Полная инструкция по производству арболитовых блоков своими руками. Производство арболитовых блоков
Арболитовые блоки - недостатки, технические характеристики, размеры, состав
Арболит в большинстве источников описывается, как материал, обладающий чудесными свойствами. Рекламные статьи превозносят арболитовые блоки, недостатки материала скромно умалчиваются. Но чудес не бывает, недостатки тоже есть. Чтобы по максимуму использовать положительные качества и нивелировать отрицательные, стоит хорошенько разобраться со свойствами арболита, его характеристиками и особенностями применения.
Состав и производство арболиттовых блоков
Начнем наш материал именно с состава и процесса производства. Все дело в том, что от качества выполнения определенных процессов зависит наличие или отсутствие определенных недостатков материала. А это является очень важным. Арболит позиционируется, как одна из разновидностей крупноячеистых легких бетонов. В качестве наполнителя в нем используется древесная щепа. Щепа связывается в монолитную структуру цементным тестом.
Материал используется в строительстве в нескольких видах:
- крупноформатные кладочные блоки;
- пустотелые блоки;
- теплоизоляционные плиты;
- смеси для заливки ограждающих конструкций по месту.
Кладочные блоки нашли наиболее широкое применение и под понятием «арболит» понимаются, прежде всего, они. Самым распространенным размером арболитовых блоков является 500×300×200 мм. Но в последние время производители стали расширять свои производственные линейки и предлагают арболит в других типоразмерах.
Технология изготовления блоков относительно проста, но как и везде, имеются свои тонкости. Качество будущих изделий зависит от соблюдения нескольких важных производственных моментов. Если производитель использует в наименовании своей продукции термин «арболит», он должен соблюдать требования нормативной документации на такие изделия, это:
- 1. ГОСТ 19222-84 "Арболит и изделия из него. Общие технические условия".
- 2. СН 549-82 "Инструкция по проектированию, изготовлению и применению конструкций и изделий из арболита".
Состав арболитовых блоков
Для изготовления арболитовых блоков используется:
- Древесная щепа;
- Химические добавки;
- Вода;
- Цемент.
#1. Древесная щепа. Итоговая прочность сильно зависит от калибра щепы. Чтобы на выходе был именно арболит, свойства которого строго нормированы, для производства должна использоваться именно щепа. Ее размеры регламентированы. ГОСТ рекомендует максимальный размер частиц 40×10×5 мм (длина/ширина/толщина).
Наилучшие показатели у блоков с размерами щепы из интервалов:
- длина – до 25 мм;
- ширина – 5..10 мм;
- толщина – 3..5 мм.
Опилки, стружки, тырса, костра, солома и все остальное, что пытаются смешивать с цементом для производства арболита, для его изготовления не подходит. Только чистая щепа без коры, листьев, грунта и прочих нежелательных примесей. Считается, что добавление до 10 % коры или 5 % листвы не оказывает серьезного влияния на характеристики арболита. Но лучше когда эти примеси отсутствуют.
Зачастую производства арболитовых блоков, организованы при лесопилках и других деревоперерабатывающих предприятиях. Для них арболит не является профильным направлением. В результате недобросовестные производители, для увеличения рентабельности производства, кроме самой щепы добавляют то, что имеется. Отсюда непредсказуемое качество продукции.
На специализированных предприятиях устанавливают производительные валковые дробилки, откалиброванные под нужный размер щепы.
Для конечного потребителя не имеет большого значения сорт древесины, из которой производится сырье, но технологи должны это учитывать для правильной дозировки минерализаторов и выбора степени уплотнения. Так, щепа лиственницы требует двойного количества добавок относительно других хвойных пород. Чаще других на производство щепы идут сосна, ель, реже лиственные породы.
#2. Химические добавки. Древесный наполнитель содержит сахара, которые препятствуют качественной адгезии цементного теста с поверхностью частичек дерева.
Для решения этой проблемы применяются 2 основные стратегии:
- 1. Высушивание древесного сырья до применения в производстве в течение нескольких месяцев.
- 2. Минерализация поверхности щепы в растворе химических компонентов.
Наилучшие результаты достигаются при комплексном подходе к решению задачи. Снижение содержания сахаров и минерализация сырья позволяет решить и другие важные задачи:
- повышение биологической стойкости материала;
- снижение водопроницаемости при эксплуатации готового изделия.
Для решения всех этих задач, при производстве арболита могут использоваться следующие компоненты: хлорид кальция (ГОСТ 450–77), жидкое стекло (ГОСТ 13078–67), силикат-глыба (ГОСТ 13079–67), сернокислый глинозем (ГОСТ 5155–74), известь (ГОСТ 9179–77).
#3. Вода. Получать арболитовые блоки, характеристики которых соответствуют заданным, можно, следуя определенному порядку технологических операций. Вода с добавлением минерализаторов готовится заранее. Расход компонентов принимается в следующих соотношениях:
Расход на 1м3 арболита, кг | 12 | 12 | 8+4 |
Щепа засыпается в смеситель принудительного действия. Обычные гравитационные бетономешалки не обеспечивают достаточной гомогенизации. Вода с растворенным минерализатором перемешивается и равномерно распределяется по поверхности щепы. Перемешивание происходит на протяжении 20 секунд. На следующей стадии происходит добавление цемента. Перемешивание с цементом длится 3 минуты.
#4.Цемент. Достаточная для применения в строительстве прочность материала достигается только при применении цемента с маркой не ниже 400. Цемент имеет свойство быстро терять марку при хранении. Даже на выходе с завода цемент часто не соответствует заявленным характеристикам. Поэтому лучше когда, арболитовые блоки, технические характеристики которых должны соответствовать требованиям, предъявляемым к конструкционным материалам, изготавливаются из 500-го цемента.
Формование блоков
Формование необходимо завершить в течении ближайших 15 минут после перемешивания. В зависимости от степени механизации последующих процессов различают следующие способы формования:
- ручное формование без вибрирования;
- ручное формование с вибрированием;
- производство на вибростанке;
- производство на вибростанке с пригрузом.
Механизация процессов позволяет получать более высокие по качеству и стабильные по параметрам арболитовые блоки. При этом размеры, геометрия и плотность сохраняются от изделия к изделию.
Выдерживание изделия в опалубке применяют при кустарном производстве, когда снятию опалубки сразу после формования препятствует слишком жидкая консистенция раствора. В общем случае формы снимают без выдержки.
Сырые блоки остаются на съемном днище-поддоне или прямо на полу цеха.
Арболитовые блоки, состав которых одинаков, могут получать различные характеристики в зависимости от способа и степени их уплотнения. Основной целью прессования смеси в форме не является повышение ее плотности. Главная задача – это создание равномерно распределенной по объему структуры из произвольно ориентированной, полностью укрытой цементным тестом, щепы.
Вибрация при уплотнении применяется очень дозировано. Чрезмерное вибрирование приводит к осаждению цементного теста на дне формы. Важно сохранять его равномерное распределение по объему с полным укрытием зерен наполнителя. Даже в арболите высокой плотности щепа не плавает в растворе цемента с водой. Цементное тесто работает, как клей, покрывающий зерна наполнителя. Меняется только концентрация щепы в объеме и толщина покрывающего ее цементного камня.
