Утилизация обжиговой пыли для получения цемента (стр. 1 из 3). Утилизация цемента
Утилизация обжиговой пыли для получения цемента
Содержание
Введение
Глава 1. Характеристика цемента и технологический метод его производства
Глава 2. Сухой способ производства цемента
Глава 3. Получение цемента из обжиговой пыли
Цемент из остатков товарного бетона
Глава 4. Экологический мониторинг атмосферного воздуха в зонах загрязнения отходами цементного производства
Образование пыли является основной проблемой в производстве цемента, а регенерация пыли - экономически необходимой. Упомянутая книга может быть рекомендована читателю для детального знакомства с оборудованием для контроля загрязнения воздуха, применяемым в цементной промышленности.
Экономический эффект, получаемый при повторном использовании уловленной пыли, недостаточен, чтобы полностью покрыть стоимость пылеулавливающего оборудования. Однако удаление пыли необходимо для выполнения требований законодательства по охране окружающей среды и для предотвращения загрязнения близлежащей местности. Осуществление этого процесса является не простой проблемой.
Цемент не является природным материалом. Его изготовление - процесс дорогостоящий и энергоемкий, однако результат стоит того - на выходе получают один из самых популярных строительных материалов, который используется как самостоятельно, так и в качестве составляющего компонента других строительных материалов (например, бетона и железобетона). Цементные заводы, как правило, находятся сразу же на месте добычи сырьевых материалов для производства цемента.
Производство цемента включает две ступени: первая - получение клинкера, вторая - доведение клинкера до порошкообразного состояния с добавлением к нему гипса или других добавок. Первый этап самый дорогостоящий, именно на него приходится 70% себестоимости цемента. А происходит это следующим образом: первая стадия - это добыча сырьевых материалов. Разработка известняковых месторождений ведется обычно сносом, т.е. часть горы "сносят вниз", открывая тем самым слой желтовато-зеленого известняка, который используется для производства цемента. Этот слой находится, как правило, на глубине до 10 м (до этой глубины он встречается четыре раза), и по толщине достигает 0,7 м. Затем этот материал отправляется по транспортеру на измельчение до кусков равных 10 см в диаметре. После этого известняк подсушивается, и идет процесс помола и смешивания его с другими компонентами. Далее эта сырьевая смесь подвергается обжигу. Так получают клинкер. Вторая стадия тоже состоит из нескольких этапов. Это: дробление клинкера, сушка минеральных добавок, дробление гипсового камня, помол клинкера совместно с гипсом и активными минеральными добавками. Однако надо учитывать, что сырьевой материал не бывает всегда одинаковым, да и физико-технические характеристики (такие как прочность, влажность и т.д.) у сырья различные. Поэтому для каждого вида сырья был разработан свой способ производства. К тому же это помогает обеспечить хороший однородный помол и полное перемешивание компонентов. В цементной промышленности используют три способа производства, в основе которых лежат различные технологические приемы подготовки сырьевого материала: мокрый, сухой и комбинированный.
Мокрый способ производства используют при изготовлении цемента из мела (карбонатный компонент), глины (силикатный компонент) и железосодержащих добавок (конверторный шлам, железистый продукт, пиритные огарки). Влажность глины при этом не должна превышать 20%, а влажность мела - 29%. Мокрым этот способ назван потому, что измельчение сырьевой смеси производится в водной среде, на выходе получается шихта в виде водной суспензии - шлама влажностью 30 - 50%. Далее шлам поступает в печь для обжига, диаметр которой достигает 7 м, а длина - 200 м и более. При обжиге из сырья выделяются углекислоты. После этого шарики-клинкеры, которые образуются на выходе из печи, растирают в тонкий порошок, который и является цементом.
Цемент - один из важнейших строительных материалов, предназначенных для бетонов и строительных растворов, скрепление отдельных элементов (деталей) строительных конструкций, гидроизоляций и др. Цемент представляет собой гидравлический вяжущий материал, который после смешения с водой и предварительного затвердевания на воздухе продолжает сохранять и наращивать прочность в воде.
Производство цемента обусловлено необходимостью его производства для применения, главным образом, в строительстве. Строительство жилья на основе цемента позволяет получить объекты с низкой теплопроводностью и высокой морозостойкостью.
Технология цементного производства позволяет использовать в нём отходы добывающей, металлургической отраслей, а также побочные продукты этих производств. Некоторые отходы даже улучшают свойства цемента. Гибкая технология позволяет осуществлять комбинирование производства цемента с производством металлов, химических продуктов и энергии.
Существует много разновидностей цемента. Они отличаются друг от друга конечными свойствами, условиями производства и наличием в них различных видов добавок.
Портландцементом называется гидравлическое вяжущее вещество, твердеющее в воде и на воздухе, получаемое путём совместного размола портландцементного клинкера и гипса для регулирования сроков схватывания. Марку портландцемента определяют при испытании на сжатие стандартной цементной палочки размерами 4×4×16 мм.
Существуют следующие марки портландцемента, выпускаемые промышленностью строительных материалов:
ПЦ 400 ДО и ПЦ 400 Д20. Применяется для производства асбестоцементных изделий, строительства жилья, промышленных зданий и сооружений.
ПЦ 500 ДО. Применяется для строительства мостов, путепроводов, железобетонных труб, пролетных строений и блоков.
ПЦ 600 ДО. Применяется для строительства мостов, туннелей, высокопрочных сооружений на объектах Министерства Обороны.
Сырьем при производстве цемента по мокрому способу являются следующие компоненты: карбонатный компонент - мел, силикатный компонент - глина, железосодержащие добавки - пиритные огарки, конверторный шлам, железистый продукт.
Мел и глина добываются в карьерах экскаваторами. Влажность глины - до 20%, мела - до 29%.
Глина грузится в автосамосвалы и подается к глиноболтушкам, где производится приготовление глиняного шлама. Глиняный шлам из приемника перекачивается насосом в вертикальные бассейны.
Мел грузится экскаватором в думпкары. Думпкары имеют двусторонние толкатели для сталкивания мела в бункер. Из бункера мел с огарками по транспортеру поступает в мельницу самоизмельчения (гидрофол). Одновременно в гидрофол подаются глиняный шлам (насосом или самотеком из вертикальных бассейнов), а также вода и ЛСТ. Приготовленный шлам подается в вертикальный бассейн. Отсюда шлам подается в сырьевую мельницу, в которой и происходит его помол. Готовый шлам перекачивают в вертикальные шламобассейны, где происходит его корректировка. Откорректированная сырьевая смесь насосами перекачивается в горизонтальные бассейны, а оттуда - в следующие горизонтальные бассейны. Через шламовый питатель сырьевая смесь из бассейна подается в печи для обжига.
Количество подаваемого в печи сырья регулируется контрольным баком. Скорость наполнения зависит от числа оборотов печи и от текучести шлама. Контроль за качеством шлама ведет лаборатория. Обеспыливание отходящих газов обычно происходит с помощью электрофильтров, которые работают в режиме автоматического регулирования. Охлаждение клинкера из печей производится в колосниковых холодильниках или в рекуператорных.
Колосниковые холодильники имеют производительность около 70 т/ч. Температура клинкера на выходе из колосникового холодильника составляет не более 90 градусов. Клинкер из печей с температурой 1250 градусов поступает в шахту холодильника, где установлены неподвижные колосники и резко охлаждается воздухом, подаваемым вентилятором высокого давления. Далее клинкер поступает на решетку, которая состоит из подвижных и неподвижных колосников. Крутая передняя и пологая задняя полость колосников обеспечивают продвижение клинкера вперед и его интенсивное перемешивание. В разгрузочном конусе холодильника установлена встроенная дробилка для измельчения крупных кусков клинкера.
Рекуператорный холодильник имеет производительность 35 тонн в час. Температура клинкера на выходе - не более 400 градусов. В холодильнике имеется несколько барабанов, закрепленных по окружности корпуса, которые вращаются вместе с печью.
Со склада клинкер поступает с помощью мостового грейферного крана в бункера цементных мельниц. Туда же подается гипс, откуда вся эта басня дозируется в цементные мельницы. Для интенсификации процесса помола при производстве бездобавочных цементов на тарельчатый питатель подается лигносульфанат технический (ЛСТ) в количестве 0,01%.
Транспортировка готового цемента в цементные силоса производится пневмонасосами. Силос представляет собой железобетонную емкость диаметром около 10 м и высотой примерно 25-30 м. Силосный склад цемента насчитывает обычно более десятка силосов. Отгрузка цемента из цементных силосов производится в бункер для погрузки в автотранспорт или отгружается в железнодорожные вагоны. Упаковка цемента в бумажные мешки (50 кг) производится упаковочными машинами. Определение количества отгрузки цемента производится взвешиванием на железнодорожных весах. [4]
Типовая технологическая схема

При сухом способе производства цемента известняковое сырье дробят в две стадии - в щековой дробилке, потом в молотковой дробилке.
Глина, входящая в состав цементного сырья, измельчается в валковой дробилке и сушится в барабане. После этого помолотый известняк, глина и огарки совместно измельчаются в барабанной мельнице, после чего высушиваются с помощью дымовых газов, которые поступают из запечных теплообменников.
mirznanii.com
Утилизация обжиговой пыли для получения цемента
Измельченный высушенный материал разделяется на грубую и тонкую фракции в проходном сепараторе. Грубая фракция подвергается дополнительному измельчению, а тонкая фракция улавливается в циклонах и подвергается гомогенизации в смесительных силосах сырьевой муки.
Сырьевая мука последовательно проходит обработку на нескольких ступенях циклонных теплообменников, нагревается, частично декарбонизируется, после чего поступает во вращающуюся печь, где из сырьевой муки формируется цементный клинкер. Далее клинкер охлаждается в холодильнике и поступает в силосный склад клинкера.
С силосного склада цементный клинкер через ленточный конвейер поступает в барабанную мельницу для совместного помола с гипсом и минеральными добавками, которые одновременно поступают из бункеров.
Сжигание топлива, необходимое для производства цемента, обеспечивается подачей горячего воздуха от клинкерного холодильника. Дымовые газы, отходящие от циклонных теплообменников, увлажняются в башне, затем очищаются от пыли с помощью электрофильтров и с помощью дымососа через трубу выносится в атмосферу. Воздух, отходящий от цементных мельниц, очищается в аспирационной шахте, циклонах и рукавных фильтрах.
