Из чего и какими способами делают цемент. Производство цемента
Из чего и как делают цемент: его состав
Цемент входит в число основных строительных материалов. Он используется при создании связующих строительных растворов, цемент используют при изготовлении бетонных и железобетонных изделий. От качества данного материала зависит, насколько прочное и долговечное будет здание, или железобетонная конструкция.
История цемента началась в Англии, где в 1824 году был зарегистрирован патент на его изобретение. В то время для изготовления цемента использовалась известковая пыль, смешанная с глиной. Полученная смесь подвергалась воздействию высокой температуры, при которой она спекалась.
Обожжённый полуфабрикат цемента называется клинкер. Цементом он становится после перемалывания клинкера до порошкообразного состояния.
В строительстве используется основное свойство цемента – при смешивании с водой он постепенно твердеет, а затем превращается в прочный камень. Характерную для готового изделия прочность материал может приобрести даже в воздушной среде, если присутствует избыточная влажность.
Сырьё для производства
Сегодня процесс изготовления цемента изменился. Изготовляют его несколькими способами, да и компоненты, входящие в его состав, тоже отличаются от использовавшихся две сотни лет назад.
Чтобы было понятно, из чего делают цемент и как происходит его производство, необходимо знать, какие виды сырья используют сегодня производители этого важного строительного материала.
Так как сырьём для производства цемента гост31108 2003, гост 30515 2013 служат естественные породы, то и предприятия, занимающиеся его изготовления, чаще всего размещают поблизости от мест добычи этих пород.
Все ископаемые, из которых делается цемент, делятся на два вида:
- Карбонатные ископаемые, отличающиеся характеристиками и особенностью структуры. Именно структура породы обеспечивает эффективное её взаимодействие с остальными ингредиентами состава продукта.
- Глинистые и горные породы, имеющие осадочное происхождение. Имея минеральную основу, при увлажнении они приобретают пластичность и увеличиваются в объёме. Так как для данного вида сырья характерна вязкость, то их можно использовать, производя цемент сухим способом.
Теперь следует назвать конкретно, какие ископаемые относятся к каждому из видов сырья, используемых при производстве цемента.
К карбонатным породам относят следующие виды природного сырья:
- мел, представляющий разновидность известняка. Обладает способностью легко измельчаться;

Мел
- мергелистый известняк, в природе встречается как в рыхлом, так и в твёрдом состоянии. В породе могут содержаться примеси глины, поэтому данный вид известняка считается сырьём переходным, обладающим свойствами, характерными и для известняков, и для глины;
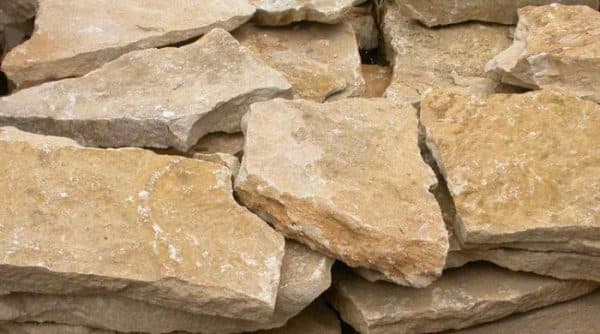
Мергелистый известняк
- известняки — ракушечники, не имеющие включений кремния. Порода имеет пористую, легко разрушающуюся при сжатии структуру;
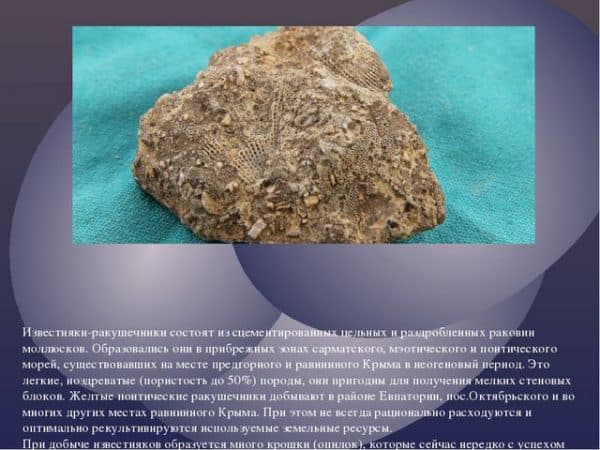
Известняки — ракушечники
- доломитовые породы и другие ископаемые осадочного происхождения. Они содержат карбонаты, придающие породе ценные свойства.

Доломит
Глинистые породы включают следующие виды ископаемых:
- глина с минеральными включениями, набухающими при контакте с водой;

Глина
- суглинки, содержащие повышенную концентрацию частиц песка;
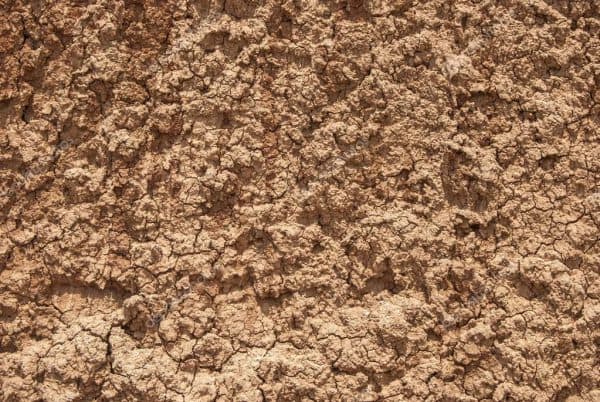
Суглинки
- сланцы, имеющие глинистую основу. Данное сырьё относят к горным породам, повышенной прочности. При механическом воздействии разделяется на пластинчатые пластины. Характеризуется стабильным составом и низким содержанием влаги;
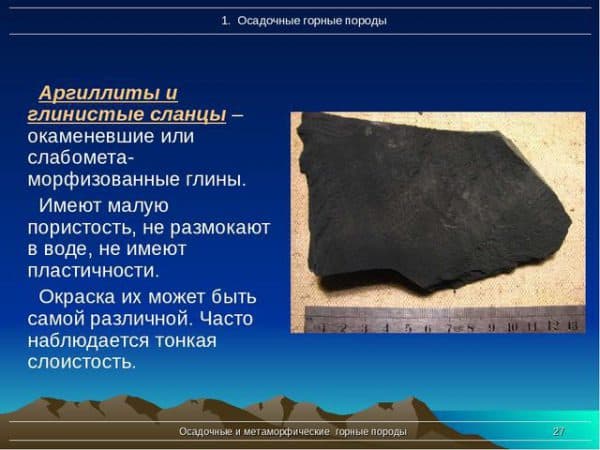
- лесс, пористая порода, с включениями частиц кварца и силиката.
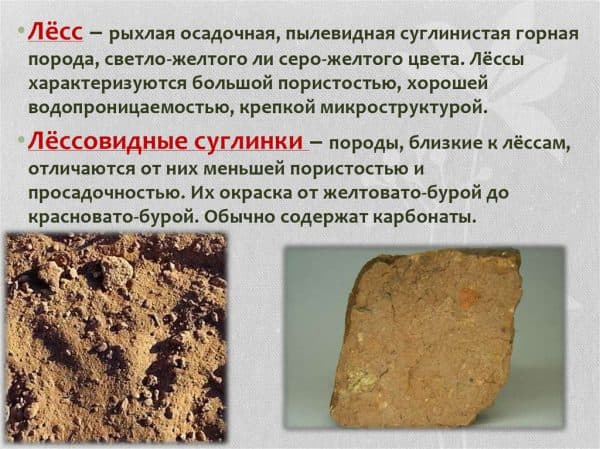
Лесс
Кроме данных видов сырья, при изготовлении цемента используют некоторые виды производственных отходов. Для улучшения качества в его состав добавляют добавки, предусмотренные технологическим процессом: глинозём и кремнезём, плавиковый шпат и апатиты.
Применение песка просто необходимо при проведении самых разных ремонтных и строительных работ. Тут все о применении карьерного песка.
При проведении отделочных работ на кухне, в ванной или в любом другом помещении необходимо знать время высыхания плиточного клея. Здесь можно узнать, сколько сохнет плиточный клей.
В настоящее время декоративная штукатурка по праву является самым популярным и прогрессивным методом отделки. Перейдя по ссылке ознакомитесь с самостоятельным ее приготовлением.
Все добавки, называемые пластификаторами, также природного происхождения. Они влияют в лучшую сторону на следующие качества цемента:
- увеличивают стойкость к изменениям температуры;
- усиливают прочность;
- подвижность и эластичность продукта;
- уменьшает проникновение воды в готовое изделие.
В зависимости от свойств, добавленных в состав цемента пластификаторов, его раствор будет застывать быстрее, или же медленнее.
Состав
Часть людей работающих в сфере строительства не знают, из чего делается цемент.
Состав цемента может быть различным в зависимости от марки и предназначения.
Однако вне зависимости от вида цемента, то есть рецепта, использованного при его производстве, основой для него служат два компонента – известняк с добавлением глины.

