости не попадает в зону ответственности ГосГор-технадзора РФ:(1 штука)
3.Внутренний барабан для обжиговой печи, огнеупоры для обжиговой печи:(1 комплект)4.Спиральный транспортер подачи сырья с нержавеющими тарельчатыми дисками Φ1100(1 ком-плект)
5.Ковшевой элеватор(1 комплект)
6.Машина для промывки и обеззараживания сырья:(1 комплект)
7.Агрегат для смешивания сырья из нержавеющей сталди (1 комплект)
8. Электрический щит управления
Участок №2.
Выпуск готовой продукции:
1.Сушильная машина из нержавеющей стали (сушка горячим воздухом):(1 комплект)
2. Обжиговая печь, работающая на горячим воздухе:(1 комплект)
3. Мельница:(1 комплект)
4. Машина по выпуску готовой продукции:
5. Вибросито
6. Система дымоотвода:
7. Электрический щит управления
Участок №3
Упаковка и складирование
1. Лаборатория по контролю качества готовой продукции
2. Спиральный транспортер Ф1100
3. Машина для упаковки готовой продукции в пластиковые пакеты
4. Машина для упаковки в картонную тару
5. Весы
6. Инструменты и оборудование, необходимые для обслуживания комплекса
7. Электрический щит управления
Передача технологии производства и технической документации
Все оборудование соответствует государственным стандарта КНР.
Примечание 1. По заказу в комплекс может быть добавлен пресс для производства таблеток и машина для упаковки таблеток. Примечание 2. По заказу комплекс дополняется древорубками и строгальными машинами для производства опилок. И 3 транспортерами подачи сырья.
Примечание 3. Обжиговая печь работает на каменном угле, по желанию заказчика возможна поставка печи, работающей на жидком или газовом топливе.Для производства необходимы вода (400 т в день, водяной пар:давление:0.4MPa кол-во потребления:1.5T/H), регенерация и повторное использование невозможны; электроэнергия Энергия:Напряжение:380 трехфазный 50HZ
Освещение: Напряжение:220 двухфазный 50HZ Трансформатор:100KVA
Электричество: Электричество должно подаваться в течение 24 часов Ежегодное использование электричества: - примерно 600000 KWH
Сырье: опилки 1400-1500 куб.м в месяц, 50-52 куб.м в день
Толщина фракции:10—80 мм зольность:≤2% влажность:30%
Лучше использовать сосновые и еловые опилки.
Активирующая составляющая
Сырье |
Объем добавок, не менее |
Молекулярная формула |
Стандарт |
Фосфорная кислота |
1% - 900 кг |
h4PO4 |
GB2091—80 |
Серная кислота |
1% - 900 кг |
h3SO4 |
GB625—89 |
Соляная кислота |
1% - 900 кг |
HCL |
GB622—89 |
1.3 Технологическая схема размещения оборудования

Пояснение к технологическому процессу:
После просеивания древесных опилок и смешивания их с фосфорной кислотой, подаем эту смесь в обжиговую печь для углефикации и активизации. После активизации продукт готов наполовину. Если в процессе подготовки в полуфабрикате выявлено большое количество фосфорной кислоты, то после промывки избыток будет направлен в сбор для шихты (шлака). Затем уголь еще раз промывается, сушится, измельчается до готовой продукции.
Требования к производственным площадям:
Заводская площадь: примерно 1800 м2
1.Участок подготовки - 600 м2
2. Участок сушки - 150 м2
3. Участок упаковки - :150 м2
Склад готовой продукции: - примерно 400 м2
Склад сырья: примерно 500 м2
Склад металлических запчастей:20 м2
Дополнительно необходимо предусмотреть рядом с территорией завода:
1.Место для хранения угля
2.Место для хранения угольного шлака
Характеристика качества получаемой продукции
Оборудование производит 3 сорта. Качественный показатели могут меняться за счет увели-чения или уменьшения в продукте активирующих элементов, в зависимости от имеющейся потребности. В приведенной выше таблице указаны объемы добавок, принятые в КНР.
Сорт |
сорт—1 |
сорт—2 |
сорт—3 |
Обесцвечивание жженого сахара % |
≥110 |
≥100 |
≥90 |
Хлорид % |
≤0.05 |
≤0.08 |
≤0.1 |
Зольность % |
≤5 |
≤6 |
≤6 |
Влажность % |
≤10 |
≤10 |
≤10 |
PH |
3—5 |
3—5 |
3—5 |
В комплектацию не включены подводящие трубопроводы воды, запорная арматура, вентиляционное оборудование.
www.luniwei.com
Способ получения активированного древесного угля
Изобретение относится к сорбционной технике и может быть использовано для производства адсорбента - активированного древесного угля. Способ получения активированного древесного угля включает пиролиз древесины осины, измельчение полученного древесного угля до размера частиц 0,2-2,0 мм, активацию пероксидом водорода при температуре 250-300°C в течение 5-10 минут при давлении 30-50 МПа, сепарацию, промывку дистиллированной водой и сушку. Изобретение позволяет получить качественный уголь, способный к эффективной сорбции бензола из водных сред. 2 табл.