Измельченная смесь сепарируется - крупка поступает на дополнительное измельчение, а готовый цемент с помощью пневмокамерных насосов поступает в цементные силосы.
Из цементных силосов цемент тарируется в контейнеры “Big Ben" или в мешки, или отгружается в железнодорожные вагоны для транспортировки цемента (холеры) или автоцементовозы.
В нашей компании Вы можете купить качественный цемент разных марок оптом по заводской цене на самых выгодных для Вас условиях с доставкой. Мы осуществляем производство и продажу оптом портландцемента марки М400 и М500.
Мы производим поставки высококачественного цемента оптом навалом и в мешках с завода и со склада из Москвы машинами и вагонами - себряковцемент, мордовцемент, щуровский цемент, новоросцемент, сухие смеси универсальные. Вы можете купить у нас качественный цемент для строительства и ремонта, бетона и кладки, для фундаментов и растворов, строительства крупногабаритных железобетонных конструкций.
Сухой способ производства цемента
При сухом способе производства цемента известняковое сырье дробят в две стадии - в щековой дробилке, потом в молотковой дробилке.
Глина, входящая в состав цементного сырья, измельчается в валковой дробилке и сушится в барабане. После этого помолотый известняк, глина и огарки совместно измельчаются в барабанной мельнице, после чего высушиваются с помощью дымовых газов, которые поступают из запечных теплообменников.
Измельченный высушенный материал разделяется на грубую и тонкую фракции в проходном сепараторе. Грубая фракция подвергается дополнительному измельчению, а тонкая фракция улавливается в циклонах и подвергается гомогенизации в смесительных силосах сырьевой муки.
Сырьевая мука последовательно проходит обработку на нескольких ступенях циклонных теплообменников, нагревается, частично декарбонизируется, после чего поступает во вращающуюся печь, где из сырьевой муки формируется цементный клинкер. Далее клинкер охлаждается в холодильнике и поступает в силосный склад клинкера.
С силосного склада цементный клинкер через ленточный конвейер поступает в барабанную мельницу для совместного помола с гипсом и минеральными добавками, которые одновременно поступают из бункеров.
Сжигание топлива, необходимое для производства цемента, обеспечивается подачей горячего воздуха от клинкерного холодильника. Дымовые газы, отходящие от циклонных теплообменников, увлажняются в башне, затем очищаются от пыли с помощью электрофильтров и с помощью дымососа через трубу выносится в атмосферу. Воздух, отходящий от цементных мельниц, очищается в аспирационной шахте, циклонах и рукавных фильтрах.
Измельченная смесь сепарируется - крупка поступает на дополнительное измельчение, а готовый цемент с помощью пневмокамерных насосов поступает в цементные силосы.
Образование пыли является основной проблемой в производстве цемента, а регенерация пыли - экономически необходимой. Упомянутая книга может быть рекомендована читателю для детального знакомства с оборудованием для контроля загрязнения воздуха, применяемым в цементной промышленности.
Экономический эффект, получаемый при повторном использовании уловленной пыли, недостаточен, чтобы полностью покрыть стоимость пылеулавливающего оборудования. Однако удаление пыли необходимо для выполнения требований законодательства по охране окружающей среды и для предотвращения загрязнения близлежащей местности. Осуществление этого процесса является не простой проблемой.
Попытки использования цементной пыли путем ее возвращения на стадию обжига в том виде, в каком она была уловлена, нельзя признать успешными по двум основным причинам.
Эта пыль настолько мелкая, что значительная часть ее снова выносится отходящими газами еще до поступления на стадию цементообразоваиия. Помимо больших потерь это приводит также к большому увеличению нагрузки на трубчатую пылеулавливающую систему.
Еще более существенной причиной является присутствие в пыли значительных количеств сульфатов и хлоридов щелочных металлов, которые не позволяют получать цемент достаточно хорошего качества. Поскольку требования охраны окружающей среды становятся все более жесткими, а пылеулавливающее оборудование все более совершенным, то происходит улавливание все более мелких частиц пыли. Чем меньше размеры частиц, тем, как правило, выше содержание щелочных элементов в пыли. Таким образом, упомянутая проблема качества становится все более серьезной.
Известные способы, предназначенные для изменения физического состояния и (или) уменьшения содержания щелочных элементов в цементной пыли, не находят практического применения по экономическим или другим причинам.
Усовершенствованный метод, относящийся к экономичному способу переработки цементной обжиговой пыли с любым размером частиц и содержанием щелочных металлов был предложен А.Т. Мак-Кордом Пыли придается такое физическое состояние и химический состав, который позволяет повторно использовать ее для изготовления цемента. При этом хлорид калия может быть достаточно легко выделен в кристаллическом виде с хорошей степенью чистоты.
Усовершенствованный процесс включает:
1) обработку цементной обжиговой пыли водным раствором хлорида калия при повышенной температуре;
2) добавление к полученной взвеси цементной пыли небольших количеств масла и жирных кислот, хлопьеобразование и комкование твердой фазы;
3) удаление хлопьев и комков твердого вещества из жидкой фазы;
4) легкую промывку твердого материала для дальнейшего снижения содержания щелочных металлов;
5) охлаждение раствора для кристаллизации хлорида калия и 6) отделение полученного кристаллического вещества. Остаточный раствор после удаления основного количества кристаллического Хлорида калия все еще насыщен солью и после нагревания может быть направлен на стадии обработки новых порций цементной пыли.
Некоторое время назад бетонные конструкции изготовляли путем смешивания индивидуальных компонентов - наполнителя, песка, цемента и воды - на месте, в стационарном смесителе. Затем бетон наливали в контейнер, а оттуда переносили в соответствующие формы. В конце каждого рабочего дня или периодически в течение дня смеситель и контейнеры промывали водой, чтобы предотвратить засыхание находящихся в них остатков бетона. Промывная вода с содержащимися в ней твердыми частицами направлялась в сток.
Затем стационарные смесители были заменены так называемыми транзитными миксерами на грузовиках, которые на центральном предприятии загружались сырьем, которое перемешивалось за время перевозки и по прибытии на место выгружался готовый бетон. По возвращении из каждой поездки грузовик промывался водой с той же целью, что и в предыдущем случае.
Еще более недавно были построены очень крупные промышленные предприятия, единственной продукцией которых являются сборные бетонные конструкции, начиная от небольших бетонных блоков для индивидуальных застройщиков и кончая конструкционными элементами и облицовочными панелями для больших зданий. И в этом случае все устройства, контактирующие с сырым бетоном, необходимо регулярно промывать водой, чтобы предотвратить затвердевание бетона и поломку Оборудования.
Возвращаясь к вопросу о транзитных миксерах, рассмотрим работу завода среднего размера, использующего около 150 грузовиков. Предположим, что каждый грузовик в конце рабочего дня покрыт отложениями толщиной от 0,5 до 1-1,5 м. Этот слой должен быть сброшен с грузовика и удален, а грузовик вымыт к следующему рабочему дню.
Если 75 грузовиков имеют отложения в среднем толщиной 1 м, то это означает, что необходимо удалить 75 м бетона и вымыть 150 грузовиков.
Раньше на многих заводах грузовики просто промывали большим количеством воды, сбрасывая сточные воды в канализацию. Местные власти выступали против такой практики и сейчас во многих районах это запрещено законом.
В некоторых местностях, где это позволяют условия рельефа, грузовики с цементом в конце дня направляются к ближайшему карьеру или другому подходящему месту, где можно сбросить бетон, а затем возвращаются в гараж, где их моют так, как описано выше. Однако такая процедура является дорогостоящей, поскольку приходится платить за холостой пробег грузовика к месту сброса и обратно, а также дополнительно оплачивать время и работу водителя. Совершенно очевидно, что такой метод очистки является убыточным для предприятия, производящего бетон. К тому же, хотя этот метод и кажется очень простым, большинству производителей становится все труднее найти подходящие места для сброса бетона.
mirznanii.com
УТИЛИЗАЦИЯ ПРОМЫШЛЕННЫХ ОТХОДОВ НА ЦЕМЕНТНЫХ ЗАВОДАХ
Транскрипт
1 УТИЛИЗАЦИЯ ПРОМЫШЛЕННЫХ ОТХОДОВ НА ЦЕМЕНТНЫХ ЗАВОДАХ Обжиговая цементная печь - отличное средство утилизации промышленных отходов. Суждение верно Обжиговая цементная печь обеспечивает: постоянный безопасный производственный процесс благодаря ее тепловой стабильности, что требует непосредственно производственный процесс; полное разрушение органических молекул, даже наиболее устойчивых; полную нейтрализацию некоторых токсичных компонентов образующихся в ходе горения; связует металлические включения с составляющими цемента благодаря устойчивым химическим соединениям. Эта технология предоставляет большую экологическую выгоду. Суждение верно Производство цемента не приводит к образованию жидких или твердых промышленных отходов. Это возможно при оптимальном использовании энергии отходов и приводит к значительному снижению использования твердого топлива.* Если сравнить цементный завод, сжигающий промышленные отходы и цементный завод, использующий исключительно мазут в обжиговых печах, в одинаковых объемах, то в первом случае имеет место, безусловно, лучший экологический эффект. С промышленными отходами в цементном производстве обращаются с особой осторожностью Суждение верно Соответствие общепринятым требованиям - один из высших приоритетов, наряду с безопасностью. Все цементные заводы классифицируются как установки по переработке отходов Общественные слушания и специальные префектурные решения устанавливают пределы для использования промышленных отходов. Строгая и тщательная процедура проверки определяет, какие промышленные отходы возможно использовать в производстве цемента. Все отходы проходят две стадии анализа: - первая проверка определяет, технически совместимы ли отходы с оборудованием завода; - вторая проверка определяет влияние отхода на качество цемента. * В 1993, использование промышленных отходов позволило сэкономить более 300,000 pet (нефтяные эквивалентные метрические тонны), что составляет 15% годового потребления энергии для Французского производства цемента.
