Секреты производства тротуарной плитки с помощью вибролитья. Технология изготовления плитки тротуарной методом вибропрессования
Технология производства тротуарной плитки методом вибролитья
Дороги и тротуары при помощи брусчатки выглядят намного красивее, чем асфальтированные. Ранее мастера по созданию дорог пользовались необработанным камнем, но он имел острые края, сколы и асимметричную форму. Дорожки, которые выкладывались из такого камня, не приносили удобства. Со временем люди начали придумывать различные методы его обработки, в современном мире популярностью пользуется технология производства тротуарной плитки методом вибролитья.
Производство тротуарной плитки – одна из самых крупных промышленных отраслей, где осуществляют свою деятельность большие заводы и фабрики, а также частные предприятия. Этот результат получился потому, что плитка пользуется огромным спросом.
Методика производства тротуарной плитки
Существуют следующие способы производства тротуарной плитки:
- производство тротуарной плитки методом вибропрессования;
- выполнение изделий вибролитьем.
В процессе производства тротуарной плитки методом вибропрессования и вибролитья всегда используется компонент, который отвечает за прочность и долговечность готового изделия. С помощью добавления красителей плитка получается различных цветов.

Краситель поможет сделать плитку того цвета который вам необходим
Технология производства тротуарной плитки вибропрессованием отличается от процесса литья. В этом случае оборудование потребуется сложной конфигурации и функциональности.
Пресс-формы с готовым раствором обязаны находиться в вибропрессе, но в большинстве случаев это условие выполняет технологическая установка. Производство вибропрессованной тротуарной плитки исключает ручной труд, изготовление иного вида очень сложное.
Технология производства тротуарной плитки методом вибролитья потребует механизмы, приобрести их мастера могут по доступным ценам, а некоторые из них специалисты рекомендуют сделать самостоятельно в домашних условиях. Многие предприниматели начинали свою деятельность именно с такого процесса.
Технология вибролитья
Технология вибролитья подразумевает заливание пресс-форм бетонным раствором, который представляет собой высокое водоцементное соотношение.

Технологический процесс вибролитья
Процесс вибролитья тротуарной плитки образуется следующими операциями:
- Замес бетонного раствора – эта операция подразумевает перемешивание всех компонентов: цемента, песка, щебня, пластификатора и красителя. С помощью красителя специалисты добиваются подходящего цвета. Пластификатор повышает подвижность раствора без добавления воды. Обычно применяется 2 состава бетона. Один из них нужен для фактурного слоя. Что касается красителя, то он добавляется только в туда.
- Формирование в вибростоле – бетонная смесь заливается в пресс-формы, установленные на виброуплотнителе. После чего включается электрический мотор, стол начинает подавать вибрации. Смесь уплотняется, образуя пустоту и избыток. Задача мастера по регулировке всей работы, чтобы в дальнейшем плитка была одинаковая.
- Процесс вызревания – залитые пресс-формы обязаны стоять на ровном столе несколько дней без движения. Сокращать сроки не рекомендуется, в противном случае прочность изделия будет низкая, плитка начнет крошиться. Поэтому необходимо приготовить несколько комплектов форм, чтобы свободные участки технологической линии не оставались без работы.
- Распалубка и выбивание из пресс-формы готовое изделие. Для интенсивной работы формы необходимо поместить в горячую воду на несколько минут. После чего их переносят на отдельный стол, который предназначен для распалубки. Принцип его работы аналогичен вибростолу. С помощью вибрации плитка постепенно отходит от формы.
- Отмывание форм от раствора. Для этого необходимо сделать слабый раствор соляной кислоты. После чего поместить туда формы. С помощью этой процедуры пресс-формы специалисты могут использовать для следующей заливки.
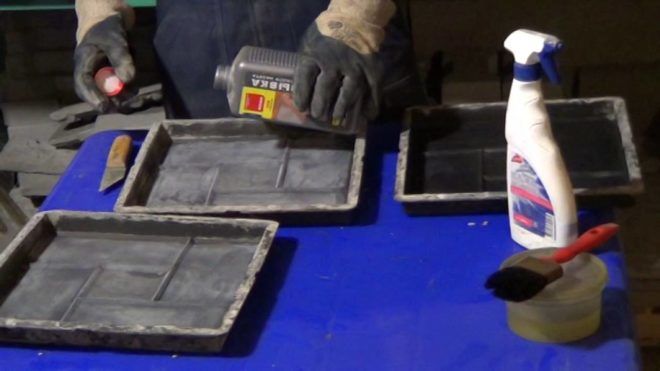
После использование обязательно помойте пресс-формы это продлит их срок службы
Плитка, которая была изготовлена методикой вибролитья, по итогу становится гладкой. Ее применение не предусмотрено для температуры ниже нуля. Но ее преимущество заключается в том, что оформленные ею дорожки и тротуары довольно оригинальны.
У такой методики также имеются свои достоинства:
- готовая плитка имеет разные формы;
- тротуарную плитку специалисты могут сделать разного цвета;
- мастера также могут сделать материал с роскошной глянцевой поверхностью.
Производство тротуарной плитки
Состав бетона
С помощью состава бетонного раствора есть возможность определить эстетику готового покрытия и эксплуатационные особенности изделий. Тротуарной плиткой пользуются не только в частных загородных домах для сооружения дорожек, но и при оформлении городских улиц.
Бетонный раствор, из которого будет изготовлена плитка, обязан соответствовать требованиям ГОСТа. По этому принципу все бетонные изделия обязаны производиться из мелкозернистого и тяжелого бетона, обладать прочностью. А также они обязаны быть надежны в эксплуатации при низких температурах и поглощать влагу.
Состав для смеси тротуарной плитки, которая производится вибролитьем, имеет отличие – огромное число заполнителя, в качестве него часто используют щебень. В таком случае размер зерен принимается от 5 до 20 мм. Производство этим методом предусматривает присутствие подвижности раствора, поэтому здесь присутствуют эффективные стабилизаторы и пластификаторы.
Если в состав входят такие породы щебня, как гранит, количество цемента часто уменьшается, ведь с помощью каменного каркаса структура будет плотной и прочной.
Основные пропорции по этой технологии очень похожи с рецептом тяжелого бетона. Если имеются особенные формы, то плитку мастера могут изготовить запросто самостоятельно. Это относится и к раствору, который специалисты замешивают гравитационным смесителем.
Подборка соотношения компонентов
При производстве тротуарной плитки самостоятельно не рекомендуется использовать классическую схему. Для простоты производства плитки своими руками необходимо повысить подвижность раствора. В таком случае быстрота вибрации станет меньше, соответственно, состав бетонной смеси немного изменится.
Главные пропорции бетонного раствора, которые используют для заливания тротуарной плитки, могут быть следующие: часть массы цемента, 1,5 части массы песка, 2,5 части массы щебня, 0, 35 части массы воды, пластификатор и пигмент.

Материалы для изготовления плитки
Если повысить класс бетона, то пропорционально увеличится расход цемента, а пропорции заполнителей станут ниже. По итогу состав раствора будет изменен, но искусственный камень останется плотным, сохраняя полный набор свойств.
Подбор материала
Чтобы готовая плитка была гарантированно плотной, стойкой по отношению к морозам и водонепроницаемой, главное – подобрать материалы качественные.
Главный компонент любого бетона – цемент. В таком случае необходимо выбрать среднеалюминатный, который содержит минеральные добавки не больше 5%, а класс надежности должен быть 42,5.
Мытый карьерный песок будет в виде мелкого заполнителя. Модуль крупности должен составлять 2–2,5. Он относится к строительному песку 1 класса. С помощью этого компонента расход раствора становится меньше и, соответственно, стоимость его намного ниже при довольно высоких коэффициентах качества.
Гранитный щебень применяется вместо крупного заполнителя. Размер его зерен должен быть от 3 до 10 мм.
При высокой подвижности раствора этот материал становится очень прочным, надежным и долговечным. По цене он довольно дорогой, поэтому лучше купить обычную смесь, диаметр зерен которого составляет от 5 до 20 мм. При этом крупный заполнитель необходимо убавить.