Уплотнение блоков производится на значения, достаточные для взаимной переориентации зерен наполнителя и увеличения площади их соприкосновения. Сжатия и деформации самой щепы не происходит. Это обеспечивает сохранение размеров блока после снятия уплотняющего усилия.
Необходимость точной дозировки всех компонентов и соблюдения технологии
Точность дозирования компонентов регламентируется ГОСТом. Допустимые отклонения не могут превышать нескольких процентов. В условиях недостатка воды не происходит гидратация всего объема цемента. Ее избыток нежелателен по нескольким причинам:
- Превышение водоцементного соотношения снижает прочность.
- Избыточная пластичность препятствует выниманию сырого блока из формы непосредственно после формования.
- Увеличивается время хранения блока на поддоне до первичного схватывания.
Концентрация минерализаторов щепы, идущей в арболит, важна для прочности и долговечности материала. Дозировки компонентов, приводимые в нормативах, рассчитаны на определенный калибр заполнителя и его влажность на уровне 25 %. Оптимальную дозировку подбирают опытным путем на основе испытаний готовых образцов.
Плотность арболита
По назначению материал условно делят на 2 типа:
- теплоизоляционный;
- конструкционный.
Определяющим фактором является плотность изделия. Считается, что блоки с плотностью до 500 кг/м3 не подходят для использования в составе несущих конструкций. Но они могут применяться для теплоизоляции при возведении наружных стен в строениях, где нагрузка от кровли или перекрытий воспринимается колонами или другими элементами.
Типичными для конструкционных блоков являются значения плотности из интервала от 550 до 700 кг/м3. Но можно купить изделия и с плотностью до 850 кг/м3. Слишком высокие величины указывают на хорошую несущую способность элементов, но уступают более легким в теплоизоляционных качествах. Плотность материала замеряется при установившейся массе, когда блок прекращает терять влагу.
Стены из литого арболита могут иметь плотность порядка 300 кг/м3, но по несущей способности не уступают сложенным из камней с плотностью 550 кг/м3.
Прочность арболитовых блоков
Несущая способность блоков характеризуется их прочностью на сжатие. По результатам испытаний изделиям может присваиваться марка и класс по прочности на сжатие. В общем случае они связаны с плотностью материалов.
400 - 500 | М 5 | В 0,35 |
450 - 500 | М 10 | В 0,75 |
500 | М 15 | В 1,0 |
500 - 650 | - | В 1,5 |
500 - 700 | М 25 | В 2,0 |
600 - 750 | М 35 | В 2,5 |
700 - 850 | М 50 | В 3,5 |
Как и в случае изделий из тяжелого бетона, марка является средней величиной по результатам испытаний партии образцов. Класс характеризует гарантированную прочность, 95 % образцов должны соответствовать по классности.
Для реальных испытаний с хорошей выборкой зависимость между маркой и классом через переводные коэффициенты не является корректной. В этом случае разрыв между маркой и классом может рассказать о культуре производства на предприятии. Чем меньше разрыв, тем выше организация производства. В отечественной практике изготовления арболитовых блоков это учитывается с помощью коэффициентов вариации. Для изделий 1-ой категории качества допускается значение 18 %, для высшей – 15 %.
В кирпичной кладке мелкий размер изделий делает понятие классности бессмысленным. При покупке крупных кладочных камней, каковыми и являются арболитовые блоки, стоит отдавать предпочтение изделиям с присвоенным классом.
Для возведения несущих стен одноэтажных зданий высотой до 3 м допускается использовать блоки класса от B 1.0. Для более высоких стен нужны элементы класса от B 1.5. Для 2-х - 3-х этажных строений используют блоки классов B 2.0 и B 2.5.
Прочность арболита на сжатие типична для ячеистых бетонов. Важным отличием является прочность блоков на изгиб, которая составляет от 0,7 до 1,0 МПа. Модуль упругости элементов может доходить до 2300 МПа. Такие величины делают арболит особенным среди ячеистых бетонов. Если для пенобетона и газобетона велика вероятность трещинообразования, то для арболита такая проблема не стоит.
Теплопроводность арболита
Теплопроводность для арболита является одним из ключевых параметров.
Она растет с увеличением его плотности в следующей прогрессии:
Рекомендованная ГОСТом толщина ограждающих конструкций из арболита в умеренных широтах составляет 38 см. Но стены такой толщины возводятся редко. На практике для стен жилых домов блоки 500×300×200 мм кладут плашмя в один ряд. Вместе с внутренней и наружной отделкой этого достаточно для поддержания комфортной температуры в помещениях без появления проблем с выпадением конденсата.
Дополнительная теплоизоляция часто выполняется с помощью теплых штукатурных систем толщиной 1,5-2 см с добавкой перлита. Для не отапливаемых или периодически отапливаемых помещений (бани) нередко применяют кладку блоков на ребро.
Влагопоглощение арболита
В характеристиках арболита указывают величину водопоглощения до 85 % для теплоизоляционных блоков и до 75 % для конструкционных. Эти значения требуют осмысления. Структура блока представляет собой склеенные цементным камнем разрозненные зерна щепы. Они ориентированы относительно друг друга случайным образом.
Вода, наливаемая на поверхность блока, свободно протекает сквозь него. Естественно, что при окунании вода способна вытеснить большой объем содержащегося внутри блока воздуха. Если блок вытащить из воды, вода вытекает, а цементный камень быстро высыхает.
Арболитовые блоки находящиеся в естественной среде, например в стене дома, фактически не накапливают в себе влагу из окружающего воздуха. Это происходит благодаря очень низкой сорбционной влажности материала, т. к. минерализованные щепа и цемент являются негигроскопичными и слабо смачивающимися материалами. Именно это стало причиной популярности использования материала для строительства бань.
Если поливать ничем не закрытую стену из арболита с внешней стороны водой, есть вероятность увидеть ее и внутри. Поэтому материал не используют без фасадной отделки. Для арболита рекомендуют отделку штукатурными растворами или устройство навесных фасадных систем.
Морозостойкость
Низкое сорбционное влагопоглощение дает арболиту хорошую стойкость к промерзанию. Минимальное значение составляет F25 и доходит до F50. Защита арболита от прямого воздействия влаги, позволяет повысить реальную морозостойкость материала в конструкции. Кроме этого существуют реальные примеры эксплуатации зданий из арболита на протяжении 7 - 10 лет без повреждений для стен. Причем речь идет о стенах, которые ни чем не защищены от воздействия внешних факторов среды.
Усадка материала
Считается, что арболит совершенно не подвержен усадке. Но небольшие усадочные процессы в первые месяцы все же присутствуют. В основном они прекращаются еще на этапе созревания блока на производстве. Некритичное уменьшение размеров блока (на 0,4 - 0,8 %) возможно уже после укладки блоков в конструкцию.