2 Каждое соотношение продукт/отход проходит предварительные анализы и проверку на возможность использования их в настоящих условиях цементного производства, согласно с префектурным решением. Эта процедура, утверждена DRIRE (Французский Региональный Директорат Промышленности, Исследования Окружающей среды, который проводит постоянную проверку природы происхождения и места применения используемых материалов, т.е. не влияют ли отходы на качество цемента). Таким образом, промышленные отходы находятся под строгим контролем, как с технической, так и с юридической точки зрения. Наибольшая часть промышленных отходов может сжигаться в процессе производства цемента. Частично верное суждение Обжиговая цементная печь может сжигать широкий спектр отходов, но она также имеет более строгие требования, чем другие печи. Топливо должно иметь максимально стабильные характеристики (калорийность, процент содержания воды, хлора, и т.п.) Отход не может применяться пока не прошел специальный процесс обработки. Существуют различные составляющие промышленных отходов, которые могут утилизироваться в процессе производства цемента: твердые и пастообразные отходы, такие как угольные и нефтяные шламы; жидкие отходы, такие как растворители, минеральные масла (например, отработанное моторное масло), клеи, лаки, браки краски; твердые бытовые отходы, такие как картон, древесина, пластмассы, пена полистирола, ткани, шины. Запрещается использование в процессе производства цемента следующих отходов: взрывчатые вещества; газы, в том числе сжиженные; радиоактивные материалы; медицинские отходы; отходы с высоким содержанием хлора. Качество цемента зависит от видов топлив используемых в ходе производственного процесса. Суждение не верно Задачей любого цементного завода является, производство качественного цемента, независимо от природы происхождения сырья, используемого на заводе и независимо от горючего, сожженного в печи. Опыты показали, что цемент стандартного качества может производиться, при использовании промышленных отходов, полностью, или частично заменивших в процессе производства применяемое топливо (например, мазут или уголь). Цементные заводы оборудованы установками, способными сжигать различные виды топлива, управляемыми автоматизированной системой, которая позволяет персоналу быстро и безопасно изменять вид топлива или смешивать различные их виды таким образом, что достигается оптимальная теплота их горения. Нужно отметить, что во Франции, цемент - высококачественный, стандартизированный продукт, как засвидетельствовано французской маркой качества NF. Качество подвергается контролю Лабораторией Тестирования Материалов в Париже, под зорким взглядом Комитета по качеству «NF», который составлен из властей, изготовителей, конечных пользователей, представителей малого бизнеса, и консалтинговых фирм.
3 Металлические элементы, содержащиеся в отходах, могут оказаться в цементе и, возможно, имеют негативное воздействие на пользователей. Суждение не верно Присутствие металлических элементов в цементе, безопасно и ни в коем случае не изменяет качество строительных продуктов, и не оказывает специфического влияния на окружающую среду или на здоровье. Нужно отметить, что эти металлические элементы присутствуют практически везде в природе в мелких количествах и что множество каждодневных продуктов содержит их. Некоторые даже присутствуют в лекарствах, применяемых для лечения серьезных болезней. Таким образом, совершенно естественно присутствие небольшого количества металлических включений в добываемом сырье, по простой причине, что они - часть нашей геологической и географической окружающей среды. Частицы металлических элементов всегда присутствовали в сырье и ископаемом топливе, используемом в производстве цемента. Используются или нет промышленные отходы в процессе производства - основной химический состав цемента остается тем же самым как тем из основных компонентов: известняк и глина. Независимо от использования альтернативного топлива, нет никакого изменения в качестве конечного продукта. Различные физико-химические тесты показывают, что поведение цемента на открытом воздухе всегда отвечает требованиям его стандартизации. Низкая активность химических соединений металлических элементов в клинкере, в конечном счете, переходит в нерастворимый продукт. Испытания во Франции проводили, чтобы изучить поведение цемента на открытом воздухе, по готовым изделиям было видно, что нет никакого риска воздействия на окружающую среду вообще. Исследования показали, что цементные продукты в сравнении с природными материалами либо идентичны, либо практически совпадают по параметрам. Кроме того, нет диффузии металлических элементов через структуру бетона. Есть две простых причины для этого: во-первых, они химически связаны и таким образом «пойманы в ловушку» в цементном растворе; во-вторых, плотность бетона (твердость материала) значительно ограничивает внутреннюю циркуляцию воды. Именно поэтому цемент и связанные продукты могут использоваться в контакте с питьевой водой без риска для здоровья. Горение промышленных отходов на цементных заводах выпускает ядовитые газы в атмосферу. Суждение не верно В последние годы цементная промышленность вложила и продолжает вкладывать значительные финансовые инвестиции, в совершенствование систем газоочистки. Сегодня, выбросы газов незначительны. Использование промышленных отходов в качестве топлива на цементных заводах не изменяет воздействие цементной промышленности на окружающую среду. Исследования ADEME (Французское Агентство по Управлению Окружающей средой и Энергетическими ресурсами) показали, что цементные заводы имеют чрезвычайно эффективные системы борьбы с загрязнением, тем самым не оказывают негативное воздействие на население. Чтобы сохранить окружающую среду, все установки, которые сжигают отходы, обязаны соблюдать одинаковые стандарты выпуска. Суждение не верно Каждому типу промышленной установки ввели определенные ограничения в соответствии с используемым сырьем и произведенным продуктом. Эти ограничения
4 налагают на изготовителя определенные правила о том, как лучше всего управлять качеством его производства и окружающей среды. Именно поэтому цементные заводы и традиционные установки для сжигания отходов, чьи основные методы работы и эксплуатационные требования различны, имеют разные требования к стандартам выбросов. Сжигание промышленных отходов цементными заводами составляет нечестную конкуренцию традиционным мусоросжигательным заводам. Суждение не верно. Цементные изготовители находятся в сфере создания качественного цемента; фирмы, сжигающие отходы находятся в сфере утилизации. В Европе имеет место высокий уровень требований к сжиганию отходов, развитие обоих отраслей промышленности жизненно важно для нахождения решений в плане утилизации отходов. Цементное производство и фактическое сжигание взаимодополняют друг друга с точки зрения: 1) их географического положения 2) технических процессов, согласно происхождению промышленных отходов. Эти отрасли промышленности могут сосуществовать рядом. Эта взаимозависимость позволяет производственникам, таким как цементные заводы уже оборудованными очень эффективными печами, выполнять свою основную задачу (производить качественный цемент) и в то же время оказывать помощь в утилизации промышленных отходов, не увеличивая загрязнения окружающей среды. Это решение должно быть поддержано, поскольку оно целесообразно по двум причинам: возможность получения энергии из отходов; увеличение дохода от промышленной установки, путем добавления дополнительной функции: утилизация отходов. Выбор цементного завода как места работы - хорошее решение для населения. Суждение верно Цементные заводы, способствуют увеличению материального благосостояния общества, рабочую занятость, предлагают дополнительное обслуживание, обучение. Утилизация отходов с низкой энергетической ценностью может также быть выполнена в цементных печах. Это может быть полезным для общества, поскольку построение новых, специализированных установок для сжигания отходов может вызвать негативную реакцию общества.
5 ВОПРОСЫ И ОТВЕТЫ 1.Почему сжигают отходы производства? Сжигание - хороший путь утилизировать некоторые промышленные отходы, как например опасные органические отходы. Разрушение органических молекул происходит через окисление в течение сгорания при очень высоких температурах. Сгорание должно произойти для того, чтобы целиком уничтожить молекулы загрязняющего агента и избежать ядовитых эмиссий. 2.Что такое - co-incineration? Co-incineration (совместное использование) подразумевает сжигание промышленных отходов в установке, которая не является традиционной печью для сжигания, но чьи технические характеристики дают возможность утилизации отходов. Это как раз цементные печи, которые предоставляют очень благоприятные условия (температура, время нахождения в щелочной среде, концентрация кислорода, отсутствие отходов). 3. не оказывает ли этот метод большего негативного воздействия на окружающую среду? Нет. Имеет место сокращение негативного воздействия на окружающую среду: Цементный процесс не производит ни водных сбросов, ни твердых отходов; Экономия энергии; Сжигание отходов позволяет цементным заводам уменьшать использование ископаемого топлива; ADEME (Французское Агентство по Управлению Окружающей средой и Энергетическими ресурсами) показал, что разрушение органических молекул и накопление (путем фильтрации) загрязнителей на цементных заводах превосходны и оптимально уменьшают выбросы в атмосферу; Использование промышленных отходов в качестве топлива ни в коем случае не нарушает экологию, в частности не увеличивает количество пыли, образованной в ходе производства цемента. Нужно указать, что в последние годы цементная промышленность сделала значительные финансовые инвестиции, чтобы уменьшить выбросы пыли. Сегодня, выбросы пыли являются незначащими по сравнению с полным уровнем цементного производства. Если мы сравниваем ситуацию цементного завода, сжигающего промышленные отходы и завода использующего стандартное топливо, то безусловно лучший экологический эффект будет на первом заводе. (Определенно, горение в цементной печи не производит отходов, нуждающихся в обработке или хранении, и нет никаких водных сбросов). 4. Мы часто слышим термин высокотемпературный, но это не всегда соотносится с хорошим сгоранием. Высокая температура - один из существенных факторов, но не единственный. Кислородное содержание и время нахождения в печи также являются важными аспектами для рассмотрения. Вместе, эти три фактора гарантируют хорошее сгорание и полное разрушение отходов в обжиговой цементной печи. 5. Определенные отходы могут выделять угарный газ и канцерогенные неустойчивые органические соединения, проходя предварительный подогрев при входе в печь. Упоминаемые продукты - угарный газ и неустойчивые органический соединения образуются при любом сгорании, включая, например, автомобильный выхлоп. Это явление не является основным для цементной печи. Кроме того, уровни выбросов на