При помощи этого способа при образовании каменного каркаса будет большая подвижность и однородность.
Производство в домашних условиях
Перед тем как начать производство тротуарной плитки, требуется подготовить место для хранения и формирования готовых изделий. Уплотнение обязательно даже при довольно высокой подвижности раствора. Вибраторы подходят как собственного изготовления, так и погружные.
В процессе перемешивания всех составляющих, для получения необходимой смеси для начала засыпается песок, после чего вода с добавками и цемент. Последним компонентом необходимо добавлять щебень. По времени смешивание компонентов занимает не более 3 минут. Раствор обязан соответствовать однородной массе.
После того как смесь будет расформирована по пресс-формам, ее нужно обязательно закрыть пленкой, она не даст влаге испаряться из изделия. Спустя 3 дня нужно начинать распалубку и переносить изделие на стеллаж с влажными опилками.

Распалубка процесс извлечения плитки с формы
Преждевременно доставать тротуарную плитку, вибролитье которой претерпело нарушений процесса, не стоит.
Эта технология изготовления тротуарной плитки подразумевает поддержания температуры на отметке 17 градусов. Через 28 дней плитка будет довольно прочной и готовой к использованию, но в течение всего этого времени ее необходимо регулярно увлажнять. Процесс вибролитья, технология которого подразумевает усадку смеси в форме, затягивается на целый месяц, но результат такого производства радует мастеров.
Видео по теме: Технология производства тротуарной плитки
promzn.ru
Изготовление тротуарной плитки
Производство тротуарной плитки – идея бизнеса. Технологии изготовления тротуарной плитки.
.Тротуарная плитка не только декоративный, но и технологичный материал, используется для укладки тротуарных дорожек любых конфигураций. Бетонная тротуарная плитка производится двумя методами:
- Метод вибролитья в формах с использованием пластификатора.
- Метод вибропрессования смесей с низким водо содержанием.
В обоих способах применяется механическое воздействие для плотной укладки смеси бетона, что позволяет получать плитку с низкой пористостью благодаря минимальному содержанию воды в бетоне. Чаще при производстве качественной бетонной плитки используется метод вибролитья.
Как начать бизнес на производстве бетонной тротуарной плитки.
Для производства плитки методом вибролитья подойдёт помещение от 100 м², с трёхфазным электроснабжением, из оборудования понадобится:
- Вибростол формовочный.
- Распалубочный стол.
- Комплект пластиковых форм.
- Бетономешалка принудительного типа.
- Ёмкость с подогревом для воды.
- Ёмкость для промывочного раствора.
Для приготовления бетона используется портландцемент М500 (в клинкере содержание СЗА не должно превышать 8%). Цемент нужно использовать одного производителя, разные сорта цемента при окраске красителем дают разные оттенки готовой плитки. Также используется песок с модулем крупности от 2, щебень фракции 5 – 10 мм, марка щебня по прочности на сжатие 1000, морозостойкости не ниже 200, добавка пластификатор, воздухововлекающая добавка, пигмент, вода.
Расход материалов для приготовления бетонной смеси на 1м². плитки (толщина плитки 6 см):
- цемент – 36 кг,
- песок — 45 кг,
- гранитный щебень фр. 5 – 10 мм – 45 кг,
- пластификатор – 0,7% от массы цемента,
- пигмент – 2,5 от массы цемента,
- воздухововлекающая добавка — до 0, 02 % от массы цемента.
Технология изготовления тротуарной плитки вибролитьём.
Процесс производства тротуарных плиток можно разделить на этапы:
- Смазка пластиковых форм.
- Приготовление бетона.
- Заполнение бетоном пластиковых форм.
- Вибролитьё.
- Выдержка заполненных форм.
- Распалубка форм.
- Подготовка форм к новой заливке (мойка, смазка).
1.Подготовка форм.
Предварительно перед началом заливки, формы для последующей качественной распалубки следует смазывать специальной смазкой. Такую смазку можно приобрести, или изготовить самостоятельно.
Смазку для пластиковых форм можно приготовить, смешав 30% машинного масла и 70% дизельного топлива.
2.Приготовление бетона.
При приготовлении бетона предпочтительней использовать бетономешалку принудительного действия, для более качественного перемешивания раствора.
Состав раствора на одну бетономешалку:
- Гранотсев – 50л.
- Цемент М 400 – 25л.
- Песок – 25л.
- Вода – 25л.
- Пластификатор С3 – 100гр.
- Пигментный краситель.
3.Заливка.
Формы устанавливают на вибростол, и равномерно заполняют раствором, формы находятся на вибростоле 15 – 20 секунд. Излишки бетона убирают шпателем.
4.Сушка и хранение.
После процесса заполнения бетоном, формы укладывают на ровную площадку на 48 часов для сушки. Важно чтобы поверхность площадки для сушки была ровной, если формы будут стоять под уклоном, бетон будет перемещаться, и плитка будет иметь не одинаковою толщину. Такую плитку практически невозможно уложить равномерно.
5.Распалубка.
После сушки, необходимо из формы извлечь готовую плитку. Для удачного извлечения плитки и повышения срока службы пластиковых форм, их помещают на 5 минут в ёмкость с горячей водой (60 — 70°С).
Затем плитку выбивают на распалубочном столе специальными приспособлениями.
После извлечения плитки, формы очищают от остатков бетона, моют в 7 — 10% ном растворе соляной кислоты, и окончательно промывают обычной водой. После просушки формы обратно смазывают смазкой для новой заливки бетона.
Технология изготовления тротуарной плитки методом вибропрессования.
В основе этой технологии стоит метод виброуплотнения полусухой бетонной смеси с низким содержанием цемента и воды.
Такой метод позволяет производить тротуарную плитку с высокими эксплуатационными свойствами с водопоглощением менее 5%, и повышенной морозостойкостью F-200 — F-300. Плитка, изготовленная на вибропрессе, имеет намного больший ресурс по сравнению с вибролитьевым методом.
При изготовлении тротуарной плитки методом вибропрессования понадобится оборудование:
- Вибропресс гидравлический.
- Технологические поддоны.
- Бетономешалка принудительного типа.
Технология изготовления тротуарной плитки вибропрессом.
1.Приготовление бетона в бетономешалке:
2.Формование.
Смесь бетона загружается в матрицу вибропресса, пуансон опускается, включаются вибраторы на 5 секунд, происходит уплотнение формовочной массы. Матрица и пуансон подымаются рычагом, на виброплощадке стоит поддон с отформованной плиткой. Технологический поддон с плиткой переносится на сушку, на его место ставится новый поддон.
Тротуарная плитка, изготовленная методом объёмного вибропрессования, полностью соответствует ГОСТу 17608-91 по таким характеристикам как водопоглощение, морозостойкость, прочность, истираемость. По сравнению с литьевой плиткой для изготовления расходуется меньше цемента, пластификатора, модифицирующих добавок, что делает себестоимость изготовления такой плитки заметно ниже, при этом срок службы вибропрессованной плитки намного дольше литьевой.
Основным преимуществом плитки изготовленной методом вибролитья является её внешний вид, которого добиться вибропрессованием достаточно сложно.
Бизнес на производстве тротуарной плитки не требует больших вложений в оборудование, рентабельность производства составляет 100 – 130%
Популярные бизнес идеи
idei-biz.com
Выбропрессование тротуарной плитки: технологическое описание процесса
Технология производства тротуарной плитки вибропрессованием намного проще, нежели метод: вибролитье. Это происходит из-за того, что данный процесс требует намного меньшего участия человека – вся работа выполняется вибропрессом, который полностью управляется автоматически. Работник только лишь засыпает в машину все необходимые материалы, а на конечном этапе производства забирает готовую плитку. Машины же могут иметь различия внешние, а также отличаться по техническим характеристикам, но сам процесс производства тротуарной плитки от этого не измениться.