Некоторое сокращение высоты блоков может происходить и под весом вышележащих элементов, перекрытий и конструкций кровли. Для предотвращения проблем с отделкой не рекомендуется выполнять штукатурные работы в первые 4 месяца после завершения основного комплекса работ.
Огнестойкость арболитовых блоков
По огнестойкости арболитовые блоки имеют следующие параметры:
- группа горючести - Г1, т. е. это трудногорючий материал;
- группа воспламеняемости - В1, трудновоспламеняемый материал;
- по дымообразующей способности - Д1, малодымообразующий материал.
Звукоизоляция
По шумапоглощению арболитовые блоки превосходят такие материалы как кирпич и древесина. Коэффициент шумапоглощения арболитовых блоков составляет 0,17 - 0,6 в акустическом диапазоне от 135 до 2000 Гц.
Паропроницаемость
Арболит это дышащий материал степень его паропроницаемости составляет до 35 %. Именно поэтому в домах построенных из данного материала не бывает сырости, а микроклимат кофортный как в холодное так и в теплое время года.
Недостатки арболитовых блоков
Как бы ни был хорош арболит, недостатки материала все же стоит знать и учитывать.
Поколебать решимость застройщика способны несколько сомнительных моментов:
- 1. Обилие на рынке блоков «гаражного» качества.
Их прочность, сопротивление теплопередаче неведомы даже производителю. Имеются трудности с приобретением заводского арболита в регионах. Выше мы писали про самые важные моменты производства арболитовых блоков. Как вы понимаете выполнить определенные задачи в кустарных условиях просто не возможно.
- 2. Недостаточная точность геометрии.
Точность геометрии арболитовых блоков уступает таковой у других легкобетонных кладочных камней (пенобетона, газобетона). Особенно это характерно для производств с большой долей ручного труда. Отклонения в размерах и взаимном расположении поверхностей заставляют увеличивать толщину швов до 10 - 15 мм. А это влечет промерзание кладки по швам, перерасход материала и снижение скорости кладочных работ.
Производители рекомендуют использовать для кладки теплые перлитовые растворы, но их приготовление обходится дороже. В последнее время для улучшения геометрии блоков начинают применять фрезерование поверхностей.
- 3. Необходимость защиты от прямого воздействия влаги.
Ничем не защищенная кладка в теории может быть проницаемой для больших напоров ветра, но реального подтверждения такого явления не получено. Нанесение на поверхность штукатурных покрытий решает проблемы с проницаемостью.
- 4. Высокая стоимость арболитовых блоков.
Это связано с недостаточными автоматизацией производственных процессов, степенью проработки технологии и скромными объемами производства. В итоге себестоимость пенобетонных и газобетонных блоков ниже в 1,5 раза.
- 5. Наличие ограничений в выборе отделочных материалов.
Для правильной эксплуатации важно сочетать с арболитовой кладкой только «дышащие» варианты отделки.
Достоинства арболитовых блоков
Тех, кто решается на строительство по арболитовой технологии, должны вдохновлять ее многочисленные достоинства:
+ 1. Экологичность материала.
Даже входящие в его состав минерализаторы не выделяют в атмосферу вредных веществ.
+ 2. Высочайшая паропроницаемость.
+ 3. Легкость материала.
Легкость материала и его упругость не требуют устройства мощного и жесткого фундамента. Дополнительным бонусом является сейсмостойкость.
+ 4. Легкость обработки.
+ 5. Простой монтаж крепежа.
В арболит можно вбивать гвозди и вкручивать саморезы, как в дерево.
+ 6. Низкая теплопроводность.
Отличное сопротивление теплопередаче при достаточной для малоэтажного строительства прочности позволяет обходиться без дополнительного утепления и получать однослойную структуру стены.
+ 7. Низкая звукопроницаемость.
+ 8. Отказ от армирования.
Возможность отказаться от армирования кладки и устройства монолитных поясов на небольших объектах.
+ 9. Биологическая стойкость.
+ 10. Негорючесть.
Примите участие в опросе:
Вам будет интересно
srbu.ru
оборудование, технология, пропорции и формы

Рейтинг материала
16 out of 5
Практичность16 out of 5
Внешний вид20 out of 5
Простота изготовления20 out of 5
Трудоемкость при использовании20 out of 5
ЭкологичностьИтоговая оценка
Арболитовые блоки относятся к легким стеновым строительным материалам. Они изготавливаются из опилок, древесины, цемента, воды и других составляющих.
В качестве основной составляющей используется древесная щепа, которая представляет собой рубленую древесину. У таких блоков больше граница прочности, чем у пеноблоков и газоблоков. Важными характеристиками материала являются: высокая устойчивость к трещинам и ударопрочность.
Технология производства
Первоначальным этапом производства арболита является тщательная подготовка всех необходимых компонентов, затем следует приготовление основы, ее отлив в формы для дальнейшего получения блоков.
Подготовка основы
Наполнитель для блоков включает в себя стружки и опилки в пропорции 1:2 или 1:1. они должны быть хорошо просушены, для этого их выдерживают 3-4 месяца на открытом воздухе, периодически переворачивая и обрабатывая раствором извести.
В последнем случае на 1 куб. метр сырья необходимо около 200 л раствора извести 15%. В нем будут находиться древесные компоненты в течение 4 дней, которые требуется перемешивать 2-4 раза в день.
На данном этапе главная цель – это убрать сахар, содержащийся в опилках. Он может стать причиной их дальнейшего гниения.
Щепу можно купить готовую, а можно сделать самим, соорудив щепорез. Что это такое и как он работает, расскажет видео:
Необходимые компоненты
После того как опилки подготовлены, к ним присоединяют следующие добавки:
- Гашеная известь;
- Сернокислый кальций и алюминий;
- Портландцемент 400 марки;
- Растворимое жидкое стекло;
- Хлористый кальций.
Как правило, доля этих компонентов в арболитовой смеси не превышает 4% от массы цемента. Они придают конечному продукту устойчивость к гниению, обеспечивают высокую огнеупорность и пластичность.
Технология изготовления
Арболитовые блоки имеют оптимальные параметры 25 см*25 см*50 см. они удобны не только в процессе изготовления, но и при укладке. Процесс отливки заключается в следующем: блоки заполняются арболитовой смесью из трех слоев. После каждого подхода следует тщательное уплотнение деревянным молотком, обшитым жестью.
Лишняя масса ударяется при помощи линейки, а форма выдерживается сутки с температурой воздуха от +18оС. По истечению времени блоки извлекаются из форм путем небольшого постукивания и выкладываются на ровное основание для полного затвердения на 2 дня и просушивания на срок от 10 дней.
На фото — процесс выемки арболитового блока из станка после формовки:
Оборудование
Чтобы производить арболитовые блоки может потребоваться различное оборудование в зависимости от объема производства и используемого сырья. Процесс изготовления данного строительного материала и его конечный результат должны отвечать ряду критериям: ГОСТ 19222-84 и СН 549-82.
Чаще всего для производства арболита используются остатки деревьев хвойных пород. Их измельчение производится на рубильной машине (РРМ-5, ДУ-2 и прочие). Более тщательный процесс дробления производится на дробилках (ДМ-1) или молотковых мельницах. На вибростолах из измельченной древесной смеси отделяются кусочки земли и коры.
