Как сделать деталь, напечатанную на 3D-принтере, более прочной. Как распечатывать детали в воздухе на 3д принтере
Как производится печать деталей на 3d принтере
Технология 3D печати была разработана еще в прошлом столетии. Однако до настоящего времени она применялась лишь в промышленности. 3D принтер может воссоздать любой трехмерный объект, детали и даже целое здание, дом. Первый дом созданный по этой технологии находиться в Дубае. Дом строится менее чем за сутки по данной технологии. Принтер с каждым годом совершенствуются, и разрабатываются такие модели, которые могли бы воссоздать органы, имплантаты и протезы, а также еду.
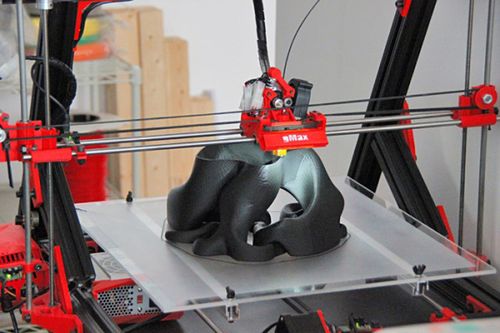
Технология 3D печати FDM
О чём пойдет речь:
Процедура проектирования и печати
Для начала необходимо спроектировать 3d модели для печати на 3d принтере. Есть специальная программа, с помощью которой можно спроектировать любой объект, любой формы и цвета. Затем нужно переходить к обработке модели, то есть к преобразованию ее в цифровой код, с помощью генератора G-кода. Именно с такого кода принтер считывает информацию о том, как распределить материал. Цифровой код представляет собой изображение, состоящее из многочисленных горизонтальных линий или штрихов. Как показано на фото. Далее осуществляется печать обработанной модели.
Принципы осуществления печати общие для всех моделей 3D принтера, но особенности печати у разных моделей 3D принтера могут отличаться. Принцип работы заключается в том, что головка осуществляющий печать перемещается по плоскости и наносит материал согласно созданной в программе модели. После нанесения одного слоя, платформа, на которой создается объект, снижается на толщину первого слоя, после этого наносится следующий слой, и платформа снова снижается на величину равную толщине слоя, и так продолжается до создания полноценной трехмерной модели.
Особенности печати
Для каждого принтера существуют определенные технологии печати. Самыми популярными методами печати являются FDM и SLA.

FDM печать
Первый метод основан на технологии плавления специальной нити. Осуществляется следующим образом, по контуру модели накладывается специальная нить и плавиться, создавая нужную форму. Для этой технологии печати используются синтетические материалы как пластик, полиамид, нейлон поликарбонат и другую синтетику. Эти материалы выпускаются в виде катушек нити.
Кстати, при изготовлении пластиковых бутылок используется эта же технология. Приобрести материалы для принтера можно онлайн через компании, предоставляющие услуги по поставке.

Схема технологии FDM
3D принтер, осуществляющий печать по такой технологии работает по принципу и алгоритму. Нить помешается в специальный контейнер, в котором она плавиться под воздействием температуры.
А затем выдавливается на платформу. Контейнер с нитью перемещается по определенной траектории, надавливая слой за слоем. Если модель сложная используются два материала, один для основы, другой для модели. Первый предназначен для опоры, при создании объектов с отдельными или повисшими элементами. То есть, принтер сначала создает основу, а затем на ней воссоздает отдельные детали.
Второй метод основан на использовании для печати, в качестве основного материала фотополимерные смолы. Изначально они находятся в жидком состоянии, но затем застывают под воздействием лазера. Эта технология позволяет создать объекты с очень маленькой толщиной. Печать формируется следующим образом. Если в первом методе платформа снижалась на толщину одного слоя, то здесь предусмотрена немного другая процедура.

SLA печать
То есть, платформа погружается в контейнер с жидкой фотополимерной смолой, после каждого слоя на величину равную толщине. Затем с помощью лазера вырезается объект. И после завершения объект погружают в специальные растворы, чтобы очистить от пыли и остатков.
Печать деталей из металла и пластика
Как уже было упомянуто выше, технологии печати 3D применяются для изготовления деталей из любых доступных материалов, в том числе пластика и металла. Чтобы осуществить печать деталей на 3d принтере, помимо самого принтера и материалов необходимы определенные навыки, и ознакомиться с технологией.
Но если нет возможности сделать это самостоятельно, то можно обратиться в специальные фирмы, которые предоставляют услуги по изготовлению металлических или пластиковых деталей. Практически все фирмы реализуют свои услуги через Интернет, и таким образом можно заказать необходимую деталь или запчасти, не выходя из дома. В анкете указываются все данные о будущем объекте, а услуги оплачиваются любым удобным способом.
Для ознакомления с технологией 3d печати можно посмотреть видео, или пошаговую инструкцию с фото.
3d печать металлом
Технология 3d печати стремительно набирает популярность не только среди юридических лиц, осуществляющих массовое производство деталей, но и рядовых потребителей. Они приобретают принтер для себя, чтобы создавать объекты для дома, личного пользования, игрушек, сувениров и других целей, не исключено и создание малого бизнеса по изготовлению деталей по заказу. Почему люди стремятся приобрести принтер, использующие металл для создания объектов?

Печать металлом на 3d принтере может сэкономить расходы и время на приобретение, и поиск нужной детали или запчасти для авто, или имплантатов, а также многое другое.
Металл, который применяется в 3D принтерах, уступает настоящему только прочностью. То есть, детали из металла имеют свойство подвергаться коррозии до определенной степени. Однако обычное железо при этом может заржаветь полностью, а этот нет. Металл для 3d принтера применяется в виде порошка. Технология печати металлом также осуществляется по слоям. Некоторые производители вело запчастей, также применяют 3d технологии, и оказывают услуги по их реализации.
Применение 3d принтера и печать деталей из пластика
Каждый человек может сделать 3d печать дома на 3d принтере. Технология очень простая, программа для проектирования модели доступна всем без исключения.
Применить 3d технологию можно в целях создания макетов, или копий реальных зданий или оригинальных архитектурных сооружений или оказывать услуги.
Что касается стоимости принтеров, принтеры которые осуществляют печать из пластика, может приобрести любой человек. Пластик самый доступный и дешевый материал, а изготовить из него можно практически все, начиная от игрушек и кончая посудой. Более того, пластик можно декорировать и покрасить при желании, или же подобрать по текстуре и цвету из широкого разнообразия, в отличие, например, от других материалов как металл.
printergid.ru
Как сделать деталь, напечатанную на 3D-принтере, более прочной
Как нам всем хорошо известно, детали, напечатанные на обычном домашнем 3D-принтере, получаются не такими прочными и служат не так долго, как оригинальные. Мы подумали, что было бы здорово научиться как-нибудь укреплять напечатанные детали, и немного над этой идеей поработали.
Такие более прочные детали позволят нам использовать их в реальном деле, при высокой нагрузке. Тогда, вместо того чтобы искать оригинальные детали на замену сломавшимся в гаджетах, роботах, машинах, механических игрушках или для любого разрабатываемого проекта, мы сможем просто напечатать их.