Технология вибропрессования
Мелкоштучные изделия из бетона получается изготовлять благодаря технологии обьемного вибропрессования. Тем самым обеспечивая им разнообразную форму, толщину, цветовую палитру. Плитки получаются в соответствии строгой геометрической форме и параллельной поверхности, тем самым обеспечивая продукции высокий уровень прочности и точности в обозначенных размерах. При использовании в процессе работы данной техники, можно уменьшить до минимума влияния человеческого фактора, а также существенно увеличить темпы производства. Вибропрессованием изделия можно производить не только на песчано-бетонной основе, но и также применять разные материалы, которые представляют собой отходы основного производства, такие как шлаки от топлива, осколки кирпича, деревянные опилки. Та тротуарная плитка, что изготавливается сегодня на профессиональной технике, прослужит более 16 лет. Подробнее о процессе можно узнать в видео интернет-сообществах, посвященных строительной тематике.

Вибропресс
Есть два основных метода изготовления плитки из бетона:
- Вибропрессование низкосодержащих смесей жесткого типа;
- Вибролитье, где в процессе работы будут использованы пластифицирующие добавки.
Не важно, каким методом была изготовлена плитка, готовые бетонные изделия в обоих случаях будут низкопористые, так как процент воды в них минимален, и тем самым обеспечивая плотную укладку. Стоит сказать, что нельзя выделить какой-то один преимущественный метод изготовления. Для разных областей и условий применения плитки соответствуют и различные технологии.
Технологические особенности производства тротуарной плитки
Данный процесс – это укладка готовой бетонной смеси в специальную пресс-форму, что расположена на станине (деталь постоянно находится в процессе вибрации). Далее на бетон опускается пуансон и через определенное время давящими движениями полностью уплотняет смесь. Также в непрерывной вибрации работает и пуансон. Как только основные детали поднимаются вверх – можно забирать уже готовые плитки. Данный метод очень высокой производительности и отличается тем, что может работать на полной автоматизации. Такая технология в работе помогает легко выпускать большие объемы продукции, ведь здесь не задействован ручной труд в большом количестве. В сети интернет можно посмотреть множество информативных видео о том, как работает и как устроена данная машина.

Готовая тротуарная плитка из бетона
При помощи стационарных вибропрессов происходит плиточная формовка.
Так как в работе используются полусухие бетонные смеси, которые имеют пониженное водоцементное отношения, то готовые плитки обладают высокой прочностью, повышенным уровнем морозостойкости и низкий процент водопоглощения (менее пяти). Такие изделия имеют точные геометрические размеры и стабильные основные эксплуатационные параметры.
Основные детали машини – матрица и пуансон. На поверхность пуансона нанесен определенный рисунок, который в свою очередь будет отпечатан на тротуарной плитке, ее лицевой части. Задача матрицы – следить за тем, чтобы стенки изготавливаемого изделия формировались без дефектов. Плитки изготавливаются на специальных поддонах, которые сменяются и подаются на участки суши.
Тротуарная плитка, различные по форме бордюры и водоотливы – вся эта продукция изготавливается при помощи метода: вибролитье. При покупке вибропресса стандартной комплектации, его стоит оснастить еще некоторыми деталями, ведь без них он будет неавтоматизированный и его уровень производимости будет крайне низким. Подробнее о том, как автоматизировать вибропресс, можно узнать в обучающих видео на страничках строительных сайтов.
Основные мифы, относительно работы вибропресса в производстве
- Первое заблуждение: Ценовая политика данной машины очень высока и у предприятий малого бизнеса нет возможности его приобрести.
- Второе заблуждение: Высокая стоимость сменных деталей машины, и для того, чтобы идти в ногу со временем и выпускать новые плитки – нужно постоянно докупать и обновлять оснастки.
- Третий миф: Управление вибропрессом – дело сложное, к которому нужно привлекать только профессионалов с высокой квалификацией.
- Ошибка номер четыре: для того, чтобы переналадить машину на изготовление новых плиток необходимо нанимать обученных специалистов.

Модель вибропресса 800 мини
Но не стоит поддавать панике наперед, нужно подробно проанализировать процесс изготовления тротуарной плитки, и вскоре выяснится: все вышеперечисленные пункты – все лишь стереотипы, придуманные людьми, которые не понимают нюансов работы современных машин вибропрессования на небольших заводах, что специализируются на выпуске всеразличных строительных материалов. Также, в нижепредставленном видео можно найти подробную инструкцию о том, как своими руками сделать станок для выпуска бетонных изделий:
Поэтапная схема технологии производства тротуарной плитки
Данная схема будет рассмотрена на примере классической сборки вибропресса с рычажным типом управления. Данная машина оснащена вибраторами электромеханического типа с рычажными приводами подъема двигающихся деталей пресса. Специалисты условно разделяют процесс изготовления продукции на три основных этапа:
- Приготовление бетонной смеси
Для данного процесса необходим бетоносмеситель. Если изготовляются однослойные плитки, то одного будет достаточно, соответственно, двухслойные изделия требуют работы двух бетоносмесителей. Когда бетон уже приготовлен – смесь далее отправляется в матрицу пресса.
- Формование плитки
Далее в работу подключается необходимая деталь – пуансон, под действием виброимпульсов которого смесь уплотняется. Процесс выбропрессования не занимает больше 4-6 секунд. Следующий шаг – двигающиеся детали при помощи рычажного управления поднимаются вверх, и на площадке с технологическим поддоном можно наблюдать отформированные плитки. При необходимости процесс изготовления повторяется: поддон отправляется на сухой участок, а на его место сразу же загружается следующий.
- Просушивание плиток
На участке суши бетонные плитки должны обязательно быть обработаны тепловлажным воздействием. Для этой цели как нельзя лучше подойдет водяной пар. Если площадь помещения позволяет, то плитки могут затвердевать на портландцементе, таким образом существенно снижая затраты на обработку изделий тепловым воздействием. Готовыми плитки будут по прошествии 8-9 часов.

Схема изготовления продукции на вибропрессе
Для того чтобы изготовление продукции не просто состоялось, а было качественным и быстрым, необходимо в своем арсенале иметь такой набор оборудования:
- Бетономешатель автоматического управления;
- Пресс-машина рычажного типа;
- Набор специальных поддонов (для того, чтобы на начальных этапах изготовительные работы были менее затратными, можно сделать данные поддоны своими руками, посмотрев обучающие видео в интернете).
Вконтакте
Google+
trotuaplitka.ru
Состав бетона для тротуарной плитки — основные компоненты и тонкости изготовления
Проблема мощения дорог стояла перед людьми всех эпох. Смена сезонов, дожди и отрицательные температуры быстро приводили в негодность любое покрытие. Наиболее стойким к перемене погоды остается натуральный камень, но его использование требует существенных вложений и не гарантирует идеальной поверхности дороги.
Искусственный камень позволяет получить не только долговечное, но и весьма привлекательное покрытие, именно поэтому весьма востребованы бетонные элементы мощения. Состав бетона для тротуарной плитки определяет не только эксплуатационные особенности изделий, но и эстетику будущего покрытия. Тротуар из бетона востребован как при оформлении городских улиц, так и на частных участках.
Основные свойства и способы производства
Бетонная тротуарная плитка, как и любой другой элемент мощения, должна соответствовать требованиям ГОСТ 17608-91. По нормативу все виды изделий должны:
- изготавливаться из тяжелого или мелкозернистого бетона;
- обладать классом по прочности от В22,5;
- отличаться прочностью на растяжение при изгибе не менее 3,2 МПа;
- обладать морозостойкостью не менее F100 и водопоглощением не более 6%.
Кроме того, при производстве тротуарной плитки применяются технологии, позволяющие выпускать изделия в один или два слоя, с использованием пигмента или без него.
Требования к составу
Цемент не должен содержать минеральные добавки свыше 5%, а также трехкальциевый алюминат свыше 8%. Водоцементное отношение не может превышать 0,4, а количество воздуха в смеси должно находиться в пределах 4 – 5%. Для обеспечения высоких показателей по морозостойкости в бетонную смесь вводятся специальные добавки с воздухововлекающим эффектом.
Подобные требования накладывают существенный отпечаток на состав искусственного камня. Рецепт бетона для тротуарной плитки во многом зависит от технологии производства и применяемых материалов. Так, основными способами изготовления элементов мощения считаются вибропрессование и вибролитье.
