Инструкция по изготовлению гранулятора для пеллет. Производство пиллетов технологический процесс
Технология производства пеллет и древесных гранул своими руками
Пеллеты — это небольшие гранулы из отходов древесного производства, сельского хозяйства или заводов по изготовлению природного топлива. Используются они в качестве экологического чистого и безопасного топливного материала для домашних очагов. Сделать пеллеты своими руками не так сложно, если есть необходимое оборудование и материалы.
Преимущества пеллет
Пеллеты обладают рядом преимуществ перед другими видами отопительного материала:
- Большая теплоотдача,
- Удобное хранение,
- Экономичность использования,
- Пожаробезопасность,
- Экологичность,
- Возможность хранения рядом с жилыми помещениями,
- Не вызывает аллергии при горении и хранении,
- Доступность,
- Экономическая выгода: использование пеллет снижает стоимость отопления дома и хозяйственных построек в несколько раз,
- Высокая теплопроводность.
В России данный вид топлива только набирает популярность, но в европейских странах и США он широко используется.
Отопительные гранулы не только выгоднее, чем щепа с торфом, брикеты или же уголь, но и намного удобнее во время транспортировки, разгрузки и погрузки.
Этапы производства древесных гранул
В домашних условиях для производства пеллет хорошо подходит любая древесина, щепа, стружка, опилки, торф, лузга, древесная кора и даже солома. Если топливный материал предназначается для отопления хозяйственных построек, можно использовать и куриный помет.
Измельчение и сушка
Для измельчения перерабатываемого сырья используют дробилку. На выходе материал должен иметь максимальные размеры: 2,5*2,5*2 см. Но для большей экономии электроэнергии в процессе сушки, рекомендуется измельчать древесину до максимально возможной мелкой фракции. Сушка необходима, если влажность используемого материала более 12%. Древесный материал с меньшей, чем 8%, влажностью нуждается в дополнительном увлажнении.
Сушильные аппараты бывают двух типов. Ленточные устройства для просушки опилок или щепы стоят дороже, но в работе более безопасны и надежны. Работать они могут на горячем воздухе, специальных топочных газах или же на пару. Барабанная сушилка имеет более простое устройство, и может быть изготовлена в домашних условиях. Опилки или щепа просушиваются во вращающемся барабане при помощи горячего воздуха, идущего от сгораемого топлива.
Водоподготовка
После сушки исходный материал подвергается, если это необходимо, повторному измельчению.
Оптимальные размеры сырья — не более четырех миллиметров.
Водоподготовка — очень важный этап процесса изготовления пеллет. Если древесина имеет влажность менее восьми процентов — она будет плохо прессоваться, поэтому ее необходимо дополнительно увлажнить. Лучше всего использовать смеситель шнековый, в котором предусмотрена опция подачи водяного пара или же горячей воды. Более предпочтителен пар, так как он увеличивает пластичность щепы, опилок или стружки твердой древесины.
Гранулирование и охлаждение
Основа гранулирования — прессование. Проводится прессование при помощи пресса или же гранулятора. Исходное сырье засыпается в принимающее устройство аппарата, поступает в рабочую камеру, где обрабатывается и нарезается на гранулы нужного размера. В рабочей камере гранулятора температура может достигать ста градусов из-за адиабатических процессов и сопутствующих сил трения.
Оптимальные температурные условия для образования гранул высшего качества — от ста до ста двадцати градусов.
Если температура выше — начнутся необратимые сложные физические процессы, которые приведут к значительному ухудшению качества гранул. Чтобы произвести кондиционирование готовых пеллет после прессования, нужно их охладить. Обычно для охлаждения древесные пеллеты рассыпают на плоской и ровной поверхности. После того как гранулы приобрели нормальную температуру, их можно расфасовать по мешкам или пакетам для хранения.
Оборудование для производства древесных гранул
Изготовление пеллет в домашних условиях предполагает наличия специального оборудования:
- Для первичного и повторного измельчения нужна дробилка,
- Для корректировки влажности сырья — сушильная камера,
- Сито,
- Аппарат для гранулирования или пресс.
Получить древесные гранулы будет проще, если использовать гранулятор со стальной плоской матрицей.