Необходимость в разработке такого руководства возникла у автора тогда, когда он купил на eBay велосипедные подвесные сумки. Одну для подруги, другую для себя. Крепление сумок подразумевало, что руль имеет толщину в один дюйм (2,54 см), и едва подходило к женскому велику. Руль же мужского велосипеда имел диаметр 3,15 мм, и на него крепление не налезало.
Поэтому появилась мысль изготовить деталь по размеру соответствующего крепления, напечатав ее на 3D-принтере.
Шаг 1. Требующаяся деталь
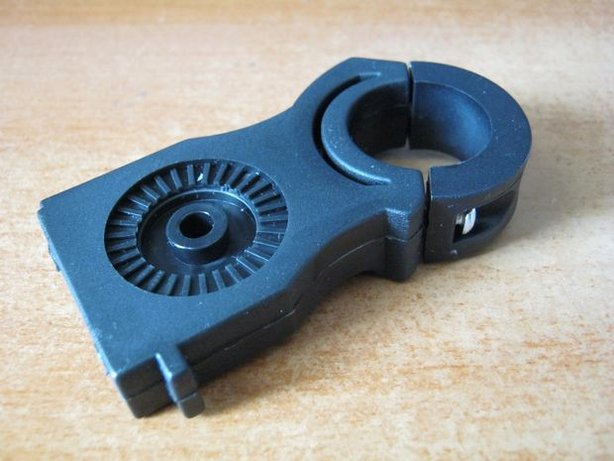
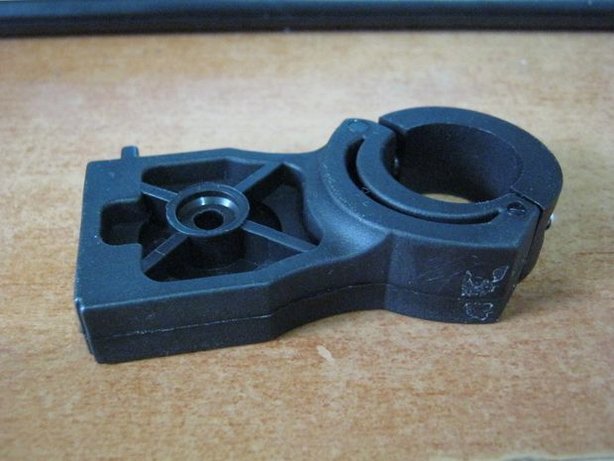
Вот узел, который нужно воспроизвести на 3D-принтере.
Чтобы что-то напечатать, для начала требуются файлы 3D-модели. Их, соответственно, нужно найти и скачать в интернете или же разработать самостоятельно. Второй вариант представлялся единственно возможным, поскольку готовых 3D-моделей для такой специфической детали найти невозможно, и нужно было модифицировать ту, которая имелась, так, чтобы она налезала на руль.
Однако всем прекрасно известно, что напечатанные на 3D-принтере детали прочностью не отличаются. Напечатанный обычным способом данный узел получился бы не настолько прочным, чтобы надежно держать тяжелую сумку на тряской дороге. Тогда возникла мысль как-то укрепить эту деталь, придав ей достаточно прочности.
Автор несколько лет занимался судомоделированием и имел возможность убедиться, насколько слои стекловолокна и эпоксидки делают более крепкими даже тонкие фанерные детали, в результате чего они без проблем выдерживают высокие нагрузки.
Поэтому и в данной работе было решено задействовать стекловолокно и эпоксидный клей-смолу.
Первоначально планировалось снять чертеж детали, внести необходимые изменения по размерам и покрыть все стекловолоконной тканью с эпоксидным клеем. Итак, приступим к моделированию.
Шаг 2. Проект первый
Деталь должна быть такой. Все размеры подогнаны, всё в целом увеличено и утолщено. Увеличены и поверхности, чтобы на них можно было наклеить стекловолокно.
Кроме того, на каждой из сторон предусмотрены желобки, чтобы заполнить их эпоксидкой для придания еще большей прочности. Смоделированы также сквозные отверстия, чтобы части узла было проще соединять друг с другом и чтобы стекловолокно и смола соединяли их изнутри.
Деталь напечатана на принтере Up и проверена на предмет того, подходит ли она по размерам.
Тип заполнения выбран решетчатый, что позволило оставить достаточно пустого пространства внутри детали. В обычной ситуации это уменьшает прочность, но сделано это было сознательно. В детали просверлено еще несколько отверстий, чтобы позволить эпоксидному клею проникнуть внутрь и укрепить ее.
Шаг 3. Нанесение стекловолокна и эпоксидного клея на первый проект
Это самая грязная часть работы. С эпоксидкой и стекловолокном работать сложно. Всё везде липнет так, что потом почти не отмоешь.
Сначала полоски стекловолоконной ткани были наклеены на обе половинки детали, чтобы они лучше скреплялись.
Затем всё было выложено на кусок нейлона, поскольку эпоксидная смола, к счастью, к нейлону прилипает не так смертельно. После этого эпоксидка была нанесена на поверхность детали, вырезан соответствующей формы и размера кусок стекловолоконной ткани, поверх которой был опять-таки нанесен эпоксидный клей. Клея было столько, что стекловолокно стало прозрачным.
Вся эта процедура повторилась для другой стороны детали, после чего смола день застывала. Даже немного больше, чтобы всё скрепилось намертво.
Шаг 4. Еще эпоксидки для дополнительного укрепления с боков
Решено было также добавить еще эпоксидного клея в специально предусмотренные для этого торцевые бороздки.
Шаг 5. Проект второй
При разработке первого проекта имелось в виду, что деталь через просверленные в ней дополнительные отверстия будет частично заполнена эпоксидной смолой, а снаружи ее будет держать пропитанное эпоксидкой стекловолокно. В процессе печати первой детали родилась идея смоделировать только ее оболочку, а внутри все вообще сделать только из эпоксидного клея и стекловолокна.
И вот, пока первый проект застывал, решено было приступить к моделированию второго. Хотелось сравнить оба варианта в плане прочности и легкости в изготовлении. Во втором проекте в заполнении двух фрагментов детали (для крепления нужно две части) был использован различный подход.
На фото видно, что второй проект – это пустая оболочка со стенками в 1 мм толщиной. Округлый фрагмент отделен от большего, чтобы упростить процесс заполнения. Его нужно потом, когда эпоксидка будет застывать, закрепить винтами.
Шаг 6. Заполнение второго проекта эпоксидкой и оптоволокном
Для начала было мелкими кусочками нарезано стекловолокно, и получившимися клочьями обе части детали заполнены чуть больше, чем наполовину. Затем нужно по каплям добавлять эпоксидный клей и немного придавливать обрезки, чтобы они хорошо пропитывались.
Шаг 7. Заполняем дальше проект 2. Фрагмент 1
Продолжаем капать и утаптывать, пока вся стеклоткань не пропитается, после чего добавляем еще обрезков стеклоткани, повторяя этот шаг до окончательного заполнения детали. Теперь закрепим винтами второй фрагмент детали. В конце концов уровень смеси эпоксидки и стекловолокна должен быть до краев.