Специфика прессования с одновременной вибрацией
Наиболее распространенным методом при промышленном производстве тротуарной плитки можно назвать именно вибропрессование. Такая технология позволяет получать значительный объем продукции за рабочую смену, но требует большого опыта работников и оператора, отвечающего за производство бетонной смеси.
Особенности рецептуры
Рецепт искусственного камня для вибропрессования отличается отсутствием инертных заполнителей крупностью более 5 мм. Технология предполагает уплотнение при прессовании смеси с одновременной вибрацией, что сказывается на требованиях по содержанию воды.
Композит для вибропрессования должен быть однородным, но жестким для предотвращения расслоения при уплотнении.
Для создания такой системы крупный заполнитель противопоказан, так как требует большего количества подвижной растворной части для однородного распределения.
Именно поэтому пропорции цемента, песка или отсева, воды, пигментов и добавок существенно отличаются от классических для тяжелого искусственного камня. Такой материал называется мелкозернистым бетоном.
Основные пропорции
Специфика уплотнения смеси не позволяет выпускать подобную плитку в домашних условиях, ведь обеспечить должную нагрузку своими руками очень сложно. Чаще всего пропорции цемента и мелкого заполнителя принимаются 1:3 или 1:4 соответственно, а количество воды не превышает 30% от массы цемента. Для окрашивания изделий применяются минеральные и органические пигменты с дозировкой в пределах 1 – 3% от веса цемента.
Технология вибролитья
Такой способ производства не отличается производительностью, но позволяет выпускать изделия сложной геометрии и рисунка. Благодаря использованию подвижной смеси и умеренному уплотнению, композит заполняет все изгибы формы, поэтому узор любой сложности проявляется четко и практически без изъянов.
Состав раствора
Состав смеси для тротуарной плитки, изготовленной вибролитьем, отличается большим количеством заполнителя, а также возможностью применения щебня с размером зерен 3 – 10 или 5 – 20 мм. В этой технологии важно добиться подвижности смеси, поэтому рецепт отличается присутствием эффективных пластификаторов и стабилизаторов.
Кроме того, при введении щебня из плотных горных пород, например, гранита, количество цемента можно уменьшить, ведь каменный каркас обеспечит получение плотной и прочной структуры бетона.
Фактически состав композита и основные пропорции сырьевых компонентов при производстве тротуарной плитки по технологии вибролитья очень близки к рецептам классического тяжелого бетона. При наличии специальных форм такие изделия несложно произвести в домашних условиях, а изготовление смеси легко осуществить своими руками при помощи гравитационного смесителя.
Подбор базового соотношения компонентов
При производстве тротуарной плитки собственными силами лучше всего отойти от классической схемы. Так, если увеличить подвижность смеси, то можно уменьшить интенсивность вибрации, что существенно упрощает изготовление изделий в домашних условиях. Состав бетона при таком подходе следует немного видоизменить.
Основные пропорции бетона, применяемого для заливки тротуарной плитки можно представить в виде следующей схемы:
- 1 массовая часть цемента;
- 1,5 – 1,7 массовые части песка;
- 2,5 – 3 массовые части щебня;
- 0,35 – 0,4 массовые части воды;
- пластификатор + пигмент.
При увеличении класса бетона пропорционально возрастает расход цемента, и уменьшаются пропорции заполнителей. В результате состав композита меняется, но искусственный камень сохраняет плотную структуру и весь набор свойств.
Выбор материалов
Для создания тротуарной плитки с высокой прочностью, морозостойкостью и водонепроницаемостью важно подобрать материалы соответствующего качества.
Цемент
Основным элементом любого бетона является цемент. Для изготовления элементов мощения следует выбирать среднеалюминатные цементы с содержанием минеральных добавок не более 5%, а также с классом по прочности 42,5. На упаковке подобного вяжущего указана марка ЦЕМ I 42,5 Н или Б. К среднеалюминатным цементам относятся вяжущие с содержанием С3А от 5 до 8%. Узнать содержание алюминатов можно у продавца, спросив паспорт на цемент.
Мелкий заполнитель
В качестве мелкого заполнителя лучше всего применять мытый карьерный песок с модулем крупности 2 – 2,5.
Такой материал относится к пескам строительным первого класса, при его использовании состав бетона отличается меньшим расходом вяжущего и низкой себестоимостью при более высоких показателях качества.
Крупный заполнитель
При использовании крупного заполнителя лучше всего приобрести гранитный щебень с размером зерен 3 – 10 мм. Такой материал обеспечит повышение прочности и долговечности при высокой подвижности смеси. Но его стоимость высока, поэтому можно приобрести стандартную смесь зерен диаметром 5 – 20 мм и скорректировать рецепт, сократив содержание крупного заполнителя.
Такой подход обеспечит высокую подвижность и однородность при формировании каменного каркаса в теле композита.
Самостоятельное изготовление
Производство элементов тротуара своими руками необходимо начать с подготовки места для формовки и хранения изделий. Даже при высокой подвижности полученной смеси после заливки форм их необходимо уплотнить. Подойдут погружные или самодельные вибраторы.
Уплотнение следует вести не более 5 – 10 с, иначе произойдет расслоение смеси и ухудшение внешнего вида элементов тротуара.
Стандартная рецептура
При изготовлении композита с классом по прочности В25 можно использовать следующий состав на 1 м3:
- цемент = 390 – 420 кг;
- песок = 700 – 750 кг;
- щебень = 1000 – 1050 кг;
- вода = 155 – 165 кг;
- пластификатор + пигмент (при желании окрасить изделия).
Технология смешивания
При смешении компонентов сначала загружается песок, затем вода с добавками и цемент, и в последнюю очередь щебень. Перемешивание осуществляется не менее 2 – 3 минут до получения однородного материала.
Тротуарная плитка из бетона такого состава будет обладать интенсивной кинетикой твердения, поэтому очень важно предотвратить потерю влаги с ее поверхности.
Уход за изделиями
После укладки смеси все формы необходимо накрыть пленкой, предотвращающей испарение влаги с поверхности изделий. Через 2 – 3 суток можно произвести распалубку и поместить плитку на стеллажи с влажными опилками или ветошью в помещении с постоянной температурой не менее 17 0С. Изделия необходимо постоянно увлажнять, и через 28 суток они наберут проектную прочность и будут готовы к использованию.
tehno-beton.ru
Технология производства вибропресcованной продукции
Производство ДорСтройЭлемент находится в Кургане, в его основе высокопроизводительная машина отечественного производства «КВАДР». Производство «ДорСтройЭлемент» почти полностью автоматизировано. 3 оператора контролируют весь цикл работ от приготовления формовочной смеси до укладки и складирования готовой продукции на транспортный поддон.
Применение такого метода, как вибропрессование дает возможность изготавливать не только тротуарную плитку, но также водостоки, бордюры, стеновые камни. При изготовлении изделий методом вибропрессования бетонная смесь требует гораздо меньше воды, чем при обычной заливке бетона в формы. Известно, что слишком большое количество воды в бетоне уменьшает его прочность. Полусухое прессование исключает лишнюю влагу, а значит, потом в плитке не будет опасных воздушных полостей и проблем с морозостойкостью.
Условно производство вибропрессованных изделий разделяют на три этапа:
1) Приготовление бетона.
Основными материалами для приготовления смеси служат песок, щебень, цемент, вода и пигменты, если плитка будет цветная. Песок и щебень используются в качестве заполнителя, цемент – как вяжущее вещество. Обычно используется серый цвет, но если необходимо получить яркие, чистые цвета, то используется белый цемент.
Цемент обеспечивает высокую прочность и влагоустойчивость изделий.
Щебень повышает прочность изделия на сжатие, увеличивает его долговечность, уменьшает ползучесть, усадку и расход цемента.
Песок обеспечивает пластичность смеси, уменьшает количество трещин в изделиях и делает их поверхность более гладкой.