6 цементных заводах, как показывает практика, были намного ниже, чем большинство других источников загрязнения (обсуждается также устойчивое сокращение выбросов CO 2 ) 6. Высокие температуры производят существенное количество закиси азота (кислотные дожди). Правда, однако, эти высокие температуры являются характерными для производства клинкера и также гарантируют полное разрушение промышленных отходов. Кроме того, европейская Директива косвенно признает этот факт. Однако, цементная промышленность развила технологии уменьшения данных выбросов, не ставя под угрозу качество цемента. 7. Должны ли устанавливаться лимиты на использование промышленных отходов? Теоретически нет никаких причин налагать лимиты на количество используемых промышленных отходов. Некоторые американские цементные заводы используют отходы в качестве основного топлива. Все равно, есть некоторые технические пределы, связанные с особенностями веществ и с требованиями главной деятельности установки. Хлор, например, является одним из веществ, которое проблематично для цементных печей; таким образом, сжигание хлорсодержащих веществ должно быть ограничено. 8. Разве не должен быть составлен конкретный список отходов, у которых существует возможность применения в установках, согласно точным физикохимическим свойствам каждого рассматриваемого типа? На цементном заводе уровень нейтрализации отходов - превосходен. Некоторые отходы не разрешены к применению, или из-за их природы или из-за наложенных ограничений. Критерии приемлемости гарантируют совместимость использования определенных отходов с качественным цементным производством. 9. Разве содержание хлора в отходе не является вредным для цемента? Содержание хлора ограничено европейскими инструкциями, гарантирующими качество цемента. Содержание хлора проверено в каждом шаге в процессе, от выбора сырья к горючему, включая промышленные отходы. 10. Разве не имеет место выбросы диоксинов при горении некоторых промышленных отходов в цементном производстве. Тесты, проводимые во Франции и Германии, показали, что процесс горения на цементном заводе не производит ни диоксинов, ни фуранов. Причиной тому служат высокие температуры в печи, а так же присутствии извести, известного ингибитора формирования диоксина. 11. Индустриальные сточные воды не являются горючим. Почему тогда они сжигаются на цементных заводах? Сжигание сточных вод не является прибыльной деятельностью цементных заводов. Цементная промышленность сжигает эти стоки в качестве помощи населению. Эта практика помогает уменьшить выбросы закиси азота благодаря улучшенному контролю над температурой пламени. 12. Нефтеотходы часто ядовиты, и растворители нуждаются в соответствующей обработке также, как и шлам чистки резервуаров и трубопроводов, которые концентрируют металлические и минеральные загрязнители. Не должны ли эти
7 типы промышленных отходов быть запрещенными для использования в процессе цементного производства из соображений безопасности? ADEME провел тесты, чтобы оценить использование таких отходов в цементных заводах, которые показали, что использование их безопасно, и тесты подтвердили полное уничтожение отходов благодаря полному соединению металлических элементов в клинкере. 13. Какие еще воздействия на окружающую среду могут иметь место в результате производства цементного завода использующего альтернативное топливо? Вышеупомянутые тесты, проведенные ADME также доказали, что эмиссии завода использующего альтернативное топливо сопоставимы с выбросами завода использующего стандартное топливо. Таким образом, использование альтернативного топлива в цементной печи не оказывает дополнительного влияния на окружающую среду; фактически, отсутствуют жидкие и твердые отходы, которые были бы образованы в результате утилизации рассматриваемых видов отходов иным образом. 14. Почему не существует экологических процедур для цементных заводов, утилизирующих отходы? Фактически, есть экологические процедуры. В частности это описано и имело хорошую практику использования в цементном производстве. 15. Почему цементные производители, не устанавливают такие же стандарты для выбросов как установки для сжигания отходов? В цементной промышленности (наряду с другими отраслями промышленности, такой как стекольная) технические особенности печи непосредственно связаны с процессом производства. Для каждой промышленности стандарты для выбросов определены специально установленными нормами, которые принимают во внимание особенности производства. 16. Обсуждалось, что производители цемента не должны устанавливать те же самые нормы выбросов, как и традиционные мусоросжигательные заводы, разве это не нечестная конкуренция? Нет. У каждой установки есть свои собственные особенности. Невозможно сравнить цементные заводы и традиционные установки для сжигания отходов. 17. Было сказано, что промышленные отходы производят более щелочной клинкер и, следовательно, конечный продукт - цемент, низшего качества. Верно ли это мнение? Нет. Промышленные отходы не вводят значительно большего количества щелочей в процесс цементного производства, и произведенный клинкер не является более щелочным. Присутствие щелочей становится актуальным только лишь в случае использования с добавками, содержащими определенные формы кварца. Они могут привести к краткосрочному температурному резонансу, который может фактически быть выгодным в строительных целях. 18. Нет ли риска, что цемент, произведенный с применением промышленных отходов, может быть более низкого качества, чем нормальный цемент? Цемент производился более 10 лет с применением промышленных отходов без любого намека на дефекты. Весь цемент, произведенный во Франции, отвечает стандартам и тестируется в лаборатории в Париже. Ежегодно испытывается около 2500 образцов. В ходе тестов не обнаружено различий в качестве цемента из-за типов горючего, используемого при его производстве.
8 19. Вы проверяли физические свойства своих строительных материалов, а какую информацию Вы имеете о долговременных физико-химических реакциях тяжелых металлов с клинкером? Использование промышленных отходов не увеличивает количество металлических элементов, находящихся в соединении с продуктом. Нужно отметить, что такие металлические элементы существуют только в малых количествах и, как показали исследования, требовалось бы в раз больше этих элементов для того, чтобы произошли какие- либо существенные физико-химических реакции 20. Кто был бы ответственен в случае несчастного случая, произошедшего вследствие нарушения качества цемента, произведенного с применением ТБО: предприятия, которые производят отход или цементные производители, которые утилизируют его (отход)? Цемент - стандартизированный продукт независимо от того, какое топливо используется при его изготовлении. Нет никаких причин ожидать любые несчастные случаи, французские цементные производители гарантируют качество своего продукта. 21. Обязано ли предприятие маркировать тару с цементом, произведенным с применением промышленных отходов, чтобы отличить его от обычного цемента? Цемент - стандартизированный продукт независимо от горючего, используемого, для его производства. Нет никакой потребности делать акцент на различиях в используемом топливе. 22. Граниты, найденные в некоторых областях Франции, содержат высокие уровни естественной радиоактивности. Может ли цемент иногда быть радиоактивным? Цемент сделан из известняка, который низок в естественной радиоактивности. Радиоактивность, как было проверено, остается значительно ниже экологических нормативов. 23. Во время производства цемент поглощает остатки сгорания, содержащие почти все тяжелые металлы, найденные в опасных промышленных отходах. Верно ли суждение? Все металлические включения соединены в готовом изделии, что не позволяет им воздействовать с окружающей средой. Это доказательство тому, что металлы не выделятся в окружающую среду. Нужно отметить, что основной источник металлических элементов - природный ресурс, а не применяемый промышленный отход 24. Что случается с тяжелыми металлами, не соединившимися с клинкером? Они остаются и накапливаются в цементной печи? Металлические элементы (большинство которых происходит из природного сырья) соединены и таким образом полностью инертны в клинкере. Те, которые могут быть найдены в кирпичах цементной печи, повторно возвращаются в процесс и абсорбируются клинкером. 25. Хронические болезни развиваются за длительные периоды времени без ярко выраженных признаков, таким образом, очень сложно поставить диагноз (например, общее отравление, вызванное интоксикацией свинецсодержащей краски или асбеста). Есть мнение, что цемент, произведенный с промышленными отходами, содержит больше тяжелых металлов, чем произведенный с другим горючим, может ли он вызвать подобные типы пагубных болезней?
9 Промышленные отходы не изменяют ни содержания, ни природы металлических элементов, содержащихся в цементе. Они связаны в продукте и не могут реагировать с внешней средой. Содержание металлов в цементе не представляет опасности для окружающей среды. 26. Питьевая вода иногда поставляется через бетонные водные трубопроводы. Нет ли риска в том, что тяжелые металлы (ртуть, хром, мышьяк, и т.д.) содержавший в цементе могут оказаться растворенным в воде и таким образом постоянно потребляться населением? Специализированные лаборатории, контролирующие качество питьевой воды, провели испытательное сравнение клинкера произведенного с использованием стандартного топлива с клинкером, произведенным с применением альтернативного топлива. Поскольку никаких различий в результатах тестов не было обнаружено, нет никакого особого риска относительно здравоохранения. 27. Объем утилизации в цементных печах, вероятно, увеличится. Так как бетон содержит тяжелые металлы, сжигание отходов приведет, по прошествии долгого времени к накоплению опасных элементов. Бывшие в употреблении строительные материалы - изделия, они не используются повторно в производстве цемента. Именно поэтому нет никакого короткого или долгосрочного риска накопления металлических элементов. Кроме того, рассматриваемая рециркуляция весьма отличается от рециркуляции потребительских товаров, таких как алюминиевые банки, стекло, и т.д. У цементных установок весьма продолжительный срок службы (одно столетие в среднем). Таким образом, рассматриваемая рециркуляция значительно не влияет на накопление металлических элементов, даже в течение долгого срока. 28. Какая выгода для цементных производителей от использования промышленных отходов в качестве горючего по сравнению с использованием ископаемого топлива? Выгода находится в разнообразии источников энергии и сокращении издержек производства, приводящих к улучшенной конкурентоспособности для французских цементных производителей на мировом рынке. 29. Вы предлагаете вариант сжигания промышленных отходов в цементных печах как дополнение к основному направлению производства. Возможно это тактика, чтобы склонить на свою сторону должностных лиц, желающих поддержать справедливый баланс на французском рынке утилизации отходов? В Соединенных Штатах, например, 75 % промышленных отходов используют на цементных заводах, и часто у этих отходов нет никакой энергетической ценности! Может быть ваш бизнес направлен на захват французского рынка сжигания? Цель цементных производителей - произвести качественный цемент в самых лучших экономических условиях. Это - наша главная задача, наша деловая цель номер один. Использование отходов только один из аспектов путей достижения этой цели. Это становится тем более очевидным, когда каждый полагает, что технические ограничения цементных заводов препятствуют тому, чтобы они рассматривали все типы отходов.
docplayer.ru
Разработан эффективный способ утилизации бетонных отходов. Cleandex
Отходы не всегда выглядят, как бутылки из под содовой или груды невостребованных печатных изданий. Люди постоянно приспосабливают окружающую среду под свои потребности, а это неразрывно связано с появлением новых отходов.
Мы постоянно сносим, возводим, реконструируем здания, как результат – миллионы тонн строительного мусора. До недавнего времени единственным способом переработки бетонных отходов был механический: его разбивали и на выходе в лучшем случае получали обломки, которые можно было использовать в качестве основания для дорожного покрытия. Исследователи из группы бетонных технологий, Институт строительной физики общества Франхофера (Fraunhofer Institute for Building Physics) изобрели новый способ: использование молнии для раскола отдельных бетонных блоков на более мелкие составляющие, на отдельные компоненты. Другими словами это всё тот же метод электродинамической фрагментации, который ещё в 40-е годы 20 века был предложен советскими учёными, но так и не получивший своего развития.