Почти то же самое для меньшего, округлого фрагмента.
Шаг 8. Заполняем проект 2. Фрагмент 2
Для этого фрагмента применен несколько другой подход: деталь не заполнялась с самого начала наполовину. На дно был уложен только один слой стеклоткани, затем еще один – с перехлестом на края. Эти слои пропитывались эпоксидкой до тех пор, пока не стали полностью прозрачными, после чего на них один за другим укладывались и придавливались, чтобы впитали клей, следующие слои. Немного эпоксидки добавлялось через каждые 2-3 слоя.
Первый способ давал нам деталь, внутри которой больше эпоксидной смолы и чуть меньше стекловолоконной ткани. При втором способе в детали больше стекловолокна и меньше эпоксидки между слоями.
Шаг 9. Теперь всё должно застыть
Периодически детали проверялись, в образующиеся при впитывания смолы пустоты добавлялось еще смолы. Где надо, добавлялось стекловолокна. На полное застывание ушел примерно день. В продаже есть эпоксидные клеи, которые застывают быстрее, можно также добавить больше отвердителя, чтобы ускорить процесс. Мы, однако, этого не рекомендуем, потому что это только осложнит работу и будет мешать клею проникнуть во все углы.
Шаг 10. Сборка готового узла
Детали получились довольно неплохими, особенно по второму проекту. Крепление их на сумку прошло без проблем. Подошли отлично. Теперь нужно закрепить сумку на велосипед.
Шаг 11. Удаляем пластиковые части
Этот шаг на самом деле не предусматривался. Предполагалось просто использовать напечатанные на 3D-принтере и укрепленные детали. Но когда дело дошло до ошкуривания, напечатанная «кожица» просто стала отламываться по углам, остальное тоже снималось без проблем. «Кожица» эта никакой дополнительной прочности не давала, поэтому и была практически полностью снята, и деталь стала композитной эпоксидно-стекловолоконной.
Шаг 12. Итоги
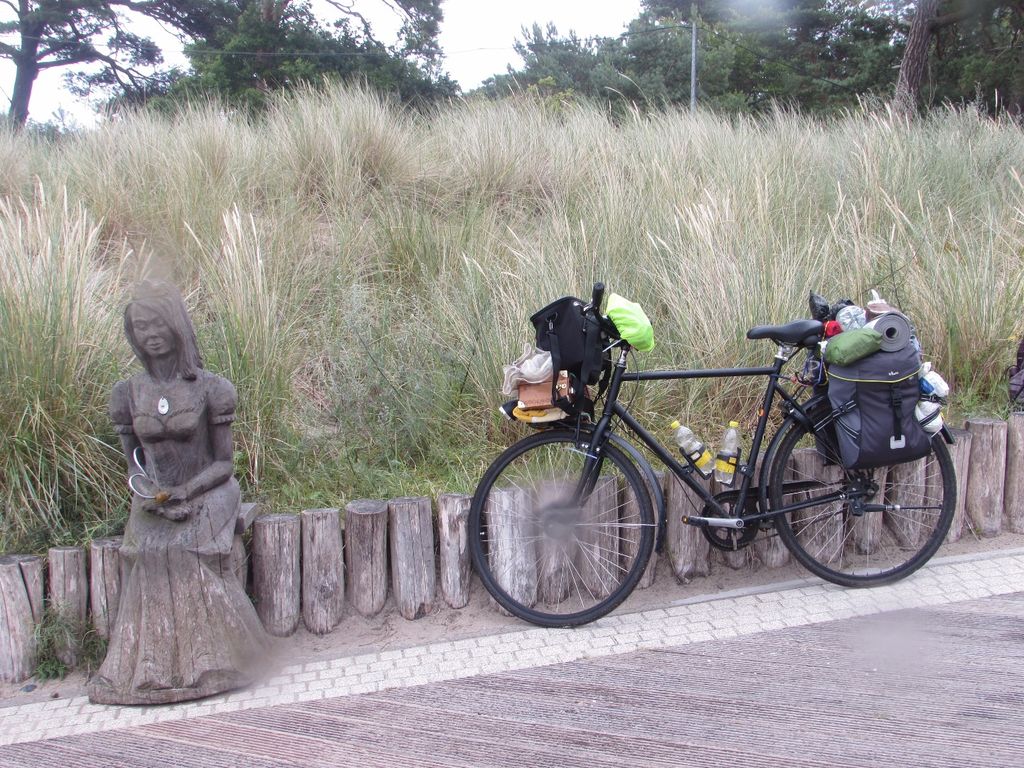
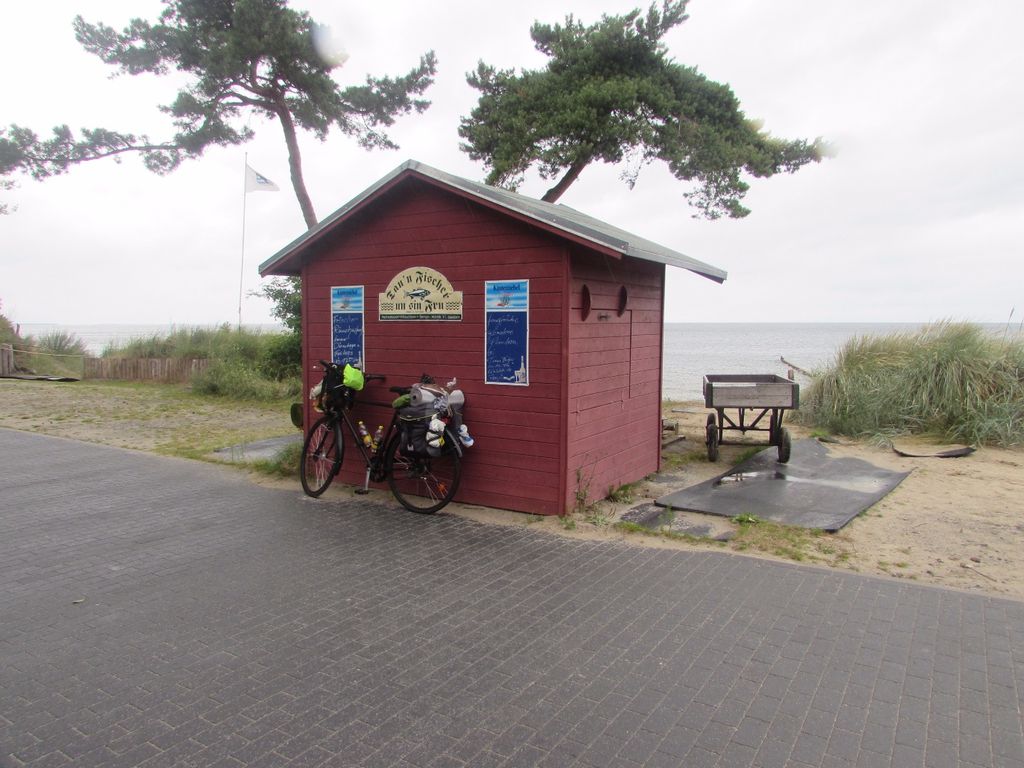
Деталь без проблем продержалась во время 20-дневной поездки по Швеции, Польше, Германии и Дании. Передняя сумка было все время до отказа заполнена едой, было пройдено немало ухабистых дорог. Детали прослужили на отлично и по-прежнему крепче камня.