Смесь обязательно должна быть жёсткой, в ней должно быть мало воды. Сырьевые материалы взвешиваются на высокоточном оборудовании, на весовых дозаторах с погрешностью не более 1%. Процесс изготовления почти полностью автоматизирован. Оператор задаёт в программу компьютера рецептуру приготовления «теста» для изделий. И затем компьютер сам регулирует подачу цемента, песка, щебня, воды и красителей. Также с его помощью отслеживается уровень влажности и определяется готовность. Для хорошего перемешивания смеси используется специальный бетоносмеситель или, проще говоря, бетономешалка. Раствор вымешивается 5 минут. Готовая бетонная смесь похожа на консистенцию мокрой земли, при сжатии она образует комок.Как только бетон готов, его сразу же переправляют на вибропресс.
2) Формование.
При формировании плитки работают две из частей вибропресса – это матрица (пресс-форма) и пуансон («зеркальное отражение пресс-формы). На поверхность пуансона нанесен узор - рисунок, он и оказывается на лицевой части плитки, формируя её поверхность, а матрица образует стенки плитки.
Полученный полусухой раствор засыпается в матрицу. Вибропресс равномерно и плотно распределяет все частицы смеси по ней, вытесняя пузырьки воздуха. Затем, опускается пуансон и под высоким давлением запускается процесс вибропрессования. Под действием виброимпульсов происходит уплотнение материала. Длится он порядка 20 секунд. Сила пресса такая, что плитка сразу каменеет. За счет этого, удаётся избавиться от лишней воды и воздуха. Сама смесь максимально уплотняется, что придает изделию высокую прочность, низкое водопоглащение и как следствие – морозостойкость. Затем пуансон с матрицей поднимаются, оставляя на виброплощадке технологический поддон с отформованными изделиями. Этот поддон снимается и подаётся на участок сушки, а его место занимает другой и операция повторяется.
3) Сушка изделий.
Важно, что именно на этом этапе достигается желанная прочность продукции. Сформированные изделия уезжают в пропарочную камеру, где подвергаются тепловлажной обработке при температуре 50°C в течение 8 часов. В качестве теплоносителя используется водяной пар. Бетон как клейковина муки, затвердевая, склеивает всю смесь без выпечки. В этом случае после остывания и высыхания они приобретают 70% марочной прочности. На этом этапе с помощью специального оборудования контролируются показатели качества готовой продукции. Сложенную на поддоны плитку фиксируют при помощи упаковочных механизмов лентой и металлическими скобами. В таком виде она набирает прочность на складских площадках ещё 2-3 дня, происходит дозревание продукции. Затем освободившиеся поддоны повторно подаются на формовочный участок и цикл повторяется. За смену с конвейера сходит около 300 кв.м тротуарной плитки или 1000 кв.м бортовых камней.
Мы не останавливается на достигнутом и постоянно совершенствуем качество нашей продукции. Все изделия «ДорСтройЭлемент» жестко отвечают всем требованиям ГОСТ.
xn--45-6kc5ake1a0a.xn--p1ai
Технология производства тротуарной плитки - KeyProd
К тротуарной плитке, изготавливаемой по ГОСТ 17608-91 «Плиты бетонные тротуарные», предъявляются жесткие требования по морозостойкости (не менее 200 циклов замораживания и оттаивания), прочности (не менее 30 Мпа), водопоглощению (не более 5%) и истираемости (не более 0,7 г/см?).
Поэтому создание материала требуемого качества начинается с подбора необходимых качественных материалов для его изготовления.
Для приготовления бетона обычно используют портландцемент М500Д0 (ГОСТ 10178-85) в клинкере которого содержание С3А не должно превышать 8%.
При выборе цемента желательно остановиться на каком-то одном заводе, т. к. при добавлении пигментов в бетон, краситель окрашивает не заполнители (песок и щебень), а именно цементное вяжущее.
Замена поставщика и сорта цемента приводят к тому, что изменяется и конечный цвет полученного после окраски бетона. Причиной этого является разница в первоначальном цвете цемента.
В качестве мелкого заполнителя следует применять строительные пески с модулем крупности не ниже 2, отвечающие требованиям ГОСТ 8736-93.
В качестве крупного заполнителя следует использовать щебень из магматических горных пород (например, гранитный) фракции 5-10 мм, отвечающий требованиям ГОСТ 8267-82.
В качестве поставщиков предпочтительны карьеры, гарантирующие отгрузку щебня гидравлической классификации (промывки) и не содержащего в момент отгрузки фракции мельче 5мм.
Марка щебня по прочности при сжатии должна быть не ниже 1000, по морозостойкости не ниже 200, рекомендуемое содержание в щебне зерен пластинчатой (лещадной) и игловатой формы не более 25% по массе.
Вода для бетонных смесей должна удовлетворять требованиям ГОСТ 23732-79.
Для повышения морозостойкости, прочности и улучшения технологических свойств бетона в бетонную смесь следует вводить комплексную добавку, содержащую пластифицирующий компонент (С-3 или ЛСТ) совместно с воздухововлекающим или гидрофобизующим (СНВ или ГКЖ-94) компонентом.
2. ОРГАНИЗАЦИЯ ПРОИЗВОДСТВА
Для организации производства тротуарной плитки методом литья потребуется как минимум:
• Один бетоносмеситель принудительного действия.
• Формовочный вибростол. Частота вибрации 50Гц Амплитуда вибрации в размахе до 1,5 мм. Эти условия достигаются на предлагаемых нами вибростолах.
• Распалубочный вибростол. При организации небольшого производства плитки несложной формы (квадрат, прямоугольник) можно отказаться от распалубочного вибростола и выбивать плитку вручную, или изготовить приспособление для выбивания на основной стол.
• Ванна с подогревом.
• Ванна для раствора соляной кислоты.
• Парк пластиковых форм, с расчетом на выдержку изделий.
• Стеллажи с ровными полками для раскладки заполненных форм на сушке.
ТЕХНОЛОГИЯ ИЗГОТОВЛЕНИЯ ТРОТУАРНОЙ ПЛИТКИ: ПОДРОБНОЕ ОПИСАНИЕ ПРОЦЕССА
Технология изготовления тротуарной плитки включает в себя несколько основных этапов:
— подготовка форм;
— приготовление бетонной смеси;
— формование на вибростоле;
— выдерживание изделий в течение суток в формах;
— распалубка изделий;
— упаковка и хранение
Подготовка форм
Формы для изготовления тротуарной плитки могут использоваться пластиковые, резиновые и резиноподобные (полиуретановые). Количество циклов формования, которое выдерживают формы, составляет: для резиновых — до 500 циклов, для пластиковых — 230-250, для полиуретановых — 80-100 циклов.
Формы перед заливкой в них бетона смазывают специальными составами или заливают бетон без предварительного смазывания формы. При работе без смазки новые формы обрабатывают антистатиком, после распалубки формы осматривают и при необходимости промывают 5-10% раствором соляной кислоты.
Для смазки форм можно использовать эмульсор, ОПЛ-1 (Россия) и СЯА-3 (Англия).
Для сохранности поверхности формы нельзя использовать смазки, содержащие нефтепродукты.
Наносимый на поверхность форм слой смазки должно быть тонким, так как из-за избытка смазки на поверхности готового изделия остаются поры.
Смазки эмульсор и ОПЛ-1 наносятся кистью перед каждой заливкой, смазку СРА-3 наносят кистью или напылением. Смазки СВА-3 хватает на 2-3 формовки.
Температура при нанесении должна быть 18-20°С.
Пластиковые формы после использования промывают в слабом растворе соляной кислоты (около 5%-7%) после мытья в кислоте необходимо промыть водой.
Приготовление бетонной смеси
Для приготовления декоративного бетона лучше использовать бетоносмеситель принудительного действия.
В основном порядок приготовления смеси не отличается от приготовления обычного бетона. Пигмент подается примерно за 30 секунд до подачи цемента.
Рецептура приготовления бетона
Песок — 1 часть
Цемент (марка 500) — 1 часть
Щебень фракции 5-20 мм — 2 части
Пигмент — не более 5% от массы цемента
Пластификатор — по рецептуре завода-изготовителя.
Ориентировочно расход компонентов бетонной смеси на 100 кв. м. плитки толщиной 6 см составляет:
цемент — 3,6 т,
щебень гранитный фракции 5-10 мм — 4, 5 т,
песок — 4,5 т,
пластификатор С-3 — до 0, 7% от массы цементы,
воздухововлекающая добавка СНВ — до 0, 02% от массы цементы,
пигмент — 2…5% от массы цемента.