Изобретение относится к сорбционной технике и может быть использовано для производства адсорбента в виде активированного древесного угля, применяемого, в частности, для адсорбирования из водной среды бензола.
Известен способ получения адсорбента в виде древесного угля из цельной древесины (Выгородов В.А. и др. Технология лесохимического производства, М., Лесная промышленность, 1987 г., с.310).
Древесный уголь, полученный из древесины твердых лиственных пород, обладает высокой адсорбционной способностью по отношению к бензолу, загрязняющему водные среды, а древесный уголь из древесины мягких лиственных пород адсорбирует бензол в тех же средах, но за длительный промежуток времени, исчисляемый десятками минут.
Недостатком известного способа является использование дорогого, остродефицитного сырья твердолиственных пород древесины, запасы которой при современных методах хозяйствования катастрофически уменьшаются.
Известен способ получения древесного активированного угля из твердолиственного сырья, преимущественно дуба (Бронзов О.В. и др. Получение, основные свойства и области применения древесного угля. «Лесная промышленность», М., 1979, с.107-108 - прототип). Активирование древесного угля, полученного пиролизом твердолиственной древесины, проводят водяным паром при температуре 850-900°C.
Недостатками известного способа являются высокая энергоемкость процесса активации, использование твердолиственного сырья, которое является дефицитным и дорогим.
Техническая задача изобретения - повышение эффективности способа получения активированного древесного угля на базе естественно возобновляемых, доступных и дешевых ресурсов, к которым относится древесина осины, способного быстро и качественно сорбировать бензол из водных сред при снижении энергоемкости процесса активирования, снижении трудозатрат и обеспечении химической активации угля, который не содержит токсичных продуктов и не требует нейтрализации.
Поставленная техническая задача достигается тем, что в способе получения активированного древесного угля, включающем пиролиз древесины, измельчение полученного древесного угля, его активацию, сепарацию, промывку дистиллированной водой и сушку конечного продукта, - пиролизу подвергают древесину осины, процессы измельчения и сепарации проводят с отбором частиц с размером 0,2-2,0 мм, для активации используют пероксид водорода, при этом процесс активации одной массовой части отобранных частиц древесного угля проводят их выдерживанием в капсулах в присутствии 2,5 массовых частей 10%-ного раствора пероксида водорода при температуре 250-300°C в течение 5-10 минут при давлении 30-50 МПа.
Изобретение имеет следующие отличия от прототипа:
- пиролизу подвергают древесину осины;
- процессы измельчения и сепарации проводят с отбором частиц с размером 0,2-2,0 мм;
- для активации используют пероксид водорода, при этом процесс активации одной массовой части отобранных частиц древесного угля проводят их выдерживанием в капсулах в присутствии 2,5 массовых частей 10%-ного раствора пероксида водорода при температуре 250-300°C в течение 5-10 минут при давлении 30-50 МПа.
Это позволит повысить эффективность способа получения активированного древесного угля на базе естественно возобновляемых, доступных и дешевых ресурсов, к которым относится древесина осины, способного быстро и качественно сорбировать бензол из водных сред при снижении энергоемкости процесса активирования, снижении трудозатрат и обеспечении химической активации угля, который не содержит токсичных продуктов и не требует нейтрализации.
В просмотренном нами патентно-информационном фонде не обнаружено технических решений, содержащих указанные отличительные признаки, а также - совокупность указанных отличительных признаков.
Изобретение применимо и будет использовано в отрасли в 2008 г.
В таблице 1 представлены уровни концентрации бензола (промилле) в водном растворе при воздействии исследуемых углей для различных временных интервалов. Доза: 0,5 г исследуемого угля в 50 мл модельного раствора.
В таблице 2 представлена кинетика снижения концентрации бензола в модельном растворе.
Способ выполняли следующим образом.
ПРИМЕР.
Способ получения активированного древесного угля включает пиролиз древесины осины, измельчение полученного древесного угля, его активацию пероксидом водорода, сепарацию, промывку дистиллированной водой и сушку конечного продукта, причем процессы измельчения и сепарации проводят с отбором частиц с размером 0,2-2,0 мм, при этом процесс активации одной массовой части отобранных частиц древесного угля проводят их выдерживанием в капсулах в присутствии 2,5 массовых частей 10%-ного раствора пероксида водорода при температуре 250-300°C в течение 5-10 минут при давлении 30-50 МПа.