Вот еще несколько полезных замечаний.
- Интересно, что эпоксидка не очень хорошо прилипает к ABS. Именно поэтому дополнительные отверстия, через которые она будет проникать внутрь и скреплять конструкцию, просто обязательны.
- Укреплять деталь снаружи гораздо сложнее, чем заполнять ее. Времени на первый вариант уходит масса, но заполненная деталь получается легче. Бесспорно, укрепленная деталь значительно прочнее, чем просто напечатанная и не укрепленная. Это легко проверить, если испытать на скручивание укрепленную и не укрепленную детали. Укрепленная подобна камню, обычная легко меняет форму.
- Второй метод укрепления гораздо проще и дает гораздо более опрятный результат. После застывания смолы почти ничего не надо чистить. А то, что получилось, имеет крепость гранита!
- Оба варианта заполнения при различных количествах стекловолокна дают одинаковое ощущение прочности и массивности. Однако тот, где волокна больше, теоретически и почти без сомнений должен выдерживать больший вес.
- По второму проекту узел получается более тяжелым, поскольку внутри он полностью состоит из стекловолокна и эпоксидной смолы. Вес немного уменьшается после удаления окружающего пластика. При этом, впрочем, изменятся и размеры детали. Поэтому о размерах нужно подумать заблаговременно и учесть снятие пластика при моделировании.
- Во втором проекте тоже можно предусмотреть желобки-бороздки и пустоты, тогда вес удастся снизить.
Перевод статьи Strengthening a 3D Printed Part с сайта Instructables.com
3dpt.ru
Вопросы и ответы по 3D-принтерам и 3D-печати
Часто задаваемые вопросы
Купил 3D-принтер - что дальше?
3D-принтер не видит/не печатает STL файл
ответ: практически все 3D-принтеры не должны видеть или печатать STL файлы (хотя есть и исключения), так как данный тип файла содержит геометрию модели в виде сетки, полученную в результате полигонального моделирования или экспорта из CAD-программ. STL файлы загружаются в программу подготовки модели к печати (слайсер) и преобразуются в управляющий код (g-cоde) для принтера. Полученный в результате "слайсинга" файл и видит 3D-принтер. Подробности здесьС помощью какой программы подготовить STL файл к печати?
ответ: для подготовки STL-файла к печати необходимо использовать слайсер - программу, с помощью которой вы задаете настройки печати модели для принтера. Такая программа (слайсер) может быть как распространенная и не привязанная к конкретному принтеру, к примеру Cura, slic3r, KISSlicer и др., так и индивидуальная для конкретного 3D-принтера (поставляется в комплекте с принтером). В данной программе задаётся множество параметров - скорость печати, толщина слоя, температура и многие другие. Информация по слайсерам здесьЧто такое 3D-принтер и как он работает?
Что такое кинематика 3D-принтера?
Что такое шаговые двигатели и драйверы?
Что такое прошивка 3D-принтера и куда она заливается?
Вопросы по дефектам и проблемам 3D-печати
Статьи по теме
Большинство вопросов и ответов даны в статьях. Просьба ознакомиться:
- Дефекты 3D печати - Попробуем ввести классификацию - 20 наиболее распространенных проблем 3D печати (Часть 1) - 20 наиболее распространенных проблем 3D печати (Часть 2)
Не давится PLA пластик и щелкает экструдер
ответ: Проблема в недостаточном охлаждении термобарьера экструдера.
На стенках при печати появляются волны.
ответ: волны на стенках, т.н. вобблинг (от wobble (англ.) колебания) связаны с наличием люфтов в механизмах перемещения принтера. В кинематиках типа Prusa вобблинг связан с нежестким соединением винтов оси Z с двигателями. Для решения этой проблемы в муфты, соединяющие винты и валы двигателя необходимо положить шарики от шарикоподшипников, а разрезную муфту установить в натяг.В начале печати стол/каретка начинает стучать об стенку.
ответ: Для устранения проблемы необходимо проверить концевой выключатель, нажимается ли он кареткой/столом и целостность проводов выключателя.Вопросы по адгезии (прилипанию модели к столу)
Пластик не прилипает к столу.
ответ: при печати на стеклянных поверхностях для улучшения адгезии необходимо применять различные клеи (например клей от The 3D или Picaso, можно использовать клей-карандаш или БФ-2). Печатать рекомендуется на стеклянных поверхностях (лучше зеркалах) из-за их ровной поверхности, обеспечивающей ровный первый слой.Деталь при печати сильно прилипла, не получается снять ее со стола.
ответ: проблема связана с очень маленьким зазором при печати первого слоя, и он “вмазывается” в поверхность стекла. Необходимо увеличить зазор. А для удаления детали со стекла ее можно поместить в морозильную камеру холодильника.При печати детали отгибает углы.
ответ: при печати делали необходимо ее закрывать от сквозняков. Отгибание углов связано с сильной усадкой материала при его охлаждении. Для равномерной усадки, которой обладают все пластики, необходимо поддерживать стабильную температуру с помощью термокамеры. Термокамерой может служить и коробка, которой можно накрыть принтер, так и установка дверцы в принтер.Вопросы по расходным материалам
Как печатать PLA-пластиком
ответ: PLA-пластик имеет рабочие температуры печати от 200 до 230 градусов (зависит от состава материала, который использовал производитель). Если на вашем 3D-принтере подогреваемый стол, то дополнительных средств для прилипания модели к столу не требуется. Если у вас стол без подогрева или модель не прилипает к столу, то проверьте калибровку стола и воспользуйтесь средствами для адгезии (лак/клей для печати и др.).Как печатать ABS-пластиком
ответ: ABS-пластик имеет рабочие температуры печати от 230 до 250 градусов (зависит от состава материала, который использовал производитель). Печать ABS-пластиком подразумевает наличие подогреваемого стола и средств для адгезии (лак/клей для печати, ABS-сок и др.).
У пластика неравномерный диаметр
ответ: Колебания диаметра более, чем на 0,05 мм считаются браком. В данном случае необходимо обратиться к компании-производителю с просьбой о замене катушки на качественную.В пластике наблюдаются инородные включения.
ответ: это является браком, с данным дефектом необходимо обратиться к производителю. Такие дефекты могут привести к засорению сопла принтера.При печати наблюдается запутывание пластика
ответ: так называемый нахлест связан с тем, что вы при эксплуатации расслабили намотку катушки, и верхние витки попали под нижние. Рекомендуем размотать часть катушки до места с равномерной намоткой и аккуратно намотать обратно, соблюдая натяжение.Вреден ли АBS-пластик?