В ряде регионов, где есть трудности с доставкой гранитного щебня, можно применять высокопрочный морозостойкий мелкозернистый бетон без использования гранитного отсева. Для приготовления такого бетона применяют портландцемент М500ДО, песок и комплексную добавку, состоящую из микрокремнезема (SiO2 — аморфной модификации) и суперпластификатора С-3. Основным фактором в механизме действия микрокремнезема является реакция взаимодействия диоксида кремния SiO2 с гидроксилом кальция Ca (OH) 2, образующегося при твердении цемента, с образованием гидросиликатов (т. е. как бы дополнительного количества цементного камня). Применение микрокремнезема в количестве 10% от массы цемента и суперпластификатора С-3 в количестве 1% от массы цемента позволяет получать мелкозернистые бетоны с прочностью до 70 МПа и морозостойкостью 300 циклов.
Приготовление пигмента:
Изготовление цветного декоративного бетона невозможно без применения пигментов.
Пигменты должны быть устойчивы к щелочной среде твердеющего цементного вяжущего; кроме того, они должны быть свето— и атмосферостойкими.
Пигменты не должны растворяться в воде затворения. Этим требованиям лучше других отвечают неорганические оксидные пигменты.
С помощью таких пигментов можно получить практически любой тон, и, в первую очередь, приглушенную цветовую гамму, которая свойственна природе.
Добиться получения чистого цвета, например желтого или голубого, можно лишь используя белый цемент.
Количество пигментов, добавляемых в бетон, составляет 2…5% —для пигментов с хорошей красящей способностью, выпускаемых, например, фирмой Байер (Германия) или Усов и Прехезе (Чехия).
Пигменты с более низкой красящей способностью (в основном отечественных производителей) приходится вводить в количестве до 8%.
К недостаткам отечественных пигментов следует отнести и непостоянство цвета у пигментов одной марки.
Следует отметить, что излишнее увеличение тонкодисперсной фракции в виде пигментов может привести к ухудшению качеств бетона (снижению прочности, морозостойкости и т. д. ), поэтому снижение его доли в бетоне при достаточной насыщенности является желательным.
Цвет бетона зависит также и от соотношения воды и цемента, и количества цемента в бетоне.
При твердении бетона избыток воды испаряется и оставляет в бетоне мелкие поры, которые рассеивают свет и «просветляют» бетон.
Чем выше В/Ц, тем светлее кажется бетон.
Поэтому при производстве плитки методом вибропрессования (с очень низким В/Ц), невозможно получить бетон насыщенных цветов.
Неорганические порошковые пигменты (Fe2O3, Fe3O4, FeO (OH), Сr2O3, MnО, ТіО и их смеси) в обязательном порядке перед применением смешивают с водой до образования сметанообразной консистенции и настаивают в таком состоянии не меньше 1 часа для увеличения дисперсности, величина которой и характеризует красящую способность.
Приготовленный краситель может храниться достаточно долго, так как имеет стабильную формулу, но цвет по мере хранения может быть ярче из-за увеличения дисперсности пигмента. Перед добавлением в бетон его перемешивают.
Органические фталоцианиновые голубой и зеленый красители (ГОСТ 6220-76 с изм. 9-92) дают очень насыщенные оттенки бетона и обладают высокой светостойкостью (7-8).
Допускается содержание в бетоне не более 0,5% от массы цемента.
Единственное отличие в их применении заключается в том, что цветной слой бетона приготавливается методом растирания в растворосмесителе или бетоносмесителе лопастного типа.
Ключ к успешным результатам использования пигментов заключается в тщательном контроле.
По возможности необходимо придерживаться следующих правил:
— взвешивать все ингредиенты
— брать цемент в одном месте
— соблюдать стандартное время смешивания
— контролировать содержание воды, учитывая также ее содержание в песке и вяжущем материале
— перед использованием другого цвета очистить все оборудование
— избегать взбалтывания бетонной смеси
— осторожно использовать добавки, которые могут влиять на окончательный цвет и другие свойства бетонной смеси
Методика приготовления жидкого С-3 (CП-3, ПФМ-НЛК) из сухого
Подготовка воды. Налить в емкость воду комнатной температуры (около 20оС). Для ускорения процесса растворения воду нужно подогреть до 30 — 40оС.
Засыпка сухого С-3. Засыпать в емкость сухой С-3 из расчета 35% массы сухого вещества на 65% массы воды. При этом постоянно перемешивать получающийся раствор, например с помощью дрели с насадкой.
Перемешивание. После полной засыпки сухого С-3 раствор следует тщательно перемешать в течение 10-15 минут.
Отстаивание. Для того чтобы органические вещества хорошо растворились нужно дать отстоятся раствору в течение 10 — 15-ти часов (лучше 24 часа).
Повторное перемешивание. После отстаивания раствор следует перемешать еще в течение 10 — 15-ти минут. После этого он готов к употреблению.
Примечание Количество сухого С-3, которое нужно взять для приготовления 1м3 жидкого С-3 определяется по формуле:, где 1000 — вес 1м3 воды, ρ — требуемая плотность жидкого С-3 (обычно 1,18), ν — концентрация сухого вещества в растворе (при плотности 1,18 обычно 0,35), λ — массовая доля воды в сухом порошке С-3 (обычно 0,08).
Количество воды, необходимое для получения 1м3 жидкого С-3 можно рассчитать по формуле:, где С —рассчитанное выше количество сухого С-3 в растворе.
Например: если нужно получить 1м3 жидкого С-3 с концентрацией 35% из сухого порошка с влажностью 8%, то нужно взять 1000 1,18 0,35 / (1 — 0,08) = 449 кг сухого С-3 и добавить 1000 * 1,18 — 449 = 731 кг воды.
Порядок загрузки бетоносмесителя:
Щебень, вода, песок, пигмент, пластификатор.
Цемент (добавить после того как предыдущие материалы образуют однородною массу).
Время от приготовления бетона до его укладки должно быть минимальным, так как большинство пластифицирующих добавок полифункционального действия (т. е. являются ускорителями), особенно важен временной фактор в жаркую погоду
Оптимальный режим перемешивания:
песок + пигмент — 15-20 с;
песок + пигмент + щебень — 15-20 с;
песок + пигмент + щебень + цемент — около 20 с;
песок + пигмент + щебень + цемент + вода + добавки — 1-1,5 мин;
всего — 2-2,5 мин.
Для повышения долговечности бетона, его износоустойчивости и сопротивления удару в бетон можно добавлять также полипропиленовые, полиамидные или стеклянные щелочестойкие волокна длиной 5-20 мм и диаметром 5-50 мкм в количестве 0,7-1,0 кг на 1м3 бетона.
Длина волокон должна соответствовать наибольшему диаметру крупного заполнителя в бетоне. Волокна, обладающие хорошей дисперсией, образуют в бетоне трехмерную решетку, которая значительно повышает прочность на изгиб, ударную стойкость и износостойкость бетона.
Полипропиленовое и щелочестойкое стекловолокна вводят с водой затворения; полиамидное волокно вводят в готовую бетонную смесь, т. е. на последнем этапе, при этом время перемешивания смеси увеличивают на 30 —50с.
При использовании добавки микрокремнезема принимают следующий график приготовления бетонной смеси:
песок + микрокремнезем + пигмент — 30-40 с;
песок + микрокремнезем + пигмент + цемент — около 30 с;
песок + микрокремнезем + пигмент + цемент + вода + добавки — 1-1,5 мин.
Формирование на вибростоле
Разложить формы на вибростоле максимально плотно друг к другу.
Готовая бетонная смесь имеет удобоукладываемость ОК = 3-4 см. Поэтому для ее уплотнения используют кратковременную виброобработку.
После приготовления бетонной смеси ее укладывают в формы и уплотняют на вибростоле.
При производстве цветной плитки в пластиковых формах для экономии пигмента можно применять послойное формование: первый лицевой слой бетона приготавливается с использованием пигмента, второй слой бетона без него.
