Способы производства строительного цемента. Цементные технологии
Как делают цемент: технология производства цемента
Любое строительство или ремонтные работы невозможны без использования универсального строительного материала – цемента разных видов и марок. Мы настолько привыкли к этому продукту, что даже не задумываемся над проблемой, а как делают цемент. Можно ли его можно изготовить в домашних условиях и не переплачивать?
СодержаниеСвернуть
Сразу ответим на вопрос – можно ли сделать цемент своими руками? Имея необходимое оборудование и исходные материалы – получить цемент в домашних условиях можно. На данный момент времени в Российской Федерации большим спросом пользуются мини-заводы по производству цемента, мощностью порядка 120 000 тонн цемента в год. Производить же цемент для единичной стройки экономически невыгодно. Проще и дешевле купить этот необходимый строительный материал на заводе или в магазине.
Состав цемента
Цемент получается при длительном дроблении клинкера и гипса. Клинкер — продукт равномерного обжига до спекания однородной сырьевой смеси, состоящей из известняка и глины определённого состава, обеспечивающего преобладание силикатов кальция.
При измельчении клинкера вводят добавки: гипс СaSO4·2h3O для регулирования сроков схватывания, до 15 % активных минеральных добавок (пиритные огарки, колошниковую пыль, бокситы, пески) для улучшения некоторых свойств и снижения стоимости цемента.
Производство цемента на заводах
На данный момент времени производителями цемента используются три технологии производства связующего:
- Мокрый способ.
- Сухой способ.
- Комбинированный метод.
Стоит заметить что «сухую» технологию используют зарубежные производители цемента: Египет, Турция и Китай. «Мокрая» же технология традиционно используется отечественными цементными заводами.

Сухой способ
Здесь нет необходимости использовать воду. Исходный материал (глину и известняк) дробят на специальном оборудовании. Сушат и перемалывают в мелкодисперсную муку, смешивают пневматическим способом и подают на обжиг.
Образовавшийся в результате обжига цементный клинкер измельчается до соответствующей степени фракции, фасуется в упаковку и отправляется на склад готовой продукции. Данный способ позволяет снизить затраты на производство, однако отличается «капризностью» к однородности исходных материалов и является экологически опасным вариантом.
Мокрый способ
Неоспоримые достоинства данного метода заключается в возможности точного подбора состава исходного сырья при высокой неоднородности исходных компонентов: порода, вид породы и пр. Исходный материал (шлам) представляет собой жидкую субстанцию, содержащую до сорока процентов влаги.
Перед тем как сделать цемент, состав шлама корректируется в специальных технологических бассейнах. После выдержки сырья в бассейне, производится отжиг в специальных вращающихся печах и последующее измельчение.
Мокрый способ требует большего расхода тепловой энергии расходуемой на высушивание исходного сырья. Это существенно увеличивает себестоимость производства цемента, однако качество конечной продукции не страдает от возможной неоднородности клинкера, как при мокром варианте.
Комбинированные способы
Данная технология опирается на мокрый вид получения связующего. Промежуточную субстанцию обезвоживают по специальной технологии. Клинкер гранулируют с добавлением воды, после чего производят отжиг и последующее измельчение до той или иной марки цемента.
В числе достоинств комбинированного способа производства цемента: высокий выход «годного», возможность использования отходов металлургической промышленности.
Как делают белый цемент
Технология производства белого цемента незначительно отличается от технологии производства обычного «серого» материала. Как и обычный «серый» материал, белый цемент выпускают сухим и мокрым способом. Основное отличие технологии – обжиг исходного сырья при высокой температуре и резкое охлаждение в воде.
Клинкер белого цемента характеризуется как «маложелезистый» и содержит в своем составе: минеральные добавки, известняк, гипс, соли и другие компоненты. В качестве исходного сырья для клинкера используются карбонатная и глинистая порода (известняк, каолиновая глина, отходы обогащения, кварцевый песок).
В Российской Федерации белый цемент производится только на одном предприятии – ООО «Холсим (Рус) СМ» (до 2012 года ОАО «Щуровский цемент»). Большинство белого цемента поставляется на рынок России из-за рубежа следующими компаниями: «Холсим» (Словакия), «Cimsa иAdana» (Турция), «AalborgWhite»(Дания) и «AalborgWhite» (Египет).
Основное достоинство белого цемента его уникальная характеристика – белоснежность, а основной недостаток в разы большая стоимость по сравнению с обычным «серым» материалом.
Заключение
Теперь вы знаете, как делают цемент на заводе в общем случае. Информацию как правильно делать цемент во всех подробностях, цифрах, схемах, таблицах и других тонкостях смотрите в специальной литературе.
cementim.ru
Технология производства цемента | Новости в строительстве
Технология производства цемента сводится к получению цементного клинкера из сырьевой смеси , получаемого двумя способами : сухим и мокрым.
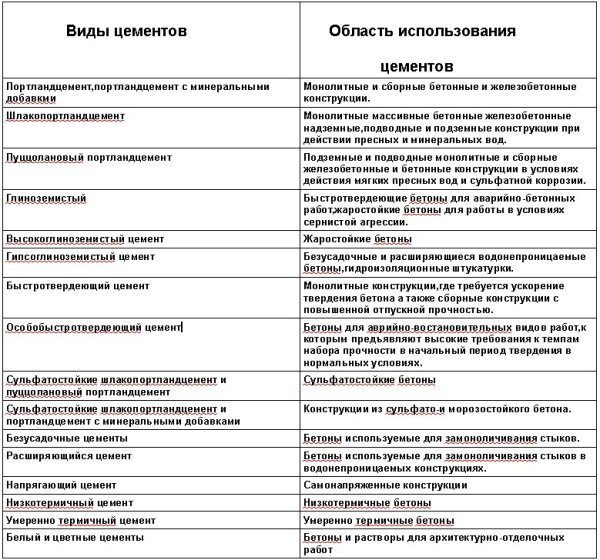
Виды цементов и область их использования.
Производство цемента для строительных нужд характеризуется следующими основными видами цемента: Портландцемент, шлакопортландцемент, гидрофобный и другие виды.
Для получения цемента используют цементный клинкер, которого получают путем обжига в печах сырьевой смеси из породы известняка и глины при высоких температурах. В зависимости от присутствия в сырьевой смеси наличия необходимых компонентов, таких как оксид кальция и алюмосиликатов,в состав водят различные добавки.
Все добавки водят с целью усиления важных строительных свойств цементного клинкера. Сырьевую смесь из глины и известняка приготавливают мокрым способом или в сухом виде из расчета на одну часть глины добавляют три части известняка. Для повышения качества сырьевого состава и уменьшения расходов на топливо в смесь добавляют поверхностно-активные добавки.Из всех выпускаемых промышленностью видов цементов наиболее важное значение имеет портландцемент.♣ Портландцемент и получение цементного клинкера
♦ Портландцемент это гидравлическое вяжущее которое способно твердеть в воде и на воздухе.Получают путем тонкого помола клинкера с добавлением соответствующих добавок.Клинкер представляет спекшуюся сырьевую смесь известняка и глины в виде зерен размером до 40 мм. Важнейшие свойства цемента,которые перечислены ниже, зависят на прямую от качества клинкера:
♦ Прочность а также скорость ее нарастания при твердении цемента,стойкость в различных условиях во время эксплуатации,долговечность.Во время помола к клинкеру в целях регулирования сроков схватывания вводят 1.5…3.5% гипса от массы цемента,в пересчете на ангидрид серной кислоты SO3.Портландцемент выпускают без добавок или с активными минеральными добавками в количестве до 15% от массы цемента.Технология получения портландцемента в основном сводится к следующим операциям:
Изготовлению сырьевой смеси надлежащего состава, ее обжига до спекания и помола. Для получения качественного портландцемента в клинкере должны содержаться следующие важнейшие оксиды (химический состав):
1.CaO-62…..68%,
2.SiO2-18…26%,
3/Al2O3 -4…9 %,
4/Fe2O3 -0.3….6 %.