Саму арболитовую смесь рекомендуется приготавливать на лопастных растворосмесителях или смесителях принудительного цикличного действия. Перевозить готовую смесь к специальным формам можно с помощью кюбелей или бетонораздатчиков. А сам подъем транспортера не должен превышать 15о вверх и 10о вниз при скорости движения до 1 м/с. Падение смеси осуществлять на высоте не более одного метра.
Уплотнение конструкций можно произвести как ручными трамбовками, так и вибропрессом (Рифей и прочие). Если изготовить блоки из арболита необходимо в небольших объемах, то можно воспользоваться специальным мини-станком. Если речь идет о промышленных масштабах, то используют целые линии по производству арболитовых блоков, которые включают в себя станки для изготовления блоков, прессы и смесители.
Так выглядит линия по производству арболитовых блоков
Лучший процесс затвердения достигается путем использования тепловых камер с ТЭНом, ИК-излучением и т. д. В них можно контролировать необходимую температуру и уровень влажности.
Формы для блоков
Формы для производства арболитовых блоков могут быть следующих размеров: 20 см*20 см*50 см или 30 см*20 см*50 см. для строительства конструкций из арболитовых блоков формы могут выпускаться и других размеров (для перекрытий, вентиляционных систем и т. д.).
Формы для блоков можно купить, а также можно изготовить своими руками. Для этого понадобятся доски толщиной 2 см, которые сбиваются в необходимую по размерам форму. Внутренняя часть обшивается фанерой и сверху пленкой или линолеумом.
Схема по изготовлению формы для арболитовых блоков
Как сделать арболитовые блоки своими руками
Список оборудования:
- Разъемная форма и вставки для нее;
- Падающий и вибростол;
- Установка для подъема формы;
- Ударно-встряхивающий стол;
- Лоток для смеси;
- Поддон для формы из металла.
Имея все необходимое оборудование для производства блоков, можно получать 300-400 м3 стройматериала в месяц. При этом площадь для установки всего оборудования потребуется около 500 кв. м и затраты на электроэнергию 10-40 кВт/ч.
Изготовление больших блоков требует их дополнительного армирования. Когда форма заполнена на половину арболитовой смесью, сверху заливается слой бетона с арматурой, после этого продолжается заполнение арболитом.
При самостоятельном изготовлении блоков из арболита органические вещества необходимо залить водой, после чего – цементом до однородного состояния. Для этого потребуется 3 части цемента, 3 части опилок или древесной стружки и 4 части воды. Получившаяся смесь должна быть сыпучей и в тоже время удерживать форму при сжатии в руке.
Перед заливкой внутренняя часть формы смазывается известковым молочком. После этого можно выкладывать подготовленную смесь слоями с тщательной утрамбовкой. Поверхность блока выравнивается шпателем и заполняется штукатурным раствором на высоту 2 см.
Видео о том, как осуществляется производство арболитовые блоки своими руками:
Рекомендации
- Уплотнить смесь можно при помощи дерева, обитого железом.
- Наибольшей прочностью обладают блоки, которые находились под пленкой во влажном состоянии около 10 дней. При этом температура воздуха не должна быть ниже 15 градусов.
- Предотвратить пересыхание блоков можно, периодически поливая их водой.
Достаточно просто самостоятельно изготовить данный строительный материал. Если соблюдать все технологии, то конечный продукт будет прост в применении, обладать высокой прочностью, пожаробезопасностью и длительным сроком эксплуатации.
Понравилась статья? Поделитесь с друзьями в социальных сетях:Вконтакте
Одноклассники
Google+
И подписывайтесь на обновления сайта в Контакте, Одноклассниках, Facebook, Google Plus или Twitter.
stroyres.net
Как выбрать арболитовые блоки | Строительный портал

Арболит представляет собой интересный строительный материал. В основе его названия лежит французское слово «дерево». По своей сути арболитовые блоки представляют собой легкий бетон с древесным наполнителем, составляющим до 90% от общего объема смеси. Сам материал был разработан в СССР еще в шестидесятых, причем быстро завоевал популярность благодаря своим качествам. Одних заводов по производству арболита было построено больше сотни.
Оглавление:
- Арбалитовый блок - что это?
- Преимущества и недостатки арболитовых блоков
- Технология производства арболитовых блоков
- Как изготовить арболитовые блоки своими руками?
- На сколько целесообразно строить из арболита дом?
Арбалитовый блок - что это?
Арболитовый блок состоит из древесных опилок разных фракций и связующего цемента. Производство арболитовых блоков вновь начинает приобретать свою популярность. Несмотря на то, что жилые дома и крупные постройки выгоднее возводить из керамзитобетонных панелей, арболит еще долго останется актуальным благодаря своим качествам.
Одной из важнейших характеристик обозначают значительный предел прочности на сжатие, доходящий до показателя М100 отдельных конструкционных разновидностей. Сейчас его применение более целесообразно для возведения внутренних стен и перегородок, а также для обеспечения тепло- и звукоизоляции. Производство домов имеет широкое распространение, поскольку арболитовые блоки, цена которых находится на примерно том же уровне, что и керамзитобетонные - способны предоставить конкуренцию другим материалам по ряду причин.
Преимущества и недостатки арболитовых блоков
Любой строительный материал имеет как свои преимущества, так и недостатки. К сильным сторонам арболитовых блоков причисляют следующие:
- Прочность материала, которая зависит от плотности. Разновидности арболита, предназначенные для возведения строительных конструкций, по прочности не отличаются от пено- и газобетонных блоков. Но в отличие от них, возведение малоэтажного дома из арболитовых блоков не потребует дополнительного бетонного пояса.
- Эластичность материала, достигаемая за счет наличия в составе армирующих древесных опилок. Благодаря этому даже при воздействии значительных нагрузок арболиту свойственно больше деформация, нежели механическое разрушение.
- Арболит характеризуется низкой теплопроводностью, благодаря чему он занимает свое место среди других эффективных теплоизолирующих материалов. Благодаря этому качеству, стена из арболитовых блоков толщиной в 30 см аналогична по своим показателям теплопроводности метровой из кирпича.
- Показатель звукоизолированности в четыре раза превосходит аналогичный у кирпича, и составляет от 0,16 до 0,6.
- Долговечность материала составляет 50 циклов на замерзание и оттаивание, что соответствует 50 климатических годам. Показатель долговечности превосходит аналогичные у домов из пенобетона, расчетная долговечность которых составляет 35 лет.
- Арболитовые блоки имеют существенно меньший вес, нежели конкурирующие с ними аналоги из пено- и керамзитобетона. 1 м3 весит в три раза меньше кирпичной кладки аналогичного объема, и в 1,5 раза меньше керамзитобетона. Это позволяет упростить конструкцию фундамента, что в свою очередь снижает затраты на возведение постройки.
- Важным достоинством материала является его практически полная негорючесть, несмотря на обилие древесной составляющей. Сам древобетон при воздействии на него открытого источника пламени образует малое количество дыма, и при этом не выделяет токсичных веществ.