Для раздельного формования необходимо иметь два смесителя для приготовления бетона первого и второго слоя.
Технология послойного формования.
Приготовить бетон в меньшем бетоносмесителе с пигментом (см. приготовление пигмента), а в большем бетоносмесителе без него.
Разложить (максимально покрывая дно формы) цветной бетон слоем в 1-2 см.
Вкл. вибратор на 5 — 10 сек., бетон должен покрыть дно формы ровным слоем.
Добавить бетон без пигмента в формы столько, сколько необходимо до краев формы, но не меньше. Вкл. вибратор на 5-10 сек.
Срезать металлическим уголком (двигать его углом вперед) лишний бетон, выравнивая его по краю формы.
Первый — фактурный слой обеспечивает качественные основные показатели плитки:
Состав одного м. куб. готового бетона:
цемент — 500 кг щебень с песком (2:1) — 1 м. куб.
пластификатор — 2,5-3,5 кг
краситель — 7,5-12 кг
Второй — основной слой задает плитке желаемую толщину и является основным носителем прочности
Состав одного м. куб. готового бетона:
цемент — 250 кг
щебень с песком — 1 м. куб.
пластификатор — 2,5-3,5 кг
краситель — отсутствует
При другой подвижности бетона необходимо подобрать свое время уплотнения на формовочном столе.
ПРИМЕЧАНИЕ: Амплитуда и интенсивность колебаний столешницы вибростола должна быть умеренной, бетон в формах не должен «кипеть», он должен уплотняться под собственной тяжестью.
Интенсивность вибрации должна быть одинаковой по всей поверхности столешницы, этого можно достигнуть жестким оребрением. Регулировка вибрации проводится путем уменьшения размеров или веса пластин дисбаланса находящихся на якоре электродвигателя под крышками.
Выдержка изделий
После формования изделия в формах — снять формы с вибростола и плотно сложить на поддон слоями, перекладывая листовым материалом (пресс — картон, пластик, жесть) в 10 слоев или установить в штабели высотой 3-8 рядов в зависимости от толщины и конфигурации плитки.
Поддоны с заполненными формами накрыть полиэтиленовой пленкой, для предохранения от высыхания.
Бетон, в зависимости от температуры и состава, набирает прочность в течение 1-2 дней и можно проводить разопалубку изделий (освобождение изделий из форм) …
Температура выдерживания должна быть не менее 15 °С.
Распалубка
Распалубку фигурных изделий производят на специальном выбивочном столике с вибрацией при этом для облегчения распалубки формы с изделиями рекомендуется подогреть 2-3 мин в ванне с горячей водой (температура 60-70 °С).
При этом используется эффект высокого теплового расширения полимеров по сравнению с бетоном.
Для уменьшения трудоемкости виброразопалубочную машину и ванну укомплектовывают длинным кабелем который позволит транспортировать не плитку, а ванну и разопалубочную машину к плитке. Их устанавливают возле поддонов с созревшим бетоном и проводят разопалубку Формы в ванне располагают в горячей воде рядами по 4.
Плитку укладывают на поддоны «лицом к лицу» — «спина к спине».
Технологическая цепочка:
формы с плиткой — ванна,
разопалуб. машина-плитка — на склад,
формы — к вибростолу для последующего цикла.
При небольших объемах, вместо разопал. маш., можно монтировать плиту с отверстием под плитку на штангах высотой 100 мм на вибростоле.
После проведения разопалубки ее снять и использовать его по прямому назначению.
Распалубка квадратных плит и фасадной плитки происходит без каких-либо специальных приспособлений.
Следует отметить, что распалубка без предварительного нагрева укорачивает срок службы формы приблизительно на 30% и может привести к браку готовой продукции, особенно у тонких изделий.
Технология производства тротуарной плитки методом вибропрессования
Технология производства тротуарной плитки методом вибропрессования состоит в формировании бетонных изделий путем виброуплотнения смеси с малым содержанием воды с обязательным последующим пригрузом формующего пуансона.
Процесс проходит на специальных вибропрессах, которые устанавливаются стационарно. Характерной особенностью используемой бетонной смеси является пониженное водоцементное соотношение. Такая характеристика позволяет производить плитку с более высокой прочностью и при этом уменьшать расход цемента. В целом технология производства тротуарной плитки путем вибропрессования позволяет создавать изделия с достаточно высокими показателями морозостойкости (-300F и менее), низким уровнем водопоглощения (менее 5%), четкими геометрическими формами и стабильностью характеристик.
В формировании плитки участвуют две части вибропресса – пуансон и матрица. На поверхности пуансона нанесен рисунок, который и переносится на лицевую сторону плитки. Матрица формирует стенки плитки. Весь процесс формирования изделия происходит на технологических поддонах, которые затем перемещаются на участок, предназначенный для сушки.
В принципе применение метода вибропрессования позволяет изготовлять помимо тротуарной плитки также бордюры, водостоки, стеновые и перегородочные камни.
На сегодняшний день предлагается большое количество самых разнообразных вибропрессов. Но процесс изготовления изделий у всех примерно одинаковый. Так что можно сказать, что технология производства тротуарной плитки путем вибропрессования подразумевает прохождение трех этапов.
Первый шаг – приготовление бетона. На этом этапе требуется дополнительное оборудование – бетономешалка. Справедливости ради надо отметить, что она понадобится и для изготовления литой плитки. При этом если плитка однослойная, можно обойтись одним смесителем, а если двухслойная – понадобится два. Что касается соотношения составляющих смеси, то универсального рецепта не существует. После того, как бетон готов, его подают прямо в матрицу пресса.
Второй этап – формирование изделия. Необходимо отметить, что конкретные действия аппарата на этом этапе будут несколько отличаться в зависимости от модели, но суть состоит в том, что бетонная смесь попадает в матрицу и прижимается сверху пуансоном. Затем включается механизм виброплощадки и вследствие действия виброимпульса происходит уплотнение изделия. Занимает это обычно около 3-5 секунд. Следующий шаг – освобождение плитки от матрицы и пуансона. Зачастую они просто поднимаются, а на технологическом поддоне остается готовое изделие. Теперь его можно перемещать на участок, предназначенный для просушки изделий, а на его место ставить новый поддон.
Третий этап – сушка. Технология производства тротуарной плитки обязательно включает стадию качественной просушки изделий. Дело в том, что именно в этот период достигается необходимая прочность продукции. Обычно применяется два способа просушки – тепловлажная обработка при помощи водяного пара или сушка в производственном помещении. В первом случае потребуются дополнительные расходы, а второй возможен лишь при использовании портландцемента.
После того, как прочность бетона будет составлять 1,5-2,0 МПа (достигается где-то за 5-8 часов) плитку можно снимать с поддонов. При этом поддон отправляется на повторную загрузку.
Таким образом, использование технологии вибропрессования позволяет в достаточно короткие сроки производить большое количество качественной тротуарной плитки. К преимуществам этого метода также можно отнести то, что он в достаточно высокой степени механизирован и, в отличие от литой плитки, не требует большого количества форм для заливки. К тому же большинство вибропрессов имеют большой ресурс усовершенствований, что позволяет изготавливать самые разнообразные изделия.
www.keyprod.ru
Как изготавливают тротуарную плитку. Характеристики основных методов
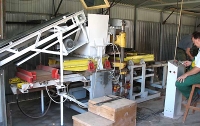

Полную картину, каким способом, и при помощи какого оборудования делают тротуарную плитку, мы можем увидеть только на профильном предприятии. Итак, представим себе небольшое путешествие на завод, в цех по изготовлению тротуарной плитки. Переступив порог, первое, что нас впечатлит - это внушительные размеры помещения. Еще бы! В настоящем цеху производят не 10 и не 100 квадратных метров плитки, а тысячи ежедневно. Поэтому пространства должно быть более чем достаточно. Главным образом для того, чтобы разместить все необходимое оборудование. Что же мы можем увидеть? Самым главным устройством в производстве тротуарной плитки считается вибропресс. Выглядит он следующим образом:
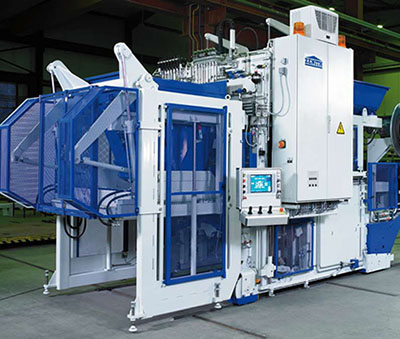
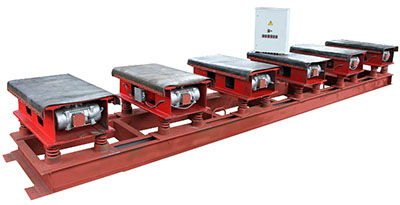
• Формы Они могут быть изготовлены с самого разнообразного материала. Это пластик, полиуретан, силикон, резина, формопласт и др. Однако не всякие формы можно встретить в массовом производстве. Некоторые слишком дороги, а другие качественно не соответствуют регулярному использованию. В технологии вибропрессования используются специальные пресс формы, которые сделаны из стали.