Адсорбционные свойства полученных образцов древесного угля изучались в Санкт-Петербургском Центре исследования и контроля воды на модельном водном растворе бензола. Исследования выполнены с использованием хроматографа Agilent 6850.
При проведении экспериментов для получения сравнительных показателей использовались угли из натуральной древесины осины (пример 1) и дуба (пример 2).
Результаты экспериментов представлены в таблице 1.
Качественная и количественная картина адсорбции бензола полученными по примерам образцами древесного угля очевидна из данных табл.1. Для оценки интенсивности процесса адсорбции различными образцами древесного угля введем коэффициент адсорбции К
где Кнач, Кi - соответственно начальная и текущая концентрация бензола в исследуемом модельном растворе.
Расчетные значения коэффициентов К сведены в таблице 2.
По результатам анализа данных таблиц 1 и 2 видно, что активированный уголь, полученный заявленным способом, поглощает 95% бензола в течение 5-10 минут и продолжает улучшать эти характеристики в последующее время (до 60 мин).
Таким образом, заявленное техническое решение позволяет повысить эффективность способа получения активированного древесного угля на базе естественно возобновляемых, доступных и дешевых ресурсов, к которым относится древесина осины, способного быстро и качественно сорбировать бензол из водных сред при снижении энергоемкости процесса активирования, снижении трудозатрат и обеспечении химической активации угля, который не содержит токсичных продуктов и не требует нейтрализации.
Эффект заявленного технического решения достигается при совокупности всех заявленных признаков.
Таблица 1 | |||||||
№ п/п | Образцы углей | Размер отобранных частиц древесного угля, мм | Соотношение частиц древесного угля и пероксида, мас. ч. | Температура активации, °С | Время активации, мин | Продолжительность очистки загрязненной воды, мин | Уровень концентрации бензола в водном растворе, промилле |
1 | 2 | 3 | 4 | 5 | 6 | 7 | 8 |
1 | Древесный уголь из натуральной осины | - | - | - | - | 0 | 1,2 |
5 | 0,85 | ||||||
10 | 0.26 | ||||||
30 | 0,16 | ||||||
60 | 0,12 | ||||||
2 | Древесный уголь из натурального дуба | - | - | - | - | 0 | 1,1 |
5 | 0.04 | ||||||
10 | 0,025 | ||||||
30 | 0,02 | ||||||
60 | 0,009 | ||||||
3 | Древесный уголь из осины, полученный заявленным способом | 0,2 | 1:2,3 | 250 | 5 | 0 | 1,4 |
5 | 0,85 | ||||||
10 | 0,02 | ||||||
30 | 0,02 | ||||||
60 | 0,01 |
Продолжение таблицы 1 | |||||||
1 | 2 | 3 | 4 | 5 | 6 | 7 | 8 |
1,0 | 1:2,4 | 275 | 7 | 0 | 1,4 | ||
5 | 0,83 | ||||||
10 | 0,02 | ||||||
30 | 0,02 | ||||||
60 | 0,01 | ||||||
2,0 | 1:2,5 | 300 | 10 | 0 | 1,4 | ||
5 | 0,8 | ||||||
10 | 0,02 | ||||||
30 | 0,02 | ||||||
60 | 0,01 |
Таблица 2 | ||||||
N п/п | Образцы углей | Продолжительность контакта, мин | ||||
0 | 5 | 10 | 30 | 60 | ||
1 | Древесный уголь из натуральной осины | |||||
1,0 | 1.5 | 4,5 | 7,5 | 10.0 | ||
2 | Древесный уголь из натурального дуба | |||||
1,0 | 27,5 | 44.0 | 55,0 | 122,2 | ||
3 | Древесный уголь из осины, полученный заявленным способом | |||||
1,0 | 17,5 | 70,0 | 77,7 | 140,0 | ||
Способ получения активированного древесного угля, включающий пиролиз древесины, измельчение полученного древесного угля, его активацию, сепарацию, промывку дистиллированной водой и сушку конечного продукта, отличающийся тем, что пиролизу подвергают древесину осины, процессы измельчения и сепарации проводят с отбором частиц с размером 0,2-2,0 мм, для активации используют пероксид водорода, при этом процесс активации одной массовой части отобранных частиц древесного угля проводят их выдерживанием в капсулах в присутствии 2,5 мас.ч. 10%-ного раствора пероксида водорода при температуре 250-300°C в течение 5-10 мин при давлении 30-50 МПа.
www.findpatent.ru
Способ производства древесного активированного угля
Изобретение относится к области производства активного угля для углеродных фильтрующих материалов умеренно-сорбционного типа. Сущность изобретения состоит в том, что после сушки древесной массы осуществляют совмещенные пиролиз и активацию древесной массы с использованием в качестве активирующего агента летучих пиропродуктов, термовыдержку при температуре пиролиза и активации, последующее охлаждение продукта. Совмещенные пиролиз, активацию, термовыдержку и охлаждение осуществляют как электроактивные, т.е. сопровождают электрозаземлением при потенциале 0,1-50 В. 1 табл., 2 ил.