Глина
Количество известняка в три раза превышает количество глины. Такие пропорции необходимы для получения качественного клинкера, являющегося полуфабрикатом для производства цемента.

Известняк
Теперь можно назвать основные компоненты состава, чтобы каждому было ясно, из чего делают цемент:
- клинкер, основа конечной продукции, определяющая её характеристики прочности. Используется в виде гранул диаметром до 60 мм. Его термообработка выполняется при температуре, доходящей до 1500°. При плавлении клинкера образуется масса, для которой характерно высокое содержание кремнезёма и кальциевого диоксида;
- данные компоненты влияют на эксплуатационные характеристики конечного продукта. Перед обжигом гранулы клинкера измельчаются до пылеобразного состояния;
- гипс, определяющий скорость затвердевания цемента. В базовых рецептах предусмотрено добавление в состав чистого гипса до 6 % от общего количества компонентов;

Гипс
- специальные добавки (пластификаторы, морозостойкие присадки, жидкое мыло и т.д.), усиливающие свойства, уже имеющиеся у продукции, или же придающие ей специальные характеристики, способные расширить область применения цемента.
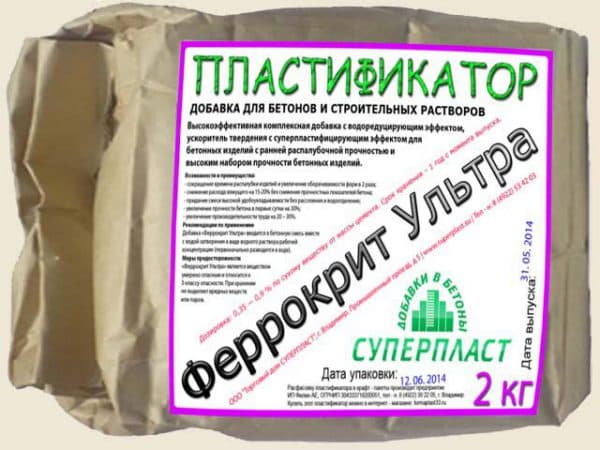
Пластификатор
Производство
Изготовление материала выполняется в определённом порядке, поэтапно. В технологии его производства предусмотрены следующие операции:
- Ингредиенты, предназначенные для изготовления клинкера, предварительно смешиваются. Обязательно необходимо точное соблюдение пропорций состава – 25 % глины и 75% известняка.
- Полученный состав обжигается при высокой температуре. При высокотемпературном обжиге глина и известь соединяются, образуя клинкер.
- Готовый продукт измельчается шаровыми мельницами, состоящими из барабанов, расположенных в горизонтальном положении, внутри которых размещены стальные шары. Помещённый в них клинкер размельчается до состояния порошка.
- Чем мельче полученные фракции цемента, тем лучшие эксплуатационные характеристики он будет иметь.
Существует несколько методов изготовления данного строительного материала. Их выбор обусловлен многими факторами, основными из которых является специфика имеющегося на предприятии оборудования и спрос на определённые марки цемента.
Разработанные технологии имеют отличие в способах подготовки сырья, используемого при производстве состава. Порядок его изготовления остаётся прежним.
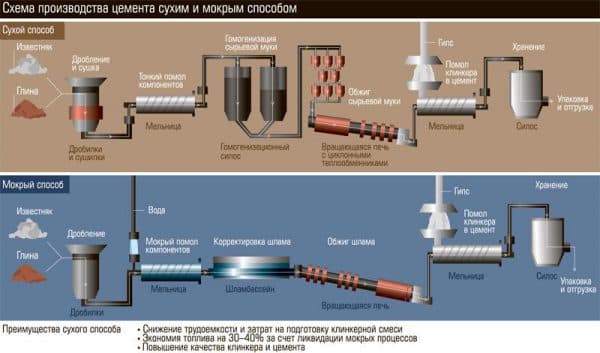
Производство
Разработаны следующие методы:
- Мокрая технология, предусматривающая замену извести мелом. В процессе смешивания компонентов состава происходит измельчение их в шаровой мельнице. Это процесс выполняется с добавлением воды. В результате образуется шихта, имеющая концентрацию влаги до 50%.
- Полученный материал затем обжигается в печи. После обжига он уже становится клинкером. Затем его измельчают.
- Сухая технология значительно уменьшает себестоимость производства, так как она объединяет несколько технологических операций в единый процесс. При использовании данной технологии компоненты, поступающие в шаровую мельницу, одновременно размалываются и сушатся.
- Для сушки используется воздействие горячих газов. Готовая шихтная масса имеет консистенцию порошка.
- Комбинированная технология объединяет особенности вышеописанных способов производства. В зависимости от оборудования, используемого на предприятии, может быть получен полусухой состав, имеющий влажность до 18%.
- Во втором варианте первоначально подготавливается сухая смесь, затем увлажнённая до 14 %. В обоих вариантах подготовленный состав затем отжигается и перемалывается.
Подробнее о производстве цемента смотрите на видео:
Классификация
Существует много разновидностей и различных марок данного строительного материала. Различают их по основному составу и добавкам, придающим каждому виду особые свойства.
Среди основных типов выделяют:
- портландцемент, с которого начиналось производство популярного в строительстве продукта. Для изготовления связующих растворов его не используют. Он применяется для создания бетонных изделий высокой прочности, штукатурке и отделочных работах;
- часто используют при возведении фундаментов. Для этого необходимо знать, как разводить цемент с песком;