ответ: при печати ABS выделяет неприятный запах, и необходимо проветривать помещение. Вреда нет никакого, выделения не превышают ПДК (предельно допустимую концентрацию).Почему при печати мягкими пластиками (Flex) через несколько слоев прекращается подача прутка?
ответ: если на вашем принтере система подачи прутка Bowden, то мягкие пластики встречают слишком сильное сопротивление при прохождении через трубку к печатающей головке. Попробуйте увеличить температуру сопла, чтобы сопротивление было минимальным.
Вопросы по сборке и калибровки 3D-принтера
Ось едет не в ту сторону
ответ: если перемещение происходит не в том направлении, то необходимо разъем шагового двигателя перевернуть на 180 градусов.При замене драйверов шаговых двигателей с А4988 на DRV8825 нужно ли что-то менять в прошивке?
ответ: Если вы хотите использовать их с тем же делителем (1/16), то ничего не нужно. Если хотите использовать с делителем 1/32, то в прошивке необходимо в 2 раза увеличить число шагов на тех осях, где установлены эти драйвера. Так же, не забывайте о правильной регулировке тока драйвера.После установки TMC2100/2208/2130 при печати происходят сдвиги слоев.
ответ: для данного типа драйверов необходимо хорошее охлаждение и достаточно точная регулировка напряжения Vref.Вопросы по прошивке 3D-принтера
Не могу разобраться в Marlin
ответ: прочитайте статьи по прошивке:
Подготовка модели к печати. Слайсеры
Программа CURA - как в ней работать
ответ: прочитайте статьи, написанные специально для вас. Список:
Программа KISSlicer - как в ней работать
ответ: прочитайте статьи, написанные специально для вас. Список:
Программа Repetier-Host - как в ней работать
ответ: прочитайте статьи, написанные специально для вас. Список:
Программа Simplify3D - как в ней работать
ответ: прочитайте статьи, написанные специально для вас. Список:
Программа Slic3r - как в ней работать
ответ: прочитайте статьи, написанные специально для вас. Список:
Что такое G-CODE?
ответ: прочитайте статьи, написанные специально для вас. Список:
Справка по 3Dtoday
как пользоваться порталом и что тут есть?
где я могу почитать информацию по 3D-принтерам и 3D-печати?
Поиск вопросов - ответов на портале
Если вы не нашли ответ на интересующий Вас вопрос в данном разделе справки - воспользуйтесь поиском по сайту. Может быть аналогичный вопрос уже обсуждался в блогах. Форма поиска здесь - http://3dtoday.ru/search/3dtoday.ru
Как начать печатать на 3D принтере!


После заливки прошивки в Arduino у меня возникли вопросы: «А как печатать? Какую программу запускать? Какие файлы нужны?». Принтер понимает только G-коды.
Что бы вам было проще во всем разобраться, я нарисовал простенькую схему, которая показывает как работать с принтером:

Схема печати на 3Dпринтере
Теперь поясню эту схему.
В любом 3D-редакторе рисуем файл и сохраняем в формате *.STL. Например такую:

3d деталь в редакторе
Далее открываем этот файл в слайсере Slic3r — именно в этой программе заложен алгоритм работы принтера, именно она по заданным параметрам определяет траекторию движения печатающей головки, скорость подачи пластика и создает на основе этих данных файл с G-кодами с расширением *.gcode. G-коды — это команды для принтера, например, команда «G0 X10 Y10 Z15″ перемещает печатающую головку в позицию с координатами x=10,y=10,z=15. Файл с G-кодами можно спокойно посмотреть в блокноте и внести поправки. Вот как выглядит программа Slic3r:

программа slic3r
Получив файл с G-кодами, запускаем Pronterface и загружаем этот файл. После того, как печатающая головка нагреется, можно приступать к печати. В процессе печати программа Pronterface считывает строку с G-кодом и отправляет её в принтер, принтер, отработав код,посылает ответ «команда выполнена» и ждет следующей команды и так до тех пор, пока не будет достигнут конец файла. Попутно Pronterface показывает на экране, что в данный момент выполняет принтер, куда движется и какой слой детали печатается. Вид программы:

программа Pronterface
Существуют другие программы для печати, которые совмещают в себе сразу Slic3r и Pronterface, с красивым графическим 3d-интерфейсом, но честно говоря, я пока не осилил их. Вот список нескольких таких программ: RepRap, Skeinforge, ReplicatorG. Существуют версии под win32,win64 и linux. Так же есть программы написанные на питоне и являющиеся кроссплатформенными.
Чуть не забыл — сама напечатанная деталь:

напечатанная 3d деталь
Выглядит ужасно, т.к. это одна из первых моих напечатанных деталей, я еще тестировал с настройками. Все нормальные детали установлены в принтер Кстати, по виду детали можно сразу понять, какие есть косяки в конструкции принтера, где ненатянут ремень, или есть люфт, или перекос
Как вы уже убедились, прежде, чем начать печатать детали, надо настроить и откалибровать принтер, задать в программах температуру плавления пластика и установить скорость печати.
Обо всем этом я уже пишу статьи,так что ожидайте инфу в ближайшие дни Что бы не пропустить выход статей,подпишитесь на рассылку:
diylife.ru
Технология 3d печати больших деталей
Нашел интересную статью о том, как печатать ABS пластиком большие детали без изгиба и отлипания детали. Основная проблема при печати больших деталей в том, что они изгибаются. Происходит это из-за того, что напечатав первый слой, проходит относительно много времени, прежде чем принтер преступит к печати второго слоя. Это приводит к остыванию первого слоя. Пластик немного сжимается в размерах, но этого недостаточно для искривления всей детали и отлипания от подложки.
Затем, принтер печатает второй слой по «усохшемуся» первому слою. Это приводит к еще большему напряжению первого слоя. Далее печатается третий слой по «усохшемуся» второму слою. Каждый последующий слой добавляет напряжение в детали. И как результат — она изгибается дугой и отлипает.
Далее, я расскажу, как автор статьи решил эту проблему:
Он сделал очень простую вещь — основание детали представляет собой полоски длиной и шириной порядка 1-2см, не более, и высотой пару миллиметров. Т.е. деталь как бы стоит на сваях

3d печать без изгиба детали
Во всей детали он делает отверстия таким образом, что бы самый длинный слой оказался длиной 1-2см. Вот как это выглядит:

Деталь без искривлений
Красными линиями я показал, что любой слой, так или иначе прерывается специальными отверстиями.
Здесь кажется, что основание детали цельное, но это не так. Посмотрите видео и вы все поймете:
Результаты впечатляют.
Да, не везде можно применить такой метод. Но самое главное — это рабочая технология :)
diylife.ru
Как сделать деталь, напечатанную на 3D-принтере, более прочной: 3d_tutorials
Как нам всем хорошо известно, детали, напечатанные на обычном домашнем 3D-принтере, получаются не такими прочными и служат не так долго, как оригинальные. Мы подумали, что было бы здорово научиться как-нибудь укреплять напечатанные детали, и немного над этой идеей поработали.