Аппарат для дробления сырья можно купить, а можно смастерить собственноручно или даже заменить циркулярной пилой, предварительно установив на нее режущий диск с фрезами лепестковой формы. Если в качестве сырья используются опилки или некрупная стружка, то первичное дробление можно пропустить.
Важной частью является и сито. Оно нужно для просеивания измельченного сырья для выявления инородных материалов и крупных необработанных частиц. Собрать его просто: сбивается деревянный каркас, а на основание натягивается сетка с ячейкой не более 2 мм.
Еще один важный элемент — сушилка. Ее также можно изготовить своим руками. Для этого две железные бочки свариваются между собой. У каждой из них удаляется дно. Полученная конструкция крепится на станине и приводится в движение электродвигателем. Горячий воздух подается в рабочую емкость тепловой пушкой.
Изготовление гранулятора
Чтобы сделать гранулятор для пеллет своими руками, нужны определенные технические навыки. Если в хозяйстве нет достаточного количества материалов и деталей для изготовления прибора, его стоимость может получиться даже выше, чем у уже готовой модели.
Матрица
Гранулятор опилок должен иметь хорошую матрицу — от этого зависит продуктивность и эффективность аппарата. Матрица бывает цилиндрическая и плоска. Цилиндрическая представляет собой барабан с установленными внутри катками. Обрабатываемое сырье утрамбовывается и вдавливается в специальные каналы, где происходит формирование гранул. На выходе гранулы обрезаются ножами. Матрица плоская сделана в форме диска. Гранулы формируются схожим образом, но каналы, в которых происходит прессование, имеют форму цилиндра и длины в восемь — десять миллиметров. Обычно матрицу покупают уже готовой, но можно и изготовить ее самостоятельно.
Для изготовления нужен лист металла не менее 2 см толщиной, несколько шестеренок, вал, а также двигатель с редуктором. Оптимальная мощность двигателя — 15 кВт. Вал же может крепиться как горизонтально, так и вертикально.
Из листа металла вырезается ровный диск. Не рекомендуется использовать менее тонкий металл — матрица будет часто деформироваться. Размеры матрицы зависят от предполагаемых объемов перерабатываемого сырья. Для 350 кг в час диаметр матрицы должен быть около 50 см. Для меньшего объема подойдет диск, диаметров 20- 25 см. В центре диска пропиливается отверстие для крепления на редукторном валу, а также паз. Фрезой пропиливаются конусообразные отверстия для прессования гранул. Шестеренки или ролики выступают в роли катков. Они должны быть равны ширине матрицы, а крепятся к валу при помощи муфты.
Сборка гранулятора
Основа для гранулятора древесных пеллет варится из отреза трубы или же листа железа. Каркас аппарата должен состоять из двух частей: в первой гранулы формируются, а во второй части происходит их обрезание. Матрица устанавливается в первой части так, чтобы между ней и стенками корпуса оставался небольшой зазор. К нижней части корпуса крепится несколькими подшипниками и муфтой выходной редукторный вал. Для более простой очистки основу корпуса делают разъемной. Место соединения скрепляют болтами, а сам гранулятор прочно крепят к раме из уголков. Рядом с корпусом устанавливают двигатель, к которому подключают вал.
После того как все соединения проверены, делают пробный запуск гранулятора. Сделанный по данной схеме аппарат способен не только обеспечить отопительным материалом дом, площадью около 150 кв.м, но и позволит изготовить пеллеты для продажи.
Виды древесных пеллет
Заводы по производству пеллет изготавливают топливные гранулы двух типов: белые или светлые, и серые.
Светлые пеллеты
Производители отопительного материала относят пеллеты светлые к более качественному и экологически чистому сырью, не содержащему примесь золы или древесной коры. Чаще всего гранулированию подвергаются чистые опилки или очищенная от коры щепа, а также стружка. Еще одна особенность производства светлых пеллет — сушка сырья в специальных камерах, не имеющих контакта с твердым топливом. Объясняется это просто: во время работы сушильные аппараты, использующие обычные виды топлива, прогоняют опилки по рабочей камере вместе с продуктами горения, которые содержат и примеси золы. Это влияет на качество и зольность уже готовых гранул.