- Простота обработки арболитового материала представляет собой еще одно преимущество. Древобетон достаточно легко подвергается обработке любым инструментом, хорошо держит в себе вкрученные шурупы и саморезы, и при этом не требует монтажа армирующей сетки перед нанесением штукатурных растворов.
- Стойкость к воздействию внешних источников, таких как гниение и образование грибка. Арболит характеризуется хорошей паропроницаемостью, благодаря чему материал «дышит» и способен регулировать влажность воздуха. Но в этом кроется и его главный недостаток, речь о котором пойдет несколько ниже.
- Последним убедительным преимуществом арболита является его экологичность. В состав входят натуральные компоненты, такие как цементный камень, древесина, вода и хлористый кальций, который используют в пищевой промышленности.
Минусы арболитовых блоков состоят в следующем:
- Материал отличается повышенной влагопроницаемостью. К примеру, при значительной влажности внутри помещения древобетон начинает втягивать влагу в себя. Под ее воздействием материал способен разрушаться. По этой причине имеет смысл приобретать либо блоки с повышенной влагостойкостью, либо обшивать арболитовую стены с наружной и внутренней стороны,
- Арболит отличается слабой устойчивостью к воздействию агрессивных газов. Хорошим примером является сероводород, взаимодействие которого с влажным воздухом способно привести к появление капелек серной кислоты. Современные производители учли этот недостаток, применяя в арболитовой смеси специальные компоненты для повышения устойчивости к газам,
- Арболитовые блоки не способны противостоять атакам грызунов, которые с легкостью обустраивают в нем свои ходы. Обшивка плитами OSB способно защитить арболит от атак таких грызунов, как мыши или крысы.
Технология производства арболитовых блоков
Процесс делится на несколько этапов:
- Древесные опилки подвергаются просеиванию через сито с крупной сеткой, с размерами ячейки 1х1 см. Оптимально, если стружка имеет от 3 до 15 см в длину, и не менее 0,5 см в ширину.
- Древесина подвергается обработке и сушке. Опилки требуют выведения из них остатков сахара, негативно влияющих на прочность. Выведение осуществляется двумя способами. В заводских условиях для этого используют специальный композиционный состав на основе хлорида кальция. Иногда для выведения сахарозы применяют раствор негашенной извести, и если позволяет время и желание - то древесные опилки оставляют «под открытым небом» на срок от 2 до 3 месяцев.
- Далее стружка вновь подвергается просеиванию через сито для удаления прочих органических материалов и возможного мусора.
- В опилки добавляется смесь из портландцемента, затем она подается в форму, которая находится в постоянной вибрации. Опилки при этом смачиваются водой и жидким стеклом, и далее замешиваются в бетономешалке. В стандартном составе используется такая пропорция соотношения компонентов: на 1 мешок цемента применяют 2 мешка песка и 6 мешков подготовленных опилок. Чтобы смесь не прилипала к стенкам, на производстве обшивают камеры для смешивания линолеумом. Этот же способ рекомендуется при самостоятельном изготовлении блоков.
- После заливки в форму, арболитовую смесь подвергают прессованию, при этом до 30% объема ужимается.
- Блоки выдерживаются трое суток с момента заливки в формах-опалубках, после чего те снимаются.
- Полученные арболитовые блоки выдерживаются в помещении при стандартной комнатной температуре еще десять суток.
- После этого они укладываются на поддоны и готовы к транспортировке.
Как изготовить арболитовые блоки своими руками?
Одной из привлекательных сторон при производстве арболита является его низкая себестоимость и малая трудозатратность. Кроме этого, технологияне требует сложного оборудования. Поэтому многим людям в голову закрадывается мысль о том, как изготовить такие блоки собственноручно. Более того, некоторые даже составят в голове бизнес-план о том, как своими силами организовать небольшое производство готовых арболитовых блоков. Учитывая рентабельность такого производства и его доходность, приходит вывод, что такая идея имеет свои преимущества. Но обо всем по-порядку.
Важно учитывать, что арболитовые блоки, изготовленные собственноручно вряд ли подойдут на роль несущих стен здания, поскольку в домашних условиях не по силам соблюсти весь технологический процесс. Вторым недостатком «хэндмейда» станет значительная затратность по времени: без наличия специальных сушильных камер и раствора для удаления сахарозы процесс высушивания древесных опилок способен занять около 3 месяцев. Это без учета того, что в домашних условиях окончательная прочность древобетона будет достигнута за те же три месяца.
Если такой срок ожидания не беспокоит, то в таком случае нужно приступать к изготовлению блоков своими силами. Ввиду несложной технологической составляющей процесса изготовление арболитовых блоков в домашних условиях мало чем отличается от фабричных:
- Заготовленные опилки крупных размеров выдерживают на улице на срок до 90 дней в зависимости от условий. Периодически понадобится размешивание опилок для того, чтобы сахароза испарялась из древесины равномерно.
- После этого опилки просеивают через сито, чтобы избавить смесь от загрязнений.
- Опилки смачивают водой и добавляют цемент. Для производства 1 м3 материала требуется в среднем 1200 литров древесной щепы и 240 литров цемента. Вода добавляется в том количества, пока полученная смесь не начинает блестеть.
- После этого смесь заливается в бетономешалку и тщательно перемешивается.
- Полученный арболит заливают в подготовленные формы, которые имеет смысл заранее обшить линолеумом для предотвращения прилипания раствора.
- После трехдневной выдержки блоки вынимаются из формы и отлеживаются в течении трех недель.
Стоит обратить внимание на то, что арболитовые блоки купить проще у дилера, нежели производить их самому.
На сколько целесообразно строить из арболита дом?
Арболитовые блоки, отзывы на которые весьма разнообразные, способны заставить призадуматься о том, насколько целесообразно строить из подобного материала дом. С одной стороны производители наперебой расхваливают свою продукцию. Арболит и в самом деле обладает рядом очевидных преимуществ. По монтажу он не сложнее блоков из пенобетона, но в отличие от них надежно удерживают крепеж. К сравнению, по отзывам некоторых владельцев строений из пенобетона, на стены из этого материала даже нельзя повесить полку, поскольку он не обладает достаточной механической прочностью к такого рода нагрузкам.
Отзывы о прочности и надежности арболита встречаются повсеместно. Дома из этого материала строят уже не одно десятилетие, и многие владельцы подтверждают правильность такого выбора. Конечно, часто встречаются и настолько хвалебные дифирамбы, что поневоле заподозришь в «счастливом дачнике» специально обученного человека. Тем не менее, достоинства арболита были неоднократно подтверждены, и нужно отметить, что позиции кирпича все чаще и чаще теснятся подобными материалами. На это не последнюю очередь влияет фактор цены постройки дома.