Такие более прочные детали позволят нам использовать их в реальном деле, при высокой нагрузке. Тогда, вместо того чтобы искать оригинальные детали на замену сломавшимся в гаджетах, роботах, машинах, механических игрушках или для любого разрабатываемого проекта, мы сможем просто напечатать их.
Необходимость в разработке такого руководства возникла у автора тогда, когда он купил на eBay велосипедные подвесные сумки. Одну для подруги, другую для себя. Крепление сумок подразумевало, что руль имеет толщину в один дюйм (2,54 см), и едва подходило к женскому велику. Руль же мужского велосипеда имел диаметр 3,15 мм, и на него крепление не налезало.
Поэтому появилась мысль изготовить деталь по размеру соответствующего крепления, напечатав ее на 3D-принтере.
Шаг 1. Требующаяся деталь
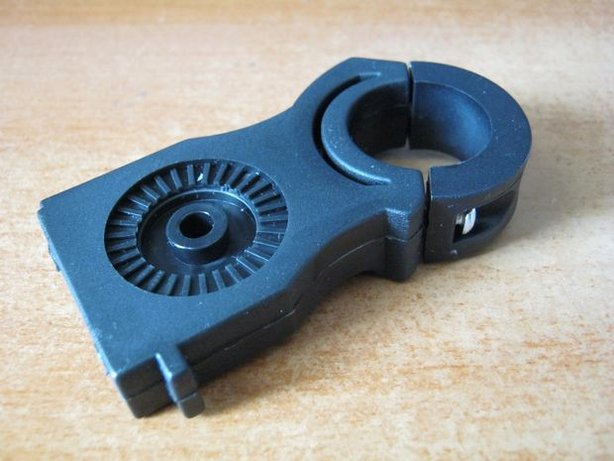
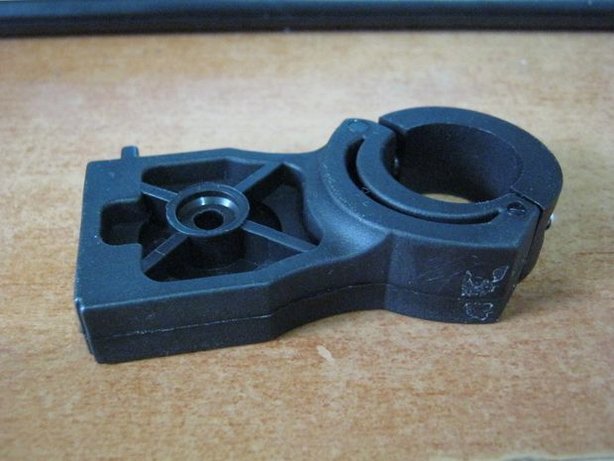
Вот узел, который нужно воспроизвести на 3D-принтере.
Чтобы что-то напечатать, для начала требуются файлы 3D-модели. Их, соответственно, нужно найти и скачать в интернете или же разработать самостоятельно. Второй вариант представлялся единственно возможным, поскольку готовых 3D-моделей для такой специфической детали найти невозможно, и нужно было модифицировать ту, которая имелась, так, чтобы она налезала на руль.
Однако всем прекрасно известно, что напечатанные на 3D-принтере детали прочностью не отличаются. Напечатанный обычным способом данный узел получился бы не настолько прочным, чтобы надежно держать тяжелую сумку на тряской дороге. Тогда возникла мысль как-то укрепить эту деталь, придав ей достаточно прочности.
Автор несколько лет занимался судомоделированием и имел возможность убедиться, насколько слои стекловолокна и эпоксидки делают более крепкими даже тонкие фанерные детали, в результате чего они без проблем выдерживают высокие нагрузки.
Поэтому и в данной работе было решено задействовать стекловолокно и эпоксидный клей-смолу.
Первоначально планировалось снять чертеж детали, внести необходимые изменения по размерам и покрыть все стекловолоконной тканью с эпоксидным клеем. Итак, приступим к моделированию.
Шаг 2. Проект первый
Деталь должна быть такой. Все размеры подогнаны, всё в целом увеличено и утолщено. Увеличены и поверхности, чтобы на них можно было наклеить стекловолокно.
Кроме того, на каждой из сторон предусмотрены желобки, чтобы заполнить их эпоксидкой для придания еще большей прочности. Смоделированы также сквозные отверстия, чтобы части узла было проще соединять друг с другом и чтобы стекловолокно и смола соединяли их изнутри.
Деталь напечатана на принтере Up и проверена на предмет того, подходит ли она по размерам.
Тип заполнения выбран решетчатый, что позволило оставить достаточно пустого пространства внутри детали. В обычной ситуации это уменьшает прочность, но сделано это было сознательно. В детали просверлено еще несколько отверстий, чтобы позволить эпоксидному клею проникнуть внутрь и укрепить ее.
Шаг 3. Нанесение стекловолокна и эпоксидного клея на первый проект
Это самая грязная часть работы. С эпоксидкой и стекловолокном работать сложно. Всё везде липнет так, что потом почти не отмоешь.
Сначала полоски стекловолоконной ткани были наклеены на обе половинки детали, чтобы они лучше скреплялись.
Затем всё было выложено на кусок нейлона, поскольку эпоксидная смола, к счастью, к нейлону прилипает не так смертельно. После этого эпоксидка была нанесена на поверхность детали, вырезан соответствующей формы и размера кусок стекловолоконной ткани, поверх которой был опять-таки нанесен эпоксидный клей. Клея было столько, что стекловолокно стало прозрачным.
Вся эта процедура повторилась для другой стороны детали, после чего смола день застывала. Даже немного больше, чтобы всё скрепилось намертво.
Шаг 4. Еще эпоксидки для дополнительного укрепления с боков
Решено было также добавить еще эпоксидного клея в специально предусмотренные для этого торцевые бороздки.
Шаг 5. Проект второй
При разработке первого проекта имелось в виду, что деталь через просверленные в ней дополнительные отверстия будет частично заполнена эпоксидной смолой, а снаружи ее будет держать пропитанное эпоксидкой стекловолокно. В процессе печати первой детали родилась идея смоделировать только ее оболочку, а внутри все вообще сделать только из эпоксидного клея и стекловолокна.
И вот, пока первый проект застывал, решено было приступить к моделированию второго. Хотелось сравнить оба варианта в плане прочности и легкости в изготовлении. Во втором проекте в заполнении двух фрагментов детали (для крепления нужно две части) был использован различный подход.
На фото видно, что второй проект – это пустая оболочка со стенками в 1 мм толщиной. Округлый фрагмент отделен от большего, чтобы упростить процесс заполнения. Его нужно потом, когда эпоксидка будет застывать, закрепить винтами.
Шаг 6. Заполнение второго проекта эпоксидкой и оптоволокном
Для начала было мелкими кусочками нарезано стекловолокно, и получившимися клочьями обе части детали заполнены чуть больше, чем наполовину. Затем нужно по каплям добавлять эпоксидный клей и немного придавливать обрезки, чтобы они хорошо пропитывались.