Изобретение относится к технологиям неорганической химии, в особенности к способам получения материалов на основе углерода, в частности к способам получения активированного угля из растительного сырья с использованием газообразных активирующих агентов.
Прототипом изобретения является способ получения активированного угля, включающий составление из принимаемой древесной массы расходного сырья-запаса, сырье-подработку, порционирование подработанного сырьевого кондиционата, термообработку имеющих место технологических переделов, предполагающую сушку сформированного порционата, совмещенные пиролиз и активацию нарабатываемой суенки с использованием в качестве активирующего агента летучих пиропродуктов, обособленную термовыдержку твердого остаточного активата и охлаждение выдержанного нормализата, завершающее термообработку распорционирование остуженного рефрижерата и передачу усредненной массы твердого предпродукта на составление товарных партий умеренно активированного угля. Особенностью принятого за прототип способа является то, что совмещенные пиролиз и активацию, а также обособленную термовыдержку и охлаждение производят как электропассивное. Для этого упомянутые технологические операции лишают возможности хода в электрически активном режиме, в частности их лишают сопровождения принудительно-форсированным электрозаземлением массы имеющих место технологических переделов. Неопределенность электрозаземления не позволяет обеспечить продолжение структуризационно-индукцированным электрическим зарядам внутреннего электросопротивления структурных образований, самовозникающих в ходе технологически-операционного трансформирования массы технологических переделов. Это не позволяет обеспечить снятие накапливаемых электрических зарядов с обрабатываемой массы. Накапливаемые электрические заряды вызывают торможение течения нужной структуризации, которая определяет качество целевого углепродукта. В частности, в целевом продукте не происходит развитие скелетно-кристаллической аллотропической составляющей. Основным недостатком принятого за прототип способа ввиду указанных особенностей является непредставляемость устранения сопротивления достижения целевым углепродуктом потенциального уровня возможного качества. Задачей изобретения является устранение основного недостатка прототипа. Сущность предложенного технологического решения состоит в том, что в предлагаемый способ, характеризуемый наличием той же, что и прототип, совокупности признаков, начиная от составления из принимаемой древесной массы расходного сырье-запаса и кончая составлением товарных партий умеренно активированного угля, внесен ряд отличий, которые состоят в том, что совмещенные пиролиз и активацию, а также обособленную термовыдержку и охлаждение производят как электроактивные. Для этого их сопровождают принудительным форсированным электрозаземлением массы имеющих место технологических переделов. Указанное электрозаземление инициируют потенциалом напряжением в 0,1 - 50 В. Недоведение напряжения инициирования в 0,1 В не позволяет достичь надежного преодоления противодействия структур отводу тормозящих развитие материало-трансформационного процесса накапливаемых электрических зарядов. Превышение этим же потенциалом напряжения в 50 В вызывает нежелательный запуск параллельного течения реакций побочного электрохимического окисления вещества технологических переделов, приводящего, в конечном итоге, к чрезмерной трансформации сырьевого вещества и нарушению качества целевого продукта. Подтверждением наличия у предложенного технического решения изобретательского уровня является отсутствие следования его явным образом из известного уровня техники (см. а.с. СССР N 1171506). На фиг. 1 изображена структурная схема установки для реализации способа, компонуемой с использованием вертикально-камерного печного агрегата, обеспечивающего манипулирование технологическими переделами с помощью стоячих цилиндрических реторт; на фиг. 2 - вариант компоновки печного агрегата в горизонтально-камерном исполнении, обеспечивающем манипулирование технологическими переделами с помощью цилиндрического массопровода. Установка для реализации способа включает площадку 1 для составления из принимаемой древесной массы расходного сырье-запаса. Площадка 1 сопряжена со станочным комплексом 2 для проведения сырье-подработки, в частности для возможного окорения древесных стволов, их распиловки на мерные поленья и чурбаки и отсортировки требуемого сырьевого кондиционата. Далее размещены площадка 3 для хранения запаса сырьевого кондиционата и площадка 4 для его порционирования. Возможным для площадки 4 может быть привязка к депо 5 для размещения набора оборотных реторт 6 и к депо 7 для размещения набора оборотных ретортных крышек 8 дыхательно-лабиринтной конструкции. Возможным для площадки 4 может быть следование за ней вертикально-камерного печного агрегата 9 или горизонтально-камерного печного агрегата 10. В вертикально-камерном агрегате 9 предусмотрено вычленение сушильной секции 11 и секции 12, обеспечивающей проведение совмещенных операций пиролиза-активации и обособленной