Средняя стоимость составляет $500 за 1 м2. При этом, стоимость указана за типовой проект «под ключ» с учетом всех этапов: от проектирования до финишной отделки. Путем несложных подсчетов получаем, что готовый коттедж комфортабельной общей площадью в 95 м2 обойдется покупателю в сумму $47 500. Отсюда делаем вывод: применение арболита больше исходит от желания сэкономить. Конкурентные аналоги арболита часто обладают теми же преимуществами, и схожей ценой. Но не во всем. Для примера, такой же типовой проект «под ключ» коттеджа в 95 м2, изготовленного из СИП панелей по канадской технологии обойдется в $33700. Дома из арболитовых блоков возводятся так же быстро, и способны прослужить такой же срок. Поэтому при желании выстроить себе отдельную «фазенду» - стоит вначале внимательно изучить все предложения в этой сфере.
Постройки из арболита надежны и долговечны. В них комфортно проживать, они требуют значительно меньших затрат на обслуживание и отопление зимой, и если заблаговременно позаботиться о том, чтобы убрать все недостатки материала - дом простоит значительный срок.
strport.ru
Производство арболитовых блоков: станки, оборудование
Технологии изготовления арболита своими руками и промышленным методом не должны иметь особых различий в наличии и последовательности следующих технологических процессов для подготовки сырья:
- производство щепы – если производство щепы осуществляется на месте, то для этой операции необходимым оборудованием является щепорез, для изготовления арболита выбирают агрегат производительностью, сопоставимой объёмам производства готовой продукции. Для производства арболитовых блоков наилучше подходит древесина хвойных видов деревьев;
- просушка материала – для качественной просушки, древесный материл выдерживают на открытом воздухе в течение трёх месяцев. Временами материал переворачивают для лучшей просушки нижних слоёв;
- придание древесине биологической стойкости – делают это для препятствия её гниению уже будучи в составе арболитовых блоков. Для этого удаляют из щепы сахар и минерализируют её при помощи обработки в растворе гашеной извести, хлористого кальция, сернокислых алюминия или кальция, жидкого стекла. Раствор может быть как однокомпонентным, так и комбинированным. Щепу выдерживают в растворе в течение четырёх суток, перемешивая по три раза на день. Объёмное соотношение в смеси должно составлять пять частей щепы и одна раствора.
Необходимое оборудование для производства арболитовых блоков
От предполагаемой производительности будет зависеть, какое оборудование необходимо применять и, соответственно, его цена. Стоит понимать, что чем более высока технологичность всего процесса, тем менее выраженными будут недостатки арболита.
В любом случае Вам понадобится:
- растворосмеситель, лучше принудительного действия;
- станок для вибрационной трамбовки либо ручной инструмент для трамбовки;
- формы для блоков с подставками к ним.
Перечисленный набор – это самый минимум, и он больше подходит для домашней мини-фабрики. Если же продукцию планируется выпускать в промышленных масштабах, то необходима целая производственная линия, где уже не обойтись без вибрационных столов, дорогостоящих смесительных, транспортировочных, сушильных и прочих установок и станков.
Совет прораба: при изготовлении арболитовых блоков своими руками можно прибегать ко всяческим хитростям для снижения цены оснащения. К примеру, можно собственноручно изготовить формы для заливки при помощи досок, которые сколачиваются вместе. Затем они оббиваются из внутренней стороны фанерой и покрываются слоем гидроизолирующего материала, будь то полиэтиленовая плёнка, линолеум или что-то другое, что не пропускает воду. Если вы решили провести собственноручное изготовление форм для арболитовых блоков, то стоит знать, что считаются стандартными их размеры — 20-30*20*50 сантиметров, но, конечно же, они могут иметь и другой размер, на Ваше усмотрение.
Также можно приспособить какой-либо вибрирующий инструмент для виброусадки смеси, помещённой в формы.

Фото: вибростанок

Форма для арболитового блока
Изготовление арболитовых блоков
Для начала необходимо приготовить смесь для производства арболитовых блоков, которая должна состоять из трёх частей древесной составляющей, четырёх частей воды и трёх – цемента. В имеющееся у Вас смесительное оборудование ингредиенты загружаются в очерёдности, соответствующей изложенной выше. В норме образовавшаяся смесь должна выглядеть рассыпчатой, но в то же время сохранять форму, приобретённую сжатием в руке.
Далее, полученный арболит помещают в форму для формирования блока. Излишки удаляют шпателем либо мастерком, форму накрывают крышкой и в течение пяти-десяти секунд подвергают вибротрамбовке. Лучше, когда операция проводится при помощи специального вибрационного станка, но можно обойтись ручной трамбовкой либо же модернизированным Вами виброинструментом.
Следующий этап производства – это сушка арболита. Для сушки с блока снимают форму, при этом он остаётся на подставке формы, на ней он и остаётся до полного затвердевания и высыхания. Также для повышения прочности изделий можно их заворачивать в плёнку на срок до десяти дней, для более медленной влагопотери.
Подводя итоги, можно сказать, что производство арболитовых блоков вполне возможно в домашних условиях, даже без использования дорогостоящих вибрационных станков и другого подобного оборудования, что значительно снижает цену на налаживание производства. С другой стороны, есть чёткая зависимость между ценой оборудования и качеством готовой продукции, снижение одного показателя неминуемо тянет за собой вниз второй, даже при соблюдении тончайших аспектов технологии.
Видео
2bloka.ru
Станок для производства арболитовых блоков своими руками
Содержание статьи:
В строительстве применяется несколько видов расходных материалов. Но наряду с традиционным силикатным кирпичом и шлакоблоками широкое распространение получил новый вид – арболит. Для его изготовления применяют отходы древесной промышленности.
Свойства арболитовых блоков
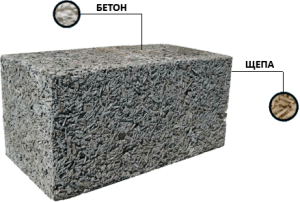
Структура арболитового блока
Прежде чем рассмотреть свойства, преимущества и недостатки арболита – необходимо определиться с его составом и спецификой оборудования. В качестве основы применяется древесная щепа, которая добавляется в раствор с водой, цементом и другими химическими добавками.
Существуют нормативные документы, в которых подробно описываются требования к свойствам и характеристикам арболита – ГОСТ 19222-84 и СН 49-82. Их необходимо детально изучить перед тем, как проектировать мини-станок для производства арболита.
Для производства строительного материала потребуется сформировать щепу с определенными геометрическими параметрами. Оптимальные размеры должны составлять 40*10*5 мм. В противном случае не будут достигнуты нужные свойства арболитовых блоков, изготовленных своими руками.
Особенности производства и параметры оборудования:
- состав. Примерное соотношение компонентов: цемент – 200 кг; опил – 125 кг; песок – 450 кг; хлористый кальций – 4% от общей массы; вода – 220 л.;
- оптимальные размеры. Длина составляет 25 см, ширина – 5-10 см; высота – 3-5 см;
- минимальное количество влаги в щепе. Для решения этой проблемы необходим комплексный подход. Сначала выполняется предварительная просушка, а затем добавляются химические компоненты для минерализации состава.