Шаг 7. Заполняем дальше проект 2. Фрагмент 1
Продолжаем капать и утаптывать, пока вся стеклоткань не пропитается, после чего добавляем еще обрезков стеклоткани, повторяя этот шаг до окончательного заполнения детали. Теперь закрепим винтами второй фрагмент детали. В конце концов уровень смеси эпоксидки и стекловолокна должен быть до краев.
Почти то же самое для меньшего, округлого фрагмента.
Шаг 8. Заполняем проект 2. Фрагмент 2
Для этого фрагмента применен несколько другой подход: деталь не заполнялась с самого начала наполовину. На дно был уложен только один слой стеклоткани, затем еще один – с перехлестом на края. Эти слои пропитывались эпоксидкой до тех пор, пока не стали полностью прозрачными, после чего на них один за другим укладывались и придавливались, чтобы впитали клей, следующие слои. Немного эпоксидки добавлялось через каждые 2-3 слоя.
Первый способ давал нам деталь, внутри которой больше эпоксидной смолы и чуть меньше стекловолоконной ткани. При втором способе в детали больше стекловолокна и меньше эпоксидки между слоями.
Шаг 9. Теперь всё должно застыть
Периодически детали проверялись, в образующиеся при впитывания смолы пустоты добавлялось еще смолы. Где надо, добавлялось стекловолокна. На полное застывание ушел примерно день. В продаже есть эпоксидные клеи, которые застывают быстрее, можно также добавить больше отвердителя, чтобы ускорить процесс. Мы, однако, этого не рекомендуем, потому что это только осложнит работу и будет мешать клею проникнуть во все углы.
Шаг 10. Сборка готового узла
Детали получились довольно неплохими, особенно по второму проекту. Крепление их на сумку прошло без проблем. Подошли отлично. Теперь нужно закрепить сумку на велосипед.
Шаг 11. Удаляем пластиковые части
Этот шаг на самом деле не предусматривался. Предполагалось просто использовать напечатанные на 3D-принтере и укрепленные детали. Но когда дело дошло до ошкуривания, напечатанная «кожица» просто стала отламываться по углам, остальное тоже снималось без проблем. «Кожица» эта никакой дополнительной прочности не давала, поэтому и была практически полностью снята, и деталь стала композитной эпоксидно-стекловолоконной.
Шаг 12. Итоги
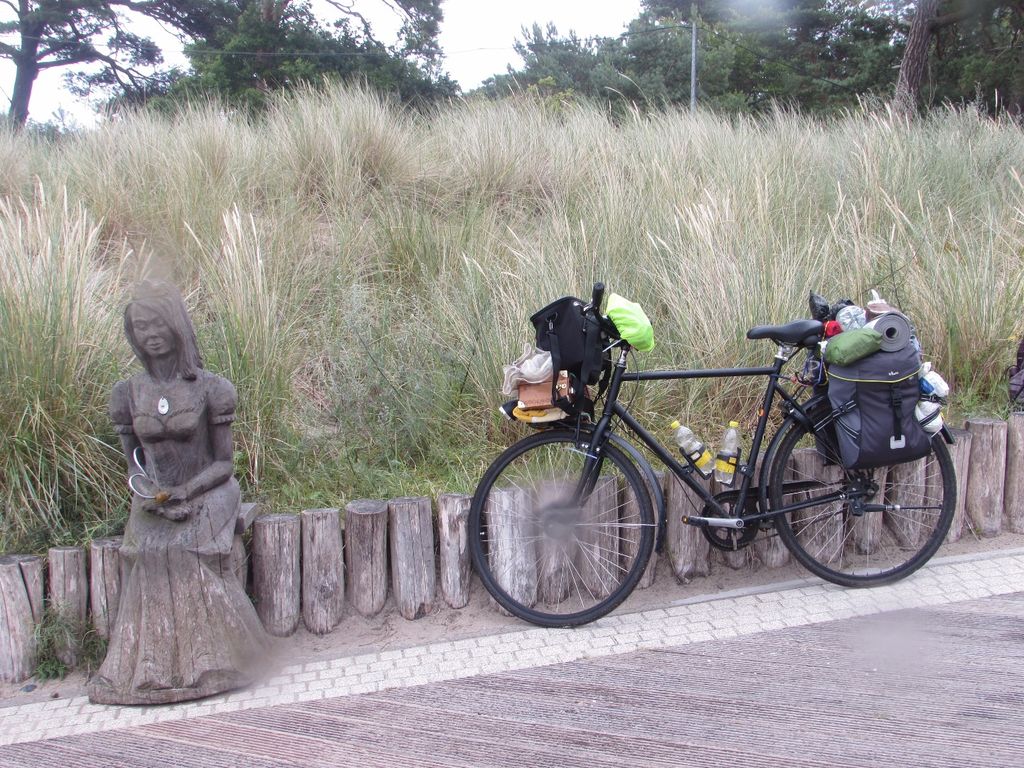
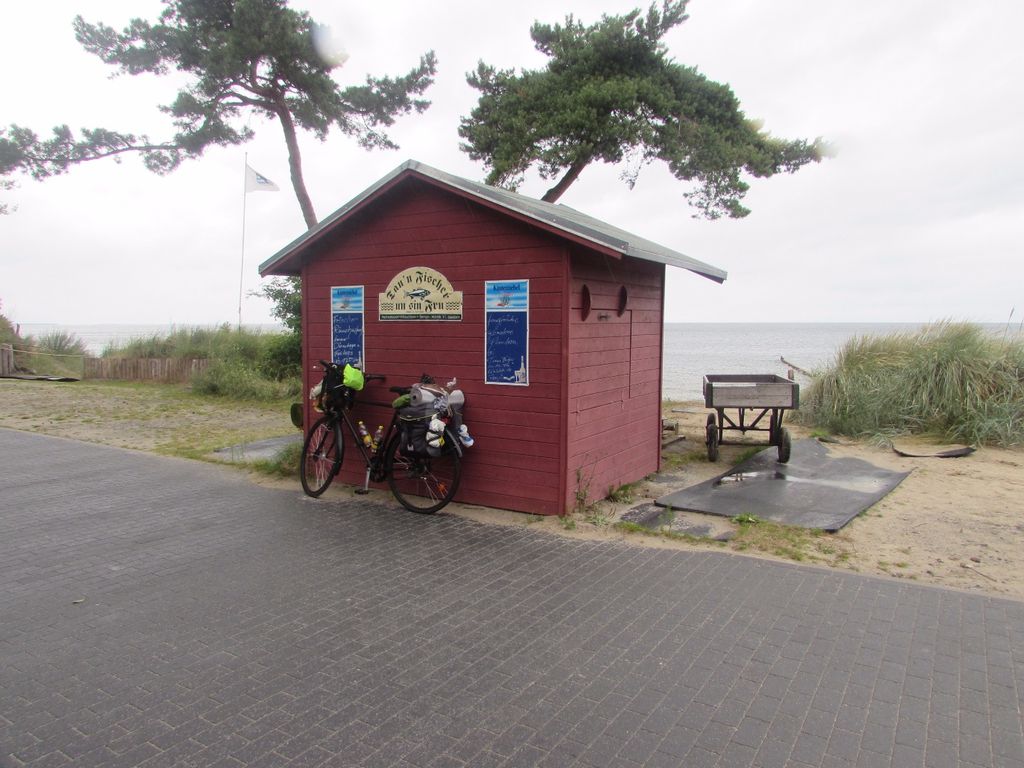
Деталь без проблем продержалась во время 20-дневной поездки по Швеции, Польше, Германии и Дании. Передняя сумка было все время до отказа заполнена едой, было пройдено немало ухабистых дорог. Детали прослужили на отлично и по-прежнему крепче камня.