♦ Другими словами можно сказать что для производства портландцемента следует использовать сырьевые материалы с большим содержанием оксида кальция и алюмосиликатов,такие как известняки и глины.В известняках преобладают карбонат кальция а в глинах различные водные алюмосиликаты (галлаузит, монтмориллонит, каолинит и другие), имеющие следующую химическую формулу: Al2O3 * nSiO2 * mh3O.Кроме этого в глинах могут содержаться диоксид кремния в виде тонкого кварцевого песка и оксида железа.
♦ Необходимый химический состав цементного клинкера можно получить при соотношении глины и известняка 1 : 3 по массе.Известняк и глину могут заменить и другие материалы,например мергели (природная смесь известняка и глины).Мел может заменить известняк.Кроме этого в сырьевую смесь можно ввести корректирующие добавки,пиритные огарки или железную руду,если в исходной глине мало оксидов железа.Если необходимо повысить содержание диоксида кремния в смеси вводят кварцевый песок.
Классификация клинкеров в зависимости от содержания основных минералов
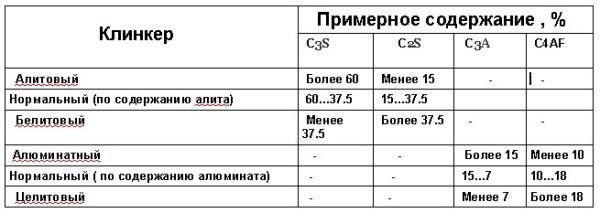
Классификация клинкеров в зависимости от содержания основных минералов
Производство цемента
♦ Для получения цементного клинкера сырьевую смесь приготовляют сухим или мокрым способом.Каждый способ имеет свои достоинства и недостатки.При мокром способе легче достигается тонкое измельчение исходных материалов и получение их гомогенной смеси.Но,зато возрастает расход топлива на обжиг который значительно больше чем при сухом способе.Получаемая при мокром способе суспензия сырьевых материалов содержит 32…45 % воды.Для повышения производительности печей и уменьшения расхода топлива,нужно стремиться к уменьшению влажности сырьевого шлама без ухудшения его текучести за счет использования поверхностно-активных добавок (ПАВ).
Рисунок-1. Вращающаяся печь размером 5 х 185 м.
1-течка для подачи шлама, 2- фильтр-подогреватель, 3-цепная завеса, внутрипечной теплообменник, 5-бандаж, 6-венцовая шестерня, 7-привод печи, 8-корпус печи, 9-огнеупорная футеровка, 10 устройство для охлаждения корпуса печи, 11- уплотнения горячего и холодного концов печи, головка печи, холодильник, 14-роликоопоры.
♦ Сырьевой шлам для обжига поступает во вращающуюся печь .Печь представляет собой длинный цилиндр (например длина-185 м с диаметром 5 метров),который медленно вращается вокруг своей оси.печь имеет наклон к горизонту а сырьевой шлам (сырьевая смесь) загружается в верхнюю часть и потом постепенно перемещается к нижнему концу печи.Из нижнего конца печи вдувается топливо в виде природного газа или пылевидного угля.При сжигании топлива,горячие газы двигаются навстречу сырьевой смеси,которая перемещаясь к нижнему концу печи претерпевает сначала физические превращения а затем существенные химические превращения.Происходит это следующим образом:
♦ В начале печи сырьевая смесь подсушивается и передвигается дальше попадая в зону с температурой 550…800 °С.Здесь происходит дегидратация водных алюмосиликатных глины.Процесс сопровождается образованием соединений, которые характеризуются сильно разрыхленной структурой частиц.при этом внутренняя энергия вещества возрастает и повышает его реакционно-способность.После этого сырьевая смесь попадает в зону с температурой 900…1000 °С,где происходит диссоциация карбоната кальция и образование его оксида.При этом реакции протекают в твердом состоянии между продуктами дегидратации глины (которые содержат оксиды алюминия и диоксид кремния) и оксидом кальция.
♦ При этом оксид кальция с оксидом алюминия образуют однокальциевый алюминат CaO * Al2O3.Оксид кальция одновременно реагирует с диоксидом кремния и образуют в больших количествах двухкальциевый силикат 2CaO*SiO2.Передвигаясь далее сырьевая смесь нагревается до температуры 1200…1250 °С, а протекании реакций в твердом состоянии усиливается.Завершается образование двухкальциевого силиката,а уже имеющийся однокальциевый алюминат насыщается далее оксидом кальция и образует некоторое количество еще более основного трехкальциевого алюмината 3CaO* Al2O3.Но часть оксида кальция все еще остается в свободном виде.
Рисунок-2. Нарастание прочности минералов клинкера портландцемента
♦ Передвигаясь еще дальше, сырьевая смесь нагревается до температуры 1450°С, где происходит частичное плавление материала и завершается реакция образования силикатов и алюминатов кальция.материал спекается образуя цементный клинкер размером 4…20 мм.После этого,выходящий из печи цементный клинкер быстро охлаждают в специальном холодильнике.При охлаждении удается избежать образование крупных кристаллов в клинкере и сохранить вместе с тем в не кристаллизованном виде стекловидную фазу.Если клинкер не охлаждать ,получиться цемент с пониженной реакционной способностью с водой.
♦ Цементный клинкер размалывают в порошок при этом добавляют небольшое количество двуводного гипса для регулирования сроков схватывания цемента.Чем выше тонкость помола,тем сильнее возрастает активность цемента .Средний размер зерен портландцемента составляет примерно 40 мкм.Толщина гидратации зерен через 6…12 мес. твердения не превышает 10…15 мкм.Таким образом можно сказать, что при обычном помоле портландцемента примерно 40…40 % клинкерной части не участвует в твердении и формировании структуры камня.
Степень гидратации клинкерных минералов во времени от полной гидратации,%
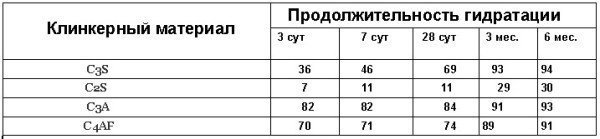
Степень гидратации клинкерных минералов во времени от полной гидратации
♦ С увеличением тонкости помола цемента увеличивается и степень гидратации цемента,возрастает также и содержание клеящих веществ (гидратов минералов) и повышается прочность цементного камня.Исходя из вышесказанного, можно сказать ,что цементы должны иметь тонкость помола характеризуемую остатком на сите № 008 не более 15 %.Обычно она равна 8…12 %.Тонкость помола цемента характеризуется также величиной удельной поверхности (см²/г)-суммарной поверхностью зерен в одном грамме цемента.Удельная поверхность цементов составляет 2500…3000 см²/г).Считается что прирост удельной поверхности цемента на каждые 1000 см²/г повышает его активность на 20…25 %.