Портландцемент
- шлаковый цемент, при изготовлении которого используется доменный шлак и активные присадки. Используется для изготовления бетона и строительных растворов;
- глинозёмистый цемент, отличается устойчивостью к воздействию влаги, быстрым затвердеванием;
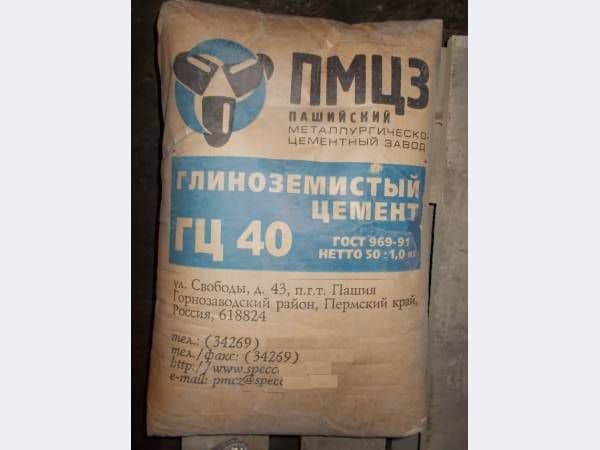
Глиноземистый
- кислотоупорный цемент, в котором используется кварцевый песок и кремнефтористый натрий. Материал устойчив к воздействию кислот, но недолговечен.
Приобретая любой из видов цемента, следует знать, что его состав активно взаимодействует с окружающей средой, при долгом хранении теряя свою прочность.
Даже если он хранится в сухом помещении, то спустя несколько месяцев его марка изменится в меньшую сторону. Поэтому, при его приобретении, следует обращать внимание на дату изготовления. Так же можете ознакомиться с нашей статьёй о технических характеристиках цемента м400.
strmaterials.com
Как изготовить цемент: технология, структура, состав
Дата: 30 января 2017
Просмотров: 1623
Коментариев: 0
Технология изготовления цемента

Сложно найти человека, который не знаком с таким востребованным строительным материалом, как цемент. Ни одна стадия возведения объекта, начиная с закладки фундамента и заканчивая отделочными работами, не обходится без применения этого вяжущего вещества. При промышленном и гражданском строительстве используются кирпич, фундаментные блоки, стеновые панели. Но как добиться того, чтобы эти составляющие образовали единую конструкцию, прочную, долговечную. Вот тут на помощь приходит цемент. На сегодняшний день – это единственное вещество, способное создать из любого набора материалов монолитное изделие, которое на протяжении десятков и сотен лет только увеличивает прочностные характеристики.
Но какой процент людей задавался вопросом, из чего получают цемент, какие компоненты делают этот материал незаменимым? Наверно, немногие. Попробуем вкратце разобраться с этим вопросом, опишем, как происходит изготовление цемента.
Общие сведения
Цемент относится к неорганическим веществам. Вяжущие свойства он приобретает при взаимодействии с водой или водными растворами солей. Отметим, что это единственный вяжущий материал, который повышает прочностные характеристики при влажных условиях. В этом его отличие от гипса, который твердеет на воздухе.

Сегодня большая часть многоэтажных зданий выстроена именно благодаря бетонным конструкциям и заливке цемента
Так, что же такое – цемент? Это измельченное минеральное сырье со специальными модифицирующими добавками. В зависимости от наполнителя, выделим следующие виды:
- Портландцемент. Наиболее широко распространенный вид, включающий до 80% силиката кальция. Сфера применения не ограничена. Используется как при основных работах, так и при отделочных, поскольку возможно добавление красителей, повышающих декоративные свойства.
- Глиноземистый. Отличительная черта – ускоренное твердение, что дает возможность применять на объектах, требующих срочной реставрации (ликвидация разрушений после аварий, пожаров, затоплений).
- Магнезиальный. Главный элемент – оксид магния, добавляющий прочность, повышающий адгезионные свойства по отношению к древесине. К недостаткам относится повышенная вероятность коррозии, сужающая сферу применения.
- Кислотоупорный. В качестве наполнителя выступает гидросиликат натрия, который затворяется жидким стеклом. Служит основой для кислотостойких бетонов, растворов. Актуален при обустройстве объектов химической отрасли.
Структура
Изготовление цемента осуществляется на базе следующих компонентов:
- клинкера, основа которого – глина и известняк. Клинкер определяет прочность материала, производится при обжиге глиносодержащего и известнякового сырья. При нагреве плавится, образуя гранулированный состав с повышенной концентрацией кремнезёма, измельчается, повторно подвергается обжигу;

Цемент изготавливают на заводах, в промышленных масштабах
- гипса, влияющего на продолжительность процесса твердения цементного состава. Вводится, согласно рецептуре, как камни или готовый порошок, концентрация которого не превышает 5%;
- модифицирующих добавок, расширяющих область использования материала за счет приобретения специальных эксплуатационных свойств.
Используемое сырье
Массовое производство материала осуществляется на специализированных предприятиях. Можно попытаться изготовить цемент самостоятельно, так сказать, для личных нужд. Но работа эта неблагодарная, требующая специальных знаний технологии производства, точного соблюдения пропорций, чего сложно добиться в домашних условиях.
Лучше воспользоваться продуктом, изготовленным под наблюдением специалистов на высокопроизводительном оборудовании. Для изготовления цементного состава необходимы следующие специальные компоненты:
- природное карбонатное сырье (известняк-ракушечник, известковый туф, мел). Доля в суммарном объеме продукта составляет 74-82%. Структура исходного материала определяет степень эффективности взаимодействия используемых ингредиентов при обжиге;
- глинистые породы (глинистый сланец, суглинки, лесс). Процентное содержание глиносодержащей породы составляет 26-18%.

Для производства цемента применяют:смесь из известняка и глины – клинкер
Специальные добавки
При изготовлении применяются и другие компоненты (соли, окислы кальция, магния, фосфора), но их концентрация незначительна. Добавки вносятся для получения каких-либо определенных свойств – жаропрочности, кислотоустойчивости и пр. Чтобы получить возможность регулировать время схватывания цементного раствора, при изготовлении добавляют гипс.
Изготавливают материал с обязательным введением специальных добавок, повышающих эксплуатационные характеристики состава. Технология производства предусматривает применение следующих корректирующих компонентов:
- Добавок на базе ископаемого сырья с высокой концентрацией глинозема.
- Улучшителей, содержащих кремнезем.
- Ингредиентов, полученных из глинистых пород.
- Компонентов, полученных из апатитов и плавикового шпата.
Введение пластификаторов, предусмотренных спецификой технологического процесса, позволяет обеспечить следующие эксплуатационные характеристики состава:
- способность оказывать сопротивление проникновению воды в массив;
- сокращение продолжительности затвердевания состава;
- повышенную прочность монолитного массива;
- устойчивость к длительным, многократным стадиям замораживания с последующим оттаиванием;
- стойкость к влиянию жидких, газообразных агрессивных сред;

При замешивании раствора своими руками необходимо строго соблюдать пропорции компонентов и позаботиться об их качестве
- улучшенную адгезию с арматурой, надежно защищенной бетонным массивом от отрицательного воздействия коррозии;
- вязкость и подвижность бетонного раствора, облегчающие выполнение кладки, заливку монолитных конструкций за счет эластичности смеси.
Особенности состава
Независимо от того, по какой технологии изготавливают цемент, клинкер включает следующие ингредиенты:
- Силикаты кальция, играющие ключевую роль для обеспечения прочностных характеристик при изготовлении цементных составов. Согласно рецептуре, применяют в составе клинкера алит, доля которого составляет 50-70%, или белит с уменьшенной до 30% концентрацией.
- Кальциевые алюминаты, быстро реагирующие с водой, влияющие на процесс твердения цементного состава. Их количество составляет от 5 до 10% общего объема клинкера.
- Ферритные компоненты, в виде кальциевого алюмоферрита, вводимого в объеме 10-15% от общей массы.
- Различные соединения кальциевых оксидов, сульфатов щелочного типа, концентрация которых незначительна.
Концентрация компонентов зависит от специфики технологического процесса, вида производимого материала. Основными составляющими при изготовлении цемента являются известняковые, глинистые материалы, определяющие качество клинкера, применяемого в процессе производства.