Бетон является чрезвычайно универсальным и в этой связи самым популярным строительным материалом. Создаваемый из смеси цемента, воды и мелких и крупных заполнителей, как правило, соотношение песка, воды и щебня определяется маркой цемента. Производственный процесс этого материала простой и недорогой. Но даже при наличии столь широких достоинств есть и обратная сторона. Согласно исследованиям Института строительной физики общества Франхофера, ежегодно от 8 до 15% мировых выбросов углекислоты связано с производством бетона, вернее, главным образом его составляющей – цемента. Эти показатели могут значительно уменьшиться, если бетон переработать. Ключевой момент в процессе утилизации бетона – отделить натуральный и искусственный камень, чтобы затем его использовать при производстве новых смесей. И достичь этого можно с помощью метода электродинамической фрагментации, в ходе которого используются короткие импульсы (менее 500 наносекунд) индуцируемого грозового разряда (та же молния, действующая в необычной среде) позволяют отделить гравий от цемента. Как правило, электрический ток идёт по пути наименьшего сопротивления, а в случае с бетоном таким «путём» будут границы между разными компонентами, между частицами цемента и гравия. В итоге формируется плазменный канал, который создаёт волну давления, по силе сравнимую с мини-взрывом, который изнутри «разрывает» бетон. Исследователи поставили цель – утилизация 20 тонн бетонных отходов в час, и реализация этой цели намечена на ближайшие два года.
www.cleandex.ru
Способ получения цемента
Изобретение относится к производству строительных материалов и может быть использовано при производстве цементов различного назначения с активными минеральными добавками. Технический результат - снижение расхода портландцементного клинкера на производство цемента, получение цемента с повышенными прочностными и эксплуатационными свойствами, переработка техногенных отходов. В способе получения цемента, включающем смешивание и совместный помол портландцементного клинкера с гипсом и активной минеральной алюминий-кремнийсодержащей добавкой, в качестве активной минеральной добавки используют техногенные термообработанные алюминий-кремнийсодержащие отходы переработки минерального сырья в виде золы-уноса ТЭС от сжигания углей, термообработанной при 950-1050°С и/или в виде золы терриконов - горелой породы шахтных отвалов угольных месторождений, термообработанной при 600-850°С, которые подают на смешивание в количестве 5-25% от веса клинкера. 7 табл.
Изобретение относится к производству строительных материалов и может быть использовано при производстве добавочных цементов различного назначения.
Чтобы снизить энергетические и материальные затраты на производство цемента, изготовляют цементы составного типа, которые кроме клинкерной части содержат активные минеральные добавки. Замена части клинкера активной минеральной добавкой значительно экономит топливо и электроэнергию на производство цемента. Активные минеральные добавки вводят в состав цементов для улучшения их строительно-технических свойств. Активные минеральные добавки при затворении цемента водой взаимодействуют с гидроксидом кальция, выделяющимся при гидратации портландцемента. Образующиеся при этом гидросиликаты кальция практически не растворимы в воде. Таким образом, растворимая составляющая цементного камня Са(ОН)2 переводится в нерастворимое соединение. В этом смысл использования активных минеральных добавок:
экономя клинкерную часть, они в то же время придают цементу ряд особых свойств.
В качестве природных активных минеральных добавок широко используют горные породы: диатомит, трепел, опоку, горелые глинистые породы - глиежи, породы вулканического происхождения: вулканический пепел, туф, пемзу, витрофир, трасс.
Искусственные активные минеральные добавки представляют собой побочные продукты и отходы промышленности: быстроохлажденные (гранулированные) доменные шлаки, белитовый (нефелиновый) шлам - отход глиноземного производства, зола-уноса - отход, образующийся при сжигании угля, отходы и побочные продукты добычи минерального сырья.
С точки зрения доступности, стоимости и экологической безопасности представляют интерес техногенные активные минеральные добавки, являющиеся, по сути, отходами и побочными продуктами различных добывающих и перерабатывающих производств.
Известно вяжущее, состоящее из портландцементного клинкера, двуводного гипса и добавки в виде щелочной алюмосиликатной породы -сыннырита при следующем соотношении компонентов, мас.%:
Сыннырит - 30 - 35
Двуводный гипс - 3
Портландцементный клинкер - остальное (патент РФ №2125545, С04В 7/12, 1999 г., [1]).
Основные недостатки известного решения - ограничения по применению в качестве активной минеральной добавки в производстве цементов и недостаточная сырьевая база (сыннырит является побочным продуктом при разработке месторождений минералов группы нефелинов).
Известен способ получения цемента, включающий двухстадийную переработку цементного клинкера с измельчением на второй стадии совместно с остальными материалами в мельнице открытого цикла, в котором на первой стадии цементный клинкер поэтапно дробят сначала в вертикальной роторной мельнице с предварительной и заключительной классификацией посредством грохота на куски мельче 5 мм. Далее материал дробят в ударной дробилке с вертикальным валом и с встроенным классификатором до крупности - 1,0 мм, и, наконец, в горизонтальной шаровой дробилке с сепаратором до удельной поверхности 2000-3000 см2/г по Блейну или клинкер совместно с кварцевым песком, взятым в соотношении от 1:1 до 1:0,5, дробят струйным методом в ударной дробилке с вертикальным валом. При этом другие компоненты цемента также предварительно перерабатывают. Доменный шлак тонко дробят в шаровой дробилке с сепаратором до удельной поверхности не менее 1500 см2/г по Блейну, золошлаки или золы-уноса размалывают в роликовой мельнице до удельной поверхности не менее 4000 см2/г по Блейну, известняки и гипсовый камень дробят последовательно в щековой и ударно-отражательной дробилках на куски мельче 5 мм, а на второй стадии помола все предварительно измельченные таким образом материалы совместно домалывают в шаровой мельнице открытого цикла до удельной поверхности цементного порошка 4000-5000 см2/г по Блейну (патент РФ №2388710, С04В 7/00, 2010 г.[2]).
Основной недостаток известного решения - сложная аппаратурно-технологическая схема, значительные энергетические затраты, что повышает себестоимость товарного продукта.
Известен способ изготовления цемента низкой водопотребности совместным помолом до удельной поверхности 400-700 м2/кг ингредиентов портландцементного клинкера, сульфатно-кальциевого ингредиента и модификатора, включающего ускоритель твердения и органический водопонижающий реагент, в котором в качестве указанного портландцементного клинкера используют гранулированный продукт обжига цементной сырьевой смеси, имеющей в своем составе примеси сульфатов и карбонатов щелочных металлов. Эти примеси обожжены в форме застывших на поверхности гранул указанного продукта капель и натеков безводных соединений и/или игл и сростков их кристаллогидратов, связанных в процессе помола ингредиентов органическим водопонижающиим реагентом с формированием солевой фазы ускорителя твердения в органическом реагенте в количестве 10-50% от массы последнего. Помол ведут при соотношении указанных ингредиентов в пределах соответственно 100:(1-7):(0,6-2,5) мас.ч. до достижения стехиометрии фазы алита в поверхностном слое частиц указанного клинкера, причем момент этого достижения и соответственно окончания помола устанавливают по критерию степени агрегации частиц указанного цемента, равной 5-15 об.% при гигроскопической влажности не более 3 мас.%.
В состав указанного цемента дополнительно может быть введена активная минеральная добавка и/или наполнитель при совместном или раздельном помоле с последующим смешением при массовых соотношениях портландцементного клинкера и активной минеральной добавки и/или наполнителя от 100: 5 до 100: 850 при гигроскопической влажности 0,01-3 мас.%.
В качестве активной минеральной добавки может быть использован один или два компонента из группы: гранулированный доменный шлак, топливный шлак, зола-уноса, вулканический пепел, пемза, туф, кварцевый песок, полевошпатовый песок, высевки от дробления гранита, хвосты обогащения руд, стеклобой, кирпичный бой, керамзитовая или стеклокерамзитовая пыль (патент РФ №2207995, С04 В7/52, 2003 г.[3]).
По назначению, технической сущности, наличию сходных признаков данное техническое решение выбрано в качестве ближайшего аналога.
Получаемый по техническому решению цемент имеет высокие потребительские свойства, но вместе с тем, используемые активные минеральные добавки в большей части дефицитны или требуют дополнительной предварительной подготовки перед применением, что повышает себестоимость товарного продукта.
Задачами предлагаемого технического решения являются: снижение себестоимости и повышение качества цемента, расширение сырьевой базы для производства цемента за счет использования недефицитных техногенных отходов переработки минерального сырья.
Техническими результатами являются снижение расхода портландцементного клинкера на производство цемента, получение цемента с повышенными прочностными и эксплуатационными свойствами, переработка техногенных отходов.
Технические результаты достигаются тем, что в способе получения цемента, включающем смешивание и совместный помол портландцементного клинкера с гипсом и искусственной активной алюминий-кремнийсодержащей минеральной добавкой, содержащей золу - унос ТЭС от сжигания углей, в качестве искусственной активной минеральной добавки используют техногенные термообработанные алюминий - кремнийсодержащие отходы переработки минерального сырья в виде золы - уноса ТЭС от сжигания углей и/или в виде золы терриконов -горелой породы шахтных отвалов угольных месторождений, которые подают на смешивание в количестве 5-25% от веса клинкера.
Кроме того, по предлагаемой технологии может быть приготовлен цемент, содержащий портландцементный клинкер, гипс и активную минеральную алюминий-кремнийсодержащей добавку в виде золы - уноса ТЭС от сжигания углей и/или в виде золы терриконов - горелой породы шахтных отвалов угольных месторождений при следующем соотношении компонентов, вес.%:
гипс | 4,5-7,5 |
зола - уноса ТЭС и/или зола терриконов | 4,5-18,5 |
портландцементный клинкер | остальное |
Сравнительный анализ предлагаемого технического решения с решением по ближайшему аналогу показывает следующее.
Известное и предлагаемое решения характеризуются сходными общими признаками:
- использование для производства цемента портландцементного клинкера и гипса;
- использование активной алюминий - кремнийсодержащей минеральной добавки, содержащей золу - уноса;
- смешивание и совместный помол портландцементного клинкера с гипсом и активной алюминий - кремнийсодержащей минеральной добавкой; содержащей золу - уноса.