Читай далее производство портландцемента
♣ Быстротвердеющий портландцемент (БТЦ)
Является портландцементом с минеральными добавками,от обычного отличается более интенсивным нарастанием прочности в начальный период твердения.Достигается это путем более тонкого помола цементного клинкера (до удельной поверхности 3500…4000 см²/г), а также повышенным содержанием трехкальциевого алюмината (60…65 %).Быстротвердеющий портландцемент выпускают марок М-400 и М-500.используется широко при зимних бетонных работах а также в производстве железобетонных конструкций.Так как цемент издает повышенное тепловыделение,его не используют в массивных конструкциях.
♣ Пуццолановый портландцемент
Получают путем совместного помола клинкера,25…40 % от массы цемента активных минеральных добавок и гипсового камня (ГОСТ 4013-82).Клинкер для этого вида цемента должен содержать не более 8%трехкальциевого алюмината и не более 5% оксида и марганца.В остальном свойства пуццоланового портландцемента не отличаются от свойств портландцемента.выпускается марок М-300 и 400.
♣ Вяжущее низкой водопотребности (ВНВ)
Это новое эффективное вяжущее на основе портландцементного клинкера.Обладает минимальной водопотребностью среди всех существующих сегодня минеральных вяжущих.Нормальная густота ВНВ составляет 16%,а обычного портландцемента -24…30%.Получают ВНВ по более новой технологии которая заключается в совместном помоле (механохимической активации) клинкера портландцемента и суперпластификатора С-3.ВНВ получают трех видов:
1.ВНВ-100-без минеральных добавок;
2.ВНВ-50-совместным помолом компонентов следующего состава:(50 % портландцемента марки М-400,50 % активной минеральной добавки,С3;
3.ВНВ-30-состоит из 30 % портландцемента М-400,70% активной минеральной добавки,С3.
В качестве активной минеральной добавки используют гранулированные шлаки,золу-унос,диатомиты,туфы,песок и другие.Прочность ВНВ существенно зависит от количества вводимой минеральной добавки.Удельная поверхность ВНВ 4800…5200 см ²/г.Морозостойкость бетонных образцов на основе ВНВ,составляет более 500 циклов.Сроки схватывания ВНВ можно широко регулировать от 30 минут до 24 часов при нормальных условиях твердения.Прочность при сжатии для ВНВ -100 составляет 90…100 МПА,для ВНВ-50 составляет-60 МПА,для ВНВ-30 прочность при сжатии составляет 40…50 МПА.
♣ Цветной портландцемент
♦ Цветной портландцемент выпускается следующих марок: М 300,400 и 500 -светло-желтого,желто-золотистого светло-розового,оранжевого,розового,светло-коричневого,красного,голубого,зеленого и черного цветов.Получают такой цемент путем совместного помола белого и цветного клинкеров с добавлением минеральных и органических красителей,минеральных добавок и гипса.В цветном портландцементе должно содержаться не более 15 % красковой руды,минеральных, синтетических или природных пигментов.
♦Для того чтобы расширить палитру таких цементов вводят в их состав органические красители.В результате получают подкрашенные цементы с разнообразной по тону окраске. Пигменты вводимые в состав цветных цементов должны иметь тонкость помола не менее 3000 см²/г, а их количество вместе с разбеливающими добавками не должно снижать активность цемента.
Содержание пигментов в цветном цементе для наглядности представлены в таблице
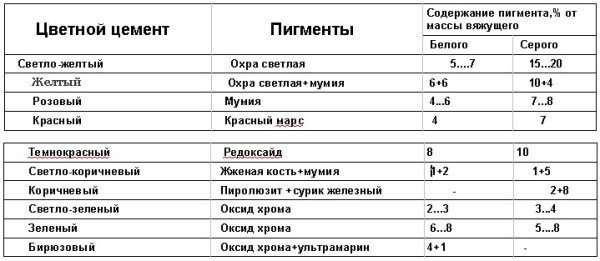
Содержание пигментов в цветном цементе
♣ Сульфатостойкий портландцемент
♦Получают такой цемент из клинкера которого нормируют минералогическим составом.Содержание в этом цементе трехкальциевого силиката должно быть не более 50%, трехкальциевого алюминия -не более 5% и сумма трехкальциевого алюмината и четырех кальциевого алюмоферрита не более 22%.
♦Введение активных и инертных минеральных добавок не допускается.Этот цемент,являясь по существу белитовый ,способен несколько замедлить твердение в начальные сроки и обладает низким тепловыделением.Сульфатостойкий портландцемент выпускается М400,используют активно для получения бетонов используемых в пресных и в минерализованных водах.
♣ Белый портландцемент
♦Белый портландцемент (ГОСТ 965-78) получают из сырьевых материалов,которые имеют минимальное содержание окрашивающих оксидов (железа,хрома,марганца).Сырьем для получения белого портландцемента служат мраморы и ” чистые ” известняки а также белые каолиновые глины.Производят более тонкий помол цементного клинкера с остатком на сите № 008 не более 12 %.Степень белизны является основным критерием или свойством при определении
stroivagon.ru
Производство цемента - способы и технологии
Цемент – универсальный строительный материал, используемый в чистом виде, а также как компонент штукатурных смесей, бетона и железобетона. Производство цемента – это энергоемкий и дорогостоящий процесс, осуществляемый разными способами. Традиционные методики основаны на предварительном получении клинкера. Гораздо дешевле конечный продукт, изготовленный по бесклинкерной технологии или кустарным методом.
Технологии производства с клинкером
1. Мокрый.
Крупные куски известкового компонента (мела) и глины сначала дробят, затем перемалывают в мельницах или измельчают в болтушках с помощью воды. Глиняный шлам перекачивается в мельницу, где он перерабатывается вместе с известняком. В специальных бассейнах выравнивается химический состав сметанообразной шламовой смеси, затем она подается в наклонную печь – вращающийся барабан диаметром 7 м и длиной около 200 м. На выходе из печи (в месте горения топлива) при температуре около 17 000 °C происходит спекание клинкера. Его охлаждают, дробят и перемалывают с гипсом и минеральными добавками (не путать с пластификаторами для цементного раствора), сушат, вновь измельчают.
Метод применяют, если влажность добытых ископаемых больше 10% или если глина и известняк имеют низкую твердость. Плюс: упрощение измельчения с помощью воды. Минус: большой расход тепла.
2. Сухой.
Схема меняется на стадии изготовления известково-глиняного шлама. Его сушат и перемалывают в сырьевую муку (операции проводятся одновременно или раздельно). Плюс: при образовании клинкера вдвое сокращается длина печи и расход топлива; если в шихту ввести СаС12, то реакция идет при пониженной температуре. Эта методика получает широкое распространение на цементных заводах, она более приемлема при влажности сырья менее 10%.
3. Комбинированный.
Начало процесса сходно с мокрым производством. Подготовленный шлам влажностью до 45% обезвоживается в вакуумфильтре до 20%, в смесь добавляется пыль для поглощения воды. Обжиг производится в шахтной печи, из нижней части которой выгружается клинкер. Плюсы: экономия энергоносителей, упрощение конструкции оборудования.
Для декоративного оформления фасадов применяют белый портландцемент. Белизну материалу придают гипс, диатомит и клинкер с малым содержанием железа, марганца и титана. Технология получения цемента отличается повышенными требованиями к чистоте сырья, проведением отжига на топливе, не образующем золы. Клинкер отбеливают в три этапа: вводят в его состав хлориды, выдерживают в специальной жидкости, охлаждают в конвертированном газе.