Наиболее сложно сделать цемент для кладки камня и штукатурных работ
Специфика производства
Изготовление цемента предусматривает выполнение следующих производственных стадий:
- добычу сырья, содержащего гипс, глину, известняк;
- дробление добытого известняка, обеспечение требуемой влажности полученного продукта;
- измельчение известняковой массы, смешивание с глиной. Соотношение известняка и глины изменяется в зависимости от особенностей используемого сырья, ориентировочно соответствует пропорции 3:1. Результат – получение комбинированного, сухого или мокрого шлама;
- обжиг сырьевой массы при температуре до 1,5 тысячи градусов Цельсия, при котором происходит спекание шлама. Состав при этом превращается в гранулированную фракцию, называемую клинкером;
- измельчение до порошкообразной фракции клинкера с использованием специальных мельниц;
- дозирование и смешивание ингредиентов согласно марке будущего цемента. Процесс смешивания предусматривает введение до 5% гипса и специальных минеральных добавок.
Нюансы технологии
В зависимости от особенностей используемого сырья, изготавливают цементный состав по проверенным технологиям, которые предусматривают различные способы подготовки исходных компонентов.
Применяемый шлам может быть получен следующим образом:
- Сухим способом, значительно снижающим затраты на изготовление цемента. Особенностью сухого метода является сокращенный цикл производства, объединяющий ряд технологических стадий. Процесс измельчения и сушки ингредиентов осуществляется одновременно в специальной мельнице, куда подаются нагретые до высокой температуры газы. Полученная шихтовая фракция представляет порошкообразный состав необходимой влажности.
- По мокрой технологии, согласно которой мел применяется вместо извести. Мел смешивается с предусмотренными рецептурой компонентами, измельчается во влажной среде. Результат – получение шихты, влажность которой составляет до 50%. Шихтовая масса подвергается обжигу с последующим измельчением полученного клинкера.
- По комбинированной технологии, объединяющей элементы сухого и мокрого метода. Процесс предусматривает как увлажнение сухого состава, последующее гранулирование, отжиг, так и высушивание полусухого шихтового состава, произведенного мокрым способом.
Производственные предприятия осуществляют изготовление цемента с учетом особенностей имеющегося оборудования, близости к месту добычи сырья. При этом учитываются потребности на конкретные марки продукции.
Итоги
Материал статьи дает специальную информацию, как и из чего, осуществляется изготовление цемента, какие сырьевые материалы, технологические решения используют при изготовлении. Все тонкости знают профессионалы, работающие на предприятиях, производящих цемент.
pobetony.ru
Состав цемента. Из чего делают цемент :: SYL.ru
Если судить по масштабам применения в строительстве растворов и бетонов на основе минеральных вяжущих, кажется, что история искусственных камней на основе цементов насчитывает долгие века. Но по-настоящему отработанная технология производства и оптимальный состав цемента стали известны менее двух веков назад.
Изобретение камня
Камни домов доисторического времени скреплялись в стене с помощью глины, но сохраниться без обжига они не могли, и самые древние постройки, дошедшие до нас, были возведены с применением известкового раствора. Обожжённый и размолотый известняк (оксид кальция – Ca(OH)₂) после затворения водой твердеет, поглощая из воздуха углекислый газ, а потом опять превращается в камень. Основной недостаток известкового вяжущего – низкая влагостойкость, поэтому сегодня он применяется больше при изготовлении силикатного кирпича.
Другой вид воздушного минерального вяжущего (то есть набирающего прочность на воздухе) – гипс. Он получается при тепловой обработке и последующем размоле природного гипсового камня (CaSO4-2h3O) или природного ангидрида (CaSCu). Гипсовое вяжущее имеет огромную историю применения с древнейшего времени до сегодняшних дней. Самые яркие примеры – роскошные лепные и скульптурные украшения, листовые материалы (ГВЛ, ГКЛ) для сухих методов строительства и отделки.
Гидравлические вяжущие вещества
Область применения воздушных вяжущих ограничена теми местами, где готовые конструкции не подвергаются воздействию влаги, в противном случае приходится применять гидрофобизирующие (водоотталкивающие) добавки или проводить гидроизоляционные мероприятия, поэтому применение гидравлических вяжущих более удобно и распространено шире.
К ним относятся вещества, образующие гидратные (молекула воды входит в кристаллическую решетку как составная часть) соединения, когда превращение в камневидное тело и дальнейший набор прочности могут происходить во влажной среде, а воздействие воды в ходе эксплуатации конструкций не приводит к их разрушению.
Растворы и бетоны для выполнения водостойких конструкций приготавливают на основе гидравлической извести (из осадочных известковых пород особого состава – мергелей) и портландцемента, причем именно последний придает монолитным и сборным элементам здания необходимую прочность, а известковые растворы применяются там, где нагрузки минимальны.
История цемента
Попытки преодолеть низкую водостойкость известковых и гипсовых составов предпринимались с древнейших времен. Цемент (caementum в переводе с латыни — дробленый, битый камень) появился путем добавления в известь различных минеральных веществ, обладавших гидрофобными свойствами. Для этого использовали размельченные остатки кирпичей из обожжённой глины, различные вулканические породы. Так, в состав цемента, который применялся строителями Древнего Рима, входили пуццоланы – отложения пепла знаменитого вулкана Везувия.
Эксперименты продолжались долгие века, пока потребность в большом количестве прочного и недорогого вяжущего вещества не заставила строителей выработать оптимальную технологию по его производству. Решающий вклад в такие исследования внесли русский военный техник Егор Челиев, издавший книгу о цементе для подводных работ (1825), и каменщик из английского Лидса Джон Аспдин, получивший патент на портландцемент (1824). Это название происходит от английского острова Портленд, расположенного в проливе Ла-Манш и состоящего из известковых пород. Камни из карьера, находящегося на этом острове, считались самым престижным строительным материалом в Англии. Полученный Аспдином искусственный камень был очень похож на него цветом и прочностью.
Интересно, что технология Челиева более соответствует тому, что теперь называется портландцементом, а цемент Аспдина изготавливался без принятого сейчас спекания исходного сырья.
Технология производства
Цементное вяжущее у разных производителей может отличатся исходным сырьем, но основные технологические операции идентичны. Первая стадия – подготовка исходного минерального сырья, т. е. несколько стадий размельчения известковых камней и глины, смешивание этих компонентов в нужных пропорциях. Из чего состоит цемент? Обычно это 3 весовых части известняка и 1 часть глины. Иногда используется осадочная горная порода – мергель, где данные компоненты содержатся в нужной пропорции.
"Сухой" и "мокрый" способ
Существует два способа получения нужного состояния смеси: "сухой" и "мокрый". Если влажность компонентов высокая, глина и мягкий известняк (мел) растворяются в воде, затем из этой суспензии, называемой сырьевым шламом, вода сильным нагревом (испарением) удаляется. Получается равномерная тонкоизмельченная смесь. Более экономичный способ – "сухой", где нет стадии доведения шлама до кипения, а смесь измельчается механическим способом.
Далее во вращающихся печах – цилиндрах диаметром около 5 м, длиной около 200 м, имеющих уклон для перемещения сырьевой массы в процессе обжига, происходит образование клинкера – окатанных гранул, появляющихся в процессе спекания смеси при температуре 1450 ⁰С в результате физических и химических взаимодействий.
Клинкер охлаждается и выдерживается до двух недель перед окончательной операцией – совместным измельчением с определенным количеством гипса, который добавляется для замедления процесса схватывания. Здесь окончательно формируется состав цемента, на этой же стадии вводятся различные минеральные добавки, придающие вяжущему нужные специфические свойства.
Химическая основа
Необходимые свойства самого популярного вяжущего определяет химический состав цемента. В результате технологической обработки сырья клинкер становится соединением различных химических веществ в виде четырех основных минералов:
- Алит – трехкальциевый силикат – составляет большую часть клинкера – 50-60%. Присутствие в молекулярной решетке ионов марганца, алюминия и железаопределяет прочность готовой растворной или бетонной смеси, набираемой в течении первых 28 суток.
- Белит – двухкальциевый силикат – составляет 15-30%, и он – основа прочности, набираемой конструкцией в более поздние сроки.
- Алюминатная фаза – трехкальциевый алюминат – 5-10%. Быстрая реакция алюмината с водой и возможное слишком быстрое схватывание требуют введения гипса, замедляющего этот процесс.