Оборудование для изготовления арболитовых блоков своими руками может быть настроено для производства строительных материалов двух типов: теплоизоляционные или конструкционные. В первом случае плотность должна быть не менее 400 кг/м³. Для теплоизоляции стен можно использовать изделия, чья удельная плотность ниже этого показателя.
Несмотря на наличие древесной щепы в составе, влага практически не впитывается благодаря предварительной минерализации. Именно поэтому арболитовые блоки, сделанные своими руками, применяют для возведения бань и частных домов.
Комплектация линии для изготовления арболитовых блоков
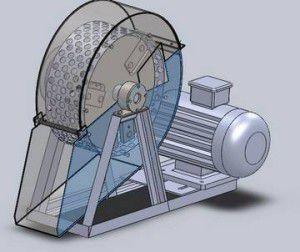
Конструкция щепореза
Важным этапом является предварительная подготовка сырья для производства арболитовых блоков своими руками. Щепу соответствующей формы можно заготавливать вручную либо соорудить простейший щепорез. Для этого необходимо сделать вал, на поверхности которого делают режущие кромки. Щепоуловитель представляет собой кожух, устанавливаемый на режущий элемент.
После заготовки сырья оно проходит стадию предварительной просушки. Дополнительно в состав можно добавлять опилки в соотношении к стружкам 1:1. Уровень влажности не должен быть выше 5%. Затем выполняется процесс формирования готовых изделий. Для их изготовления в домашних условиях потребуется следующий минимальный комплект оборудования:
- щепорез;
- бетономешалка. С ее помощью происходит замешивание раствора;
- формы. Ее размеры должны соответствовать вышеописанным габаритам;
- вибростол. Он необходим для равномерного распределения материала в объеме формы;
- прессовальная машина. Под давлением происходит формирование строительного материала;
- приспособление для переноски заготовок. После прессования арболит будет еще достаточно хрупок. Поэтому для транспортировки к месту просушки необходимы специальные переносные устройства.
Наибольшую сложность представляет производство самодельного вибростола и прессовальной машины. Именно они являются основным оборудованием для производства арболитовых блоков своими руками.
Ближайший аналог станка для арболита — устройство для формирования шлакоблоков. Его конструкцию можно взять в качестве основы для производства самодельной линии.
Линия для производства арболитовых блоков
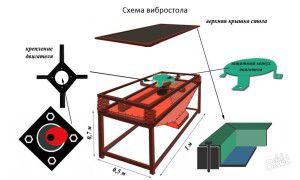
Схема вибростола для арболита
Оптимальным вариантом является производство самодельного вибростола, а также небольшого ручного пресса для окончательного формирования строительного материала. В дальнейшем их можно использовать в оборудовании по производству шлакоблока, тротуарной плитки и т.д.
Для производства вибростола понадобится опорная рама и стальная столешница. Последняя будет крепиться на опорных пружинах. Вибрация происходит за счет движения эксцентрика, расположенного в центре столешницы.
Прессовальная форма должна иметь съемное дно. После окончательного формирования изделия оно помещается на деревянную подставку и переносится в зону просушки. В качестве пресса можно использовать любую самодельную конструкции. Оптимальной является рычажная схема.
Для массового производства блоков своими руками необходима профессиональная линия. Ее стоимость зависит от производительности и комплектации.
В видеоматериале показан пример производства с минимальной комплектацией линии:
stanokgid.ru
Производство арболитовых блоков своими руками
Это довольно интересный строительный материал, который известен еще под такими «народными» названиями, как «древобетон» и «опилкобетон». Из этого уже становится понятно, что входит в состав приготовляемой смеси. Арболит не является очередным «прорывом» в технологии, так как известен достаточно давно и в силу некоторых исторических обстоятельств был в нашей стране незаслуженно забыт. Хотя практическое применение доказало высокую эффективность строительства из арболитовых блоков.
Достаточно сказать, что до перестройки существовал ряд предприятий, которые занимались выпуском этой разновидности стенового камня. Но впоследствии часть из них была перепрофилирована, часть распродана, а некоторые до сих пор стоят бесхозные, в полном разорении.
Прежде чем рассматривать технологию самостоятельного изготовления блоков из арболита, стоит выяснить, а целесообразно ли вообще этим заниматься? Ведь в продаже имеется огромный ассортимент стройматериалов, более «понятных» и привычных. Чтобы было более ясно преимущество данных изделий, укажем, что они изготавливаются на основе древесины, цемента и полимеров.
Основные достоинства продукции
Прочность
Во-первых, резко снижается количество отбракованных изделий, так как риск их повреждения как при транспортировке на объект, так и при проведении монтажных работ сводится к минимуму. Этим может достигаться значительная экономия.
Во-вторых, подразумевается и повышенная устойчивость к деформациям, в том числе, и на изгиб. Это позволяет возводить сооружения на «проблемных» грунтах, на менее «мощных» фундаментах, что существенно удешевляет строительство. Даже в случаях значительных подвижек грунта или возникновения иных причин, вызывающих появление трещин в основании, стены из арболита «устоят».
Высокие эксплуатационные качества
-
Использование данного материала во многих случаях позволяет не применять дополнительных средств утепления, а в случае обустройства такого слоя экономить на «теплоизоляторе». Арболит тепло практически не проводит.
- То же касается и звука. Поэтому такие постройки отличаются качественной шумоизоляцией. В этом плане они в несколько раз лучше кирпича (в 5 раз) или, например, древесины (в 7).
- Воду практически не впитывает, а ячеистая структура (причем крупная) обеспечивает надежный воздухообмен.
- Арболит считается одним из самых экологичных материалов.
- Он легко обрабатывается, надежно удерживает крепеж (шурупы, дюбеля), чего не скажешь, например, о пенобетоне.
Простота самостоятельного изготовления и монтажа
- Можно своими руками готовить различные стройматериалы. Например, блоки из газо- , пенобетона делаются не только на промышленных установках, но и непосредственно на месте применения. Технологии схожи, но качество готовой продукции из арболита получается выше.
- Малый вес делает возможным все мероприятия фиксации блоков по месту проводить вручную.
- Абсолютная ровность граней позволяют делать «финишную» отделку любым материалом
Низкая затратность строительства
Кроме уже указанных способов экономии (в том числе, и на отоплении), при правильном изготовлении расход самого дорогостоящего компонента всех легких бетонов – цемента – может быть сокращен примерно в 3 раза.
Компоненты
Вяжущее вещество — как правило, используется цемент марок «400» или «500».
Наполнители — здесь вариантов достаточно, причем могут использоваться и сочетания рекомендуемых ингредиентов (из древесины).
Основные:
- стружка;
- опилки;
- щепа.
Дополнительные компоненты (не более 5% от общей массы основного):
- хвоя;
- древесная труха (кора, листья).
Добавки
Для повышения прочности и ряда других характеристик целесообразно вводить в состав и некоторые вещества. Например, жидкое стекло или его смесь с окисью кальция (1 к 1). Все зависит от того, для чего нужны блоки – несущий элемент конструкции или нет, условия дальнейшей эксплуатации, особенности климата и ряд других факторов.