Без клинкера
В качестве сырья используют зольную пыль, известняк, глину с содержанием песка, минеральные отходы с кальцием, алюминием, кремнием, доменный шлак после выплавки чугуна. Этапы получения цемента «холодным способом»:
- плавление сырья при 1 450 °C в плавильной печи, работающей на угле, жидком топливе или газе;
- водное охлаждение расплава с одновременной грануляцией, помол гранулята;
- смешивание гранул с определенным количеством порошкообразного шлака, песка, глины или извести, добавление специального активизатора (2 – 5%).
Преимущества метода: исключаются расходы на строительство барабанной печи, снижается потребление топлива, сокращается технологическое время. Даже при мелкосерийном производстве себестоимость продукта уменьшается втрое.
Изготовление своими руками
При возведении каменного забора или бетонировании дорожки иногда используют цемент собственного производства: в домашних условиях изготавливают его оригинальный заменитель. Смесь получают, взяв по 1-й части серы и смолы (расплавленных в разных емкостях), 2 части просеянного песка, 3 части свинцового глета (оксида свинца). Поверхность, на которую наносится домашний цемент, предварительно покрывают олифой и высушивают.
stoneguru.ru
Цемент — из чего и как делают, и как проходит процесс производства
Цемент — из чего и как его делают — этот вопрос интересует многих обывателей. Необходимо отметить, что для его производства требуется достаточно сложное оборудование, хотя технология не очень сложна.
Цемент — из чего делают и как проходит процесс производства? ↑
Видео — цех по производству сырья для цементного заводаНачнем с того, что основной компонент в цементном производстве — это клинкер. Это специальная смесь из двух природных материалов, которые проходят обжиг в печах при высоких температурах. Как было сказано выше, материалов два:
- Известь;
- глина.
Стандартная рецептура клинкера — 75% извести, 25% глины. Иногда вместо глины используют другие природные материалы, которые по своему составу и качеству похожи на глину. К примеру, доломит или трепел. Клинкер, смешанный из двух компонентов искусственным путем, так и называется «искусственный». Но есть в природе и натуральный клинкер, который можно использовать уже в готовом виде. Одним из представителей такого материала является «известковый мергель». Это горная порода.
Но по причине, что месторождения природного клинкера встречаются достаточно редко, основная масса цементных заводов используют в производстве искусственный. К тому же известь и глина являются распространенными природными материалами.
Но клинкер — это основное, но не единственное сырье для производства цемента. В процессе помола клинкера добавляются гидравлические материалы, которые улучшают цементные качества и влияют на скорость затвердевания. Чаще всего добавляют гипс в размере 3% от объема клинкера или доломит в размере 15%.
Процесс производства ↑
Видео сырья в дробильном цехе в производстве цементаПервый этап — это смешение компонентов для производства клинкера. Второй этап — это обжиг, где происходит образование самого клинкера, когда два материала соединяются между собой под действием высокой температуры. Это спекшаяся масса, состоящая из зерен с размерами небольшого ореха.
Третий этап — помол. Этот процесс происходит внутри шаровых мельниц, похожих на большой горизонтальный барабан, внутри которого заложены металлические шары и конусы (цильбепсы). Попадая внутрь мельницы, клинкер измельчается до состояния порошка.
Внимание! Чем тоньше помол, тем марка цемента выше, то есть его характеристики лучше.
Соединение цемента с водой должно происходить по всей поверхности частиц. И чем большей площадь поверхности, тем лучше цементные качества. То есть маленьких частиц больше, чем больших, а соответственно общая площадь соприкосновения увеличивается. Можно привести пример. Один грамм стандартного цемента имеет удельную площадь 2000-3000 см2. Тот же вес высокопрочного цемента имеет удельную площадь уже 6000 см2.
Технологии производства цемента ↑
В основном все технологии отличаются друг от друга только одним процессом — это подготовка сырья. Таких технологий три:
- Мокрая.
- Сухая.
- Комбинированная.
В первом варианте как компонент для клинкера используется мел, а не известь. Для этого происходит смешение всех составных частей в специальном барабане, где происходит не только смешение, но и измельчение. Обязательное условие — это вода, которая так же добавляется в барабан. Поэтому данная технология и носит название «мокрая».
Полученная таким способом масса носит название шихта, ее влажность обычно 30%-50%. Она поступает по технологической цепочке в печь обжига, где превращается в шарики. Это и есть клинкер, который подвергается помолу.
Сухой способ многие специалисты считают будущим цементного производства. Здесь многие процессы объединены, что сокращает срок выпуска цемента и удешевляет его производство. К примеру, процесс помола и сушки компонентов можно проводить в шаровой мельнице, куда подаются горячие газы, идущие навстречу материалам. Поэтому шихта представляет собой измельченный порошок.
По своему названию комбинированный способ уже говорит о том, что в его процессе используются все этапы двух предыдущих технологий. Но и здесь есть отличия. К примеру, на некоторых заводах шихта, произведенная мокрым способом, высушивается в специальных фильтрах, где ее влажность доводиться до 18%, То есть получается полусухая смесь.
Другой способ — это когда все происходит наоборот. То есть, сначала готовится сухая смесь из компонентов, затем в нее добавляется вода в размере 10%-14%. Происходит гранулирование материала, и только после этого его подают на обжиг.
Вот так кратко можно ответить на вопрос, из чего делается цемент и по каким технологиям. Как видите, чтобы разбираться во всем тонкостях производства нужно обязательно быть специалистом.
mastter.ru
ООО «ЦЕМЕНТНЫЕ ТЕХНОЛОГИИ» - г. Стерлитамак (республика Башкортостан)
Общие сведения
Юридическое наименование организации:ОБЩЕСТВО С ОГРАНИЧЕННОЙ ОТВЕТСТВЕННОСТЬЮ «ЦЕМЕНТНЫЕ ТЕХНОЛОГИИ»
Регион: г. Стерлитамак (республика Башкортостан)
Юридический адрес:453104, Республика БАШКОРТОСТАН, г. СТЕРЛИТАМАК, ул. ПРОФСОЮЗНАЯ, 10
Руководство организации:Директор Мяжитов Рафаэль Сяитович
Основной вид деятельности (по классификатору ОКВЭД)Организация «ЦЕМЕНТНЫЕ ТЕХНОЛОГИИ», ООО осуществляет следующие виды деятельности:Оптовая торговля прочими строительными материалами(Оптовая торговля, включая торговлю через агентов, кроме торговли автотранспортными средствами и мотоциклами / Оптовая торговля несельскохозяйственными промежуточными продуктами, отходами и ломом / Оптовая торговля лесоматериалами, строительными материалами и санитарно-техническим оборудованием / Оптовая торговля лакокрасочными материалами, листовым стеклом, санитарно-техническим оборудованием и прочими строительными материалами)
Отрасль народного хозяйства (по классификатору ОКОНХ)Оптовая торговля(Торговля и общественное питание / Внутренняя торговля)
Информация о государственной регистрации
ОГРН (Основной государственный регистрационный номер): 1030202380515
Орган государственной регистрации:Инспекция МНС России по г. Агидель Республики Башкортостан.