термовыдержки. После печного агрегата 9 спланирована охладительная площадка 13. Площадка 13 размещена доступной для печного кранового манипулятора 14. Горизонтально-камерный печной агрегат 10 предусматривает включение в установку депо 15 для размещения набора внутримассопроводных грузоносителей 16. При этом в агрегате 10 предусмотрено вычленение сушильной секции 17, секция 18 совмещенных пиролиза-активации, секции 19 термовыдержки и охладительной секции 20. После печных агрегатов 9, 10 осуществлено размещение поста 21 распорционирования имеющего место технологического передела, пребывающего в состоянии охлажденного рефрежирата. Пост 21 введен на усреднительную бункерную секцию 22. После этой секции 22 размещено фракционирующее устройство 23. Основной подситовый выход устройства 23 выведен на дозирующий бункер 24 весовой продуктозатаривающей станции 25. Указанная станция 25 оборудована транспортной системой 26 для отвода сформированных мешочных продуктоупаковок 27. Вспомогательный надситовый выход фракционирующего устройства выведен на дробильно-крошильный агрегат 28. После агрегата 28 размещено сепарационное средство 29. Основной подситовый выход средства 29 связан с дозирующим бункером 24. Печные агрегаты 9, 10 соединены с устройствами 30 принудительного электрозаземления. Примеры реализации способа. Пример 1. Для ресурсного обеспечения, реализующего предложенный способ технологического процесса, осуществили приемку заготовленной сырой древесной массы. Принятая древесная масса была сформирована древесиной, пригодной для переработки в технологический древесный уголь-сырец. Она соответствовала ГОСТ 24260-80 "Сырье для пиролиза и углежжения". Влажность древесины соответствовала классу "сырая масса". В частности, влажность древесины была равна 50 мас. %. Доля включений гнили не превышала 0,7 мас.%. Из принимаемой древесной массы произвели составление расходного сырье-запаса. Для этого из нее произвели изъятие стволов ольхи, ивы, рябины, а также стволов всех пород, диаметр которых не доходил до 14 см. Далее предприняли сырье-подработку. В ходе сырье-подработки древесные стволы подвергли при необходимости окорению, распиловке на поленья и чурбаки длиной 1,0 - 1,25 м и выдержке до трансформирования сырья в начальный технологический передел с влажностью 25 мас.%, соответствующей классу "воздушно-сухой сырьевой кондиционат". Получив подработанный сырьевой кондиционат, осуществили порционирование объединяющего его материалопотока. Для этого из поленьев составили пучки объемом в 3,5 м3, употребляемые при возможной обработке материалопотока с использованием стоячих цилиндрических реторт, или объемом 0,3 м3, употребляемые при возможной обработке с использованием лежачего цилиндрического массопровода. Технологический передел был проведен в результате порционирования в состояние упорядоченного порционата. Он был способен образовывать компактный контейнеризат и мобильный материалоизолянт. После этого начали осуществлять многостадийную термообработку имеющих место технологических переделов. Указанная термообработка предполагала сушку сформированного порционата. Сушка была проведена за счет внешнего порционата в течение 8 ч нагретым до 120oC газообразным теплоагентом. В качестве упомянутого теплоагента использовали потерявшие тепло утилизационные дымовые газы. Технологический передел переходил при этом в состояние сушенки, имеющей влажность 1 мас.%. Далее произвели совмещенные пиролиз и активацию нарабатываемой сушенки с использованием в качестве активирующего агрегата летучих пиропродуктов. Выделение расходуемых на активацию летучих пиро-продуктов соответствовало 35 мас.%. Генерирование потребных летучих продуктов инициировали внешним нагревом сушенки до 600oC газообразных теплоагентом. В качестве летучегенерационного теплоагегата использовали первичные дымовые газы. Эти газы получали стороннетопочным сжиганием подходящих древесных отходов или несортовых дров. Совмещенные пиролиз-активацию длили в течение 4 ч. В результате технологический передел последовательно переходил в состояние пиролизата, обезлетученного огарка и твердого остаточного активата. Достигнув полного обезлетучивания технологического передела, начали осуществлять обособленную термовыдержку твердого остаточного активата. Осуществляемая термовыдержка протекала при 600oC, ее длительность составляла 3-4 ч. В результате термовыдержки технологический передел перешел в состояние механически стабильного нормализата. Для перевода технологического передела также еще и в химически стойкую форму предприняли оконцовывание термообработки охлаждением выдержанного нормализата. Охлаждение производили за счет внешнего теплоотвода. Теплоотвод шел в атмосферный воздух. В результате технологический передел переходил в состояние остуженного до 60oC рефрижерата. Произведенную термообработку завершили распорционированием технологического передела, предпринимаемым для его усреднения. Для этого технологический передел подвергли объединению в интегральную обобщенную массу, объединяющую на каждый текущий момент времени не менее чем восемь выходных