Химикаты
Древесина, как органическое вещество, в своем составе содержит сахар. Его нужно нейтрализовать, так как он снижает прочность готового продукта. Поэтому в состав смеси вводятся, например, кальций хлористый, алюминий сернокислый и ряд других. Но в открытой продаже таких «реактивов» нет, поэтому сахар при самостоятельном изготовлении можно нейтрализовать другим способом, о котором чуть ниже.
Технология – основные этапы и особенности
Подготовка компонентов
Все наполнители необходимо тщательно измельчить. Максимально допустимые размеры фракций (не в ущерб качеству блоков) – 2,5 см длина и 0,5 см ширина. Задача – добиться равномерного распределения всех составляющих по объему, что обеспечивает однородность структуры и, как следствие, высокое качество продукции.
Далее (для нейтрализации сахара) древесные наполнители заливаются известковым раствором (1,5%) и перемешиваются. Выдержка – не меньше 3 часов. На 1 м³ состава понадобится примерно 200 л.
После этого жидкость сливается, и масса еще выдерживается примерно 96 часов. Несколько раз за день ее следует «перелопачивать».
Приготовление раствора
Для получения необходимого его качества нужно «замес» производить в бетономешалке. Это позволит добиться действительно тщательного перемешивания. Если данную работу выполнять вручную, традиционным способом – лопатой – то не избежать образования комков, неоднородности структуры камня. Это ощутимо аннулирует все его преимущества перед аналогами.
Пропорция рекомендуется следующая: вода – 4 части, древесина и цемент – по 3.
При замесе не следует сразу загружать в барабан все, что приготовлено. Ингредиенты закладываются порционно, без выключения агрегата. Так же частями заливается и вода. Это значительно повысит качество конечного продукта.
Совет
В процессе приготовления нужно контролировать степень готовности раствора. Если после сжатия в кулаке небольшой порции на ладони (после распрямления пальцев) остается лежать комок (то есть масса держит форму), то арболит готов.
Получение блоков
Раствор заливается в специально приготовленные формы. Их габариты выбираются в соответствие с требуемыми размерами камня. Такие «шаблоны» продаются для производства пено- или газобетона. При некотором умении в обращении с инструментом их можно изготовить самостоятельно – из гладко обработанной доски, толстой (слоеной) фанеры.
Конструкция несложная. Сбивается длинный пенал, по внутренним стенкам которого с определенным интервалом делаются выпилы. В эти пазы вставляются внутренние перегородки, которые делят пенал на ячейки с размерами будущих блоков. В них и заливается раствор. После отвердевания готовая продукция вынимается и выкладывается на подготовленную площадку. На ней изделия «доходят» до окончательной готовности.
Несколько замечаний
- древесина должна быть очищена от грязи и посторонних фракций;
- она нуждается и в дезинфекции. Для этого хорошо подходит известь гашеная;
-
для повышения прочности раствор необходимо уплотнять (после заливки в опалубку или формы для блоков). Это позволит удалить из массы воздух и излишки влаги. Производится или машинками для вибропрессования, или лопатой, арматурой способом «протыкания» заливки;
- чтобы блоки не прилипали к «пеналу», необходимо внутренние стенки соответствующим образом подготовить. Они заранее отделываются пленкой, линолеумом, или обрабатываются отработанным машинным маслом перед заливкой очередной порции раствора;
- можно встретить рекомендации, что для арболита подойдет и цемент 200 или 300. Да, но если он «свежий» и блоки в дальнейшем не будут чрезмерно нагружены. Стоит учесть, что всего полгода хранения цемента снижают его основные характеристики примерно на 40 – 45%. Следовательно, «старый» М300 уже не будет таковым. Он может соответствовать по факту (зависит от условий хранения), например, М150. Поэтому рекомендация по маркам 400, 500 вполне уместна и дана не зря.
В Интернете можно встретить и много других рекомендаций по самостоятельному изготовлению арболитовых блоков, которые в основе своей схожи, а в нюансах различаются. Стоит понимать, что этот процесс – отчасти «творческий», экспериментальный. Поэтому сначала нужно попробовать готовить небольшой партией (опытной). Тогда и станет понятно, как лучше работать с ЭТИМ цементом, с ЭТИМИ опилками и так далее.
masterim.guru
Производство арболитовых блоков. Как своими руками изготовить арболитовые блоки?
Преимущества арболитовых блоков
Другое название материала – опилкобетонные блоки. Они воплощают в себе прекрасные качества, среди которых дешевизна технологии производства, что влияет, в конечном счете, на стоимость строительства всего дома. Теплоизоляционные свойства блоков способствуют удержанию тепла в доме. Ко всему прочему, арболитовые блоки могут изготовить даже непрофессионалы ввиду легкости производства. Долговечный, прочный и пожаростойкий материал – это все про опилкобетонные блоки.
Как изготовить арболитовые блоки: технология
Арболитовые блоки можно изготовить в домашних условиях. Правда, есть один недостаток изготовления в таких условиях материала – вы не сможете приготовить его большое количество.На первом этапе нужно подготовить все компоненты будущего материала. После чего позаботиться о приготовлении основы. А на последнем этапе залить состав в формы, чтобы получить готовые блоки.
Основа для производства арболита
Нужно подготовить хорошо просушенные опилки и стружки, соблюдая пропорции один к одному. Полное высыхание данных компонентов происходит в течение трех или четырех месяцев и сопровождается обработкой раствором извести с периодическим переворачиванием.
Что добавляют в опилки?
К основному компоненту – опилкам добавляют:
- сернокислый алюминий и кальций;
- известь гашеную;
- жидкое стекло в растворимом составе;
- 400 марку портландцемента;
- кальций хлор.
Эти добавки должны составлять 4% от всей цементной массы. Они способствуют тому, что материал получает свойства огнеупорности, пластичности, а также устойчивости к процессам гниения.
Технология создания арболитовых блоков
Параметры блоков – 25х25х50 сантиметров, поэтому их легко изготавливать, а в дальнейшем укладывать. Что касается процесса отливки, то он заключается в том, что арболитовая смесь заполняет блоки тремя слоями. После каждого слоя стучат молотком из дерева, обшитым жестью для уплотнения. Посредством линейки удаляют лишнее, после чего ждут сутки выдержки формы. При этом нужно соблюдать температурный режим +18 градусов Цельсия.
По прошествии суток блоки вынимают из формы посредством небольших постукиваний. Их складывают на ровную поверхность и ждут полного застывания два дня, а просушивают в течение десяти дней.
Оборудование для создания арболитовых блоков
В целях создания арболитовых блоков своими руками нужно обзавестить самым разнообразным оборудованием, а каким именно зависит от объемов производства, а также от сырья. Зачастую для создания таких блоков берут остатки дерева хвойной породы. Для их измельчения потребуется специальная рубильная машинка либо молотковая мельница. Такой прибор как вибростол отделяет части коры и земли из древесины.
Арболитовая смесь изготавливается на растворосмесителях с лопастями либо цикличных принудительных смесителях. Для перевоза готовой смеси непосредственно к формам необходимы специальные транспортеры.
ogodom.ru