Дата регистрации: 3 июля 2001 года
Справочная информация
ИНН (Идентификационный номер налогоплательщика): 0253010786
Форма собственности (в соответствии с ОКФС):Частная собственность
Организационно-правовая форма (в соответствии с ОКОПФ):Общества с ограниченной ответственностью
Вид организации по классификации ОКОГУ:Организации, учрежденные гражданами
Местонахождение организации
Адрес организации:453104, Республика БАШКОРТОСТАН, г. СТЕРЛИТАМАК, ул. ПРОФСОЮЗНАЯ, 10
Организация ООО «ЦЕМЕНТНЫЕ ТЕХНОЛОГИИ»: общая сводка
Основным видом деятельности организации указано "Оптовая торговля прочими строительными материалами" (при регистрации компании), отрасль хозяйства - "Оптовая торговля". Юридическое лицо «ЦЕМЕНТНЫЕ ТЕХНОЛОГИИ», ООО зарегистрировано в регионе г. Стерлитамак (республика Башкортостан) по адресу 453104, Республика БАШКОРТОСТАН, г. СТЕРЛИТАМАК, ул. ПРОФСОЮЗНАЯ, 10. Руководит предприятием Мяжитов Рафаэль Сяитович (Директор). Организация была зарегистрирована 3 июля 2001 года под регистрационным номером 1030202380515 (ОГРН) в органе гос. регистрации Инспекция МНС России по г. Агидель Республики Башкортостан.
www.b2b-project.ru
Бетон: технологии будущего | Мастер по дому
В XXI в. Цементный раствор получит формирование как один из ключевых строительных материалов. Уже сегодня используются более очень много видов разных цементных растворов — от очень легких с плотностью 100 кг/м3 — до очень крепких с прочностью более 100 мпа — и широкое многообразие особенных цементных растворов с различными комплексами параметров.
Сравнительная простота и доступность бетонной технологии, широкая возможность применять районное сырье и вторичные отходы промышленности и энергетики, невысокая энергопотребность производства, хорошая цена и широкая возможность в воплощении всевозможных архитектурно-строительных решений — это все считается гарантией широкого использования цементного раствора в строительных работах.
Сегодня под термином «цементный раствор» предполагают большую гамму разных ремонтных композитов гидратационного и прочих видов твердения. Тут и традиционный тяжкий цементный раствор, и легкие ячеистые цементные растворы, и мелкозернистые цементные растворы, растворы, мастики, и фибробетоны, и особые цементные растворы, также с применением компонентов на полимерной основе и очень разных вяжущих веществ. Разнообразие видов цементного раствора обусловливает его удачное использование в условиях рыночной экономики и тех. прогресса.
В сегодняшних условиях цементные растворы становятся многокомпонентными, при их приготовлении широко применяются химические модификаторы структуры и параметров, оживленные минеральные ультрадисперсные элементы и ряд прочих действенных добавок.
В сегодняшней технологии цементного раствора с цепью управления структурообразованием, технологией производства и регулированием параметров материала применяют:
— композиционные вяжущие на разной основе (на цементе, гипсе, магнезиальных вяжущих и др.), являющиеся многокомпонентными вяжущими невысокой водопотребности; — комплексные модификаторы структуры и параметров, включающие в себя разные химические модификаторы и оживленные минеральные элементы, также ультрадисперсные; — минеральное сырье заполнителей, обеспечивающее получение экономичных и долговечных цементных растворов; — интенсивную процедуру, обеспечивающую гомогенизацию состава и создание условий благоприятного взаимные действия составляющих в процедуре появления структуры материала и ее упрочнения
основу сегодняшней технологии цементного раствора составляет создание очень качественного искусственного каменного черепка (ненатурального камня), отличающегося высокой дисперсностью, небольшой дефектностью и стойкостью структуры, также благодаря уменьшению ее перестройки в процедуре твердения.
На его основе создаются как правило очень разные высококачественные цементные растворы путем вставки в структуру материала добавочных составляющих и ее разновидности:
— при введении разных минеральных заполнителей — качественные конструкционные цементные растворы; — при регулировании воздушной фазы — разные варианты очень легких конструкционных цементных растворов и качественных бетонов ячеистого типа с очень высокими теплозащитными характеристиками; — при введении тонкодисперсных наполнителей на минеральной основе и регулировании воздушной фазы — растворы разного направления; — при введении дисперсных из волокна материалов — фибробетоны с широким регулированием параметров и возможностей; — при введении пигментов, особенных каменных материалов и использовании особенной технологии — разные варианты архитектурно-декоративного цементного раствора; — при введении отходов индустрии — получение цементных растворов с гарантированной экологической безопасностью вместе с утилизацией отходов; — при введении полимерных составляющих получение широкой гаммы П-бетонов, также для работ по ремонту, реставрации, декоративных цепей и др.; — при введении особенных элементов — получение особенных видов качественных цементных растворов — электротехнических, защитных и др.; — при введении напрягающих добавок — получение цементного раствора для самонапряженных конструкций.
В строительных работах вместе с классическими обыкновенными тяжёлыми цементными растворами с прочностью 10 — 50 мпа для разных видов конструкций получают использование новые эффектные Типы цементных растворов: очень прочные цементные растворы, цементные растворы очень высокой долговечности, безусадочные, расширяющиеся и напрягающие цементные растворы, цементные растворы, приготовленные из литых смесей бетона, особые цементные растворы, также на новых композиционных вяжущих, новые Типы легких цементных растворов и ряд прочих.
Достижения ремонтного материаловедения дали возможность соединить в общий комплекс хорошие положительные характеристики различных групп цементных растворов. Так возник новый класс цементных растворов — качественные цементные растворы. Это многокомпонентные цементные растворы, в которых применяются композиционные вяжущие вещества, химические модификаторы структуры, параметров и технологии, оживленные минеральные элементы и расширяющие добавки. Многокомпонентность системы дает возможность управлять структурообразованием на всех стадиях технологии. Качественные цементные растворы — это не только большие показатели параметров, но и большая методика, обеспечивающая получение материала отличного качества.
Композиционные вяжущие собой представляют товар механохимической активации в регламентированных условиях портландцемента или иного вяжущего с химическими модификаторами, содержащими водопонижающий ингредиент, и добавками на минеральной основе. Вместо модификаторов и активных элементов могут применятся следующие вещества и материалы, которые влияют на реологию смеси, структуру и характеристики материала, кинетику физико-химических процессов, эксплуатационную надежность:
— комплексы химических модификаторов разного направления; — дисперсные наполнители-разбавители; — ультрадисперсные наполнители-уплотнители и активизаторы; — элементы, управляющие объемными изменением структуры; — элементы, разрешающие управлять физико-химическими процессами твердения и обеспечивающие долговечность цементного раствора; — элементы, придающие цементному раствору особые свойства; — элементы, разрешающие одновременно с химическими модификаторами управлять реологией смеси из бетона и процессами отвердевания; — дисперсные волокнистые материалы; — элементы, регулирующие внутренее тепловыделение материала.
Сегодняшняя методика цементного раствора рекомендует строителям большое разнообразие цементных растворов, разного направления и технологии. В ближайщее время это разнообразие еще становится больше.