Пеллеты белые имеют высокую теплоотдачу и температуру сгорания, а цена на них значительно выше.
Серые пеллеты
Для пеллетного производства серых гранул подходит любое древесное сырье. Это может быть и горбыль, и кора, и бревна разных пород деревьев, и всевозможные отходы производства древесины. На цвет гранул влияет кора, а также процесс сушки. Некоторые производители добавляют к исходному материалу немного торфа или лузги подсолнечника, что удешевляет стоимость готового продукта. При сгорании гранул образуется немного кокса, а золоприемник котла приходится чистить гораздо чаще. Зольность серых гранул может доходить до одного процента.
Читайте также
nalugah.ru
Пеллеты своими руками - технология изготовления
Поиском новых источников топлива занимаются многие профильные НИИ различных стран. Параллельно с освоением нетрадиционных видов энергии в последнее время стали активно внедряться энергосберегающие технологии. Среди перспективных направлений в этой области — использование отходов индустрии и сельского хозяйства.
Пеллеты являются топливным продуктом, который стал отличным подспорьем в хозяйствах, где активно перерабатывается древесина и зерновые культуры.
Видео обзор самодельного гранулятора для изготовления пеллет
Сырьевая база
Изготовление пеллет своими руками основано на принципе формирования небольших цилиндрических гранул диаметром 5-10 см и длиной 5-6 см из следующих видов сырья:
- Торф
- Некондиционная древесина и отходы деревообработки (щепа, опилки, стружка)
- Отходы посевных культур (солома, лузга)
Пеллеты – топливо намного экологически чище, чем мазут или уголь. Выброс CO2 в атмосферу незначителен. Однако при использовании сырья для производства пеллет нужно обращать внимание на возможное присутствие в нем токсичных веществ.
Технология изготовления пеллет
Технологическая цепочка производства топливных гранул очень короткая. Изготовление пеллет своими руками сводится к двум основным этапам: подготовительный и производственный.
Подготовительный этап
Сюда включается:
- Сортировка сырья по видам
- Удаление из фракций инородных предметов
- Просеивание
- Сушка
Влажность массы должна быть в пределах 8-12 %. Этот показатель сохраняется для гранул, чтобы обеспечить им высокую теплотворность.
Готовую фракцию засыпают в приемный бункер, затем она попадает в пресс гранулятора. При спрессовывании масса нагревается до температуры 70-90 °С. Лигнин становится мягким и склеивает опилки. Под давлением формируются гранулы. Затем их охлаждают и хранят.
Оборудование
Хозяин, рискнувший делать пеллеты своими руками, окажется перед дилеммой: покупать или делать гранулятор. Первый вариант многие сразу забракуют по трем причинам:
- Высокие цены фирменного оборудования.
- Низкая рентабельность.
- Дефицитность товара.
Остается второе. Прежде, чем приступить к работе, необходимо определиться с выбором типа гранулятора. Он бывает с плоской матрицей и с кольцеобразной .
Гранулятор с плоской матрицей является менее затратным и проще в изготовлении. Рассмотрим его как предпочтительный вариант.
В основном весь процесс сводится к проведению сборочных операций, а отдельные узлы, из которых он состоит, покупают. Необходимо будет позаботиться о наличии следующих модулей:
- Электродвигатель
- Редуктор
- Исполнительный механизм
- Трансмиссия
Некоторые детали можно сделать самому.
Изготовление рамы
Сборка агрегата осуществляется при наличии прочной и жесткой платформы. Это сварная конструкция из профильного проката (швеллер, двутавр, уголок). Применяют электросварку, резку с помощью болгарки и дрель для сверловки крепежных отверстий. Если установка планируется мобильного типа, то в углах основания рамы варятся проушины для крепления колес.
Рабочий узел гранулятора
Исполнительный механизм представляет собой цилиндрическую емкость, состоящую из двух секций. В одной из них крепится диск-матрица и пара специальных шестеренок, сидящих на общем горизонтальном валу. Цилиндрическая емкость соединяется цепной трансмиссией с электродвигателем через редуктор.