- Ферритная фаза – четырехкальциевый алюмоферрит – 5-15 %
Меняя процентный состав этих фаз, вводя дополнительные компоненты, можно производить цемент, состав и свойства которого будут наилучшим образом соответствовать конкретной ситуации в ходе строительства.
Виды цемента
Шлакопортландцемент получается при добавлении к портландцементному клинкеру гранулированного шлака – побочного продукта выплавки чугуна в доменных печах. Применение шлака снижает стоимость, а состав цемента, произведенного по такой технологии, придает конструкциям, выполненным на его основе, повышенную устойчивость к воздействию воды с насыщенным минеральным составом, например, морской.
Быстротвердеющий – это цемент с преобладанием в клинкере алита и алюминатной фазы, отличается особо тонким помолом – всё это ускоряет набор прочности.
Сульфатостойкий портландцемент применяется для гидросооружений, подводные части которых подвергаются постоянному воздействию веществ, вызывающих сульфатную коррозию. Из чего состоит цемент, предназначенный для таких ответственных конструкций? В клинкерном сырье до минимума сведено присутствие трехкальциевого алюмината и белита.
Портландцемент с пониженным тепловыделением при наборе прочности необходим для изготовления конструкций большой массы и объема, когда тепло, выделяемое экзотермической реакцией твердения, может привести к образованию трещин. Состав такого цемента похож на сульфатостойкий.
Белый цемент
Изделия, выполненные с использованием белого цемента, обладают повышенными эстетическими качествами. Присутствие в исходном сырье окиси железа и окиси марганца придает готовому порошку характерный серо-зеленый цвет, соответственно, состав белого цемента предполагает минимальное присутствие таких солей и использование для исходного сырья светлых, каолиновых сортов глины.
Существует еще много видов цементного вяжущего, обладающего специальными качествами: гидрофобный, глинозёмистый, водонепроницаемый расширяющийся, напрягающий, пластифицированный, песчанистый и т. д.
Состав и прочность
Важнейшим показателем качества цемента является прочность изделий, изготовленных на его основе. ГОСТом установлены необходимые показатели, которые обозначаются особой маркировкой. Цифра означает предел прочности на изгиб и сжатие при лабораторных испытаниях стандартных образцов, на устойчивость к нагрузкам которых влияет и состав цемента. М400 означает, что образцы выдержали нагрузку в 400 кг/см² (или 40 Мпа).
Исследования показывают, что минеральный состав исходного сырья – важнейший фактор, влияющий на прочность цементных растворов и бетонов. Правильный подбор компонентов позволяет найти нужную пропорцию между скоростью набора прочности и конечной величиной устойчивости к нагрузкам, которая только увеличивается с течением времени. Состав цемента М500 позволяет создавать балки и плиты, способные выдерживать колоссальные нагрузки.
Сегодня в мире производится огромное количество цемента самого различного качества. Выбор сырья для него часто определяется экономическими факторами, и при правильном отношении к строительному процессу следует знать, из чего состоит цемент, который будет использоваться, чтобы сделать правильный выбор и быть уверенным в прочности и долговечности будущего дома.
www.syl.ru
Цементные заводы России - 30 предприятий
История производства цемента в России начинается с заявки на патентование нового вяжущего вещества Егором Челиевым в 1825 году. Хотя, практические работы с применением цементных смесей велись в 1813 году при восстановлении Москвы на работах по укреплению берегов Москва-реки и строительстве Кремля. Но волею судеб автором портландцемента считается англичанин Дж. Аспдин (Joseph Aspdin), запатентовавший технологию в 1824 году. Начиная с 1836 года, Россия постоянно наращивала производство цемента, которое к 1913 году достигло 1,78 млн. тонн в год. Большинство предприятий располагалось на юге России, где месторождения известняка или мергеля выходят на поверхность (как говорят ученые — южнее границы последнего ледникового периода).
Виды продукции
Все виды продукции являются производными от портландцемента. Минеральные добавки и вид основного сырья придают цементу различные свойства.
- Белый цемент — основа для отделочных смесей, цветного цемента марки ЦЦ. Применяется для строительства архитектурных объектов без последующей отделки.
- Быстротвердеющий цемент — применяется в строительстве быстровозводимых и заливных строений.
- Водонепроницаемый безусадочный цемент — применяется в строительстве для формирования гидроизоляции и заделки швов гидросооружений.
- Гидрофобный цемент — присадки снижают водопоглощающие свойства, что увеличивает срок хранения.
- Глиноземистый цемент — добавки глинозема (аллюминат и бокситы) увеличивают скорость отверждения с выделением большого количества тепла. Актуально для зимнего строительства. При добавлении гипса получается расширяющийся цемент марки РЦ.
- Напрягающий цемент — применяется для изготовления железобетонных изделий.
- Пуццолановый цемент — добавление тонкоизмельчённого активного кремнезёма увеличивает время схватывания и понижает тепловыделение. Актуально при возведении объектов с большими сечениями и объемами.
- Сульфатостойкий цемент — характеризуется жесткими ограничениями по содержанию трёхкальциевого алюмината и трёхкальциевого силиката. Применяется при возведении сооружений циклически контактирующих с водой.
В отдельную группу выделяются шлаковые цементы, которые изготавливаются из отходов металлургического производства или золы от сжигания сланцев и бурого угля. Применяется в производстве шлакоблоков.
Технология производства
Принцип производства цемента не претерпел кардинальных изменений с момента его изобретения. Основные процессы:
- Добыча известняка или мергеля открытым способом.
- Измельчение.
- Приготовление смеси.
- Обжиг.
- Выдержка. Выдержка производится в течение 1...2-х недель для завершения химических процессов.
- Помол, упаковка в мешки или закладка в силосы для хранения.
Различают два способа — сухой и мокрый. При использовании мокрого способа перемешивание происходит с добавлением воды, которую затем выпаривают. К достоинствам этого способа можно отнести равномерность смеси по составу и размеру фракций. Недостаток — большой расход энергии на выпаривание воды перед обжигом (энергозатраты составляют 20...25% стоимости).
Производится в клинкерной (вращающейся) печи с факельной горелкой. Печи для мокрой смеси вдвое длиннее и больше по диаметру, чем печи для сухой смеси. Температурный режим: верхняя загрузочная зона — 70...200 °С, зона декарбонизации — 700...1100 °С, зона спекания 1300...1450 °С, зона охлаждения — 1300...900 °С, с переходом в холодильник для быстрого охлаждения гранул.
Сухой способ приготовления смеси получил развитие с появлением устройств экспресс-анализа состава смеси и технологий с автоматизацией процесса смешивания, что снизило энергетические затраты в 2...3 раза и увеличило съем продукции с одного квадратного метра производственной площади. На выходе получаются клинкерные гранулы.
Положение в отрасли
Пик развития производства цемента приходится на 1965...1972 годы. СССР занимал первое место в мире, производя 100...140 млн. тонн в год (мощности предприятий РСФСР — 89...95 млн. тонн). В 90-е годы было выведено из производства более половины предприятий общей мощностью 17...23 млн. тонн. Оставшиеся предприятия объединены в десяток производственно-строительных групп.
Ведущие компании:
- Евроцемент Груп (13 крупнейших заводов по всей территории России).
- Холдинг Holcim Group.
- Группа компаний ЛСР.
- Консорциум United Cement Group.
- Холдинг Сибирский цемент.
- ХайдельбергЦемент Рус.
- Компания Lafarge.
Темпы ежегодного прироста за период 2009...2012 годы составлял 4,5 %, а в 2013 — 7,8% (объем 66,4 млн. тонн). В настоящее время 90% цемента производится по затратному «мокрому» способу.
Перспективы отрасли
В целом перспективы рынка цемента имеют основания для оптимизма. Потребность в цементе удовлетворяется промышленностью на 90%, а Правительство планирует строительство большого количества объектов (чемпионат мира по футболу, газопровод Южный поток, космодром Восточный, особый экономический статус Дальнего Востока и др.). Главным сдерживающим фактором развития отрасли является отставание в применении технологии сухого приготовления смеси. Законченная реконструкция ряда предприятий и ввод в строй нескольких новых позволит снизить процент «мокрого» производства до 70, что явно недостаточно (в Европе таких производств нет совсем). По данным ФТС РФ стоимость импортного цемента составляет 56...70 долларов за тонну, что существенно превышает среднюю внутреннюю цену 110...130 $/тонну (ДФО — 183 $/тонну). Такая ситуация (при объеме импорта 12...14 млн. тонн в год за последние два года) оказывает существенное давление на внутренних производителей.
www.wiki-prom.ru
состав, технология и этапы изготовления
Дата: 30 января 2017
Просмотров: 24431
Коментариев: 3
Из чего и как делают цемент?