На основе новых видов вяжущих и модификаторов получат распространение особобыстротвердеющие цементные растворы с прочностью через 3…4 часа 40…50 мпа и выше, что обеспечит большую экономию энергоносителей в строительных работах, цементные растворы твердеющие при отрицательной температуре до -30C, цементные растворы со особыми характеристиками: защитные, электротехнические, антибактерицидные, жаростойкие и др. Делая больше многообразие и объемы использования П-бетонов, в которых комбинирование минеральной и органической структур открывает возможности получения материалов с очень различными характеристиками и направлением. Для получения полимер-цементных цементных растворов для бетонополимеров и цементных растворов с полимерными заполнителями, наполнителями и волокнами будут употреблены новые мономеры и полимерные материалы, новые вяжущие и композиции составляющих, передовые технологии получения материалов.
Для цели ресурсосбережения и исправления теплотехнических параметров материала получат широкое развитие воздухонаполненные цементные растворы и изделия. При всем этом будет становиться больше степень воздухонаполнения и повышаться качество материалов. Ячеистые цементные растворы разных вариантов получения, легкие цементные растворы на пористых заполнителях, также безобжиговых и полимерных, изделия с сотовой и остальными системами сложения дадут возможность применять более улучшенные технологии изготовления, большее многообразие и многокомпонентность состава и сырья.
Получат распространение Типы архитектурного и декоративного цементного раствора: разноцветные цементные растворы, цементные растворы с разной композицией плоскости, цементные растворы — декоративные камни, не только повторяющие вид ценных облицовочных настоящих камней, но и разрешающие получить новые разные варианты материалов для отделки, не уступающих по своим характеристикам натуральным материалам, цементные растворы с верхней декоративной и защитной облицовкой.
Получат распространение биотехнология цементного раствора и новейшие материалы на ее основании. Процессы, происходящие в природе, станут основой новой отрасли строительной индустрии, производящей экологические чистенькие и эффектные материалы для строительства. Будут сделаны керамобетоны, соединяющие специфики 2-ух технологий и расширяющие возможности разновидности структуры и повышения многообразия параметров материала.
Получат распространение очень тонкие цементы и цементные растворы на их основе, материалы с массопереносом раствора и его следующей кристаллизацией в порах материала, цементные растворы с фиксированной начальной композицией и уменьшенной усадкой, разные варианты пропитанных цементных растворов, фибробетонов.
Более масштабное распространение получат мелкозернистые цементные растворы. Не маленькая однородность структуры и широкая возможность ее разновидности дают возможность получить мелкозернистые цементные растворы очень разных параметров и направления. Спецификой формирования технологии цементного раствора в последние несколько десятков лет считается внушительное повышение ее региональной составляющей. К примеру, из 10 — 12 докторских работ, защищаемых каждый год в Российской Федерации по материалам для строительства, на долю москвы доводится только одна — две работы. Другие — достижение разных регионов государства.
В СПБ удачно развиваются работы по химизации цементного раствора, защитным цементным растворам, сухим смесям, фибробетону, аэрированным теплозащитным цементным растворам. В пензе — по серным цементным растворам, высокопрочным цементным растворам, цементным растворам с применением грунтового сырья, легким цементным растворам на местном сырье. В белгороде — по цементным растворам на основе отходов горно-обогатительных комбинатов, ряду особенных и дорожных цементных растворов. В воронеже — по поробетонам, цементным растворам на каучуковом вяжущем. В саранске — по биотехнологии цементных растворов, по цементным растворам с каркасной композицией. В казани — по высокопрочным и влагостойким цементным растворам для туннелей метро, по новым гипсовым цементным растворам, по новым добавкам для цементных растворов. В уфе — по прочным к удару и коррозионностоким цементным растворам. В иванове — по цементным растворам со особыми декоративными покрытиями. В ростове-на-дону — по новым видам фибропенобетона. Много интересного и полезного предлагается и в остальных регионах. Во всех регионах особенное место занимают работы по вовлечению в производство местного натурального и техногенного сырья, благодаря чему достигается понижение цены строительства и повышение числа мест для работы
Ю.М. Баженов — глава государства ассоциации ученых и профессионалов в области ремонтного материаловедения, врач технических наук, достойный функционер науки РФ, академик русской академии архитектуры и ремонтных наук, академик мировой и русской инженерной академии.

masterdom35.ru
Цемент | Строительные материалы и технологии
-
Общие сведения, историческая справка.
Цемент (нем.Zement),собирательное название порошкообразных вяжущих веществ, способных при смешивании с водой (иногда с водными растворами солей) образовывать пластичную массу, приобретающую затем камневидное состояние. Основные виды: портландцемент, шлаковые и пуццолановые цементы, глиноземистый цемент, специальные виды цемента (например, кислотоупорный).
Сырьём для него служат известковые, маргелистые, глинистые породы и различные добавки-шлак, бокситы и др.Цемент обладает важным свойством твердеть в воде.
Историческая справка
В 1822г. в Петербурге вышла книга “Трактат об искусстве приготовлять хорошие строительные растворы”.Ещё через несколько лет её автор-русский строитель Егор Челиев издал новую книгу о том, как приготовлять цемент и бетон и как применять их для скрепления кирпичей или камней при строительстве набережен, стен и фундаментов сооружений ит.п.
В 1824г. в Англии Д.Аспинд взял патент на изготовление цемента из известковой пыли, смешанной с глиной и обожжённой при высокой температуре. Полученный при этом ноздреватый серый материал, называемый клинкером, он размалывал и смешивал с водой. При застывании образовывался очень прочный строительный камень, который изобретатель назвал портландцементом, так как по цвету и прочности он напоминал строительный камень, добываемый в английском городе Портланде.
В связи с ростом потребности в цементе в Подольском уезде выросли несколько цементных заводов, и, главным образом, возник (1875г.) крупный цементный завод Московского Акционерного Общества. Основателем завода был московский купец Пороховщиков. Завод построен на земле, принадлежавшей крестьянам д.Выползово. Землю эту купил подольский голова Ф.С. Добротворский и перепродал ее Пороховщикову, который в течение 10 лет построил небольшой завод, вложив свой капитал. Этот небольшой завод в руках Московского Акционерного Общества превратился в мощный цементный завод.
2. Основные технические свойства.
Устройство цементного завода
Цемент приготавливается из особенного желтовато-зеленого известняка, называемого "зеленкой"; слой его довольно толст (до 0.7 м) и встречается под землей 4 раза на глубине до 10 м; он очень мягок и потому легче других выламывается. Чаще для устройства цементного завода известковую гору разрабатывали сносом, т.е. часть горы вместе с верхними суглинистыми отложениями "сносят вниз", выбирая попадающийся камень и сортируя его. Затем "зеленка разбивалась на куски до 10 см в диаметре и складывалась в низкие, до 1. м штабеля для подсушки. Часть берега разравнивалась для укладки рельсов, установки обжигательных печей и вывоза материалов из-под горы наверх.
Получение силикатного цемента (портландцемента)
Обычный силикатный цемент, или портландцемент, представляет собой зеленовато-серый порошок, который при смешивании с водой затвердевает на воздухе (или в воде) в камнеподобную массу. Портландцемент получают мокрым или сухим способом. При мокром способе сырьё размалывают в мельнице, дробят, затем погружают в бассейн, размешивают и частично измельчают и потом в виде полужидкой массы-шлама подают во вращающуюся печь диаметром более 7 и длиной более 200м. Шлам ручьём течёт навстречу горящим газам, образующимся при сгорании топлива, высыхает, освобождается от углекислоты. Образовавшееся после высыхания серые ноздреватые шарикм-клинкер размалывают в шаровых мельницах в тонкий порошок, получая цемент.