Матрицу выкраивают из металлического листа толщиной 8-10 мм. Сквозные отверстия с конусообразной поверхностью и меньшим диаметром, равным диаметру пеллет, придают им форму цилиндра при сжатии массы сырья. Диск крепится на вертикальном валу редуктора с помощью шпоночного соединения. Создание необходимого рабочего давления для производства гранул обеспечивается червячной парой, установленной в цилиндре.
Как работает установка
Когда агрегат собран, изготовить пеллеты своими руками уже не представляется большой сложностью. В приемную часть цилиндра засыпается готовая масса. Попадая в рабочую зону, она продавливается через матричное отверстие.
В результате опилки приобретают размер и форму цилиндров необходимой плотности. Затем извлекаются из накопителя и отправляются на сушку.
Гранулятор такой конструкции с успехом может быть применен на небольших деревообрабатывающих и зерноочистительных предприятиях.
Видео интсрукция по изготовлению пеллет своими руками
boldproject.ru
Гранулятор для производства пеллет своими руками
Для топки дровяных печей и каминов, а также твердотопливных котлов в последние годы используют не только дрова, но и прессованные гранулы или брикеты из отходов деревообработки – пеллеты. В отличие от сжигания дров, наносящего вред экологии, использование пеллет решает проблему утилизации опила, щепы, коры древесины, и позволяет получить высокоэффективное и экологически чистое топливо.

Пеллеты своими руками
Брикеты промышленного производства имеют низкую остаточную влажность, хорошо разгораются, длительно поддерживают горение и не вызывают появления копоти, нагара и сажи, что особенно удобно при топке камина. Однако, цена их сопоставима со стоимостью сухих березовых дров. Поэтому при наличии больших объемов древесных отходов целесообразно сделать установку для изготовления пеллет своими руками.
Оборудование для производства пеллет
Пеллеты делают из опила, щепы, коры деревьев, а также из отходов сельскохозяйственной деятельности – жмыха, лузги, соломы. Сырье предварительно измельчают до размера частиц 3-5 см, просушивают в сушилках до влажности 15%, после чего помещают в дробилку мелкого дробления. Полученную массу с величиной фракции не более 2 мм загружают в пресс, где сырье прессуется. На выходе из пресса получаются гранулы с влажностью не более 12%, размер гранул зависит от конструкции оборудования. Гранулы собирают в мешки, укупоривают и используют для розжига и топки печей и котлов.
Таким образом, для самостоятельного изготовления пеллет понадобится такое оборудование:
- Дробилка или измельчитель древесины. Если в качестве сырья вы планируете использовать опилки или лузгу, этот этап производства можно пропустить. Для использования обрезков пиломатериалов, веток, коры, некондиционной доски дробление является обязательным этапом.
- Сушилка для сырья барабанного или аэродинамического типа. Сушилку можно изготовить своими руками из металлической бочки.
- Дробилка мелкого дробления, в которой происходит измельчение крупного сырья до состояния опилок.
- Пресс для пеллет или гранулятор с плоской или цилиндрической матрицей. Применение гранулятора исключает необходимость мелкого дробления сырья, так как в нем происходит одновременное перемалывание и прессование гранул.
Наиболее рациональным выходом для домашнего производства пеллет можно считать использование гранулятора с матрицей плоского типа – этот вид оборудования можно сделать своими руками, не прибегая к покупке дорогостоящих комплектующих. Измельчитель и дробилка в этом случае вам не понадобятся, а необходимость в сушильной камере зависит от влажности сырья.
Требования к сырью
Как уже говорилось, основным параметром, от которого зависит качество получаемыхпеллет – это влажность исходного сырья. Для изготовления гранул, хорошо удерживающих форму и горение, нужна измельченная древесина с влажностью 12-15%. Достичь такой влажности можно двумя путями: использовать опилки и щепу от высушенной древесины или досушивать сырье в сушильном барабане.
Из древесных отходов наиболее популярны опилки хвойных пород – благодаря высокому содержанию смолы и лигнина, гранулирование происходит быстрее, а готовые пеллеты лучше держат форму. В сырье не должно содержаться крупных включений, посторонних предметов, металлических деталей. Для этого его необходимо не только просушить, но и просеять.