Предлагаемое решение отличается от известного решения следующими признаками:
- в качестве активной алюминий - кремнийсодержащей минеральной добавки используют термообработанные алюминий - кремнийсодержащие отходы переработки минерального сырья;
- в качестве термообработанных алюминий - кремнийсодержащих отходов переработки минерального сырья на смешивание и помол подают:
- золу - уноса ТЭС и золу терриконов - горелую породу шахтных отвалов угольных месторождений;
- золу - унос ТЭС и/или золу терриконов - горелую породу шахтных отвалов угольных месторождений в количестве 5-25% от веса клинкера.
Причем, на смешивание может быть подана смесь золы - уноса и золы терриконов в различных соотношениях в количестве 5-25% от веса клинкера или зола терриконов в количестве 5-25% от веса клинкера.
Наличие в предлагаемом решении признаков, отличительных от признаков, характеризующих решение, принятое в качестве ближайшего аналога, позволяет сделать вывод о соответствии предлагаемого технического решения условию патентоспособности изобретения «новизна».
Техническая сущность предлагаемого решения заключается в следующем.
Используемые в предлагаемом решении техногенные отходы представляют собой искусственное, термообработанное минеральное сырье, образующееся при добыче и сжигании каменного угля. Зола уноса образуется в результате сжигания угля на тепловых станциях, улавливается электрофильтрами и в сухом состоянии используется на производственные нужды. Зола терриконов - горелая порода шахтных отвалов угольных месторождений - представляет собой продукт естественной термообработки породы, извлеченной из угольных шахт вместе с углем и складированной в виде искусственных насыпей - терриконов.
В случае золы - уноса термообработка материала происходит при 950-1050°С, в случае золы терриконов - при 600-850°С. Образующиеся в том и другом случае продукты обжига богаты дегидратированными глинистыми минералами, из которых образуются высокоактивные остатки кристаллов. Эти активные соединения на основе алюмосиликатов при затворении цемента водой взаимодействуют с гидроксидом кальция, образуя водонерастворимые гидросиликаты кальция, и повышают тем самым прочностные и эксплуатационные характеристики цемента.
При использовании предлагаемого технического решения реализуется вариант замкнутого технологического и экологического цикла, включающего добычу угля, его применение на ТЭС для производства электроэнергии и тепла, также утилизацию, как отходов добычи угля (золы терриконов), так и продуктов его сжигания в виде золы-уноса ТЭС в производстве цемента.
Замкнутый технологический цикл: добыча угля - производство электроэнергии и тепла - утилизация техногенных отходов - производство цемента, с точки зрения логистики требует размещения этих производств достаточно компактно на территории региона. В результате снижаются транспортные расходы, как на транспортировку угля от угольных разрезов и шахт к ТЭС или ТЭЦ, так и золы терриконов от отвалов угольных шахт и золы - уноса ТЭС к цементным заводам.
Применение в предлагаемом решении в качестве активной минеральной добавки техногенных термообработанных алюминий кремнийсодержащих отходов переработки минерального сырья направлено на решение сразу нескольких задач:
- расширение сырьевой базы эффективных, широкодоступных активных минеральных добавок для производства цемента;
- повышение качества и снижение себестоимости производства цемента;
- утилизация крупнотоннажных техногенных отходов добычи и переработки каменного угля.
Использование золы - уноса и/или золы терриконов в количестве 5-25% от веса клинкера обусловлено следующими обстоятельствами. Количество активной минеральной добавки, вводимой в добавочный цемент, определяется качеством клинкера. Чем выше качество клинкера, тем большее количество добавки может быть использовано при помоле цемента. При низкой активности клинкера ввод активной минеральной добавки минимален и может составлять 5-10% от веса клинкера. Клинкер высокого качества позволяет вводить при помоле максимальное количество активной минеральной добавки: 15-25% от веса клинкера. При введении золы - уноса и/или золы терриконов в количестве более 25% от веса клинкера активность получаемого цемента снижается ниже нормируемых показателей.
Сравнительный анализ предлагаемого технического решения с другими известными решениями в данной области показывает следующее.
1. Известен сульфатостойкий портландцемент, включающий портландцементный клинкер, сульфат кальция и изверженную алюмосиликатную горную породу с мелкокристаллической структурой, в котором указанная горная порода имеет размер кристаллов до 20 мкм и содержит минералы, представленные твердыми растворами авгитово -анортитового ряда. Кристаллы в структуре породы окружены стеклообразными прослойками, портландцементный клинкер содержит трехкальциевый алюминат С3А в количестве до 5 мас.%, а сумма трехкальциевого алюмината С3А и четырехкальциевого алюмоферрита C4AF в клинкере составляет не более 22 мас.%, при следующем соотношении компонентов, мас.%:
Клинкер указанного состава 60-90
Сульфат кальция 2-8
Указанная горная порода - остальное
(патент РФ №2237627, С04В 7/02, 2004 г., [4]).
В известном решении в качестве активной минеральной добавки используют изверженную (термообработанную в естественных условиях) алюмосиликатную горную породу с мелкокристаллической структурой. Основной недостаток этого решения - дефицитность добавки.
2. Известен «Способ изготовления цемента, бетона на его основе и бетонных и железобетонных изделий и монолитных конструкций из полученного бетона» (патент ЕА 002673 В1, С04В 7/00, 2002 г., [5]), в котором в цемент посредством совместного и/или раздельного помола с последующим смешением дополнительно может быть введен гипсовый компонент и дополнительно при помоле и/или путем смешения может быть введен активный кремнезем в виде вторичного продукта кремниевого производства и/или пыль, уловленная из отходящих газов печей ферросплавного производства в количестве 0,2-10 мас.% от указанного цемента (п.46 формулы изобретения), может быть введена активная минеральная добавка в количестве 1-85 мас.% указанного цемента (п.47 формулы изобретения), может быть введен расширяющий компонент в виде глиноземистого клинкера или глиноземистого шлака в количестве 2,5-50 мас.% от указанного цемента (п.48 формулы изобретения).
3. Известен «Портландцементный клинкер, цемент на его основе и способ изготовления коррозиеустойчивого бетона» (патент РФ №2058952, С04В 7/02, 1996 г., [6]). В известном решении цемент может содержать активную минеральную добавку в количестве 5-50% к массе клинкера (п.5 по пп.3,4 формулы изобретения), в качестве активной минеральной добавки цемент может содержать термически обработанные материалы: дегидратированный каолин, или дегидратированную каолинитовую глину, или дегидратированную глину, или глинистый сланец, или горелую породу, или глиеж (п.8 по п.5 формулы изобретения), в качестве активной минеральной добавки цемент может содержать искусственный материал: доменный гранулированный шлак, или золу-уноса, или золо-шлак тепловых электростанций (п.9 по п.5 формулы изобретения).
При помоле клинкера (п.18 по п.17 формулы изобретения) вводят активную минеральную добавку в количестве 5-50% к массе клинкера и в качестве активной минеральной добавки (п.19 по п.18 формулы изобретения) используют опоку, или трепел, или диатомит, или вулканический пепел, или вулканический туф, или пемзу, или трасс, или дегидратированный каолин, или дегидратированную каолинитовую глину, или термически обработанный сланец, или горелую породу, или глиеж, или доменный гранулированный шлак, или золу-уноса или золо-шлак тепловых электростанций.
4. Известно смешивание золы-уноса, имеющей размер частиц не более 20 мкм, в количестве от 2 до 25% по весу с цементом, содержащим цементный клинкер, включающий Al2O3 и Fe2O3, в котором соотношение Al2O3 к Fe2O3 составляет от 0,05 до 0,62, а содержание C2S составляет 35-55% по весу (патент РФ №2199498, С04 В 7/02, 2003 г., [7]).
В отличие от известных решений в предлагаемом решении в качестве искусственной активной минеральной добавки используют комплексный компонент - техногенные термообработанные алюминий - кремний - содержащие отходы переработки минерального сырья в виде золы - уноса ТЭС от сжигания углей и/или в виде золы терриконов - горелой отработанной породы шахтных отвалов угольных месторождений. Кроме того, активные минеральные добавки подают на смешение и совместный помол с портландцементным клинкером и с гипсом в количестве 5-25% от веса клинкера. Эти техногенные термообработанные активные минеральные добавки эффективны при использовании в указанных пределах и являются доступными крупнотоннажными промышленными отходами добычи и переработки каменного угля.
В результате сравнительного анализа предлагаемого технического решения с другими известными решениями в данной области не выявлено технических решений, характеризующихся аналогичной с предлагаемым решением совокупностью признаков, использование которой позволяет достигать аналогичные технические и технико-экономические результаты.
На основании вышеизложенного можно сделать вывод о соответствии предлагаемого технического решения условию патентоспособности «изобретательский уровень».
Предлагаемое техническое решение реализуется следующим образом.
На смешивание и помол подают портландцементный клинкер, гипс в количестве 4,5-7,5% от веса клинкера и активную минеральную алюминий-кремнийсодержащей добавку в виде золы - уноса ТЭС от сжигания углей и/или в виде золы терриконов - горелой породы шахтных отвалов угольных месторождений в количестве 5-25% от веса клинкера. В результате перемешивания и помола компонентов получают цемент с указанным в п.4 формулы изобретения соотношением компонентов.
Пример 1
Для оценки эффективности использования золы терриконов в качестве активной минеральной добавки использовались следующие материалы: клинкер Ангарского цементного завода, природный гипс Новонукутского месторождения (Иркутская обл.), зола уноса Иркутской ТЭЦ - 1 и горелые породы из шахтных терриконов Черемховского угольного бассейна (Иркутская обл.).
Состав исходных материалов приведен в таблицах 1 -5.