При сухом способе, которому, по всей вероятности принадлежит будущее цементного производства, навстречу горящим газам подают не шлам, а размолотое в порошок сырьё: известняк, глину, шлаки. При этом экономится топливо, которое при мокром способе расходуется на испарение воды.
Бетон и железобетон
Бетон-это искусственный каменный материал. Его получают в результате затвердевания уплотнённой смеси вяжущего вещества (обычно с водой) и заполнителем. В качестве заполнителя вяжущего вещества можно использовать цемент, силикаты, гипс, асфальт, полимеры (синтетические смолы) и др. в качестве заполнителей, образующих жесткий скелет бетона, песок, гравий, щебень. Наиболее распространён цементный бетон.
Прочность цемента приготовленного, в частности, на основе цемента как вяжущего вещества, увеличивают с помощью стальной арматуры(стержней, спиралей) и в результате этой процедуры армирования получают железобетон. При этом бетон хорошо сопротивляется сжатию, а стальная арматура растягивающим нагрузкам, предохраняя бетон от появления трещин. Железобетон - основной современный строительный материал.
В процессе изготовления железобетона для придания большей прочности бетонной смеси, перед тем как она затвердеет , производят её уплотнение, используя вибрацию. На домостроительных комбинатах и на заводах железобетонных изделий имеются специальные виброплощадки - прочные плиты на пружинах. Под ними вращаются 2 эксцентрика неуравновешенные грузы. Грузы движутся вверх-вниз, плита подскакивает на пружинах, а железобетонная панель, находящаяся на плите, уплотняется.
3. Область применения. Виды цемента.
Цемент применяют для кладки кирпича, фундамента и др. Его используют для получения бетона, а его в свою очередь для получения железобетона.
Железобетон используют в строительстве жилых домов и других сооружений. Его используют для строительства зданий, так как он обладает особой прочностью, и подтверждению этому служит “Останкинская телебашня”, которая в свою очередь сделана из железобетона.
Цемент М500 Д0
Цемент марки ПЦ 500-Д0 применяется при производстве ответственных бетонных и железобетонных конструкций в промышленном строительстве, где предъявляются высокие требования к водостойкости, морозостойкости, долговечности. Цемент этой марки эффективен при проведении аварийных ремонтных и восстановительных работ ввиду высокой начальной прочности бетона.
Цемент М500 Д20
Цемент марки ПЦ 500-Д20 применяется в промышленном, жилищном и сельскохозяйственном строительстве для производства сборного железобетона, фундаментов, балок, плит перекрытий и др., а так же успешно используется для изготовления бетонных и строительных растворов, штукатурных, кладочных и других ремонтно-строительных работ. Цемент этой марки обладает водостойкостью, морозостойкостью, пониженной сопротивляемостью коррозионным воздействиям по сравнению с обычным портландцементом.
Цемент М400 Д0
Цемент марки ПЦ 400-Д0 используется для производства сборных бетонных и железобетонных конструкций с применением термовлажностной обработки, а также для бетонных, железобетонных подземных, надземных и подводных сооружений, подвергающихся действию пресных и минерализированных вод. Цемент этой марки успешно зарекомендовал себя для изготовления бетонных и строительных растворов.
Цемент М400 Д20 Цемент марки ПЦ 400-Д20 применяется в промышленном, жилищном и сельскохозяйственном строительстве для производства сборного железобетона, фундаментов, балок, плит перекрытий, стеновых панелей и др. Цемент этой марки обладает хорошей водостойкостью и морозостойкостью.
Быстротвердеющий цемент
Быстротвердеющий цемент - это цемент, характеризующийся интенсивным нарастанием прочности в начальный период твердения. Применяется в основном для изготовления сборных железобетонных конструкций и изделий. Повышенная механическая прочность быстротвердеющего цемента в раннем возрасте твердения обусловливается соответственным минералогическим составом и микроструктурой клинкера, дозировкой добавок и тонкостью помола цемента.
Сульфатостойкий цемент
Сульфатостойкий цемент, сульфатостойкий портландцемент, разновидность портландцемента. По сравнению с обычным портландцементом сульфатостойкий цемент обладает повышенной стойкостью к действию минерализованных вод, содержащих сульфаты, меньшим тепловыделением, замедленной интенсивностью твердения и высокой морозостойкостью. Сульфатостойкий цемент получают тонким измельчением клинкера нормированного минералогического состава. Предназначается для изготовления бетонных и железобетонных конструкций гидротехнических и др. сооружений, испытывающих воздействие агрессивной сульфатной среды (например, морской воды), особенно в условиях переменного увлажнения, чередующихся замерзания и оттаивания.
Цемент, полученный на основе клинкера нормированного состава
Для бетона дорожных и аэродромных покрытий, железобетонных напорных и безнапорных труб, железобетонных шпал, мостовых конструкций, стоек опор высоковольтных линий электропередач, контактной сети железнодорожного транспорта и освещения следует поставлять цемент, изготовляемый на основе клинкера нормированного состава с содержанием трехкальциевого алюмината (С3А) в количестве не более 8% по массе.
4. Анализ конкурентов, сравнительная характеристика свойств.
Существует целый ряд альтернатив цементу, которые могут похвастаться лучшими экологическими параметрами, включая и цемент на основе извести, Aircrete, Ceramicrete, EcoCement, C-Fix, и даже цемент, не наносящий ущерба окружающей среде, в котором используются отходы как материал заполнителя.
Цемент на основе извести, вероятно, самый широко известный и самый давно известный заменитель портлендского цемента. В число экологических преимуществ здесь входят: износостойкость, способность пропускать воздух и относительно не интенсивная технология производства.
Эркрит (Aircrete) производится из целого ряда материалов, включая песок, порошкообразный цемент из золы-уноса, известь, порошкообразный алюминий и воду. Он представляет собой сверхлегкую альтернативу. Материалы смешиваются все вместе, и образующаяся смесь вспенивается для создания исключительно прочного и легкого бетона с высокими термоизолирующими свойствами.
Этот материал обычно используется для производства блоков, которые можно применять для возведения стен или же в качестве компонентов балочных перекрытий. В число прочих добавок для цемента входят, кремнистый песок, зола-уноса, оксиды железа и боксит.
Керамикрит (Ceramicrete) это фосфатный керамический материал со многими различными применениями, от обработки вредных отходов до создания строительных материалов, включая кирпичи, блоки и плитки для кровельных покрытий.
Созданный в Аргоннской национальной лаборатории в США этот материал образуется за счет смешивания порошкообразного оксида магния и растворимого фосфатного порошка с водой. Эта технология очень похожа на процесс замешивания бетона с использованием имеющегося на рынке оборудования, которое смешивает порошковые компоненты для создания вяжущего вещества.
Мокрую смесь можно затем подавать через насос или пушку, а также распылять; образующийся материал пористый с прочностью при сжатии выше, чем у бетона.
Австралийская компания, занимающаяся возобновляемыми технологиями, TecEco создала экоцемент (EcoCement). Образующийся за счет смешивания оксида магния и традиционных цементов материал позволяет уменьшить потребность в сжигании ископаемого топлива, и образует чистые и придающие прочность неорганические вещества, которые можно смешивать со многими различными заполнителями и добавками.
Находясь в виде пористого цемента, он нуждается в углекислом газе для твердения и схватывания. Поэтому, как указывают его создатели, он поглощает большие количества газов, создающих парниковый эффект, ответственность за образование которых несет, в определенной степени, и сам бетон.