Конструкция гранулятора для пеллет
Гранулятор – это емкость с установленной внутри плоской или цилиндрической матрицей. Цилиндрическая матрица – это перфорированный барабан, внутри которого вращаются катки. Уплотненная масса с помощью катков вдавливается в прессовальные каналы – отверстия в барабане, и после прессования гранул и выхода их с внешней стороны срезается ножами.

Схема гранулятора для пеллет
Гранулятор с плоской матрицей работает по тому же принципу, но матрица в нем представляет собой перфорированный диск, жестко закрепленный на валу. При вращении матрицы катки аналогичным образом спрессовывают сырье и вдавливают его в отверстия в диске. Прессовальные каналы имеют форму сужающийся к выходу конус, что позволяет максимально уплотнять гранулы. Диаметр отверстий обычно не превышает 8-10 мм.
Для установки по прессованию пеллет можно взять готовую матрицу и катки – их продают в качестве запчастей производители грануляторов для комбикорма, а можно изготовить самостоятельно из листового металла толщиной не менее 20 мм и подходящих шестерен, закрепленных на валу.
Приводом для гранулятора обычно служит электродвигатель мощностью не менее 15 кВт, и редуктор. Частота вращения матрицы должна находиться в пределах 60-100 оборотов в минуту. Вал, на котором закреплена плоская матрица, может быть ориентирован как вертикально, так и горизонтально, при этом необходимо предусмотреть емкость для загрузки сырья и выгрузки готовых гранул.
Видео — гранулятор для изготовления пеллет
Технология изготовления гранулятора
- Изготовление матрицы. Если вы решили изготовить матрицу самостоятельно, вам понадобится заготовка в виде диска толщиной не менее 20 мм. При меньшей толщине матрица быстро деформируется. Диаметр матрицы может быть любым, от него зависит производительность. Так, при диаметре 50 мм и двигателе 25-30 кВт вполне можно получать 300-350 кг пеллет в час. Для меньших объемов достаточно матрицы 25-30 см в диаметре. В центре диска сверлят отверстие по диаметру вала редуктора и выполняют паз для жесткой посадки. Отверстия для прессования и выхода гранул выполняют в виде конуса.
Матрица для гранулятора
- Шестерни или ролики для катков подбирают так, чтобы их ширина соответствовала рабочей зоне матрицы. Шестерни надевают на вал, который впоследствии будет закреплен перпендикулярно оси выходного вала редуктора с помощью муфты.
Шестерни для катков
- По размерам матрицы сваривают цилиндрический корпус гранулятора из трубы или листового металла. Корпус состоит из двух частей: в верхнюю загружают сырье, и после прохождения через систему роликов и матрицы готовые гранулы попадают в нижнюю часть корпуса, откуда по лотку высыпаются в подготовленную емкость.Матрица должна свободно вращаться внутри верхней части корпуса, при этом зазор должен быть минимальным.В нижней части корпуса делают отверстие для выхода готовыхпеллет, к нему приваривают лоток из трубы или листового металла.
Корпус для гранулятора
- Выходной вал редуктора закрепляют в нижней части корпуса гранулятора с помощью муфты и подшипников.
Выходной вал редуктора
- Для удобства чистки и обслуживания верхнюю и нижнюю часть корпуса выполняют разъемными с соединением на болты через приваренные ушки. Устанавливают матрицу и ролики в корпус.
Крепим верхнюю и нижнюю часть гранулятора для пеллет болтами
- Гранулятор устанавливают на раму, сваренную из уголка или швеллера, жестко закрепляя на ней. Крепят электродвигатель и подсоединяют его выходной вал к редуктору.
Устанавливаем гранулятор на раму сваренную из швеллера
- Раму и все детали гранулятора с внешней стороны окрашивают краской по металлу. Подключают двигатель в электросети и выполняют пробный запуск.
Процесс изготовления пеллет с помощью гранулятора
Гранулятор с матрицей плоского типа для изготовления пеллет, сделанный своими руками, способен решить проблему отопления дома площадью до 150 квадратных метров. Полученные гранулы можно использовать как для сжигания в печи или камине, так и для твердотопливных котлов. При этом вам не придется задумываться об утилизации отходов переработки древесины и сельскохозяйственного сырья.
stroyvopros.net
Производство пеллет
Основным сырьем для производства пеллет служат опилки и стружка. В данном случае речь идет лишь об отходах деревообрабатывающих предприятий, таких как лесопилки или строгальные цеха.