Таблица 2 | ||||||
Средний химический состав гипсового камня | ||||||
Содержание соединений, % вес. | ||||||
CaO | SO3 | MgO | SiO2 | Al2O3 | Fe2O3 | Прочие |
30,30 | 32,25 | 5,54 | 5,53 | 0,55 | 0,74 | 25,09 |
Таблица 3 | ||||||||||
Средний химический состав золы уноса ТЭЦ-1 | ||||||||||
Содержание оксидов, % вес. | ||||||||||
SiO2 | Al2O3 | Fe2O3 | CaO | MgO | К2О | Na2O | MnO | TiO2 | SO3 | P2O5 |
60,55 | 22,39 | 7,34 | 4,39 | 1,96 | 1,25 | 0,26 | 0,038 | 0,46 | 0,76 | 0,05 |
Таблица 4 | |||||||||
Средний химический состав золы терриконов - горелой породы шахтных отвалов угольных месторождений Черемховского угольного бассейна | |||||||||
Содержание оксидов, % вес. | |||||||||
SiO2 | Al2O3 | Fe2O3 | CaO | MgO | K2O | Na2O | MnO | TiO2 | SO2 |
65,6 | 18,7 | 6,03 | 2,2 | 2,6 | 1,9 | 0,35 | 0,027 | 0,30 | 0,29 |
Таблица 5 | |
Усредненные физико-механические свойства зо терриконовой | |
Характеристики, размерность | Значения |
Естественная влажность, % вес. | 8,8 |
Насыпная плотность, кг/м3 | 1085 |
Содержание зерен 0-5 мм, % вес. | 58,6 |
Содержание зерен 5-70 мм, % вес. | 41,4 |
Истинная плотность, г/см3 | 2,58 |
Прочность в цилиндре, г/см2 | 17,7 |
Водопоглощение, % вес. | 15,3 |
Коэффициент размягчения | 0,69 |
Оценка эффективности использования золы терриконов в качестве активной минеральной добавки в сравнении с золой уноса проводилась на цементах лабораторного помола с общим содержанием активной минеральной добавки 18% от веса портландцементного клинкера (ПЦК). С таким содержанием активной минеральной добавки были приготовлены 5 композиций. Состав и содержание гипсового камня (камень гипсовый - КГ), условия измельчения образцов во всех композициях были одинаковыми. Шестая композиция была приготовлена без золы уноса с содержанием золы терриконов 25% вес. Содержание золы уноса (ЗУ) и золы терриконовой (ЗТ) в композициях 1-6 менялось в заявляемых пределах (по пп.1-3 формулы изобретения). Седьмая композиция также содержала только золу терриконов в количестве 28% вес. и гипс. Результаты механических испытаний цементов с различными комбинациями активных минеральных добавок представлены в таблице 6.
Таблица 6 | |||
- Изменение механических свойств цементов от комбинации добавок (золы уноса и золы терриконовой) | |||
№ | Механические свойства | Прочность образца, МПа | |
Композиция 1: ПЦК+0% ЗТ+18% ЗУ+5,2% КГ | |||
1 | Пропаренные в возрасте 1 сут. | при изгибе | 3,57 |
при сжатии | 19,28 | ||
2 | Твердение в воде, возраст 7 сут. | при изгибе | 3,61 |
при сжатии | 23,02 | ||
3 | Твердение в воде, возраст 28 сут. | при изгибе | 6,35 |
при сжатии | 40,23 | ||
Композиция 2: ПЦК+5,5% ЗТ+12,5% ЗУ+5,2% КГ | |||
1 | Пропаренные в возрасте 1 сут. | при изгибе | 3,80 |
при сжатии | 20,56 | ||
2 | Твердение в воде, возраст 7 сут. | при изгибе | 3,77 |
при сжатии | 23,58 | ||
3 | Твердение в воде, возраст 28 сут. | при изгибе | 6,33 |
при сжатии | 40,56 | ||
Композиция 3: ПЦК+9% ЗТ+9% ЗУ+5,2% КГ | |||
1 | Пропаренные в возрасте 1 сут. | при изгибе | 4,14 |
при сжатии | 22,15 | ||
2 | Твердение в воде, возраст 7 сут. | при изгибе | 3,90 |
при сжатии | 24,58 | ||
3 | Твердение в воде, возраст 28 сут. | при изгибе | 6,64 |
при сжатии | 41,89 | ||
Композиция 4: ПЦК+12,5% ЗТ+5,5% ЗУ+5,2% КГ | |||
1 | Пропаренные в возрасте 1 сут. | при изгибе | 4,28 |
при сжатии | 24,23 | ||
2 | Твердение в воде, возраст 7 сут. | при изгибе | 4,41 |
при сжатии | 26,22 | ||
3 | Твердение в воде, возраст 28 сут. | при изгибе | 6,92 |
при сжатии | 43,56 | ||
Композиция 5: ПЦК+18% ЗТ+0% ЗУ+5,2% КГ | |||
1 | Пропаренные в возрасте 1 сут. | при изгибе | 4,37 |
при сжатии | 28,98 | ||
2 | Твердение в воде, возраст 7 сут. | при изгибе | 4,58 |
при сжатии | 29,56 | ||
3 | Твердение в воде, возраст 28 сут. | при изгибе | 7,22 |
при сжатии | 45,24 | ||
Композиция 6: ПЦК+25% ЗТ+0% ЗУ+5,2% КГ | |||
1 | Пропаренные в возрасте 1 сут. | при изгибе | 4,28 |
при сжатии | 27,05 | ||
2 | Твердение в воде, возраст 7 сут. | при изгибе | 4,40 |
при сжатии | 28,80 | ||
3 | Твердение в воде, возраст 28 сут. | при изгибе | 7,02 |
при сжатии | 44,09 | ||
Композиция 7: ПЦК+28% ЗТ+0% ЗУ+5,2% КГ | |||
Пропаренные в возрасте 1 сут. | при изгибе | 4,08 | |
при сжатии | 23,60 | ||
Твердение в воде, возраст 7 сут. | при изгибе | 3,89 | |
при сжатии | 26,45 | ||
при изгибе | 6,67 | ||
Твердение в воде, возраст 28 сут. | при сжатии | 39,20 |
Из полученных результатов лабораторных опытов следует, что с уменьшением отношения золы уноса к золе терриконов при одинаковом расходе активной минеральной добавки прочность цементного камня в пластичных растворах, как при изгибе, так и при сжатии увеличивается вплоть до 25% ввода активной добавки. Увеличение прочности образцов с добавкой золы терриконов наблюдается при различных сроках твердения и после пропаривания. Причем наибольший эффект достигается в композиции, где в качестве активной минеральной добавки используется только зола терриконов. При введении золы терриконов более 25% вес. (композиция 7) снижается активность получаемого цемента.
Дополнительные показатели качества цемента с добавкой 18% золы терриконов (композиция 5, таблица 6) приведены в таблице 7.
Таблица 7 | |
Качественные показатели цемента с золой терриконов качестве активной минеральной добавки. | |
Характеристики, размерность | Показатели качества |
Истинная плотность, г/см3 | 3,00 |
Насыпная плотность, г/см3 | 1,085 |
Тонкость помола: остаток на сите 0,08, % | 13,8 |
Тонкость помола: удельная поверхность, м2/кг | 326 |
Нормальная густота, % вес. | 28,5 |
Начало схватывания, мин. | 220 |
Конец схватывания, мин. | 430 |
Коэффициент водоотведения, % | 14,1 |
Исследования подтверждают гарантированную воспроизводимость результатов по предлагаемому техническому решению и возможность варьирования улучшенными потребительскими свойствами получаемого цемента в зависимости от технологических возможностей и потребностей.
Использование предлагаемого технического решения позволит расширить сырьевую базу цементной (строительной) промышленности, утилизировать техногенные термообработанные алюминий - кремний-содержащие отходы переработки минерального сырья, улучшить экологическую обстановку в районах добычи каменного угля и расположения ТЭС, снизить себестоимость производства цемента, повысить его качество и эксплуатационные свойства.
Источники информации
1. Патент РФ №2125 545, С04В 7/12, 1999 г.
2. Патент РФ №2388710, С04В 7/00, 2010 г.
3. Патент РФ №2207995, С04В 7/52, 2003 г.
4. Патент РФ №2237627, С04В 7/02, 2004 г.
5. Патент ЕА 002673 В1, С04В 7/00, 2002 г.
6. Патент РФ №2058952, С04В 7/02, 1996 г.
7. Патент РФ №2199498, С04В 7/02, 2003 г.
Способ получения цемента, включающий смешивание и совместный помол портландцементного клинкера с гипсом и активной минеральной алюминий-кремнийсодержащей добавкой, отличающийся тем, что в качестве активной минеральной добавки используют техногенные термообработанные алюминий-кремнийсодержащие отходы переработки минерального сырья в виде золы-уноса ТЭС от сжигания углей, термообработанной при 950-1050°С и/или в виде золы терриконов -горелой породы шахтных отвалов угольных месторождений, термообработанной при 600-850°С, которые подают на смешивание в количестве 5-25% от веса клинкера.
www.findpatent.ru
утилизация цемента Видео

6 мес. назад
Водитель не проверил надежность подсоединения рукава, и во время выгрузки цемента рукав сорвало. Последств...
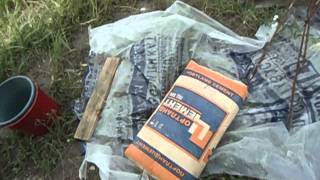
3 г. назад
Канал стройка Самостоятельная организация процесса стройки. Строительство частного дома. Строительства...

1 г. назад
Процесс утилизации двухколесной техники где-то там у буржуинов. Купить новый велосипед взамен старого...
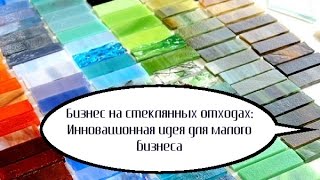
3 г. назад
Всё необходимое оборудование для реализации данной бизнес идеи можно купить в компании EURASIA GROUP. http://eurasia-group...

1 г. назад
Утилизация изношенных покрышек. Из них можно сделать еще много полезного. Недорогие аксессуары для автомоб...
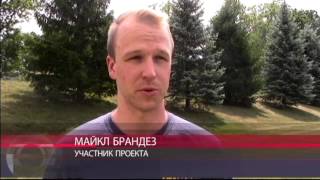
2 г. назад
Команда ученых занялась исследованиями в области переработки бетона Originally published at - http://www.golos-ameriki.ru/a/concrete-rec...
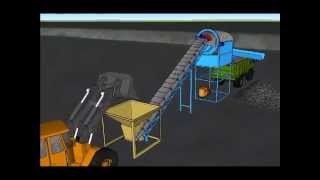
4 г. назад
Проект и оборудование очистки шламонакопителей и отстойников от илов с последующими их обезвоживанием...