C-Fix или углеродный цемент, представляет собой термопластическое сверхпрочное вяжуще вещество, которое было разработано компанией Shell в сотрудничестве с Дельфтским университетом для использования отходов, которые остались от производства топлива. Этот материал уже используется в качестве заменителя щебеночно-гудронного покрытия на дорогах Нидерландов. В компании Shell считает, что он способен заменить 90% применений бетона и асфальта.
Поскольку добыча нефти не является самым безвредным для окружающей среды процессом в мире, использование таких отходов максимально увеличивает производственный потенциал и позволяет отказаться от технологий обработки в печи с их высокими затратами энергии, которые свойственным традиционному производству цемента.
Австралийская Научная и промышленная исследовательская организация Содружества создала Hyssil, высокопрочный бетон, который обладает свойствами бетона, но позволяет в два раза уменьшить массу. У него также в пять раз выше теплостойкость по сравнению с традиционным бетоном, и его можно использовать для производства испытывающих большие нагрузки или же не нагруженных предварительно созданных строительных компонентов.
К бетонам можно также добавлять синтетические, стальные волокна или их смеси, такие как производимые Propex Concrete Systems, для существенного повышения прочности и устойчивости к растрескиванию. Хотя это не уменьшает количества используемого в смеси цемента, их введение приводит к уменьшению количества бетона (и, следовательно, цемента), который требуется для реализации строительных проектов.
Еще одной альтернативой является использование отходов как материалов-заполнителей. Такая технология не приводит к замене портлендцемента, но она позволяет создавать бетон, который наносит меньший ущерб окружающей среде. Кроме того, это может сократить объемы захоронения и уменьшить объемы добычи песка и гравия.
5. Анализ рынка цемента в России.
Из всех отраслей промышленности стройматериалов цементная промышленность является самым энергоемким производством, требующим большого опыта и немалых знаний. По-сути, каждый цементный завод – это уникальный проект. Строительство хорошего цементного завода, как правило, исчисляется не месяцами, а годами и требует значительных финансовых вложений.
Как правило, объемы производства цемента отражают общую экономическую ситуацию в стране. В условиях кризиса значительно снизились темпы строительства, подавляющее большинство региональных девелоперов вынуждены замораживать свои проекты либо переносить их реализацию на более поздний срок. И далее, по закономерной цепочке, происходит снижение производства объемов цемента либо полная остановка цементных заводов и ЗЖБИ, замораживаются проекты по введению в строй новых мощностей, строительства новых заводов и комбинатов.
К числу крупнейших производителей и поставщиков цемента можно отнести компанию «Евромецент Груп», владеющей 13 заводами на Территории РФ и 3 заводами в СНГ, «Сибирский цемент» (4 завода), «Новоросцемент» (3 завода), крупнейшего производителя цемента в Поволжье компанию «Мордовцеемнт». Заводами в Саратовской и Ленинградской областях владеет компания «Heidelbergcement» (80 млн тонн), компания «Holcim» владеет двумя заводами («Альфа-цемент»), объем производства которых составляет 140 млн тонн, компания «Воскресенскцемент», принадлежащая компании «Lafarg» выпускает 132 млн тонн цемента.
По итогам 2008 года производство цемента в России упало на 10% по отношению к уровню 2007 года. Одним из факторов падения показателей послужило сезонное снижение строительства к концу года. Другим важным моментом явился тот факт, что в 2008 году по инициативе правительства на импорт цемента была отменена пошлина. Таким образом, произошло существенное замещение части отечественного цемента менее дорогим импортным товаром и, как следствие, резкое понижение стоимости отечественного цемента. По данным компании «Евромецент Груп» в период январь-август 2008 годы доля импортного цемента на российском рынке увеличилась на 14%, что составило 6,2 млн тонн. В то же время производство и поставки отечественного цемента сократилось более чем на 1 млн тонн.
Несомненно, кризис отбросил развитие цементной промышленности на несколько лет назад. Недозагруженность мощностей цементных предприятий приведет к тяжелым последствиям. Тем не менее, основой успешного преодоления кризиса и его последствий послужат практически неограниченные ресурсы страны и при помощи господдержки поэтапное выполнение намеченных планов развития цементной промышленности. Об этом говорилось на состоявшейся в апреле 2009 года XVII Международной Конференции-Выставке BusinessCem Moscow 2009. Главной темой мероприятия было обсуждение особенностей развития цементного рынка России, совершенствование отрасли в период мирового финансового кризиса. Много внимания было уделено вопросам инвестирования, добыче, транспортировке продукции, энергосбережению и вопросам импортирования цемента.
Российский рынок цемента зависит напрямую от состояния строительства в стране. Мировой финансовый кризис крайне негативно отразился на рынке строительства, а следовательно и на цементной отрасли. За период с 2008 по 2010 гг продажи цемента в России снизились на 14,5% по отношению к показателю 2007 г, упав в 2010 г до 48,9 млн т.
Сейчас в стране наблюдается оздоровление цементного рынка. По оценкам BusinesStat, продажи цемента к концу 2011 г вырастут до 51,8 млн т. В перспективе продажи цемента продолжат расти, чему будет способствовать реализация программ, которые требуют большого количества цемента: жилищное и инфраструктурное строительство, подготовка к АТЭС-2012, Олимпиада в Сочи, развитие электроэнергетики.
Отечественные производители в 2010 г стали наращивать объемы производства цемента после кризисных лет. Росту производства в ближайшие годы будет способствовать модернизация заводов и разработка новых месторождений цементного сырья. По нашим оценкам, производство цемента в России достигнет к 2015 г 64,3 млн т.
6. Вывод
Цемент - это важнейший строительный материал. В строительной практике он применяется уже около 160 лет. Крупные научные открытия, послужившие основой создания новых видов цемента и улучшения качества существующих, относятся к последним четырем десятилетиям, причем большинство из них принадлежит советским ученым.
В России цемент начали производить в прошлом столетии. В начале 20 века, в России работало 60 цементных заводов общей производительностью около 1,6 млн. тонн цемента. Однако после Первой мировой войны большинство цементных заводов было разрушено. С приходом советской власти цементную промышленность России пришлось создавать практически с нуля.
Уже в 1962 году, СССР занял первое место в мире по выпуску цемента. В 1971 году выпуск цемента в стране превысил 100 млн. тонн. Цементная промышленность СССР отличалась высокой концентрацией производства. Средняя мощность цементного завода в СССР была почти в 2 раза выше, чем в США, и на 30% выше, чем в Японии.
Российская цементная промышленность находится в числе самых быстрорастущих мировых индустрий с темпами около 9%, при этом в ближайшие годы можно прогнозировать увеличение темпов роста.
Сегодня главным недостатком российских цементных заводов является то, что они используют мокрый способ производства цемента, который гораздо более энергоемкий, чем используемый в развитых странах мира сухой способ. Поэтому для компаний важно постепенно переходить на более прогрессивные энергосберегающие технологии.
СПИСОК ИСПОЛЬЗОВАННЫХ ИСТОЧНИКОВ И ЛИТЕРАТУРЫ
- http://businesstat.ru/russia/surveys/construction_renovation/mortar/cement
- http://www.kalitva.ru/123682-referat-cement-i-ego-produkty.html
- http://www.metaprom.ru/pub466.html
- http://www.newchemistry.ru/printletter.php?n_id=3098
material.osngrad.info