порций. Далее произвели передачу усредненной массы твердого предпродукта на составление товарных партий умеренно активированного угля. Составление товарных партий предполагало проведение фракционирования предпродукта. Фракционирование шло за счет подвержения предпродукта условному ситу-процессу, определяемому ячейкофактором с характеристическим номером 3,6 мм. В результате фракционирования технологический передел перешел в состояние подситового и надситового фракционатов. Подситовый фракционат направили на составление весового нетто-фасоната. Надситовый фасонат направили на крошение, которое могло быть проведено, например, в многовалковой дробилке. В результате крошения технологический передел перешел в состояние мелкого дезинтеграта-дробленки. Полученный передел подвергли сепарированию, которое шло за счет вовлечения дезинтеграта в условный сито-процесс, определяемый ячейкофактором с характеристическим номером 3,6 мм. В результате сепарации технологический передел перешел в состояние подситового и надситового сепараторов. Надситовый сепарат подвергли рециклу на дораскрошивание. Подситовый сепарат направили на объединение с подситовым фракционатом для образования целевого продукта. Предпринимаемые совмещенные пироиз и активацию производили как и обособленную термовыдержку и охлаждение с предусмотрением их сопровождения принудительным формированным электрозаземлением массы имеющих место технологических переделов. Течение указанного электрозаземления инициировали потенциалом заданного напряжения. Задаваемое напряжение устанавливали соответствующим минимальному пределу в допустимом интервале величины, в частности равным 0,1 В. Произведенный активированный уголь подвергли испытаниям. В результате испытаний было установлено, что суммарный объем пор по влагоемкости был доведен в полученном угле до 1,21 см3/г, активность по составляющей способности в растворе йода была доведена до 30% (оптич). Пример 2. Реализующий предложенный способ технологический процесс вели при наличии соответствия всех режимов и параметров примеру 1, за исключением того, что напряжение обеспечивающего принудительное электрозаземление потенциала устанавливали соответствующим максимальному пределу в допустимом интервале величин, в частности равным 50 В. В результате произведенных испытаний было установлено, что суммарный объем пор по влагоемкости был доведен в полученном угле до 1,27 см3/г. Активность по осветляющей способности в растворе иода была доведена до 33%. Пример 3. Реализующий предложенный способ технологический процесс вели при наличии соответствия всех режимов и параметров примеру 1, за исключением того, что напряжение обеспечивающего принудительное электрозаземление потенциала устанавливали соответствующим промежуточному уровню в допустимом интервале величин, в частности равным 10 B. В результате произведенных испытаний было установлено, что суммарный объем пор по влагоемкости был доведен в полученном угле до 1,32 см3/г. Активность по осветляющей способности в растворе йода была доведена до 36%. Положительные результаты, достигнутые в соответствии со всеми приведенными примерами реализации предложенного способа, сведены в сопоставительную таблицу, в которой они даны в сравнении с характеристиками активированного угля марки ДАК, производимого по ГОСТ 6217-74, без предусмотрения принудительного электрозаземления массы имеющих место технологических переделов. Из представленной таблицы видно, что наилучшие результаты были достигнуты при реализации предложенного способа в соответствии с примером 3. Техническим преимуществом предложенного способа по сравнению с прототипом является обеспеченность улучшенной управляемости ходом технологического процесса.Формула изобретения
Способ производства древесного активированного угля, включающий сушку, пиролиз и активацию древесной массы с использованием в качестве активирующего агента летучих пиропродуктов, отличающийся тем, что пиролиз и активацию осуществляют как совмещенный процесс, следующий после сушки исходного древесного сырья, причем после совмещенных пиролиза и активации производят термовыдержку при температуре совмещенных пиролиза и активации с предпринятием последующего охлаждения, и совмещенные пиролиз и активацию, а также термовыдержку и охлаждение сопровождают электрозаземлением при потенциале 0,1 - 50 В.РИСУНКИ
Рисунок 1, Рисунок 2, Рисунок 3MM4A - Досрочное прекращение действия патента СССР или патента Российской Федерации на изобретение из-за неуплаты в установленный срок пошлины за поддержание патента в силе
Дата прекращения действия патента: 29.03.2006
Извещение опубликовано: 20.03.2007 БИ: 08/2007
www.findpatent.ru
Справочная информация, Китай
Активированные угли могут быть получены из разнообразного углеродсодержащего сырья - древесины, каменного и бурого угля, торфа и т. п. В промышленном производстве активированных углей в качестве сырья чаще всего используется каменный уголь, скорлупа кокосовых орехов и древесина.
Активированный уголь – это адсорбент Свойства адсорбента зависят от:
- площади поверхности,
- размера пор,
- структуры распределения пор.