Цемент – широко распространенный материал, который применяют при любых видах работ, связанных с ремонтом, реставрацией, строительством. Цементная основа – вяжущие компоненты неорганического происхождения. Из цемента производятся бетонные, кладочные, штукатурные растворы, железобетонные изделия, используемые при строительстве промышленных объектов и частных построек.
Особенностью порошкообразной цементной массы, смешанной с водой, является способность постепенно твердеть, превращаясь в каменный массив. Процесс приобретения эксплуатационной прочности происходит как в воздушной среде, так и в воде. Главное условие твердения – избыточная влажность.
Все сталкивались с цементом, однако мало кто знает, из чего делают этот универсальный строительный материал, как его производят. Его основа – клинкер, специальные минеральные добавки и гипс. Рассмотрим подробно, как делают цемент, какое сырье для этого используется.

По-прежнему клинкер – это основной компонент, входящий в состав цемента
Сырьевые материалы
Производство цемента осуществляется на специальных заводах, расположенных близко к местам добычи исходного сырья для его изготовления. Главным исходным сырьем для цементного производства являются следующие естественные породы:
- ископаемые карбонатного типа. Это ценное природное сырье, отличающееся особенностями кристаллической структуры, физическими характеристиками. Материал может иметь кристаллическую или аморфную структуру, определяющую эффективность его взаимодействия при обжиге с другими компонентами;
- глинистые материалы, горные породы осадочного характера. Они имеют минеральную основу, становятся пластичными, объемно увеличиваются при избыточном увлажнении. Сырье характеризуется вязкостью, применяется при сухом методе производства.
Карбонатные породы
Остановимся на карбонатных породах, характерными представителями которых являются:
- Мел, являющийся горной породой осадочного характера, которая легко перетирается, относится к разновидностям мажущего известняка. Он популярен при изготовлении цемента.
- Мергель или мергелистый известняк – ископаемые осадочного типа, которые добываются в рыхлом или твердом состоянии, отличаются удельным весом, концентрацией влаги. Содержат примеси глины, что позволяет относить их к переходному сырью, имеющему много общего с известняковыми породами и ископаемыми на основе глины.
В состав входят активные минеральные добавки (15%) в соответствии со стандартами производства
- Известняковое сырье, ракушечники, отличающиеся отсутствием включений кремния. Порода обладает пористой структурой, легко разрушается под воздействием сжимающих усилий.
- Породы доломитового типа, а также горные ископаемые осадочного происхождения, содержащие карбонаты. Они характеризуются ценными физическими свойствами.
Глинистое сырье
К глинистым породам относятся:
- глина, содержащая минеральные включения, разбухающие при добавлении воды;
- суглинки, являющиеся разновидностью глины, с повышенной концентрацией песчаной фракции и пылеобразных частиц;
- сланцы на глинистой основе, относящиеся к горным породам с повышенной прочностью, которые при измельчении расслаиваются на пластинчатые частицы. Сырье характеризуется стабильным гранулометрическим составом, низкой концентрацией влаги.
- лесс, представляющий рыхлую горную, непластичную породу, отличающуюся пористостью, мелкозернистостью. Содержит включения силиката, кварца.
Возможно применение отходов промышленного производства, других видов природных материалов и шлаков.
Корректирующие добавки
Цементный состав делают из минерального сырья с применением специальных пластификаторов, добавляемых при производстве.

Если увеличить количество добавок до 20%, то свойства цемента будут несколько изменены
Технология предусматривает использование добавок на базе ископаемых, содержащих:
- Глинозем.
- Кремнезем.
- Глину.
- Плавиковый шпат.
- Апатиты.
Введение корректирующих добавок, с помощью которых делают цемент и улучшают его характеристики, предусмотрено технологией. Пластификаторы позволяют улучшить следующие свойства цементного состава:
- стойкость к воздействию коррозионных процессов;
- устойчивость к воздействию перепадов температуры, глубоким циклам замораживания;
- прочностные характеристики;
- продолжительность твердения;
- подвижность цементного раствора, его эластичность;
- степень проницаемости водой.
Состав
Задумывались ли вы, из чего сделан цемент? Его состав обусловлен особенностями сырья и конкретной маркой продукции. Так, пользующийся широкой популярностью портландцемент имеет следующий состав:
- Кремниевый диоксид (кремниевая кислота или кварц) – 25 %.
- Известь – 60 %.
- Алюминий (глинозем) – 5 %.
- Оксиды железа и гипс – 10 %.

Сегодня производится множество видов цемента
Процентное соотношение ингредиентов может изменяться, согласно особенностям технологии и марки цементной продукции. Отдельные виды цементов, в частности шлакопортландцемент, включают в свой состав шлак, представляющий уголь, полученный в результате обжига клинкера.
Независимо от рецептуры, основные ингредиенты при изготовлении цементного состава – глина и известняк. Концентрация известняка трехкратно превышает содержание глины, что обеспечивает необходимое качество клинкера для производства цементной продукции.
Основными компонентами, из которых производят цемент, являются:
- клинкер, определяющий прочностные характеристики, получаемый при обжиге исходного сырья (известняка, глины). Клинкер является основой конечной продукции, используется в гранулированном виде диаметром 10-60 мм. Клинкер термообрабатывается при температуре порядка полторы тысячи градусов Цельсия. Он плавится с образованием массы с высоким содержанием кальциевого диоксида и кремнезема, которые определяют эксплуатационные характеристики цементных составов. Гранулы дробятся до пылеобразного состояния с последующим обжигом;
- гипс, процентное содержание которого определяет период твердения. Базовая рецептура предусматривает использование до 6% чистого порошкообразного гипса или гипсового камня, содержащего примеси;
- специальные добавки, вводимые для усиления имеющихся свойств или придания составу специальных характеристик, расширяющих сферу применения.