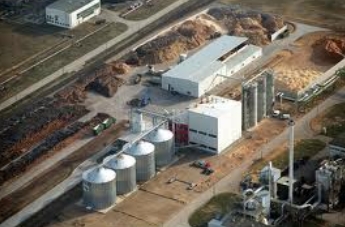
Полученные стружки в сухом состоянии прессуют под высоким давлением, при этом не добавляют клей или другие химические вяжущие элементы.
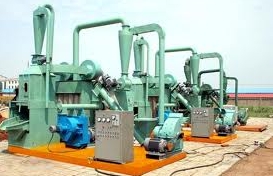
На качество конечного продукта (пеллеты) в большей степени влияет качество используемой стружки. Поэтому так важно тщательно выбирать и подготавливать опилки, а затем осуществлять постоянный контроль на протяжении всего производственного процесса вплоть до выхода готовых пеллет.
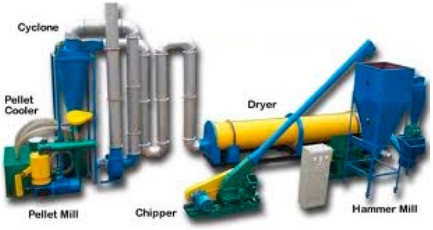
Производство 1 тонны пеллет
Для изготовления 1 тонны древесных пеллет в среднем необходимо 6-8 м3 стружки. Умение правильно гомогенизировать древесину – это целое искусство. Нужно это сделать так, чтобы потом пресс смог бесперебойно производить пеллеты с идентичными характеристиками. В первую очередь это касается размеров стружки и влажности древесины. Нужно иметь ввиду, что для разных видов древесины подходят разные характеристики прессовальной установки. Например, для древесины твердых пород (дуб, бук) используют большую силу прессования, чем при использовании хвойных или мягких пород.
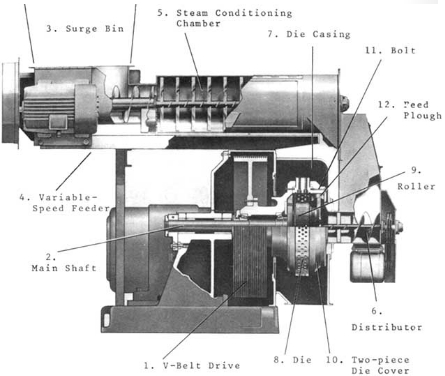
Для обеспечения постоянно высокого качества пеллет, обладающей регулированной остаточной влажностью, ее необходимо предварительно высушить в барабанной или ленточной сушилке.
После этого в большинстве случаев стружку отправляет в молотковую мельницу, предварительно прогнав через магнитный сепаратор и уловитель камней для извлечения тяжелых примесей. В мельнице ее измельчают до необходимых для пресса размеров (от 4х до 6ти мм). Для того, чтобы получить однородные размеры и формы стружки, ее большие частицы отсортировывают с помощью фильтровального сита.
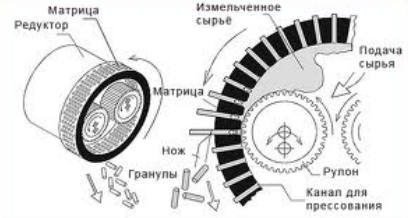
Основные составляющие элементы древесины – лигнин и целлюлоза. Под воздействием тепла, образованного при использовании пресса, лигнин становится клейким обволакивает целлюлозные волокна. Благодаря этому процесс производства пеллет происходит без добавления каких-либо посторонних вяжущих материалов. Для повышения противостояния пеллет истиранию часто используют добавки, которые облегчают процесс прессования. Это может быть крахмал или мука. Допускается их содержание до 2%, но в основном используют не более 0,5%.
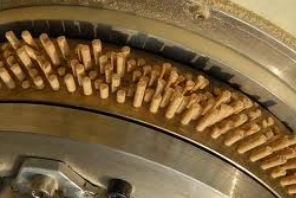
Гранулирование (производство) пеллет
Для качественного прессования нужно, чтобы в стружка была одинаковой температуры, и чтобы в ней был одинаковый процент влажности. Поэтому в накопительном резервуаре ведутся регулярные измерения этих показателей. Содержание воды допускается до 10-15%. При необходимости стружки можно увлажнить водой или паром. Для равномерного проникновения влаги в стружки перед прессованием их помещают в так называемую «ёмкость для дозревания» на 15-20 минут.