Адсорбируемое вещество – это вещество, которое должно быть адсорбировано (удалено из воды). Очень важно знать характеристики адсорбируемого вещества, так как по ним можно установить размеры и конфигурацию молекул адсорбируемого вещества. Знать размеры молекул важно по трем причинам: с ростом размеров молекул падает растворимость вещества; с ростом размеров молекул падает адсорбция, так как молекулы не могут проникнуть в поры адсорбента; чем больше молекулы, тем больше требуется времени для их прохождения в поры.
Активированный уголь обычно применяется в трех формах:
- порошковый AC (PAC),
- гранулированный AC (GAC),
- прессованный AC (EAC).
PAC в основном состоит из частиц, меньших 80 mesh (mesh – ячейка, 80 mesh соответствует диаметру ячеек в 0,177 мм) и используется в основном для очистки жидкостей в пекарной промышленности. PAC смешивается с водой и после адсорбирования примесей пропускается через механический фильтр или осаждается.
GAC в основном формируется из частиц угля больших 50 mesh (0,297 мм) и используется для очистки жидкостей (воды и жидких продуктов) и газов. Иногда отработанный GAC (для некоторых применений) может быть реактивирован и вновь использоваться.
Зерна EAC производятся в форме цилиндров и используются для очистки газов, в качестве катализатора и при восстановлении золота. Способ применения EAC аналогичен GAC. Зерна EAC тяжелее гранул GAC. EAC, как и GAC, может быть реактивирован и вновь использоваться.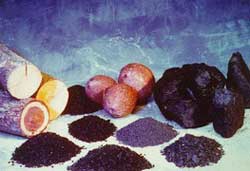
Производство активированного угля и его применение
Сначала углеродсодержащее сырье подвергают карбонизации - обжигу при высокой температуре в инертной атмосфере без доступа воздуха. Однако полученный карбонизат обладает плохими адсорбционными свойствами, поскольку размеры его пор невелики и внутренняя площадь поверхности мала. Поэтому карбонизат подвергают активации для получения специфической структуры пор и улучшения адсорбционных свойств.
Лучшее сырьё для производства активированного угля – опилки. Для получения 5-6 тонн активированного угля надо 50-52 куб.м в день, 1400-1500 куб.м в месяц, толщина фракции:10—80 мм зольность:≤2% влажность:30% Лучше использовать сосновые и еловые опилки. Хороший уголь можно получать из бурого угля и торфа верхового, несколько хуже по качеству уголь получается из низового торфа и перемолотых стеблей соломы, кукурузы, тростника и других травянистых растений.
Сложнее работать с каменными углями, так как при переходе температуры в 450 градусов Цельсия, каменный уголь становится полужидким и текучим. Происходит его спекание и дальнейшее коксование, а не активация. То есть процесс должен находится под постоянным контролем персонала.
АктивацияАктивация углей может осуществляться двумя способами.
Первый способ посредством обработки водяным паром.
Мы производим оборудование по активации водяным паром.. Активация водяным паром проводится при температуре 700 - 1000 °C в строго контролируемых условиях. При этом на поверхности пор происходит химическая реакция между водяным паром и углем, в результате чего образуется развитая структура пор и увеличивается внутренняя поверхность угля. С помощью такого процесса можно получать угли, обладающие различными адсорбционными свойствами.
Активация водяным паром позволяет получать угли с внутренней площадью поверхности до 1500 м2 на грамм угля. Благодаря этой огромной площади поверхности активированные угли являются прекрасными адсорбентами. Тем не менее, не вся эта площадь может быть доступна для адсорбции, поскольку крупные молекулы адсорбируемых веществ не могут проникать в поры малого размера.
Второй способ обработка углей специальными химическими реагентами для активации, этот способ значительно дороже.
Активирующая составляющая
Сырье |
Объем добавок, не менее, согласно гостам КНР |
Молекулярная формула |
Стандарт |
Фосфорная кислота |
1% - 900 кг |
h4PO4 |
GB2091—80 |
Серная кислота |
1% - 900 кг |
h3SO4 |
GB625—89 |
Соляная кислота |
1% - 900 кг |
HCL |
GB622—89 |
Вода |
40 тонн на тонну угля |
h3O |
|
Углесодержащие вещества активируются высокотемпературным (800-1000°C) паром или обезвоживающими химикатами. Химическая активация заключается в нагреве исходного материала до 400-500°C в присутствии сильного химического обезвоживающего агента (фосфорная кислота, хлорид цинка или др.). Большинство материалов после этого подвергается кислотной промывке. Кислотная промывка удаляет металлы, золу и другие растворимые в воде примеси (например, кремний), которые могут вымываться при эксплуатации.
Структура порВ активных углях различают три разновидности пор — макропоры, переходные поры и микропоры, которые отличаются механизмом сорбции паров и газов.