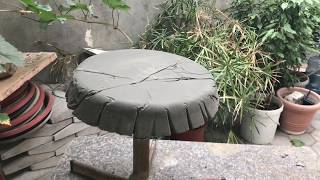
1 г. назад
Нашла ножку от нашего старого старого стула крутящегося и решила сделать из него табуреточку для сада,...

4 г. назад
Технология утилизации (переработки) бывших в употреблении деревянных железнодорожных шпал в печах цементн...
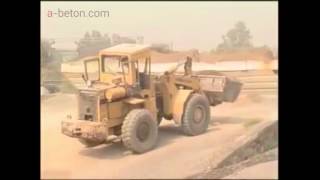
3 г. назад
Электричество - "линия жизни" современной цивилизации. В Индии угольные электростанции - главный источник...
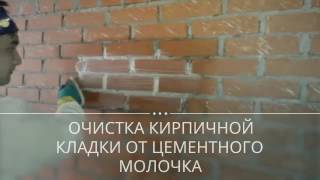
2 г. назад
Очистка кирпичной кладки под лофт от цементных пятен методом механической обработки, с применением безвре...
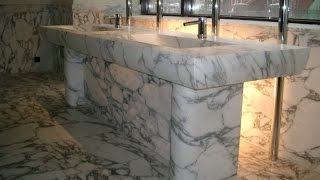
2 г. назад
Всё необходимое оборудование для реализации данной бизнес идеи можно купить в компании EURASIA GROUP. http://eurasia-group...
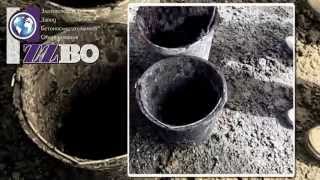
3 г. назад
Рециклинг и утилизация с переработкой бурового нефтяного шлама методом перемешивания с цементом в двухвал...
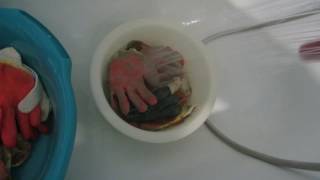
1 г. назад
Есть вопрос? Задай его под видео! Подробности ищи там же - внизу под видео. Группа в ВК: https://vk.com/stroi_saki По...
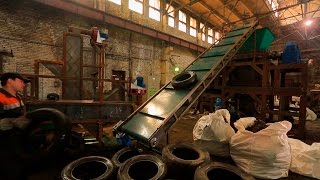
2 г. назад
ООО «Альфа-СПК», г. Кемерово. Переработка изношенных шин. В Кузбассе образование изношенных покрышек варьи...
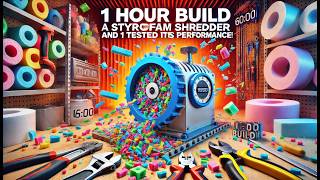
2 г. назад
Как за 1 час из подручных материалов сделать дробилку(измельчитель) пенопластового лома для получения крош...
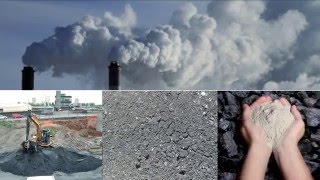
2 г. назад
Технология производства экологически чистого цемента Green Cement из отходов работы ТЭС и ТЭЦ от НИИ KIGAM (Республ...
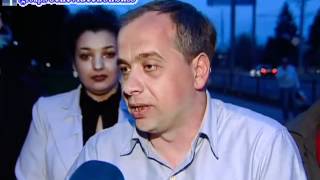
6 г. назад
Договорились быстрее, чем предполагали. Жители поселка Абакумова после программы "Вопрос власти" окружили...
turprikol.com
HeidelbergCement: отходы — это ресурс!
На данном этапе развития нашей цивилизации мы вынуждены признать, что человечество столкнулось с проблемой, которая вышла за рамки какого-то конкретного государства, и которая тесно сопряжена с мировым ростом населения и развитием промышленности, — это проблема утилизации отходов. Если принципы обращения с отходами не изменятся в ближайшем будущем, то мы рискуем столкнуться с экологической катастрофой уже в этом столетии, пишет Бизнес-71.
Государства с развитой экономикой тратят все больше средств на создание инфраструктуры по переработке и утилизации отходов, оставляя все меньшую долю для захоронения. Однако по-настоящему ускорить этот процесс может помочь промышленный сектор. Так называемая экономика замкнутого цикла позволяет производствам-источникам отходов и производствам-потребителям выстраивать цепочки взаимоотношений, когда отходы становятся ресурсом.
Цементная промышленность, представленная 5670 заводами в мире, способна выступить активным участником экономики замкнутого цикла и взять на себя определенную долю по утилизации некоторых типов отходов в регионах расположения производств. На сегодняшний день объем отходов, утилизируемых в цементных печах по всему миру, составляет более 100 миллионов тонн, но это лишь 20% от потенциала.
В силу особенностей технологии производства цемента, температура в печи, создаваемая главными горелками, достигает 2000°С, что позволяет экологично утилизировать многие виды отходов, превращая их в топливо для производства. Если кратко описать процесс, происходящий в печи цементного завода, то получится следующее: некоторое количество сырьевой смеси (около 200 т в час) протекает мимо горелок. Зола от сгорания альтернативного топлива попадает в раскаленную смесь, вступает в реакцию с минералами и становится неотъемлемой частью конечного продукта – клинкера. Далее клинкер отправляется на помол, где становится цементом. Простой расчет топливной смеси для такого производства дает цифру, равную приблизительно 30 тоннам используемого топлива в час (смесь угля и топлива из отходов), что добавляет в процесс около 20% золы, а это означает, что 6 тонн золы поглощаются 200 тоннами сырьевой смеси ежечасно. Органическая часть выступает в качестве альтернативного топлива, прекрасно замещая невозобновляемые уголь и газ, в то время как минеральная составляющая — кремний, кальций и алюминиевые компоненты — являются ценными составляющими сырьевой смеси для изготовления клинкера, замещая сырьевые материалы. В этом процессе отходов нет.
Использование в производстве золы от сжигания отходов не сказывается на качестве выпускаемой продукции. А выбросы цементных заводов, применяющих альтернативное топливо, имеют те же допустимые значения, что и заводов, работающих на обычном угле. Происходит это благодаря длительности пребывания материала в печи при высокой температуре.
Срок эксплуатации цементных заводов в зависимости от различных факторов составляет от 40 до 80 лет. Первоначальные инвестиции в строительство и получение разрешений на использование полезных ископаемых очень высоки. Таким образом, компания, решившаяся на строительство цементного завода, вернет вложенные инвестиции только через несколько десятилетий после запуска завода. Соответственно, цементники ориентированы на долгосрочные отношения с ключевыми поставщиками, в том числе топлива и сырьевых материалов, что делает их надежными партнерами на многие годы.
В таких странах, как Япония, Канада, страны Западной Европы, где тарифы на захоронение отходов высоки, экономически привлекательными становятся предприятия по переработке отходов в энергию. В этих странах цементные заводы работают в системе обращения с отходами наряду с предприятиями по переработке. Но там, где тарифы на захоронение не могут быть значительно увеличены, только цементные заводы могут предложить экономически выгодный сценарий.
Примером подобной ситуации может послужить Польша, которая достигла значительных успехов в вопросе уменьшения количества свалок, используя возможности цементных производств (80% ТБО утилизируется в цементных печах). Польша начала реализовывать проекты строительства предприятий для выработки энергии из отходов, одновременно увеличивая долю топлива из отходов для цементного производства. В 2011 году Министерство экологии Польши поставило целью перерабатывать 50% от направляемых на полигоны бытовых отходов к 2013 году и к 2020 году снизить объемы захоронений до 35% от общего объема.
В Индонезии власти негативно относятся к захоронению отходов, особенно вокруг столицы – Джакарты. Из-за особенностей этого региона ТБО содержит значительное количество органического материала. Поэтому теплотворная способность отходов мала, и они не представляют особого интереса для предприятий по выработке энергии, требующих в этом случае дотаций от государства. Цементные же производства смогли предложить решение по утилизации ТБО и промышленных отходов по тем же тарифам, что и захоронение.
Власти КНР чрезвычайно активны в вопросах обращения с отходами. За последние годы были введены в эксплуатацию новые системы водоочистки, что привело к увеличению количества перерабатываемого илового осадка с очистных станций. Ученые признают, что развитие систем водоочистки происходит стремительными темпами благодаря цементной отрасли, поскольку она предоставляет возможность утилизации осадка. Представители Инициативы устойчивости цементной промышленности (CSI)от Всемирного совета по устойчивому развитию (WBCSD) отметили предприятие HeidelbergCement на юге Китая как яркий пример для всей цементной промышленности. Отходящие от цементной печи газы используются для подсушивания илового остатка БОС до влажности 40%, чтобы затем использовать как топливо. В настоящее время проект уже обслуживает 3 миллиона жителей.
Страны Бенилюкс имеют огромные нефтяные и химические производства. Эти сектора промышленности неизбежно являются производителями широкого спектра опасных отходов, которые необходимо утилизировать особенно тщательно. Около 25 лет назад частные инвесторы решили начать производство топлива, подходящего для цементной промышленности, из твердых опасных отходов. На сегодняшний день в Бельгии существуют две развитые платформы по обращению с опасными отходами – одна в Сенеффе (эксплуатируется компанией Geocycleот Holcim), другая – Recyfuel в Лиге (совместное предприятие компаний Sita и HeidelbergCement), которые перерабатывают 50% объема опасных отходов Бельгии, а также принимают специфические отходы соседних стран.
Утилизация некоторых типов отходов в цементных печах —это эффективное и экологичное решение. Кроме того, это также способ сокращения использования невозобновляемых природных ресурсов, снижения воздействия на окружающую среду, стимулирования экономики и решения ряда локальных и мировых проблем с отходами.
Многие европейские цементные заводы HeidelbergCement уже вышли на уровень, когда более половины топлива, используемого на заводе, приходится на альтернативное. Все процессы, связанные с использованием альтернативного топлива на заводах, контролируются с особой тщательностью – от входного лабораторного контроля до замеров выбросов из заводской трубы. Имея огромный опыт использования альтернативного топлива по всему миру, компания намерена применить его и на заводах в России.
cementinfo.ru