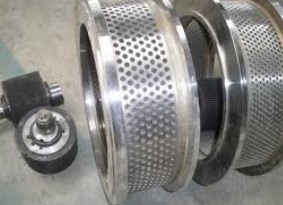
Так как для успешного производства пеллет по возможности одинаковый процент содержания воды и одинаковая температура стружки, в накопительной ёмкости постоянно проводятся измерения. Допускается содержание воды до 10-15%. В зависимости от содержания воды, стружки, при необходимости, увлажняют паром или водой. Чтобы добавленная вода равномерно проникала в стружки, они помещаются непосредственно перед прессованием на 15 – 20 минут «в ёмкость для дозревания».
pelleta.biz
Описание технологического процесса производства гриппер-пакетов
Экструзия представляет собой технологический процесс непрерывной работы, который заключается в продавливании материала, который обладает высокой вязкостью в жидком состоянии, через формующий инструмент (экструзионную головку, фильеру), с целью получения изделия с поперечным сечением нужной формы.
Метод экструзии в химической промышленности используют для нагрева, пластификации, гомогенизации, а также для придания исходному сырью нужной формы. У конечного продукта химический состав при этом такой же как и у исходного сырья. Таким образом, это позволяет получать продукт довольно стабильного качества, прибегая при этом к минимальному количеству настроек экструдера. Так можно объяснить относительную простоту машин, которые работают в химической промышленности.
Для переработки полимеров основным технологическим оборудованием в производстве изделий методом экструзии служат экструдеры.Экструдер представляет собой машину для формования пластичных материалов, с помощью придания им нужной формы и продавливания (экструзия) через профилирующий инструмент, которым служит экструзионная головка.
Экструдер включает в себя корпус с нагревательными элементами, также в него входит рабочий орган (шнека (винт Архимеда), диска, поршня), который размещается в корпусе, узел загрузки перерабатываемого материала. В состав этого оборудования также включен силовой привод, система задания и поддержания нужной температуры, а также другие контрольно-измерительные и регулирующие устройства.
В качестве дополнительного комплекта к базовому в состав линии могут быть включены также следующие элементы:1) автоматические загрузчики сырья;2) экструдеры, служащие для нанесения цветной полоски;3) коронаторы, необходимые для обработки полурукава перед печатью;4) вырубные устройства, предназначенные для перфорации пакетов;5) специальные ножи для формовки ziplock пакетов с контролем вскрытия;6) ножи для пайки пакетов любой конфигурации.
Технологический процесс экструзии продукции включает в себя последовательную пластикацию и перемещение материала вращающимся шнеком в зоне материального цилиндра. В процесс включены следующие зоны: зона питания, зона пластикации и зона дозирования расплава.
Деление шнека на так называемые зоны вполне условно, поскольку оно осуществляется, прежде всего, по технологическому признаку и указывает на то, какой операции в основном подвержен участок шнека. Цилиндр включает в себя также определенные длины зон обогрева, которая определяется путем расположения нагревателей на поверхности цилиндра и их температурой. Границы зон шнека и зон обогрева цилиндра не всегда могут совпадать. Для того, чтобы обеспечить успешное перемещение материала немаловажное значение уделяют условиям продвижения твердого материала из загрузочного бункера и на заполнение межвиткового пространства, которое расположено под воронкой бункера.
Загрузка сырья. Полимерный материал, предназначенный для экструзии, подается в бункер виде гранул, порошка или лент. Последний вид сырья свойственен обычно для переработки отходов промышленного производства пленок и проходит на специальных экструдерах, которые имеют в своем составе принудительные питатели-дозаторы, устанавливаемые в бункерах. Равномерное дозирование материала из бункера обеспечивает хорошее качество экструдата. Часто методом экструзии перерабатывают гранулированные пластики. Наиболее оптимальным вариантом питания экструдера является переработка полимера в виде гранул. Гранулы полимера не так сильно склонны к “зависанию” и практически не образуют пробок в бункере, чего нельзя сказать про порошок. Гранулы также гораздо легче пластифицировать и гомогенизировать.