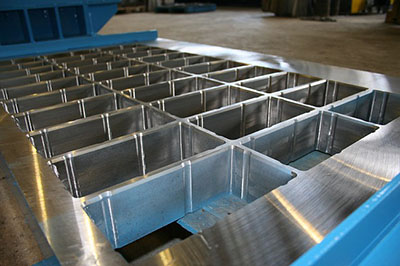
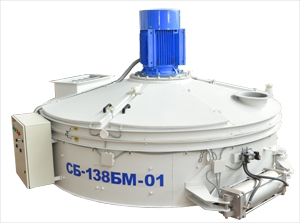

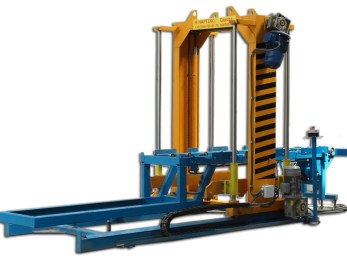
Как уже упоминалось выше, производство троутарной плитки осуществляется двумя основными способами - вибропрессованием и вибролитьем. Каждый из этих методов имеет свои преимущества и недостатки. В чем же их основные отличия? Давайте разберемся.
1. Вибропрессование. Этот метод заключается в том, что бетонная смесь вибрируется в прессформе под давлением, которое создается в вибропрессе. Зачастую используют именно этот метод при выполнении работ большого объема, поскольку он дает возможность максимальной автоматизации. Кроме этого путем вибропрессования можно получить двухслойную плитку и разнообразить цветовую палитру.Процесс изготовления плитки на вибропрессе проходит в несколько этапов:
1.1 Приготовление бетона.Для этого используют бетоносмеситель. Один, если изделие однослойное, или два, если - двухслойное. Пропорции веществ, необходимых для раствора, подбираются производителем индивидуально. Они могут зависеть от качества используемых материалов, наличия или отсутствия специальных добавок и других нюансов. После приготовления смесь сразу же погружается в матрицу вибропресса.
1.2 Формовка.Наблюдая за этим действием, мы увидим как матрица прижимается к виброплощадке и после опускания пуансона включаются вибраторы. Материал уплотняется за счет воздействия виброимпульсов. Все происходит достаточно быстро. Время получения уже отформованых изделий составляет до 5 секунд. После этого осуществляется отделение плитки от пуансона и матрицы и перемещение ее на поддоны. Заполненные поддоны перемещаются для последующей обработки, а на их место устанавливают новые.
1.3 Сушка.Это заключительный этап изготовления тротуарной плитки. Для сушки обычно используются отдельные помещения, где изделия подвергаются обработке теплым паром. Однако также сушить плитку можно и в тех же производственных помещениях. В этом случае в составе бетона обязательно должен присутствовать портландцемент. Без него изделие качественно не высохнет. После финального этапа обработки тротуарная плитка готова к снятию с поддонов примерно через 6-8 часов.
В методе вибропрессования также выделяют два подвида: • полусухое вибропрессование• полусухое гиперпрессование
Метод полусухого вибропрессования характеризуется тем, что раствор приготовляется в полусухом виде и к нему добавляется щебень. На вибрирующую станину устанавливают форму, а сверху на смесь воздействует пуансон. Плитку, полученную таким способом, иногда сложно отличить от природного камня.
Технология гиперпрессования отличается тем, что уплотнение бетона проводится не вибрацией, а высоким давлением. Этот метод реализуется при помощи гидравлического пресса одностороннего или двухстороннего действия. Тротуарная плитка, изготовленная этим методом, считается наиболее прочной.
Вибропрессованная плитка характеризуется шершавой поверхностью и зачастую является самым удачным вариантом для покрытия дорог в зимнее время. Технология вибропрессования позволяет использовать бетон с низким содержанием воды, а это значит, что изделие получается прочное и экономичное. За счет пористой структуры вибропрессованная плитка почти не подвержена разрушениям: попадающая на поверхность вода просачивается сквозь плитку и уходит в почву не задерживаясь. Воздействие высоких температур (климатически естественных) также не оказывают губительного действия на такую плитку. Она не становится мягкой, не выделяет вредных веществ.
2. Вибролитье При производстве плитки способом вибролитья бетонная смесь вибрируется в форме на вибростоле. Этот метод не отличается высокой производительностью, но при этом является более дешевым по сравнению с вибропрессованием. Кроме этого значительно расширяется ассортимент форм изделия, появляется возможность изготовления глянцевой плитки. Тротуарная плитка, изготовленная этим методом - прочна, долговечна и надежна. Технология изготовления такой плитки - длительный процесс. По своей структуре он чем-то похож на предыдущий метод.
2.1 Приготовление бетонной смесиДля замешивания бетона используются бетоносмесители. Их должно быть, как минимум два, если конечная цель - цветная плитка. Один для основного слоя, а второй - для фактурного. В первом бетоносмесителе замешивается раствор с добавлением пигмента, а во втором - без него.
2.2 Подготовка форм.Формы для вибролитой плитки могут использоваться любые: полиуретановые, пластиковые, резиновые. Располагая их на вибростоле, нужно следить за тем, чтобы расстояние между ними было минимальным. При заполнении форм раствором сначала необходимо залить цветной слой и на 3-10 сек. включить вибростол. После этого добавить бетон без красителя до краев.
2.3 Обработка воздействием вибрации.Подвергать изделия вибрации надолго не нужно, достаточно будет 5-10 сек. После окончания этого времени может потребоваться добавление смеси и ее последующая затирка.
2.4 Сушка.Для получения качественной тротуарной плитки, формы должны пройти выдержку в течение 1-2 дней. Поддоны с формами укладывают друг на друга, перестилая при этом пластиковыми листами. В таком положении они должны стоять неподвижно. Перемещать их - недопустимо.
2.5 Выбивка.Чтобы произвести распалубку изделий, необходимо нагреть формы в водяной ванне до 70 С. Если проигнорировать процесс нагрева, то в последующем это приведет к снижению качества материала.
2.6 Упаковка.Готовая тротуарная плитка укладывается лицом к лицу на специальные поддоны. Однако назвать ее готовой в полном смысле этого слова еще нельзя. Для окончательного ее затвердения понадобится еще 1-3 недели, в зависимости от времени года. Зимой этот период будет больше, а летом - сократится.
Плитка, полученная путем литья, имеет гладкую поверхность, и это затрудняяет ее применение в тех местностях, где температура воздуха опускается ниже 0. Кроме того, литая плитка изготавливается из цемента с высоким содержанием воды, а это влияет на показатели ее прочности, которую приходится компенсировать дополнительным количеством цемента. Однако даже этого недостаточно для того, чтобы с уверенностью выложить дорожное покрытие литой плиткой в местах с интенсивным движением. Поверхность такой плитки не очень хорошо пропускает воздух, и это способствует разрушениям при замерзании воды в ее структуре. Однако литая тротуарная плитка намного легче очищается от снега или грязи. Разнообразие цветовой гаммы очень велико. Поэтому именно плитка, изготовленная путем вибролитья, является лучшим материалом для полета дизайнерской фантазии.
www.belbeton.su