Макропоры — это наиболее крупные поры. У них очень большой верхний предел радиуса кривизны (около 2000 нм), нижний предел — около 100 нм. Заполнения их вследствие капиллярной конденсации паров не происходит. Удельный объем макропор находится в интервале 0,2—0,8 см3/г, удельная поверхность 0,5—2 м2/г. Следовательно, адсорбция на поверхности макропор не представляет практического интереса. Их поверхность равноценна поверхности непористых углеродных сорбентов с близкой химической природой, а сами поры выполняют роль каналов для проникновения веществ в глубь сорбента.
Переходные поры значительно меньше макропор, радиус их кривизны от 1,5 до 100 нм, т. е. он значительно больше, чем размеры адсорбируемых молекул. Удельный объем переходных пор сравнительно невелик — от 0,02 до 0,10 см3/г, удельная поверхность от 20 до 70 м2/г. Заполнение объема этих пор уже возможно капиллярной конденсацией паров. При давлениях (концентрациях) ниже соответствующих капиллярной конденсации на поверхности переходных пор может происходить адсорбция паров.
Микропоры — самые мелкие поры активных углей, имеющие радиус меньше 1,5 нм, соизмеримый с размером адсорбируемых молекул. В отличие от первых двух видов нор, в микропорах весь объем пор представляет пространство, в котором проявляется адсорбционное поле, поэтому представление о послойном заполнении и о поверхности микропор теряет физический смысл. Удельный объем микропор активных углей 0,20—0,60 см3/г. Таким образом, микропорам принадлежит определяющая роль в процессах адсорбции.
Область применения активных углей
Химическая промышленность:
- Очистка органических кислот
- Адсорбция органических соединений из растворов
- Рекуперация органических растворителей
- Адсорбция паров и газов органических веществ
- Очистка минеральных масел
- Очистка электролитов, гальванопроизводство
- Изготовление электродов
- Основа палладиевого катализатора
- Основа катализатора для синтеза винилхлорида
- Основа катализатора для синтеза винилацетата
Пищевая промышленность:
- Очистка ликероводочных изделий
- Обесцвечивание сахарных сиропов
- Очистка крахмалопаточных растворов
- Очистка ксилита и ксилитана
- Производство органических кислот (лимонная, молочная и др.)
- Очистка и отделка растительного и животного масла и жиров
- Очистка ликероводочных изделий
- Слабоалкогольных и газированных напитков
- Очистка крахмалопаточных растворов, глюкозы, глюкозо-галактозных сиропов, лактулозы
- Осветление и дезодорация пищевых масел и жиров
- Производство лимонной, молочной, пропионовой и др. органических кислот
- Обесцвечивание сахарных сиропов, ксилита
- Производство карамели
Фармацевтическая промышленность:
- Очистка растворов при производстве мед препаратов
- Производство синтетического каучука и поливинилхлоридных смол
- Основа при изготовлении катализаторов
- Гемосорбент для медицинской промышленности
- Носитель БАВ
- Производство антибиотиков
- Производство кровезаменителей
- Производство угольных таблеток
- Производство глюконата кальция, хлористого натрия
- Производство таблеток «Аллохол»
- Производство церебролизина
- Производство гепарина
Промышленная очистка
- Очистка паров и газов
- Сероочистка и очистка технологических растворов при добыче и переработке газа
- Очистка растворов, паров, газов при переработке нефти
- Производство минеральных масел, химреактивов и лакокрасочных изделий
- Ликвидация разливов нефти и нефтепродуктов
- Очистка парового конденсата и котловых вод
- Очистка промышленных газов и вентвыбросов
- Производство стекловидного тела
- Очистка вентвыбросов и воздуха от вредных газов
Топливно-энергетическая промышленность:
- Очистка парового конденсата
- Очистка оборотных вод
- Нефте - газодобывающая и перерабатывающая промышленность:
- Сероочистка и очистка технологических растворов при добыче и переработке газа
- Очистка растворов, паров, газов при переработке нефти
- Ликвидация разливов нефти и нефтепродуктов
Металлургическая промышленность:
- Извлечение золота из цианистых пульп и других растворов
- Флотация руд полезных ископаемых
- Извлечение драгоценных металлов
Охрана окружающей среды:
- Подготовка питьевой воды
- Снаряжение фильтров доочистки питьевой воды
- Очистка сточных вод
- Применение активированного угля в водоподготовке
- Предназначен для удаления растворенных органических веществ и улучшения вкусовых качеств воды (удаление запахов и привкусов).
© Авторское право принадлежит «Мега Пауэр Гонконг Груп Лимитед».Все права защищены. E-mail: [email protected]. Tel: 86 13903612274В случае использования ссылка на сайт обязательна
asia-business.ru