Загрузка межвиткового пространства шнека под воронкой бункера происходит на отрезке длины шнека, равном (1 – 1,5)D. То, насколько сыпуч будет материал, зависит от его влажности. Таким образом, чем больше влажность, тем меньше сыпучесть. Поэтому гигроскопичные материалы необходимо сушить перед загрузкой в экструдер.
При длительной работе у экструдера может произойти как перегрев цилиндра под воронкой бункера, так и самого бункера. Гранулы тогда начнут слипаться, и их подача в шнек, соответственно, прекратится. Для того, чтобы предотвратить перегревание этой части цилиндра, обычно в нем делают специальные полости для циркуляции охлаждающей воды. Зона загрузки в этом случае – это единственная охлаждаемая зона современных экструдеров. Рассмотрим зоны подробнее.
1. Зона питания. Гранулы или порошок полимера, которые поступают из бункера, заполняют межвитковое пространство шнека зоны и уплотняются.
2. Зона пластикации и плавления. В этой зоне происходит расплавление полимера, который примыкает к поверхности цилиндра. Далее в тонком слое расплава полимера идет возникновение интенсивных сдвиговых деформаций. Материал в связи с этим пластифицируется. Это в итоге приводит к интенсивному смесительному эффекту.
Давление P расплава поднимается в основном на границе первой и второй зоны. Пробка из спрессованного материала, образующаяся на этой границе, по сути, скользит по шнеку: в первой зоне это твердый материал, а во второй зоне – материал плавящийся. Наличие пробки из спрессованного материала влияет напрямую на повышение давления расплава. Расход давления, запасенного на выходе из цилиндра, идет на преодоление сопротивления сеток, на течение расплава в каналах головки и для формования экструдируемого профиля.
*3. Зона дозирования. *Расплавленная полимерная масса продолжает подвергаться гомогенизации. Она все же еще не является однофазной и состоит из расплавленных и твердых частиц. В конце третьей зоны пластик полностью гомогенизируется. Он готов к продавливанию через чистящие сетки и для формующей головки. Затем происходит прессование жидкого пластика. Он через отверстия вытягивается из формы с помощью волочильного устройства. Линия для производства пакетов с замком zip-lock предназначается для производства всех типов и размеров пакетов.
Замок формируется с помощью специальных фильер в процессе выдува рукава. Длина пакета ограничена диаметром фильерной головы. Материал после процесса формирования замка охлаждается, собирается и после проходит в цех готовой продукции. Изготовление пакета с приварным замком в несколько этапов позволяет получать упаковку с застежкой не только из полиэтилена, но также из многослойных пленок и полипропилена. Это позволяет использовать zip-lock для пищевых продуктов, для которых характерны специальные условия хранения, например, ароматных, жиросодержащих и других. К этой категории относятся также металлизированные пакеты zip-lock.
Выбор размещения оборудования цеха по производству гриппер-пакетов
Все оборудование, которое используется для производства полиэтиленовых пакетов, полностью автоматизировано. Оно также оснащено микропроцессорной системой и содержит жидкокристалический дисплей, позволяющий следить за процессом. Система служит для контроля всех процессов работы оборудования. Здесь можно задать нужный размер получаемой продукции, а также система ведет наблюдение за горячей сварку и резкой, позволяет укладывать готовую продукцию определенного количества под пресс и выполняет другие функции.
Для производства полиэтиленовых пакетов, которые будут выполняться в малых и средних объемах, оптимальной является автоматическая пакетоделательная машина. Она обладает довольно высокой производительностью, и позволяет изготавливать большое разнообразие пакетов по низким ценам. Пакетоделательная машина такого вида полностью комплектована всевозможными дополнительными опциями, что делает её удобной и позволяет получать высокое качество у готовой продукции. Микропроцессорный контроль позволяет быстро и точно установить нужный размер будущего пакета. Машина изготавливается по современным мировым стандартам и обеспечивает довольно высокую точность резки, хорошую, прочную спайку материала, удобную систему складывания пакетов.
book.calculate.ru