Очень часто цемент применяют в строительстве для создания бетона и армированных конструкций
Процесс изготовления
Производство цемента осуществляется поэтапно, предусматривает следующее технологические операции:
- Предварительное смешивание ингредиентов для изготовления клинкера, который делают из известняка, вводимого в количестве 75%, и из глины, доля которой составляет 25%.
- Высокотемпературный обжиг, после которого образуется клинкер. Он – результат процесса соединения глины и извести под воздействием повышенной до 1450 градусов Цельсия температуры.
- Измельчение, осуществляемое с помощью шаровых мельниц. Они представляют горизонтально расположенные барабаны с находящимися внутри стальными шарами, обеспечивающими измельчение клинкера до порошкообразного состояния. С уменьшением фракции помола возрастают эксплуатационные характеристики и марка цементного состава.
Этапы производства
Особенности производства предусматривают изготовление цемента различными методами, что сказывается на особенностях применяемого сырья. Это обусловлено расположением цементного производства, спецификой применяемого оборудования, спросом на определённые марки продукции.
Все варианты технологий отличаются только особенностями подготовки исходного сырья, которые осуществляются:
- мокрым путем. Мокрая технология предусматривает использование вместо извести мела, смешивание которого с необходимыми ингредиентами происходит одновременно с измельчением в горизонтальном барабане с обязательным добавлением воды. При этом образуется шихта с концентрацией влаги 30-50%. Шихтовый материал обжигается в печи, превращаясь в шарообразный клинкер, который затем измельчается;
- сухим методом. Сухая технология характеризуется уменьшенной себестоимостью производства цемента, сокращением технологического цикла. Это связано с объединением технологических операций, позволяющих одновременно осуществлять помол и сушку компонентов в шаровой мельнице под воздействием поступающих горячих газов. Полученная шихта имеет порошкообразную консистенцию;
- комбинированным способом. Комбинированный вариант объединяет особенности мокрого и сухого способа производства, но на разных предприятиях имеет определенные отличия. Один из вариантов обеспечивает возможность получение полусухого состава с влажностью до 18%, произведенного путем высушивания шихты, полученной по мокрой технологии. Второй метод предусматривает подготовку сухой смеси с последующим ею увлажнением до 14%, гранулированием, заключительным отжигом.
Заключение
Материал статьи предоставляет информацию о том, как делают цемент, какое сырье применяют, какие технологические особенности используют в процессе производства. Имеется множество технологических нюансов, которыми в совершенстве владеют специалисты, занимающиеся изготовление цемента.
pobetony.ru
состав вещества, процесс изготовления. Из каких компонентов состоит цемент, как приготовить его в домашних условиях?
Краткое содержание статьи:
Задаться вопросом, из чего делают цемент и как его можно получить в домашних условиях, можно либо во время ремонта, либо скучным субботним вечером. Учитывая возможность купить в любом магазине строительных материалов этот товар, особого смысла в налаживании целой ветки кустарного производства нет. С другой стороны, оказавшись в экстремальных условиях можно воспользоваться некоторыми своими знаниями.
Новые возможности для строительства
На протяжении тысячелетий для постройки домов использовался камень или кирпич:
- Создание любой конструкции было сложным делом, требовавшим от мастера должного уровня подготовки;
- Постройки возводились «на века», хоть и медленными темпами;
- Стоимость строительства какого-то собора могла обанкротить небольшого феодала;
- Никаких альтернатив, вроде как, не было и не предвиделось.
Люди таскали камни, обтесывали их, укладывали и надеялись, что кладка простоит десятилетия, если не века. Или обжигали кирпичи, несколько облегчая себе задачу и снижая срок эксплуатации строения. Хотя, до наших дней дошли древнеегипетские образцы архитектуры, возведенные с помощью кирпича. Так что насчет недолговечности можно поспорить.
А потом появился цемент. Сегодня большая часть многоэтажных зданий выстроена именно благодаря бетонным конструкциям и заливке цемента. Найдут ли археологи далекого будущего какие-то следы этих строений и нашей цивилизации – вопрос сложный.
Производство цемента
На первый взгляд, все просто:
- Берем известняк и глину с преобладанием силикатов кальция;
- Смешиваем в однородную субстанцию;
- Равномерно обжигаем, в крутящейся печи;
- Температуру необходимо поддерживать на уровне 1400°C, весь процесс займет от двух до четырех часов;
- В получившийся клинкер добавляем гипс и минеральные добавки;
- Доля гипса – до 5%, минеральных добавок – до 15%;
- Мелко измельчаем полученную смесь на мельнице.
От добавок будут зависеть свойства готового продукта, именно они определяют его качество и характеристики. Так что этому моменту, во время производства, уделяется особое внимание.
Напутав с процентами и добавив чуть сверху можно получить совсем другую смесь, с характеристиками, отличающимися от заданных значений.
Цемент изготавливают на заводах, в промышленных масштабах. Ежегодно счет идет на миллионы тон, а по всему миру – на миллиарды. А все на нужды развивающегося строительства, хоть уже сложно находить площади вокруг мегаполисов, учитывая разветвленность инфраструктуры.
В этом видео технолог Борис Адамов покажет весь процесс производства цемента от начала до конца:
Как сделать цемент своими руками?
Должны быть какие-то серьезные мотивы, чтоб отказаться от самого простого варианта – купить в ближайшем магазине:
- Большие объемы работ с цементом;
- Отсутствие возможности приобрести, по каким-либо причинам;
- Острое желание попробовать сделать это самостоятельно;
- Наличие понимания технологии производства и возможность запустить свой небольшой «конвейер».
Технология производства не должна отличаться от той, что используют на заводе, а это значит, что нам понадобится:
- Много сырья;
- Собственная мельница;
- Вращающиеся печи с возможностью поддержания температуры на высоком уровне.
Самый простой вариант:
- Смешать мел с каолином в пропорции 3 к 1;
- Измельчить полученную смесь на мельнице;
- Обжечь в печи, те же 4 часа при температуре в 1400°C;
- Еще раз измельчить уже обожженную субстанцию;
- Добавить 5% гипса.
Не стоит и упоминать, что гипс тоже придется измельчать до порошкообразного состояния. Все это займет слишком много времени, усилий и выльется в значительные финансовые траты.
Так что приобрести даже пару десятков пакетов цемента – всегда выгодней и проще, чем пытаться все сделать самостоятельно. Но для собственного развития можно разок попробовать, чтоб убедиться в бессмысленности этой затеи.
Как правильно сделать раствор цемента?
Любой раствор цемента состоит из трех компонентов:
- Засыпка;
- Вода;
- Сам цемент.
В качестве засыпки, чаще всего, используют песок. Чтоб придать конечному продукту прочности, иногда применяют щебенку. Соотношение составляющих зависит от целей, с которыми будет применяться будущий раствор – чем большая надежность и прочность необходима, тем больше придется добавить цемента и тем меньше используется песка.
Соотношение идет от 1 к 6, когда на каждый килограмм цемента добавляют по 6 кг песка или щебенки, до 1 к 1.
Непосредственно сам процесс изготовления выглядит так:
- Цемент и засыпку смешивают, в сухом виде;
- Лучше выкладывать оба компонента послойно, перемешивая между собой;
- Добавляется вода;
- Вплоть до процесса затвердения образовавшуюся массу перемешивают.
Главная задача – избавиться от комочков и получить на выходе прочный и надежный продукт. Правило «просто добавь воды» в этом случае работает не идеально, чем больше использовано жидкости, тем хуже будут свойства готового цемента.
Но, конечно же, существует определенная граница – использовав воды меньше этого показателя вы тоже ухудшите итоговый результат. Важно найти баланс и попытаться удержаться на этом уровне.
Секреты изготовления цемента
Для производства цемента применяют:
- Смесь из известняка и глины – клинкер;
- Гипс;
- Минеральные добавки.
Все компоненты смешивают в определенных пропорциях, измельчают до состояния порошка и обжигают в крутящихся печах. Именно благодаря вращению, выходит равномерно термически обработать всю смесь и обеспечить высокий уровень качества конечного продукта.
Что касается изготовления самого раствора:
- Купленный цемент смешивают с засыпкой – песком или щебнем;
- Равномерно перемешивается, слой за слоем, в сухом виде;
- Добавляется вода;
- Полученную вязкую субстанцию мешают и дальше, чтоб предотвратить образование комочков.
Изготовить цемент самостоятельно можно и кустарным методом, но придется обзавестись оборудованием и найти источник сырья. Это сложнее и уж точно не дешевле, чем купить готовый товар в магазине. Если решили посоревноваться с заводами в производстве цемента – ничего не выйдет, не те мощности и совершенно другие показатели себестоимости.
Если пытаетесь сделать «для общего развития» и не сильно много внимания уделяете технологии производства, конечный продукт может обмануть ожидания, даже самые скромные.
Если раньше только строители знали, из чего делают цемент, то сейчас эту информацию может найти кто угодно. Все данные в свободном доступе, можно самосовершенствоваться и пробовать делать что-то самостоятельно.
Видео о процессе производства цемента
В этом ролике в передаче «Как это сделано» будет рассказано о том, как производят цемент марки M-500, как фасуют его в мешки:
1-vopros.ru
Оборудование + Технология изготовления 2018