Вот еще несколько полезных замечаний.
- Интересно, что эпоксидка не очень хорошо прилипает к ABS. Именно поэтому дополнительные отверстия, через которые она будет проникать внутрь и скреплять конструкцию, просто обязательны.
- Укреплять деталь снаружи гораздо сложнее, чем заполнять ее. Времени на первый вариант уходит масса, но заполненная деталь получается легче. Бесспорно, укрепленная деталь значительно прочнее, чем просто напечатанная и не укрепленная. Это легко проверить, если испытать на скручивание укрепленную и не укрепленную детали. Укрепленная подобна камню, обычная легко меняет форму.
- Второй метод укрепления гораздо проще и дает гораздо более опрятный результат. После застывания смолы почти ничего не надо чистить. А то, что получилось, имеет крепость гранита!
- Оба варианта заполнения при различных количествах стекловолокна дают одинаковое ощущение прочности и массивности. Однако тот, где волокна больше, теоретически и почти без сомнений должен выдерживать больший вес.
- По второму проекту узел получается более тяжелым, поскольку внутри он полностью состоит из стекловолокна и эпоксидной смолы. Вес немного уменьшается после удаления окружающего пластика. При этом, впрочем, изменятся и размеры детали. Поэтому о размерах нужно подумать заблаговременно и учесть снятие пластика при моделировании.
- Во втором проекте тоже можно предусмотреть желобки-бороздки и пустоты, тогда вес удастся снизить.
Перевод статьи Strengthening a 3D Printed Part с сайта Instructables.com
3d-tutorials.livejournal.com
3D печать в авиастроении
Внедрение трехмерной печати – важный виток в развитии авиастроительной отрасли. Аддитивное производство рассматривается, как альтернатива фрезерованию, штамповке и литью. Использование 3D принтеров и объемного сканирования позволит облегчить летательный аппарат, а значит, сократить издержки на топливо и материалы.
Преимущества 3D печати в авиастроении
Намного проще. Традиционные технологии, которые используются в авиационной промышленности, базируются на ручной сварке, применении ЧПУ, фрезеровальных станков, литейных форм. Такой подход требует больших затрат труда, времени и сырья.
Метод селективного лазерного спекания, как и послойное наплавление, осуществляется в автоматическом режиме, являясь более быстрым и экономным.
Оборудование может работать круглосуточно. При этом количество отходов на 70-95% меньше. Готовые детали получаются легче, благодаря чему снижается вес машины.
В сравнении с классическими методами, аддитивная печать снимает производственные ограничения – можно делать высокоточные запчасти без предварительной подготовки производственной линии, упрощая этап прототипирования.
Самолеты, напечатанные на 3D принтере
Пионером отрасли стала компания GE Aviation. Производитель авиационных двигателей обратил внимание на то, что использование разных сплавов в детали существенно улучшает её физико-технические свойства и даёт возможность вывести летные характеристики самолета на принципиально новый уровень. Традиционный метод литья не позволяет объединить разные материалы в рамках одного технологического процесса.
В GE Aviation начали работать над усовершенствованием форсунок. Для производства одной детали необходимо по отдельности изготовить 20 элементов, после чего соединить их в одной запчасти. 3D принтер по металлу дает возможность изготовить деталь из цельного куска материала, экономя время и деньги. Опытные образцы форсунок прошли сертификацию в 2016 году. Теперь производитель намеривается выпускать по 25000 деталей в год, сделанных с помощью принтера для трехмерной печати.
В научной лаборатории Airbus пошли еще дальше. Инженеры из Гамбурга создали беспилотный летательный аппарат, напечатанный на 3D принтере. Примечательно, что речь идет почти обо всех элементах корпуса, кроме модуля дистанционного управления и электронных пропеллеров. Беспилотник назвали «Thor».
Четырехметровый самолет успешно поднялся в воздух и преодолел 40 километровый маршрут из Гамбурга в Штад, где совершил посадку на заводе компании. Проект носит экспериментальный характер. На нем будут тестировать разные конструкции фюзеляжа, планера, формы крыла и прочих элементов корпуса. На базе «Тора» сделают самолет с цельным корпусом, максимально приближенный к серийным моделям.
3D печать уже используется в серийных самолетах Airbus. В широкофюзеляжных лайнерах А350 устанавливается напечатанный кронштейн в составе пилона двигателя. Деталь изготавливается из титанового порошка. В экспериментальных моделях А350 и узкофюзеляжных А320neoтестируются более 1000 деталей, сделанных методом лазерного спекания. Среди них преимущественно элементы интерьера.
Производитель авиадвигателей Safran Helicopter Engines в 2017 году представила линейку газотурбинных двигателей Aneto. Компактный силовой агрегат на 30% мощнее, чем установки аналогичных размеров. При этом устройство остается надежным и экономичным. В процессе сборки используются компоненты, сделанные методом трехмерной печати – впускные направляющие лопатки и вращающаяся камера сгорания. Компания налетала 25 часов, 35 раз подняв машины в воздух, – проблем не обнаружено!
В России над внедрением аддитивных технологий в авиапромышленности работают Всероссийский научно-исследовательский институт авиационных материалов и Томский политехнический университет.
Команда ВИАМ тестирует 3D-печатные комплектующие в двигателях для самолетов МС-21. В процессе производства агрегата ПД-14 используется завихритель фронтового устройства камеры сгорания, изготовленный с помощью селективного лазерного спекания, что сокращает себестоимость и время производства запчасти в 10 раз.
В ТПУ работают над замещением литых титановых деталей самолета на 3D-печатные. Исследователи отмечают, что доля титана в гражданских авиалайнерах достигает 15-20%. Если заменить литье объемной печатью, получится снизить массу самолета, а вместе с ней и расходы на горючее, сборку и обслуживание. Специалисты сосредоточились над работой с порошками титановых сплавов ВТ6 и ВТ9. Задача состоит в том, чтобы оптимизировать использование материала и добиться высоких ТТХ.
В американском «Боинг» не отстают от европейских коллег. Первой серийной моделью, в которой будут использоваться напечатанные металлические элементы, станет лайнер 787. Производитель заключил контракт с норвежской Norsk Titanium на печать титановых запчастей в промышленных масштабах. Себестоимость титановых комплектующих достигает 17 миллионов долларов – стоимость самолета $265 млн. Boeing заявляет, что в случае успеха, смогут снизить стоимость модели на 2-3 миллиона долларов.
make-3d.ru