Цемент представляет собой искусственный строительный материал. Основными его составляющими компонентами являются клинкер и гипс. При взаимодействии с водой, водными растворами солей и другими жидкостями он образует пластичную массу, через некоторое время завертывающуюся и превращающуюся в камневидное тело. В основном цемент используется для изготовления бетона и различных растворов, используемых в строительстве.
Является гидравлическим вяжущим, обладающим способностью набирать свою прочность во влажных условиях, что принципиально его отличает от некоторых других минеральных вяжущих.
Оборудование для производства цемента
Производственная линия состоит из следующих установок: барабанная печь, прибор для предварительного нагрева сырья, мельница, охладитель, вальцы, сушилка, пылеуловитель, сепаратор, оборудование для проведения предварительной гомогенизации, дробилка и транспортер с машиной для упаковки. Перечисленные аппараты представляют собой обязательные элементы линии производства. Производители также предлагают разнообразные модификации данного оборудования, и дополнительное оснащение, позволяющее повысить производительность и безопасность, снизить затраты и себестоимость получаемой продукции.
Технология производства цемента + видео как делают
Современные технологии и материалы позволяют производить различные типы цемента. Некоторые уже практически перестали производиться, другие только приобретают известность. Также существуют смеси, предназначенные для выполнения узкоспециализированных задач.
Виды
- Портландцемент. Представляет собой один из самых известных марок. В его состав входит клинкер с гипсом, различные добавки, смесь идет мелкого помола. Активно проявляет свои свойства при контакте с водой. Название было дано в честь горной породы на территории Англии Portland, по причине аналогичного цвета после застывания.
- Белый цемент – смесь из мелкомолотого клинкера, максимально очищенного от окислов железа, что повышает скорость реакции. Используется в основном в декоративных целях.
- Шлаковый. Состоит из измельченного доменного шлака с активаторами и добавок – отсюда и название. Характеризуется повышенными показателями прочности, что и определяет основную сферу его применения – подземные и подводные несущие конструкции.
- Расширяющийся – в процессе отвердевания строительная смесь расширяется. Благодаря приобретенному позже свойству водонепроницаемости используется в подводных конструкциях, когда идет постоянное давление воды.
- Безусадочный. Обладает свойством сохранять свой объем в процессе отвердения. Используется при проведении гидроизоляционных работ, когда требуется сохранение объема цементной массы.
- Быстротвердеющий. Характеризуется максимально коротким временем для отвердевания по сравнению с другими марками цементов.
- Гидрофобный. Представляет собой модификацию портландцемента со специальными добавками, придающие стойкость цементу к процессам замерзания и оттаивания.
- Тампонажный. Используется для укрепления скважин в нефтегазовой промышленности.
- Глиноземистый. Обладает целым рядом свойств, которые позволяют его использовать вместо нескольких марок цемента в строительных работах в холодное время года и при возведении жаропрочных конструкций.
- Пуццолановый – вид, производимый из портландцемента путем добавления соединений вулканического происхождения, что позволяет использовать его при возведении водяных емкостей.
Марки
По прочности цемент делится на марки, определяющиеся пределом прочности при сжатии половинок образцов-призм размером 40×40×160 мм, которые изготавливаются из раствора с содержанием кварцевым песком 1:3. Марки имеют диапазон М200-М600 (с шагом 50 или 100), означающий прочность при сжатии (соответственно в 200-600 кг/см² (20—60 МПа)). Цемент М600 из-за своей прочности называется «военным» или «фортификационным» и стоит заметно выше остальных. В основном он используется в строительстве военных объектов и сооружений.
Также существуют и классы прочности. Основное их отличие от марок состоит в том, что прочность выводится не как средний показатель, а требует не менее 95% обеспеченности (то есть 95 образцов из 100 должны соответствовать заявленному классу). Класс прочности выражается в числах от 30 до 60, выражающиеся в МПа.
Способы производства
Существуют три метода производства цемента: сухой, мокрый и комбинированный.
При использовании сухого способа основные ингредиенты будущего цемента – известняк и глина – смешиваются в агрегате для дробления и сушки. Затем полученная смесь проходит через мельницу, которая приводит смесь в однородное состояние. Такая смесь называется сырьевой мукой, и в специальном бункере – проходит специальное смешивание – гомогенизация – получается гомогенизационный силос, который затем проходит обжиг в специальной печи, после чего смесь проходит на следующий этап. В следующей мельнице в клинкер – так называется полученная смесь – добавляется гипс и проводится повторный помол всего содержимого в агрегате. После мельницы почти полностью готовый цемент собирается в силосе для хранения. После этого из бункера готовый цемент идет на упаковку и отгрузку.
Мокрый способ состоит из следующих этапов производства. Компоненты засыпаются в дробилку и дробятся в сухом состоянии, также они смешиваются до получения однородной смеси. Затем в специальной мельнице с использованием воды проходит мокрый помол компонентов, которые после этого проходят корректировку в шламбассейне. Полученная смесь называется шламом. После корректировки шлам отправляется на обжиг, как и в сухом способе производства, во вращающуюся печь. И далее процесс аналогичен по операциям, которые проводятся при получении цемента сухим способом.
У сухого способа есть определённые преимущества: экономия топлива при производстве на тридцать-сорок процентов, поскольку исключается этап с мокрыми процессами; снижение затрат на трудовые ресурсы и подготовку клинкерной смеси; повышение качества клинкера и цемента.
Видео как делают:
Третий способ производства называется комбинированным, поскольку соединяет в себе два предыдущих. Существует варианты комбинации указанных выше способов – первым может идти сухой этап – тогда идет приготовление смеси – и дальше производство цемента по мокрому способу. Второй вариант предусматривает в первую очередь применение мокрого способа для получения водной суспензии, которая в дальнейшем проходит этапы сухого метода производства.
Читайте также
moybiznes.org